CONSULTING - GAS TURBINES
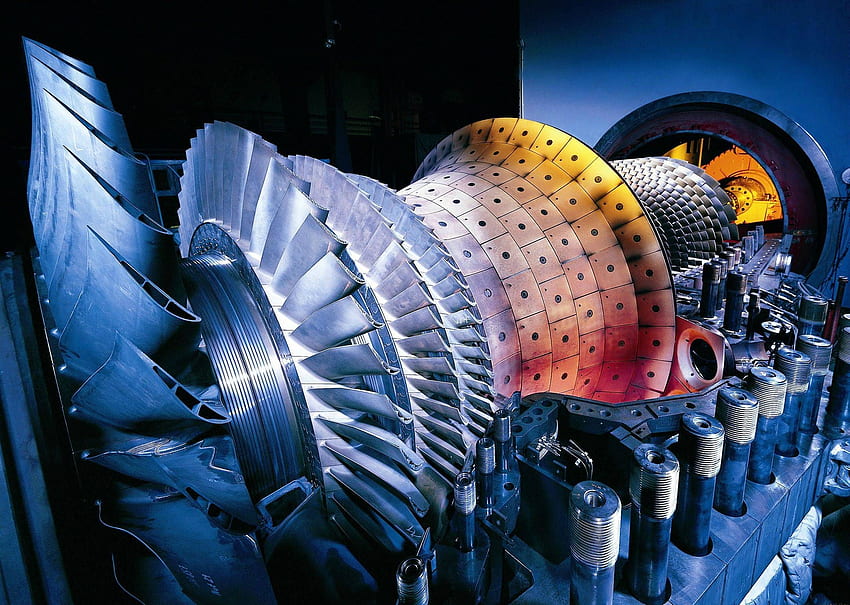
RELIABILITY
MAINTAINABILITY
AVAILABILITY
Gas turbines are complex machines used for various applications such as power generation, aviation, and industrial processes. Reliability is a critical factor in the performance of gas turbines as they are expected to operate continuously and efficiently for long periods of time.
To achieve good reliability in gas turbines, several factors need to be considered during design, manufacturing, and operation. Some of these factors include:
Material selection: The materials used in the manufacture of gas turbines should have high strength, resistance to corrosion, and high-temperature capabilities.
Robust design: The gas turbine should be designed to withstand various stresses and strains during operation, including thermal expansion, vibration, and mechanical shock.
Quality manufacturing: The manufacturing process of gas turbines should be of high quality and free from defects that could affect performance or reliability. The use of advanced manufacturing techniques such as additive manufacturing can improve the quality and reliability of gas turbines.
Regular maintenance: Regular maintenance and inspection of gas turbines are critical to ensuring their reliable performance. This includes routine checks of critical components such as bearings, seals, and blades to identify any signs of wear or damage.
Monitoring and control: Modern gas turbines are equipped with advanced monitoring and control systems that can detect and alert operators of any potential issues before they lead to a failure.
In summary, good reliability in gas turbines requires a combination of robust design, high-quality materials and manufacturing, regular maintenance, and advanced monitoring and control systems. By ensuring these factors are addressed, gas turbine manufacturers can produce machines that operate efficiently and reliably for many years.
Maintainability refers to the ease with which a machine can be serviced, repaired, and maintained to ensure optimal performance and prevent downtime. In gas turbines, good maintainability is critical to minimizing maintenance costs and maximizing uptime.
To achieve good maintainability in gas turbines, several factors need to be considered during design, manufacturing, and operation. Some of these factors include:
Access to components: The gas turbine should be designed to provide easy access to critical components that require maintenance or repair. This includes the use of removable panels, doors, and covers that can be easily opened to access components.
Standardization: The use of standardized parts and components can simplify maintenance and repair procedures and reduce the time and cost of sourcing replacement parts.
Modular design: A modular design approach can allow for easy replacement of individual components without the need for extensive disassembly of the gas turbine.
Serviceability: The gas turbine should be designed to minimize the time and effort required to service and repair components. This includes the use of quick-release connectors, easy-to-use tooling, and intuitive service instructions.
Remote monitoring and diagnosis: Advanced monitoring and diagnostic systems can provide real-time data on the performance and condition of the gas turbine, enabling early detection of potential issues and minimizing downtime.
In summary, good maintainability in gas turbines requires a combination of easy access to components, standardization, modular design, serviceability, and remote monitoring and diagnosis. By ensuring these factors are addressed, gas turbine manufacturers can produce machines that are easy to service and maintain, maximizing uptime and reducing maintenance costs
Availability refers to the percentage of time that a machine or system is available for use. In gas turbines, good availability is critical to ensuring that the machine is operational when it is needed and can perform its intended function reliably and efficiently.
To achieve good availability in gas turbines, several factors need to be considered during design, manufacturing, and operation. Some of these factors include:
Robust design: The gas turbine should be designed to withstand various stresses and strains during operation, including thermal expansion, vibration, and mechanical shock.
Quality manufacturing: The manufacturing process of gas turbines should be of high quality and free from defects that could affect performance or reliability. The use of advanced manufacturing techniques such as additive manufacturing can improve the quality and reliability of gas turbines.
Regular maintenance: Regular maintenance and inspection of gas turbines are critical to ensuring their reliable performance. This includes routine checks of critical components such as bearings, seals, and blades to identify any signs of wear or damage.
Spare parts availability: The availability of spare parts is critical to minimizing downtime in the event of a failure. Gas turbine manufacturers should maintain an inventory of spare parts and ensure that they are readily available when needed.
Remote monitoring and diagnosis: Advanced monitoring and diagnostic systems can provide real-time data on the performance and condition of the gas turbine, enabling early detection of potential issues and minimizing downtime.
In summary, good availability in gas turbines requires a combination of robust design, quality manufacturing, regular maintenance, spare parts availability, and remote monitoring and diagnosis. By ensuring these factors are addressed, gas turbine manufacturers can produce machines that are reliable, efficient, and available when needed.
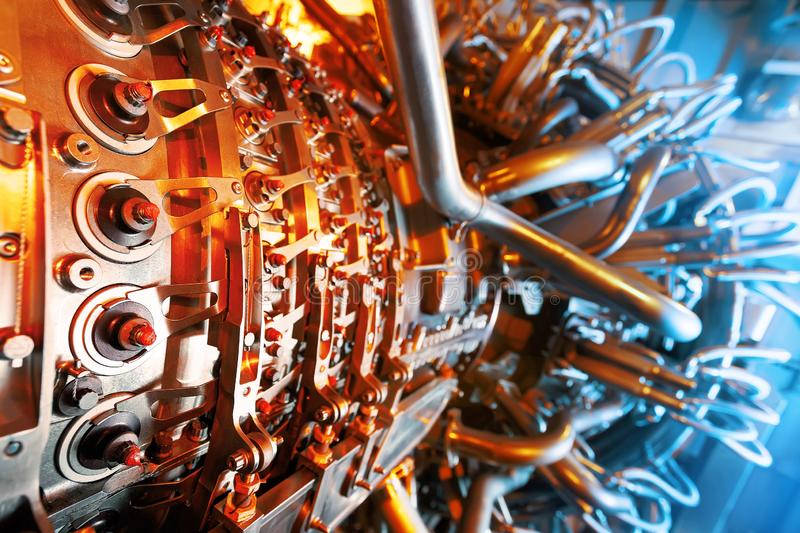
SAFETY
QUALITY
EFFICIENCY / PERFORMANCE
DESIGN & ENGINEERING
Safety is a critical factor in the design, manufacture, and operation of gas turbines. Gas turbines are complex machines that operate at high temperatures and pressures and can pose significant safety risks if not designed, manufactured, and operated properly.
To achieve good safety in gas turbines, several factors need to be considered during design, manufacturing, and operation. Some of these factors include:
Robust design: The gas turbine should be designed to withstand various stresses and strains during operation, including thermal expansion, vibration, and mechanical shock. The design should also consider safety features such as automatic shutdown systems in the event of a failure or safety-critical conditions.
Quality manufacturing: The manufacturing process of gas turbines should be of high quality and free from defects that could affect performance or safety. The use of advanced manufacturing techniques such as additive manufacturing can improve the quality and safety of gas turbines.
Compliance with safety regulations: Gas turbine manufacturers must comply with safety regulations and standards, such as those set by OSHA, EPA, and other relevant regulatory bodies. This includes ensuring that the gas turbine is designed and manufactured to meet safety requirements and that it is installed, operated, and maintained in accordance with safety regulations.
Safety training and education: Operators and maintenance personnel should receive adequate safety training and education to ensure they are aware of the potential safety risks associated with gas turbines and are familiar with the safety procedures and protocols.
Emergency response planning: Gas turbine operators should have a comprehensive emergency response plan in place to address safety incidents such as fires, explosions, or releases of hazardous materials.
In summary, good safety in gas turbines requires a combination of robust design, quality manufacturing, compliance with safety regulations, safety training and education, and emergency response planning. By ensuring these factors are addressed, gas turbine manufacturers can produce machines that operate safely and minimize the risk of safety incidents.
Quality control is a critical aspect of gas turbine design and manufacturing, ensuring that the gas turbine meets the required specifications and performs as intended. Good quality control practices in gas turbines involve the following:
Quality Management System: A robust quality management system (QMS) is essential for ensuring the quality of gas turbines. A QMS outlines the procedures, processes, and policies required to ensure that the gas turbine meets the necessary quality standards.
Testing and Inspection: Comprehensive testing and inspection are critical to ensure that the gas turbine meets the required specifications. This includes inspecting critical components such as blades, vanes, and bearings, and conducting performance tests to ensure the gas turbine operates within the required parameters.
Documentation: Accurate and comprehensive documentation is necessary to ensure that the gas turbine is manufactured and tested correctly. This includes maintaining records of manufacturing and testing procedures, inspection reports, and test results.
Supplier Management: The quality of components used in the gas turbine is critical to its overall quality. Suppliers of critical components must be selected and managed effectively to ensure that they meet the required quality standards.
Continuous Improvement: Continuous improvement is essential to ensure that the gas turbine remains competitive and meets evolving market requirements. This involves identifying areas for improvement and implementing changes to the design, manufacturing, or testing processes to address these areas.
In summary, good quality control practices in gas turbines require a combination of a robust quality management system, comprehensive testing and inspection, accurate documentation, effective supplier management, and continuous improvement. By ensuring these factors are addressed, gas turbine manufacturers can produce machines that meet the required quality standards, operate reliably, and are competitive in the market
Efficiency and performance are critical factors in the design and operation of gas turbines. The efficiency of a gas turbine is the measure of how effectively it converts fuel energy into mechanical energy. The performance of a gas turbine is a measure of its ability to generate power and operate efficiently over a range of conditions.
To achieve good efficiency and performance in gas turbines, several factors need to be considered during design, manufacturing, and operation. Some of these factors include:
Aerodynamics: Gas turbines rely on the flow of air and gases through their components to generate power. Therefore, the design of gas turbine components, such as blades and vanes, must be optimized to ensure efficient airflow and minimize energy losses.
Combustion efficiency: The combustion process in a gas turbine must be efficient to maximize the energy extracted from the fuel. This requires careful design of the combustion chamber and fuel injection system to ensure efficient and complete combustion.
Material selection: The materials used in the construction of gas turbine components must be carefully selected to ensure they can withstand the high temperatures and pressures encountered during operation. Advanced materials such as ceramics and composites can improve efficiency and performance by reducing weight and increasing durability.
Control systems: Advanced control systems can optimize gas turbine performance by monitoring and adjusting the operation of key components such as fuel injection systems, variable geometry components, and cooling systems.
Regular maintenance: Regular maintenance and inspection of gas turbines are critical to ensuring their reliable performance. This includes routine checks of critical components such as bearings, seals, and blades to identify any signs of wear or damage.
In summary, good efficiency and performance in gas turbines require a combination of aerodynamic design, efficient combustion, appropriate material selection, advanced control systems, and regular maintenance. By ensuring these factors are addressed, gas turbine manufacturers can produce machines that are efficient, reliable, and competitive in the market.
The design and engineering of gas turbines are critical to ensuring their efficient and reliable operation. Good design and engineering practices in gas turbines involve the following:
Performance optimization: Gas turbine design and engineering must be optimized to achieve the desired performance requirements. This includes selecting the appropriate size and configuration of the gas turbine, as well as optimizing its aerodynamics, combustion efficiency, and materials selection.
Robustness and reliability: Gas turbines operate under high temperatures, pressures, and stresses. Therefore, the design and engineering must ensure that the gas turbine is robust and reliable under a range of operating conditions. This includes selecting appropriate materials, designing effective cooling systems, and ensuring the structural integrity of the gas turbine.
Environmental considerations: Gas turbine design and engineering must take into account environmental considerations such as emissions and noise. This includes designing efficient combustion systems that minimize emissions, and incorporating noise-reducing features into the gas turbine design.
Advanced technology: Gas turbine design and engineering must incorporate the latest technology and advancements to improve performance, efficiency, and reliability. This includes incorporating advanced materials, control systems, and digital technologies such as simulation and machine learning.
Manufacturing considerations: Gas turbine design and engineering must take into account the manufacturing process to ensure that the gas turbine can be produced efficiently and cost-effectively. This includes designing components that are easy to manufacture and assemble, and selecting appropriate manufacturing processes.
In summary, good design and engineering practices in gas turbines require a combination of performance optimization, robustness and reliability, environmental considerations, advanced technology, and manufacturing considerations. By ensuring these factors are addressed, gas turbine manufacturers can produce machines that are efficient, reliable, and competitive in the market.
CRITICAL FACTORS
Gas turbines are complex machines that convert the energy stored in fuel into mechanical energy, which can be used for a variety of purposes, including generating electricity, powering aircraft, and propelling ships. Some critical factors to consider when discussing gas turbines are:
Efficiency: The efficiency of a gas turbine is a measure of how effectively it can convert fuel into useful work. A higher efficiency means less fuel is wasted, resulting in lower operating costs and reduced emissions.
Power output: The power output of a gas turbine is an important consideration, as it determines the amount of energy that can be generated or the speed at which an aircraft can travel.
Fuel type: The type of fuel used in a gas turbine can have a significant impact on its performance, emissions, and maintenance requirements. Common fuel types include natural gas, diesel, and kerosene.
Combustion technology: The combustion technology used in a gas turbine can affect its efficiency, emissions, and maintenance requirements. Some gas turbines use a simple cycle design, while others use a combined cycle design that incorporates a heat recovery system.
Operating conditions: Gas turbines are designed to operate under specific conditions, such as temperature, pressure, and humidity. Deviations from these conditions can affect their performance and increase the risk of mechanical failure.
Maintenance requirements: Gas turbines require regular maintenance to ensure they operate efficiently and safely. Maintenance tasks can include cleaning, lubrication, and component replacement.
Environmental impact: Gas turbines can have a significant environmental impact due to their emissions. Factors to consider include the type and amount of pollutants released, as well as the impact on local air quality and climate change.
Overall, gas turbines are complex machines that require careful consideration of many factors to ensure they operate efficiently, safely, and with minimal environmental impact
Here are some critical factors to consider when designing and engineering gas turbines for high reliability:
Material selection: Use high-quality materials that are resistant to corrosion and can withstand high temperatures and stress.
Operational environment: Consider the environmental factors such as ambient temperature, humidity, and the presence of pollutants that may impact the performance and durability of the gas turbine.
System design: Optimize the system design to ensure that all components are properly sized and integrated to work together efficiently, with no single point of failure.
Control system: Implement a reliable control system that monitors and regulates the performance of the gas turbine, including temperature, pressure, and vibration.
Maintenance requirements: Design the gas turbine with maintenance in mind, making sure that components can be easily accessed and serviced as needed.
Testing and validation: Conduct rigorous testing and validation of all components and systems to ensure they meet or exceed the required reliability standards.
Operating procedures: Develop and implement detailed operating procedures to ensure that the gas turbine is operated safely and efficiently.
Risk management: Identify potential risks and develop contingency plans to minimize the impact of any failures or disruptions.
Training and education: Ensure that operators and maintenance personnel are properly trained and educated to operate and maintain the gas turbine safely and effectively.
By considering these critical factors during the engineering and design process of gas turbines, it is possible to achieve high reliability, availability, and maintainability, ultimately leading to improved safety and reduced unscheduled shutdowns.
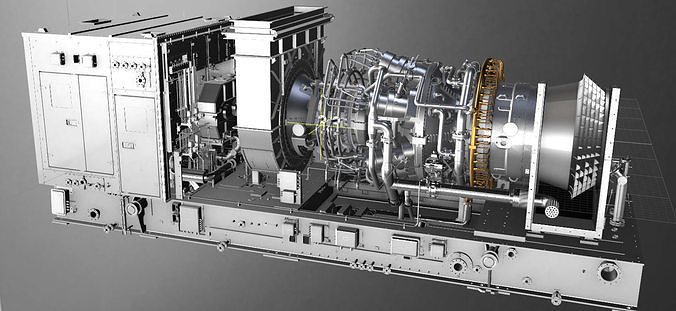
Index - Gas Turbines
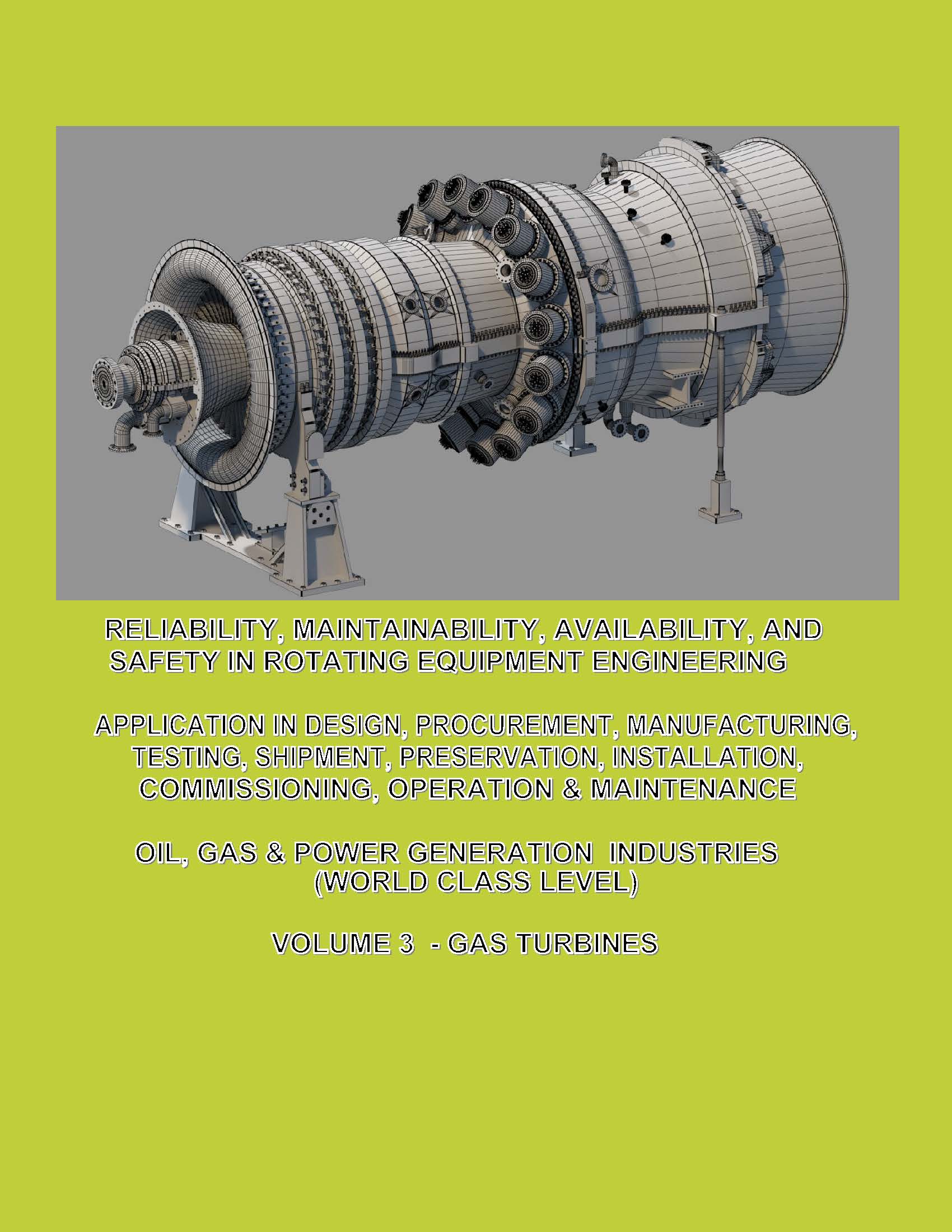
Cover - eBook - Gas Turbines
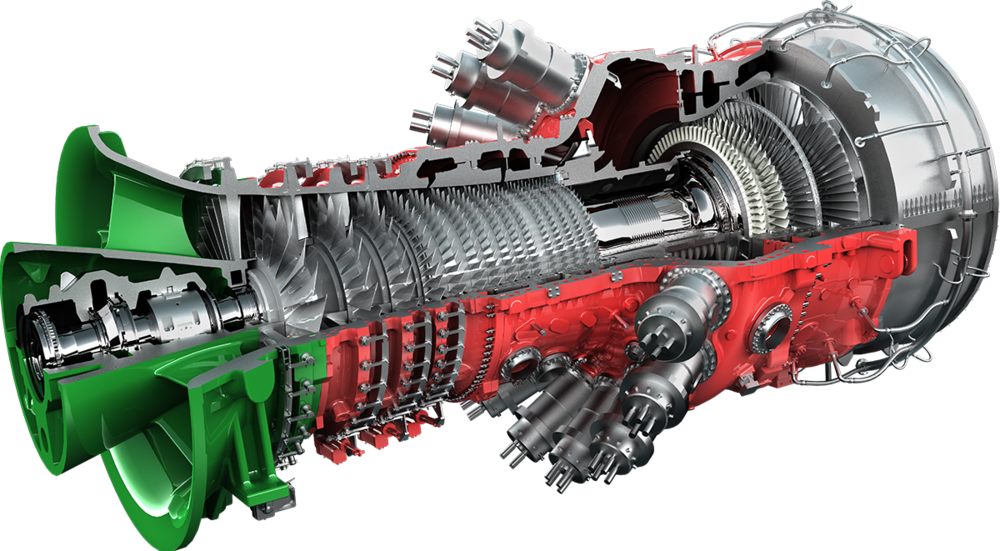
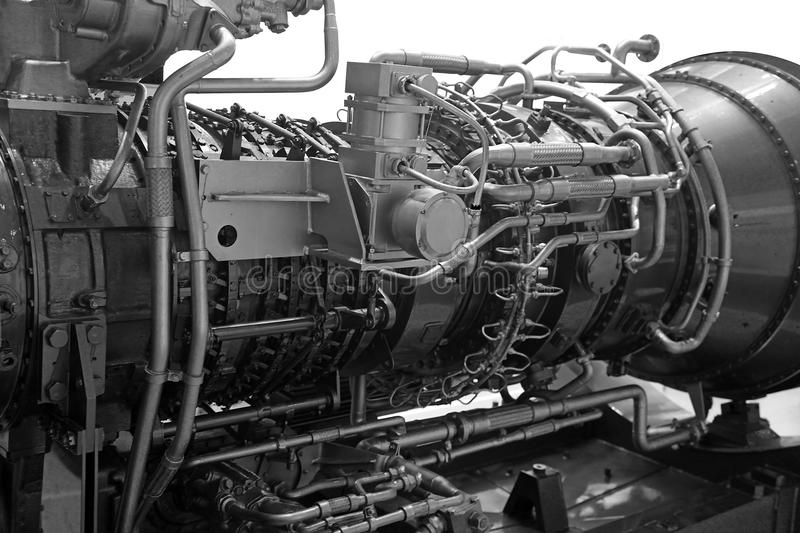