COOLING IN GAS TURBINES TO IMPROVE THERMAL EFFICIENCY & POWER DENSITY
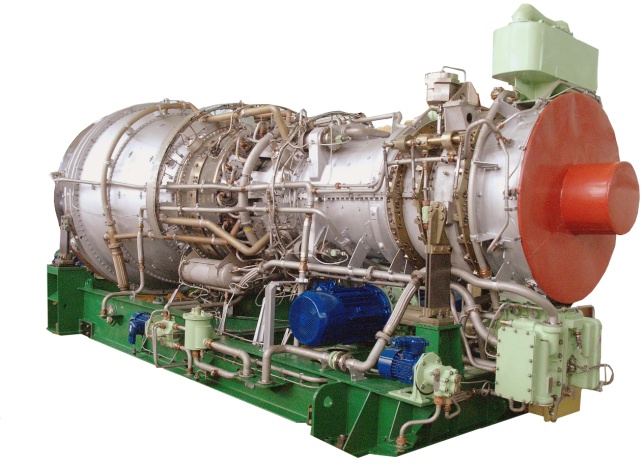
LIMITATIONS IN ENGINEERING & DESIGN USING COOLING IN GAS TURBINES
Heat Transfer Limitations: Cooling systems aim to remove heat from critical turbine components, but there are limits to the heat transfer rates that can be achieved. Achieving higher thermal efficiency and power density requires efficient heat transfer within the cooling channels and effective cooling of hot spots. Optimization of cooling channel geometries, materials, and coolant flow rates is necessary to maximize heat transfer performance.
Cooling Air Extraction and Power Loss: Extracting cooling air from the compressor reduces the mass flow available for combustion and power production, leading to a potential reduction in thermal efficiency and power density. It is crucial to strike a balance between cooling requirements and the impact on power generation efficiency to optimize overall system performance.
Pressure Drop and Cooling Air Losses: Cooling systems introduce pressure losses due to the flow resistance in cooling channels, connectors, and nozzles. These pressure losses can result in a decrease in overall system efficiency and power density. Designing streamlined cooling channels, optimizing flow distribution, and minimizing pressure losses are important to mitigate these limitations.
Cooling System Complexity: Cooling systems in gas turbines can be complex due to the integration of various components, including cooling channels, impingement nozzles, and heat exchangers. This complexity can introduce challenges in terms of manufacturing feasibility, maintenance accessibility, and potential for increased failure points. Simplifying the cooling system design while ensuring effective heat transfer is essential to enhance reliability and availability.
Erosion and Corrosion: Cooling systems, particularly those involving jet impingement, can subject turbine components to erosion and corrosion. The high-velocity coolant jets and the presence of corrosive agents in the coolant can degrade the integrity of surfaces over time, leading to potential failures. Employing erosion- and corrosion-resistant materials, surface coatings, and regular maintenance protocols can help mitigate these limitations.
Material Compatibility: Cooling systems require materials that can withstand high temperatures, corrosive environments, and erosion effects. Ensuring compatibility between cooling fluids and materials is crucial to maintain long-term reliability. Material selection and ongoing research into advanced materials with improved compatibility characteristics are necessary to address these limitations.
System Monitoring and Maintenance: Cooling systems require robust monitoring and maintenance to ensure their ongoing performance and reliability. This includes regular inspections, cleaning, and assessment of system components, as well as implementation of predictive maintenance practices. Ensuring easy access to cooling channels and integration of monitoring sensors can aid in timely detection of potential failures.
By addressing these limitations through advanced engineering techniques, computational modeling, material research, and collaboration between turbine manufacturers, cooling system designers, and research institutions, it is possible to improve thermal efficiency, power density, reliability, availability, safety factors, and mitigate environmental risks in gas turbines used in power generation, oil, and gas industries. Continual research and development efforts are vital to push the boundaries of cooling system design and optimize their performance in gas turbine applications.
WHY, WHEN, WHERE, WHAT, WHICH, AND HOW TO APPLY COOLING IN GAS TURBINES
Why Cooling is Necessary: Gas turbines operate at high temperatures, and cooling is essential to prevent components from overheating, maintain structural integrity, and extend their lifespan. Cooling helps improve thermal efficiency, power density, and overall performance while reducing the risk of failures and environmental impacts.
When Cooling is Applied: Cooling is applied continuously during the operation of gas turbines. It is particularly critical during high-load conditions or when the ambient temperature is high, as these conditions increase the thermal stress on turbine components. Cooling should be designed to meet the specific operational requirements and environmental conditions of the gas turbine.
Where Cooling is Applied: Cooling is applied to critical components such as turbine blades, vanes, combustor liners, transition pieces, and hot gas path components. These areas experience the highest temperatures and require effective cooling to prevent thermal damage and ensure reliable operation. Cooling channels, impingement nozzles, or other cooling methods are strategically placed in these locations.
What Cooling Methods to Use: Various cooling methods can be employed, including jet impingement, film cooling, convective cooling, internal cooling passages, or combinations of these techniques. The choice of cooling method depends on factors such as component design, material properties, operating conditions, and performance requirements. A combination of methods may be used to optimize cooling efficiency.
Which Cooling Technologies to Employ: Advanced cooling technologies, such as additive manufacturing for complex cooling channel geometries, thermal barrier coatings for heat insulation, and advanced cooling fluids with improved properties, can be employed to enhance cooling effectiveness, efficiency, and component durability. Selecting the appropriate cooling technologies involves evaluating their benefits, limitations, and compatibility with the gas turbine system.
How to Implement Cooling Systems: The implementation of cooling systems involves a comprehensive approach, including design, manufacturing, installation, monitoring, and maintenance. It requires collaboration between gas turbine manufacturers, cooling system designers, and research institutions. Computational fluid dynamics (CFD) simulations, prototype testing, and real-world data analysis aid in optimizing cooling system design and performance.
Additionally, it is crucial to consider the impact of cooling on the overall system, including thermal efficiency, power density, environmental factors, and safety. Balancing the cooling requirements with power generation efficiency is essential to maximize the overall performance of gas turbines.
Proper monitoring and maintenance of the cooling system, including regular inspections, cleaning, and predictive maintenance practices, are vital to ensure continued effectiveness and reliability.
Applying cooling in gas turbines involves a multidisciplinary approach, incorporating engineering expertise, materials science, fluid dynamics, and system integration. It is essential to stay updated with advancements in cooling technologies, research findings, and industry best practices to continually improve cooling efficiency and optimize gas turbine performance in power generation, oil, and gas industries.
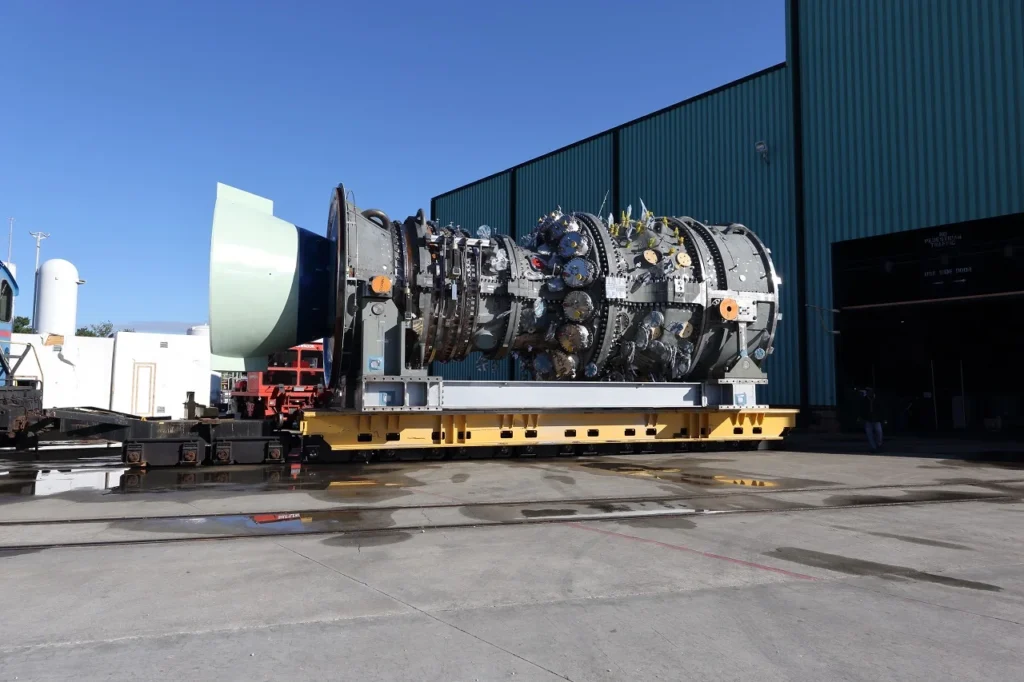
PROCEDURES, ACTIONS, STUDIES, MITIGATION, RECOMMENDATIONS TO APPLY COOLING IN GAS TURBINES
Comprehensive Design Studies: Conduct detailed design studies using computational fluid dynamics (CFD) simulations to optimize cooling system geometries, coolant flow distribution, and component materials. Evaluate the impact of different cooling methods on thermal efficiency, power density, and component reliability.
Experimental Testing: Perform experimental testing on scaled models or prototype components to validate the effectiveness of cooling methods, identify potential limitations, and validate CFD simulation results. This testing helps refine cooling system designs and understand the thermal behavior of turbine components under realistic conditions.
Material Research and Development: Invest in research and development efforts to develop advanced materials that can withstand high temperatures, erosion, corrosion, and fatigue associated with cooling systems. Explore materials with enhanced thermal properties, durability, and compatibility with cooling fluids to improve component reliability and longevity.
Enhanced Heat Transfer Techniques: Investigate innovative heat transfer enhancement techniques such as turbulators, ribbed channels, and internal surface coatings to improve cooling effectiveness within the turbine components. These techniques can enhance heat transfer rates, reduce hot spots, and improve overall thermal efficiency.
Optimized Cooling Channel Geometries: Utilize additive manufacturing techniques to fabricate complex cooling channel geometries that facilitate efficient coolant flow, improve heat transfer, and mitigate thermal stresses. Tailor the channel shapes and sizes to match the cooling requirements of specific components, considering both cooling effectiveness and manufacturability.
Real-time Monitoring and Control: Implement advanced monitoring and control systems to continuously monitor the performance of cooling systems, including coolant flow rates, pressures, temperatures, and component conditions. Real-time monitoring enables early detection of potential issues, allowing for timely intervention and maintenance actions to prevent failures and improve availability.
Predictive Maintenance: Implement predictive maintenance strategies based on sensor data, performance monitoring, and data analytics. Utilize machine learning and predictive algorithms to identify potential cooling system or component failures in advance and schedule maintenance activities accordingly. This approach helps reduce downtime and enhances overall system reliability.
Environmental Considerations: Consider the environmental impact of cooling methods and fluids used in gas turbines. Evaluate the potential for using environmentally friendly and sustainable cooling fluids. Additionally, assess the energy requirements and associated environmental footprint of cooling systems to optimize cooling efficiency while minimizing environmental risks.
Collaboration and Knowledge Sharing: Foster collaboration among gas turbine manufacturers, cooling system designers, research institutions, and industry experts. Share knowledge, best practices, and lessons learned to collectively advance cooling technologies and improve their application in industrial plants and new projects.
By implementing these procedures, actions, studies, mitigation measures, and recommendations, it is possible to enhance cooling effectiveness, thermal efficiency, power density, reliability, availability, safety factors, and mitigate environmental risks and failures in gas turbines applied in power generation, oil, and gas industries. Continued research, development, and innovation in cooling technologies will further drive improvements in gas turbine performance and sustainability.
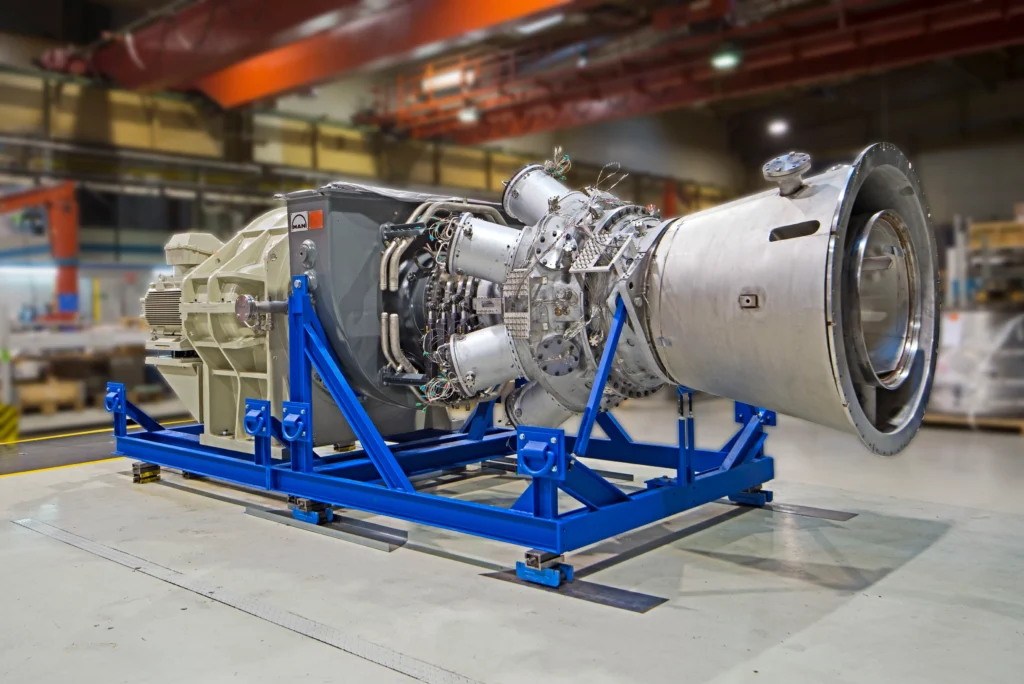