LONG TERM SERVICES AGREEMENTS (LTSA) vs FIELD REPAIR MAINTENANCE CREW SERVICES

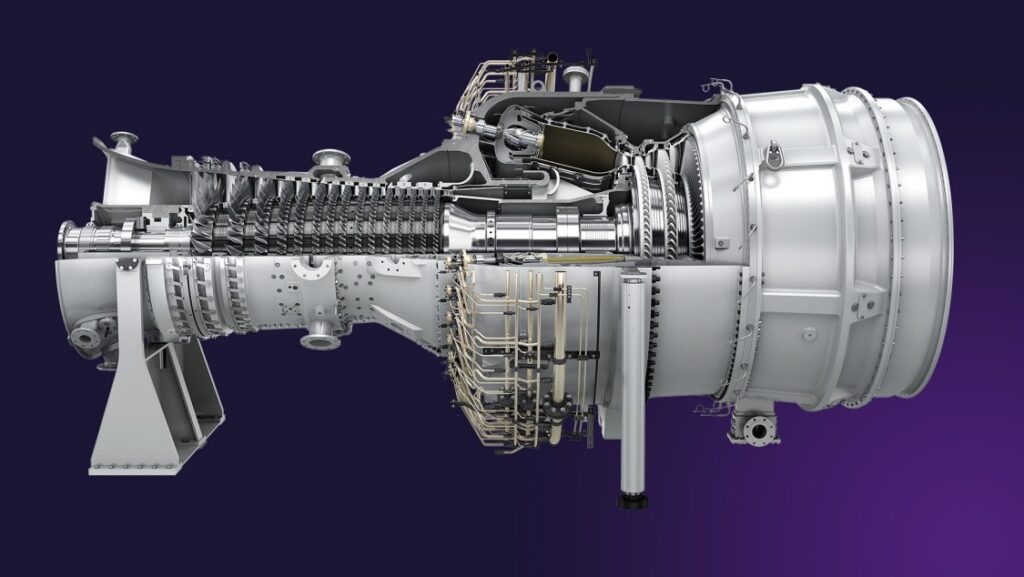
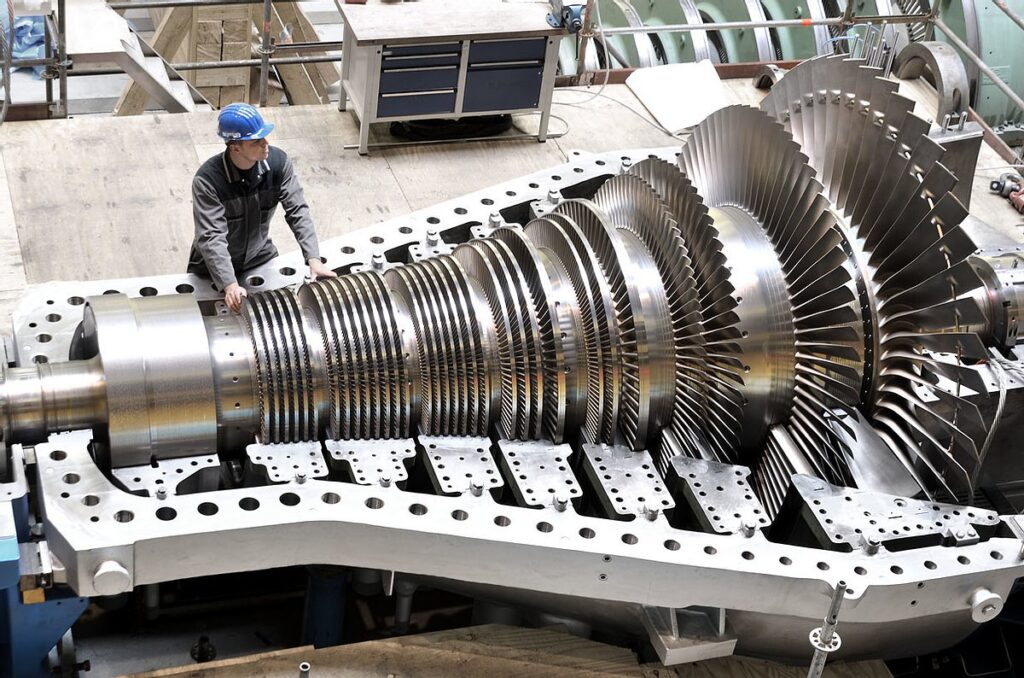
CENTRIFUGAL COMRPESSORS
GAS TURBINES
SPECIAL STEAM TURBINES
DIFFERENCIES BETWEEN A LONG TERM SERVICES AGREEMENTS CONTRACT (LTSA) AND FIELD REPAIR MAINTENANCE CREW SERVICES - TURBOMACHINERY
Long-term service agreements (LTSAs) and field repair by maintenance crews are two different approaches to managing and maintaining turbomachinery. Here are the key differences between them:
Scope of Service:
- Long-term service agreements: LTSAs involve a comprehensive scope of service provided by the original equipment manufacturer (OEM) or a third-party service provider. The agreement typically covers a range of services such as preventive maintenance, repairs, parts supply, performance monitoring, and technical support.
- Field repair by maintenance crew: Field repair by maintenance crews refers to maintenance and repair activities performed by the user’s in-house maintenance team or external contractors. It generally includes immediate repair or troubleshooting of specific issues identified during regular operation.
Expertise and Resources:
- Long-term service agreements: LTSAs are typically provided by OEMs or specialized service providers who have extensive expertise, resources, and experience in maintaining and servicing turbomachinery. They have access to OEM-approved parts, specialized tools, and advanced diagnostic equipment.
- Field repair by maintenance crew: Maintenance crews are usually comprised of the user’s own technicians or contractors who may have varying levels of expertise and resources. They may not have the same level of specialized knowledge and equipment as the OEM or dedicated service providers.
Contractual Agreement:
- Long-term service agreements: LTSAs are formal contractual agreements between the equipment owner/user and the service provider. The agreement defines the scope of work, service level agreements, performance guarantees, and financial terms such as pricing and payment schedules.
- Field repair by maintenance crew: Field repairs are typically carried out based on an ad-hoc basis without a formal contractual agreement. The maintenance crew responds to issues as they arise, and the work may be managed through work orders or service requests.
Cost Structure:
- Long-term service agreements: LTSAs often involve a predetermined cost structure, either through fixed periodic payments or based on the equipment’s operating hours or performance indicators. The costs are typically spread out over the duration of the agreement.
- Field repair by maintenance crew: Field repairs are typically billed on a time and materials basis, where the user is charged for the actual labor, parts, and any additional expenses incurred during the repair or maintenance activities.
Responsibility and Accountability:
- Long-term service agreements: In LTSAs, the service provider assumes a greater level of responsibility and accountability for maintaining the equipment’s performance and reliability. They are contractually obligated to meet certain performance targets, respond to issues promptly, and provide technical support as required.
- Field repair by maintenance crew: With field repair by maintenance crews, the user retains a higher level of responsibility for maintaining and managing the equipment. They are accountable for coordinating the repair activities, ensuring the availability of resources, and managing the maintenance crew’s performance.
Both long-term service agreements and field repair by maintenance crews have their own advantages and considerations. LTSAs offer comprehensive support and expertise, ensuring a proactive approach to maintenance and minimizing downtime. On the other hand, field repair by maintenance crews provides flexibility and control over the maintenance process, allowing for immediate response to issues. The choice between the two approaches depends on factors such as the equipment’s criticality, available resources, budget constraints, and the user’s maintenance capabilities.
FREQUENT QUESTIONS & ANSWERS - TURBOMACHINERY
Q: What is a long-term service agreement (LTSA)? A: A long-term service agreement is a contract between a plant operator and a service provider, typically an Original Equipment Manufacturer (OEM) or an authorized service provider, for the provision of maintenance, repair, and support services over an extended period. It outlines the scope of services, performance guarantees, and cost structure.
Q: What is field repair by maintenance crew? A: Field repair by maintenance crew refers to performing maintenance, repairs, and troubleshooting on turbomachinery using the plant’s own maintenance personnel or an external maintenance crew that is not specifically affiliated with the OEM.
Q: When should I consider a long-term service agreement? A: Long-term service agreements are often considered when plant operators want to ensure reliable and optimized performance of their turbomachinery over an extended period. They are suitable when specialized OEM expertise, access to genuine OEM parts, and proactive maintenance are desired to mitigate risks and maximize availability.
Q: When is field repair by maintenance crew more appropriate? A: Field repair by maintenance crew may be more appropriate when the plant has sufficient in-house expertise, resources, and flexibility to manage maintenance and repair activities independently. It can be suitable for non-critical components, routine maintenance tasks, or when cost considerations play a significant role.
Q: Where can long-term service agreements be beneficial? A: Long-term service agreements can be beneficial in various industries, including power generation, oil, gas, and petrochemical industries, where the reliable operation of turbomachinery is crucial for production processes, safety, and environmental compliance.
Q: Where can field repair by maintenance crew services be suitable? A: Field repair by maintenance crew services can be suitable in plants where there is an experienced and well-trained maintenance team capable of performing repairs and maintenance tasks effectively. It is often employed for routine maintenance, minor repairs, or when immediate response and on-site availability are critical.
Q: What are the key benefits of long-term service agreements? A: Long-term service agreements provide access to OEM expertise, specialized knowledge, proactive maintenance, performance guarantees, and genuine OEM parts. They offer predictable maintenance costs and ensure that maintenance activities are aligned with OEM recommendations, thereby improving reliability, availability, and safety.
Q: What are the advantages of field repair by maintenance crew services? A: Field repair by maintenance crew services provide more flexibility and control over maintenance activities. They may be cost-effective for routine maintenance tasks and minor repairs. Immediate response and on-site availability can be achieved, minimizing downtime and production interruptions.
Q: What are the potential drawbacks of long-term service agreements? A: Long-term service agreements can involve higher costs, contractual complexities, and limited customization options. Plant operators may also become dependent on external service providers, which can affect flexibility and control over maintenance processes.
Q: What are the limitations of field repair by maintenance crew services? A: Field repair by maintenance crew services may not provide access to specialized OEM knowledge and resources. They may not offer performance guarantees, and the expertise and availability of the maintenance crew may vary, potentially leading to delays or suboptimal repairs.
Q: How should I decide between a long-term service agreement and field repair by maintenance crew services? A: The decision depends on factors such as the complexity of maintenance tasks, the criticality of the equipment, the availability of in-house expertise and resources, the desired level of control, and the budget constraints. A thorough evaluation of the advantages, disadvantages, and specific needs of the plant will help determine the most suitable approach.
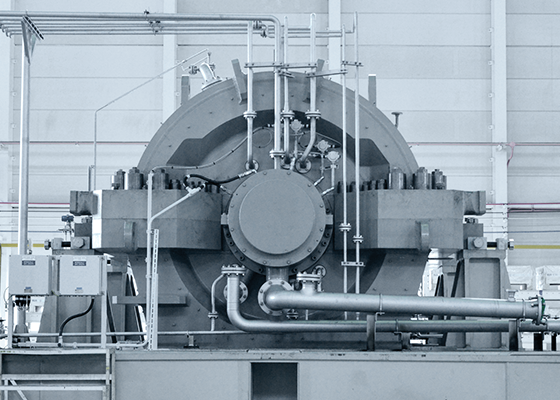
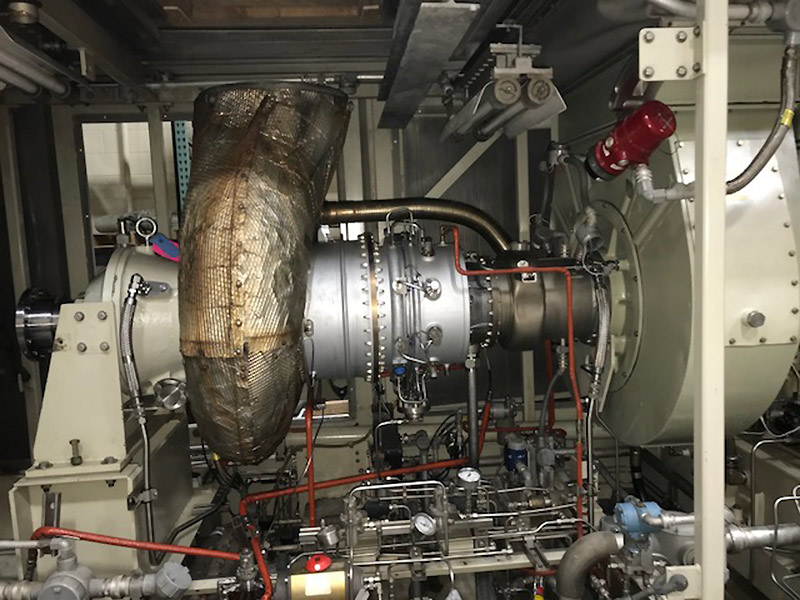
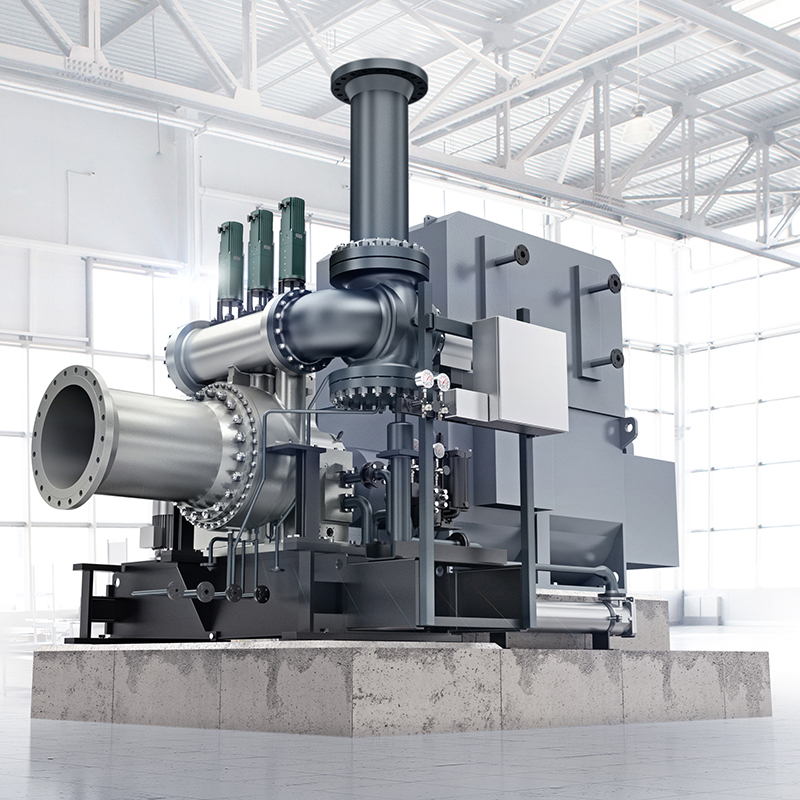