CARBON CAPTURE & STORAGE (CCS) - CENTRIFUGAL COMPRESSORS
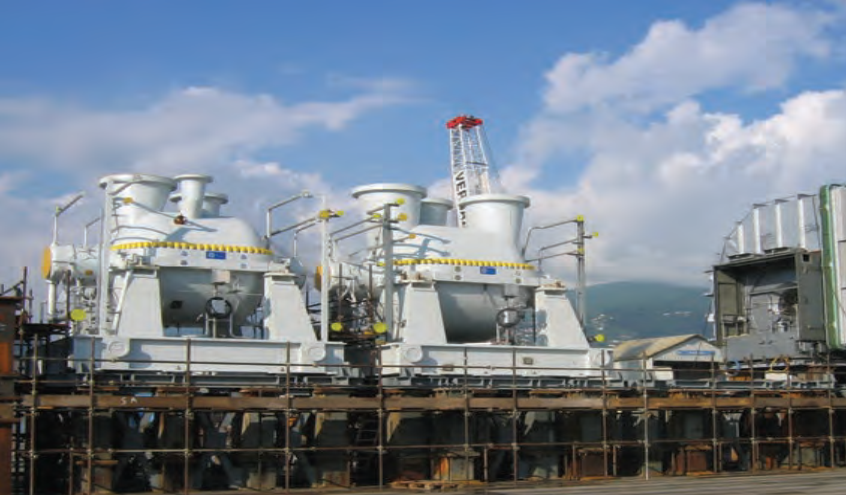
ADVANTAGES & DISADVANTAGES IN "CCS" WITH CENTRIFUGAL COMPRESSORS
Centrifugal compressors offer several advantages when used for compressing and storing CO2 underground in the oil, gas, and petrochemical industries. However, there are also disadvantages to consider. Let’s explore both sides:
Advantages of Centrifugal Compressors for CO2 Compression and Storage:
High Efficiency: Centrifugal compressors are known for their high efficiency in converting power into compressed gas. This efficiency is crucial when compressing CO2 for storage, as it minimizes energy consumption and reduces operational costs.
Compact Design: Centrifugal compressors have a relatively compact design compared to other types of compressors. This makes them suitable for installations where space is limited, such as offshore platforms or existing industrial facilities.
Wide Operating Range: Centrifugal compressors have a wide operating range, allowing them to handle varying gas flows and pressures effectively. This flexibility is beneficial when dealing with fluctuating CO2 production rates or changing storage requirements.
Low Maintenance Requirements: Compared to reciprocating compressors, centrifugal compressors generally have lower maintenance requirements. They have fewer moving parts and require less frequent inspections, resulting in reduced downtime and increased reliability.
Disadvantages of Centrifugal Compressors for CO2 Compression and Storage:
Capital Cost: Centrifugal compressors tend to have higher upfront capital costs compared to other compressor types. The complexity of their design, coupled with the need for specialized materials and manufacturing processes, can contribute to the overall expense of implementing a centrifugal compressor system.
Sensitivity to Process Conditions: Centrifugal compressors are sensitive to changes in process conditions, such as gas composition, temperature, and pressure. Variations outside their design parameters can affect performance and efficiency, potentially leading to reduced reliability and increased risk of failure.
Limited Compression Ratio: Centrifugal compressors have a limited compression ratio compared to some other compressor types, such as reciprocating compressors. This means that they may not be suitable for compressing CO2 to very high pressures, depending on the specific project requirements.
Potential for Surge: Centrifugal compressors are susceptible to surge, a phenomenon where the flow through the compressor becomes unstable, causing pressure fluctuations and potential damage. Surge can occur during low flow conditions or sudden changes in operating conditions. Surge protection systems and proper design considerations are necessary to mitigate this risk.
In summary, while centrifugal compressors offer high efficiency, compact design, and wide operating ranges, they also have higher upfront costs, sensitivity to process conditions, limited compression ratios, and the potential for surge. Assessing the specific project requirements, considering the advantages and disadvantages, and implementing appropriate control and mitigation measures are essential for utilizing centrifugal compressors effectively in CO2 compression and storage applications.
LIMITATIONS IN ENGINEERING & DESIGN USING CENTRIFUGAL COMPRESSORS IN CCS
When considering the limitations in engineering and design using centrifugal compressors for compressing and storing CO2 underground, several factors should be taken into account. These limitations can impact the overall reliability and risk mitigation of the system. Here are some key limitations to consider:
Gas Composition: Centrifugal compressors are designed for specific gas compositions and may not be suitable for handling all types of gases. CO2 from existing plants or new projects in the oil, gas, and petrochemical industries can have impurities or contaminants that could affect compressor performance or integrity. Careful analysis of the gas composition is necessary to ensure compatibility with the centrifugal compressor.
Corrosion and Material Selection: CO2 can be corrosive, especially in the presence of impurities or moisture. The selection of appropriate materials for the compressor components is crucial to mitigate corrosion risks. Compatibility with CO2 and the storage environment, such as underground conditions, must be considered during the design phase to avoid material degradation and potential failures.
Pressure and Temperature Limitations: Centrifugal compressors have specific pressure and temperature limitations, both on the suction and discharge sides. Depending on the project requirements, such as the desired storage pressure and temperature conditions, the selected centrifugal compressor should be capable of operating within the specified range. Operating beyond the design limits can lead to reduced efficiency, increased risks of failures, and compromised reliability.
Compression Efficiency: While centrifugal compressors are generally efficient, the compression efficiency can decrease at higher compression ratios or when handling certain gases like CO2. It’s essential to consider the required compression ratio and efficiency targets for the specific CO2 compression and storage application. Oversizing or undersizing the compressor can impact the overall system performance and reliability.
System Integration and Controls: Centrifugal compressors need to be properly integrated into the overall CO2 compression and storage system, considering the interconnections, control strategies, and safety measures. Inadequate integration or insufficient control systems can lead to operational issues, reduced reliability, and increased risks of failures or safety incidents.
Environmental Considerations: Underground CO2 storage requires careful consideration of environmental factors, such as geological formations and potential risks of CO2 leakage. The design of the compression and storage system should address these environmental concerns to ensure long-term reliability and mitigate any adverse impacts on the surrounding ecosystem.
Maintenance and Accessibility: Centrifugal compressors, like any mechanical equipment, require regular maintenance and inspections to ensure their continued reliability. Accessibility for maintenance and repair should be considered during the design phase to minimize downtime and optimize the overall operational efficiency of the CO2 compression and storage system.
By understanding and addressing these limitations in engineering and design, it is possible to optimize the reliability, mitigate critical risks, and minimize failures when using centrifugal compressors for compressing and storing CO2 in the oil, gas, and petrochemical industries. Careful planning, adherence to industry standards, and continuous monitoring are essential to overcome these limitations and ensure the long-term success of such systems.
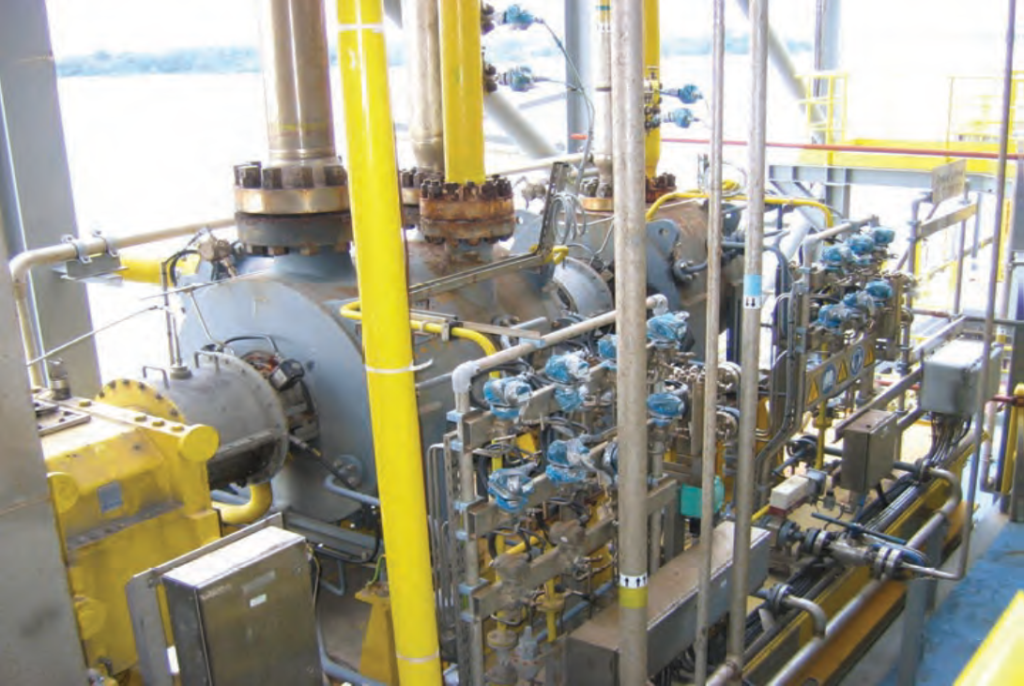
WHY, WHEN, WHERE, WHAT, WHICH, HOW TO USE CENTRIFUGAL COMPRESSORS IN CCS
WHY Use Centrifugal Compressors:
- Environmental Benefits: Compressing and storing CO2 underground can help mitigate greenhouse gas emissions, reduce carbon footprint, and contribute to combating climate change.
- Reliability and Safety: Centrifugal compressors offer high efficiency and reliability, ensuring proper compression and storage of CO2, minimizing the risk of leaks or failures.
- Industry Compliance: Many industries, including oil, gas, and petrochemical, are increasingly under pressure to reduce carbon emissions. Using centrifugal compressors for CO2 storage helps meet regulatory requirements and environmental standards.
WHEN to Use Centrifugal Compressors:
- Existing Plants: Retrofitting existing plants with centrifugal compressors for CO2 compression and storage can be a viable option to reduce emissions and enhance environmental sustainability.
- New Projects: Incorporating centrifugal compressors into the design of new projects allows for a holistic approach to environmental mitigation and long-term reliability.
WHERE to Use Centrifugal Compressors:
- Oil, Gas, and Petrochemical Industries: These industries often generate significant amounts of CO2 as a byproduct. Implementing centrifugal compressors in these sectors enables efficient compression and safe storage of CO2 underground.
WHAT Centrifugal Compressors Provide:
- High Efficiency: Centrifugal compressors offer high compression efficiency, minimizing energy consumption and reducing operational costs.
- Compact Design: Their compact design makes them suitable for installations where space is limited, such as offshore platforms or existing industrial facilities.
- Wide Operating Range: Centrifugal compressors can handle varying gas flows and pressures effectively, accommodating fluctuating CO2 production rates or changing storage requirements.
WHICH Centrifugal Compressors to Choose:
- Consideration of Requirements: Select a centrifugal compressor model that meets the specific project requirements, including gas composition, pressure and temperature ranges, and compatibility with the storage environment.
- Reliability and Maintenance: Opt for centrifugal compressors from reputable manufacturers known for their reliability, and ensure accessibility for maintenance and repairs.
HOW to Use Centrifugal Compressors:
- Design Considerations: Properly integrate the centrifugal compressors into the overall CO2 compression and storage system, considering interconnections, control strategies, and safety measures.
- Material Selection: Select materials that are compatible with CO2 and storage conditions to mitigate corrosion risks and ensure long-term reliability.
- Monitoring and Maintenance: Establish regular maintenance and inspection protocols to ensure the continued reliability of the centrifugal compressors and the overall CO2 compression and storage system.
- Environmental Risk Mitigation: Carefully assess and address environmental factors, such as geological formations and potential CO2 leakage risks, during the design and implementation of the compression and storage system.
By adhering to these considerations, using centrifugal compressors for CO2 compression and storage can effectively contribute to environmental sustainability, enhance reliability, and minimize critical risks and failures in the oil, gas, and petrochemical industries.
PROCEDURES, ACTIONS, STUDIES, MITIGATIONS, RECOMMENDATIONS USING CENTRIFUGAL COMPRESSORS IN CCS
Procedures and Actions:
a. Feasibility Study: Conduct a comprehensive feasibility study to assess the technical, economic, and environmental viability of implementing centrifugal compressors for CO2 compression and storage. This study should include site-specific factors, project scope, and potential risks.
b. Engineering Design: Develop a detailed engineering design that encompasses compressor sizing, materials selection, safety measures, control systems, and integration into the overall CO2 compression and storage system.
c. Environmental Impact Assessment: Perform an environmental impact assessment to identify potential risks and impacts associated with underground CO2 storage, ensuring compliance with regulations and mitigation of environmental concerns.
d. Safety and Risk Analysis: Conduct a thorough safety and risk analysis, including hazard identification, risk assessment, and implementation of risk mitigation measures to ensure the safe operation of the compressors and storage system.
e. Regulatory Compliance: Ensure compliance with relevant local, regional, and national regulations pertaining to CO2 compression, storage, and environmental standards.
Studies and Research:
a. Geological Studies: Conduct geological studies to identify suitable underground storage sites for CO2, considering factors such as geology, porosity, permeability, and sealing properties.
b. Gas Composition Analysis: Analyze the CO2 gas composition, including impurities and contaminants, to determine their potential impact on compressor performance, material compatibility, and storage integrity.
c. Performance Studies: Conduct performance studies to evaluate the efficiency, capacity, and reliability of centrifugal compressors under various operating conditions, ensuring they meet the project requirements.
Mitigations and Recommendations:
a. Corrosion Mitigation: Implement corrosion mitigation strategies such as material selection, coatings, and corrosion inhibitors to prevent damage to the compressor components caused by CO2 and its impurities.
b. Surge Protection: Incorporate surge protection systems to prevent compressor surge, a condition that can lead to pressure fluctuations and potential damage. Proper control systems and surge detection mechanisms are essential.
c. Maintenance and Monitoring: Establish regular maintenance and monitoring protocols to ensure the continued reliability of the compressors and storage system. This includes routine inspections, performance checks, and preventive maintenance activities.
d. Emergency Response Planning: Develop a comprehensive emergency response plan that outlines procedures for handling any potential incidents, including leaks, equipment failures, or other safety-related issues.
e. Knowledge Sharing and Collaboration: Encourage knowledge sharing and collaboration within the industry to learn from best practices, research findings, and lessons learned from similar CO2 compression and storage projects.
By following these procedures, taking necessary actions, conducting studies, implementing mitigations, and adhering to recommendations, the use of centrifugal compressors for CO2 compression and storage can effectively address environmental issues, enhance reliability, and minimize critical risks and failures in the oil, gas, and petrochemical industries.
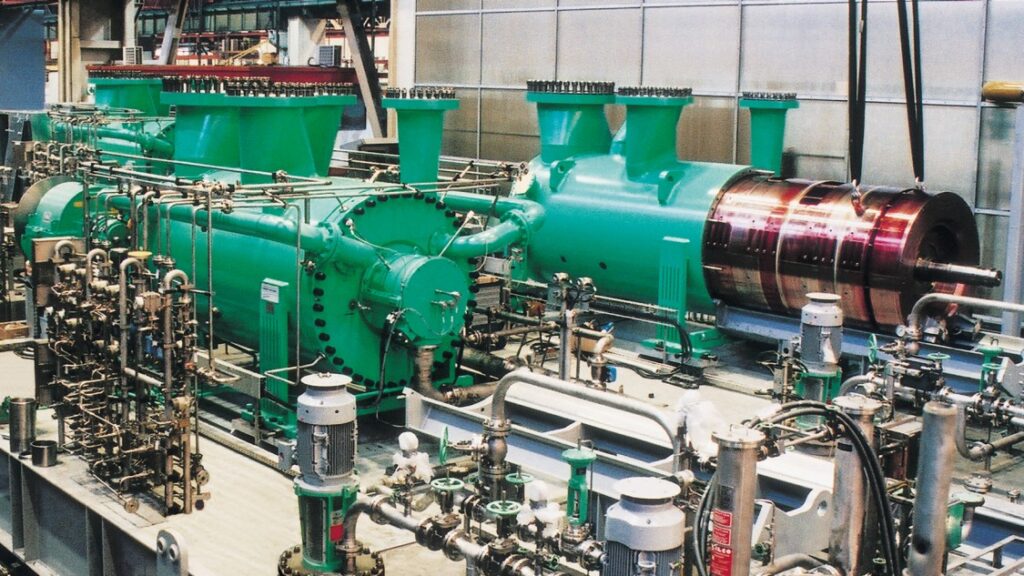