BLOG - GAS TURBINES
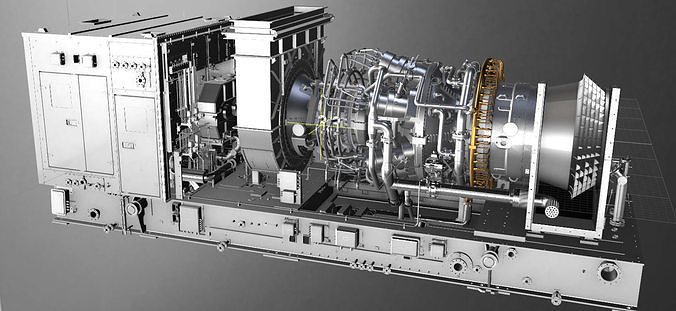
GOOD PERFORMANCE
HIGH EFFICIENCY
HIGH SAFETY
High performance in gas turbines refers to the ability of the turbine to generate a large amount of power output while consuming the minimum amount of fuel and maintaining high levels of reliability and efficiency. Achieving high performance in gas turbines is critical to their successful operation and competitiveness in the market. Here are some factors that contribute to high performance in gas turbines:
High thermal efficiency: Thermal efficiency is a measure of how effectively the gas turbine converts fuel energy into useful work output. High thermal efficiency can be achieved through advanced turbine designs, improved materials, and better combustion technology.
High power output: High power output is essential for efficient and effective operation of the gas turbine. This can be achieved through optimizing the design of the turbine and using advanced materials to improve the strength and durability of the components.
High reliability: A reliable gas turbine is essential for maintaining high performance over the long term. Achieving high reliability requires robust design and engineering practices, effective maintenance and inspection procedures, and advanced digital monitoring and control systems.
High availability: The availability of a gas turbine refers to the percentage of time that it is available and operational. Achieving high availability requires a combination of good maintenance practices, effective troubleshooting procedures, and advanced digital monitoring and control systems.
Low emissions: Gas turbines that produce low emissions are more environmentally friendly and more attractive to customers. Achieving low emissions requires advanced combustion technology and effective emissions control systems.
Low noise: Gas turbines that produce low noise levels are less disruptive to the surrounding environment and less likely to cause safety hazards. Achieving low noise levels requires advanced aerodynamics, acoustics, and noise reduction technology.
In summary, achieving high performance in gas turbines requires a combination of high thermal efficiency, high power output, high reliability, high availability, low emissions, and low noise levels. By optimizing these factors, gas turbine manufacturers can produce machines that are efficient, reliable, and competitive in the market.
High efficiency in gas turbines refers to the ability of the turbine to convert a large percentage of the energy in the fuel into useful work output. This is measured by the turbine’s thermal efficiency, which is the ratio of the work output to the energy input.
There are several factors that contribute to high efficiency in gas turbines:
Advanced design and engineering: The design and engineering of the gas turbine play a critical role in determining its efficiency. Advanced design techniques, such as computational fluid dynamics (CFD) and finite element analysis (FEA), can help optimize the turbine’s performance.
Advanced materials: The use of advanced materials, such as high-temperature alloys and ceramic composites, can help improve the turbine’s efficiency by allowing it to operate at higher temperatures and pressures.
Improved combustion technology: Efficient combustion is essential for achieving high efficiency in gas turbines. Advanced combustion technologies, such as lean-burn combustion and staged combustion, can help improve the combustion process and reduce emissions.
Advanced cooling technology: Cooling is necessary to protect the turbine components from high temperatures. Advanced cooling technology, such as film cooling and internal cooling, can help improve the efficiency of the turbine by reducing the cooling air required.
Digital monitoring and control systems: Digital monitoring and control systems can help optimize the performance of the gas turbine by adjusting the operating parameters in real-time based on the conditions of the turbine.
Combined cycle operation: Gas turbines can be used in combination with steam turbines in a combined cycle operation to achieve even higher efficiency. In a combined cycle, the exhaust heat from the gas turbine is used to generate steam that drives a steam turbine, increasing the overall efficiency of the system.
In summary, achieving high efficiency in gas turbines requires a combination of advanced design and engineering, advanced materials, improved combustion technology, advanced cooling technology, digital monitoring and control systems, and combined cycle operation. By optimizing these factors, gas turbine manufacturers can produce machines that are highly efficient and competitive in the market
High safety in gas turbines refers to the ability of the turbine to operate without posing a significant risk to personnel, equipment, or the environment. Achieving high safety in gas turbines is essential to prevent accidents, protect workers, and minimize the risk of damage to the turbine and surrounding equipment.
Here are some of the factors that contribute to high safety in gas turbines:
Robust design and engineering: A gas turbine’s design and engineering must be robust and reliable to ensure its safe operation. This includes ensuring that all critical components are properly sized, designed, and tested to withstand the expected operating conditions.
Advanced monitoring and control systems: Advanced digital monitoring and control systems can help detect and prevent unsafe operating conditions. These systems can monitor various parameters, such as temperature, pressure, and vibration, and provide real-time feedback to operators to allow them to make adjustments as necessary.
Safety devices and systems: Gas turbines are equipped with a variety of safety devices and systems, such as automatic shutdown systems, emergency cooling systems, and fire suppression systems, to prevent accidents and minimize the impact of any incidents.
Proper training and procedures: Proper training and procedures are essential to ensure that personnel are aware of the potential hazards associated with operating gas turbines and know how to respond to emergencies.
Compliance with regulations: Gas turbine manufacturers and operators must comply with various regulations and standards related to safety. This includes meeting requirements related to emissions, noise, and other environmental factors, as well as complying with regulations related to worker safety and equipment certification.
In summary, achieving high safety in gas turbines requires a combination of robust design and engineering, advanced monitoring and control systems, safety devices and systems, proper training and procedures, and compliance with regulations. By prioritizing safety in the design, operation, and maintenance of gas turbines, manufacturers and operators can minimize the risk of accidents and ensure the safe and efficient operation of the turbine
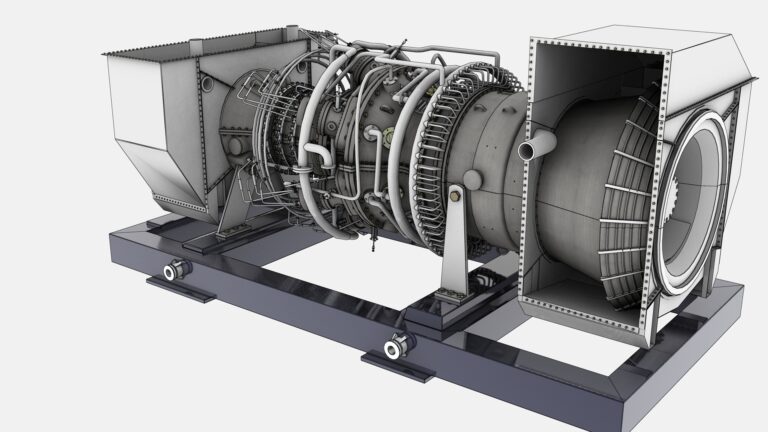
COMBUSTION SYSTEM
TURBINE BLADES
FUEL INJECTION SYSTEM
Combustion instability: This is a phenomenon in which the combustion process becomes unsteady and may cause vibrations, noise, and even damage to the gas turbine. Combustion instability can be caused by factors such as fuel quality, flame shape, and flow dynamics.
Emissions: Industrial gas turbines are subject to strict emissions regulations, and the combustion system plays a critical role in controlling emissions of pollutants such as nitrogen oxides (NOx) and particulate matter. Achieving low emissions while maintaining high efficiency and performance is a major technical challenge.
Combustion dynamics: The combustion process in industrial gas turbines can produce pressure waves that can interact with the turbine blades and cause damage. Careful design of the combustion system is necessary to minimize the risk of these pressure waves and ensure safe and reliable operation.
Fuel flexibility: Industrial gas turbines may need to operate on a variety of fuels, including natural gas, biogas, and liquid fuels. Designing a combustion system that can accommodate different fuel types while maintaining high efficiency and low emissions can be a significant technical challenge.
Combustion liner durability: The combustion liner is the part of the combustion system that is exposed to the highest temperatures and pressures. Maintaining the integrity and durability of the combustion liner is critical to ensuring safe and reliable operation of the gas turbine.
Fuel injection system reliability: The fuel injection system delivers fuel to the combustion chamber at high pressure and under extreme conditions. Ensuring the reliability of the fuel injection system is critical to maintaining safe and efficient operation of the gas turbine.
Combustion system cooling: The combustion process generates a significant amount of heat, and effective cooling of the combustion system is necessary to prevent damage to the gas turbine components. Careful design of the cooling system is critical to maintaining safe and reliable operation of the gas turbine
High-temperature corrosion: Turbine blades in industrial gas turbines are exposed to high temperatures and can be subject to corrosion due to the hot gases flowing over them. This can lead to reduced efficiency and blade damage over time.
Fatigue: The repeated cycles of heating and cooling that turbine blades experience during operation can lead to fatigue failure over time. This is a critical issue that must be managed to prevent catastrophic failure.
Creep: Turbine blades are designed to operate at high temperatures, but at these temperatures, the metal can experience creep, which is the deformation of the material under a constant load. Creep can lead to reduced blade life and eventually failure.
Blade cooling: Cooling of turbine blades is necessary to prevent them from melting or becoming damaged due to the high temperatures they are exposed to. Effective cooling design is critical to ensuring safe and reliable operation of the gas turbine.
Blade manufacturing: Manufacturing of turbine blades is a complex process that requires high precision and quality control. Any defects or variations in the manufacturing process can lead to reduced blade life and increased risk of failure.
Blade material selection: The selection of materials for turbine blades must take into account factors such as high-temperature performance, corrosion resistance, and fatigue resistance. Selecting the right materials is critical to ensuring safe and reliable operation of the gas turbine.
Blade repair and maintenance: Over time, turbine blades may become damaged or worn and require repair or replacement. Effective repair and maintenance practices are critical to ensuring safe and reliable operation of the gas turbine.
Blade vibration: Turbine blades can experience vibration due to a variety of factors, including unbalanced forces and resonant frequencies. Vibration can cause damage to the blades and other components of the gas turbine and must be managed to prevent failure
Fuel quality: The quality of the fuel delivered to the combustion chamber can have a significant impact on the performance and reliability of the gas turbine. Poor quality fuel can cause fouling of the fuel injectors and other components of the fuel injection system, leading to reduced efficiency and increased maintenance costs.
Fuel pressure: The fuel injection system must deliver fuel to the combustion chamber at high pressure to ensure efficient combustion. Maintaining the proper fuel pressure is critical to ensuring safe and reliable operation of the gas turbine.
Fuel atomization: Fuel must be atomized into small droplets to ensure efficient combustion. The fuel injection system must be designed to deliver fuel in a way that achieves the proper level of atomization.
Fuel flow rate: The amount of fuel delivered to the combustion chamber must be carefully controlled to achieve the desired combustion characteristics. The fuel injection system must be able to deliver fuel at a wide range of flow rates to accommodate different operating conditions.
Fuel system leaks: Any leaks in the fuel injection system can lead to a loss of fuel pressure, reduced efficiency, and potential safety hazards. Proper maintenance and inspection of the fuel injection system are critical to preventing leaks.
Fuel filter maintenance: Fuel filters are used to remove contaminants from the fuel before it enters the fuel injection system. Proper maintenance of the fuel filters is critical to preventing blockages and ensuring the proper flow of fuel.
Fuel pump reliability: The fuel pump is a critical component of the fuel injection system that must operate reliably under high pressures and temperatures. Ensuring the reliability of the fuel pump is critical to maintaining safe and reliable operation of the gas turbine.
Fuel system design: The fuel injection system must be designed to deliver fuel to the combustion chamber in a way that achieves the desired combustion characteristics while minimizing the risk of emissions and other issues. Careful design of the fuel injection system is critical to ensuring safe and efficient operation of the gas turbine
INLET AIR FILTERS
VARIABLE IGV & GOVERNOR SYSTEM
EXHAUST SYSTEM
Filter efficiency: Inlet air filters are designed to remove contaminants from the air before it enters the gas turbine. The filter efficiency is critical to ensuring that the gas turbine is protected from harmful particles that could damage components or reduce efficiency.
Pressure drop: As air passes through the filter, there is a pressure drop across the filter media. Excessive pressure drop can reduce the flow of air to the gas turbine, reducing its efficiency and potentially causing damage to components.
Filter maintenance: Inlet air filters require regular maintenance to ensure that they continue to operate effectively. If filters become clogged with debris, their efficiency can be significantly reduced, and they can cause pressure drop issues.
Filter selection: Selecting the right type of filter is critical to ensuring the effective removal of contaminants from the air. Factors such as the size and type of contaminants present in the air, the operating environment, and the desired level of filter efficiency must be considered.
Filter installation: Proper installation of the inlet air filters is critical to ensuring that they operate effectively. Filters must be installed correctly, and their seals must be checked to ensure that air does not bypass the filter.
Filter media selection: Different types of filter media are available, and the selection of the appropriate media is important. Factors such as the type of contaminants, the expected filter efficiency, and the expected service life must be considered.
Filter bypass: Inlet air filters can fail or become overloaded with debris, which can result in air bypassing the filter. Bypassing the filter can cause damage to components and reduce the efficiency of the gas turbine.
Filter monitoring: Regular monitoring of the inlet air filter system is important to identify issues such as pressure drop, filter efficiency, and potential failures. Effective monitoring can help to prevent damage to the gas turbine and ensure its continued operation
VIGV wear and tear: The variable inlet guide vanes (VIGV) are used to control the flow of air into the gas turbine, and they are subject to significant wear and tear over time. Proper maintenance and inspection of the VIGV are critical to ensuring that they operate effectively.
VIGV fouling: The VIGV can become fouled with debris, reducing their effectiveness and potentially causing damage to the gas turbine. Regular cleaning and inspection of the VIGV are necessary to prevent fouling.
Governor system failure: The governor system is responsible for controlling the speed of the gas turbine by adjusting the VIGV. A failure in the governor system can cause the gas turbine to operate at an unsafe speed, potentially causing damage or even catastrophic failure.
Governor system maintenance: Proper maintenance and inspection of the governor system are critical to ensuring that it operates effectively. Regular calibration and testing are necessary to ensure that the governor system is functioning correctly.
VIGV actuation: The actuation of the VIGV is critical to controlling the flow of air into the gas turbine. Proper actuation requires the use of high-quality actuation mechanisms and control systems that can respond quickly and accurately to changes in operating conditions.
VIGV control system: The control system for the VIGV must be designed to respond to changes in operating conditions quickly and accurately. Any delay or inaccuracy in the control system can cause the gas turbine to operate inefficiently or unsafely.
VIGV design: The design of the VIGV must be optimized to ensure that they can operate effectively under a wide range of operating conditions. Proper design is critical to ensuring the efficient and reliable operation of the gas turbine.
VIGV material selection: The materials used in the construction of the VIGV must be selected carefully to ensure that they can withstand the high temperatures and stresses associated with gas turbine operation. Improper material selection can result in premature failure of the VIGV
Temperature: The exhaust gas temperature of a gas turbine can be very high, which can cause significant wear and tear on the exhaust system components. Proper material selection and cooling mechanisms are critical to ensure that the exhaust system can handle the high temperatures.
Corrosion: The exhaust gas can contain corrosive compounds that can corrode the exhaust system components, leading to premature failure. Proper material selection and corrosion protection mechanisms are essential to mitigate this risk.
Exhaust gas flow: The flow of exhaust gas through the exhaust system must be carefully controlled to prevent excessive pressure drop, which can reduce the efficiency of the gas turbine. Proper design of the exhaust system, including the selection of the appropriate ducting and silencing components, is critical to ensure that the exhaust gas flows smoothly.
Exhaust stack design: The design of the exhaust stack must be optimized to ensure that the exhaust gas is released at a safe distance from people and equipment. Proper stack design can help to minimize the risk of environmental contamination and ensure compliance with local regulations.
Exhaust emissions: The exhaust gas can contain pollutants that must be treated to meet environmental regulations. The design and selection of exhaust treatment systems, such as catalytic converters, are critical to ensure compliance with local emissions regulations.
Exhaust silencers: The noise produced by the gas turbine exhaust can be significant, and the installation of exhaust silencers is often required to comply with local noise regulations. The selection and installation of the appropriate silencing components must be carefully considered to ensure that they do not cause excessive pressure drop or interfere with the performance of the gas turbine.
Exhaust system maintenance: Proper maintenance of the exhaust system is critical to ensure its continued operation. Regular inspection and cleaning of the exhaust components are necessary to prevent corrosion and ensure that the exhaust system is operating effectively.
Exhaust system monitoring: Regular monitoring of the exhaust system is important to identify issues such as excessive pressure drop, corrosion, or emissions compliance issues. Effective monitoring can help to prevent damage to the gas turbine and ensure its continued operation.
SECTIONS - GAS TURBINES
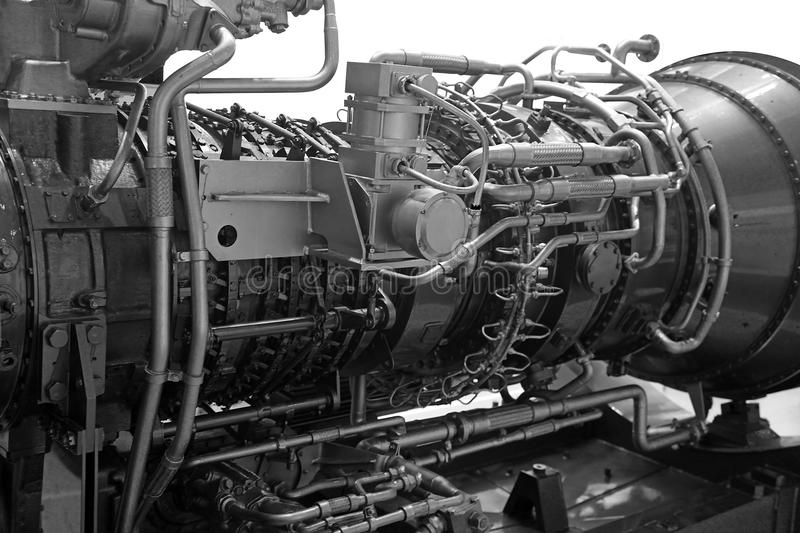