EMISSION REDUCTION METHODS IN GAS TURBINES
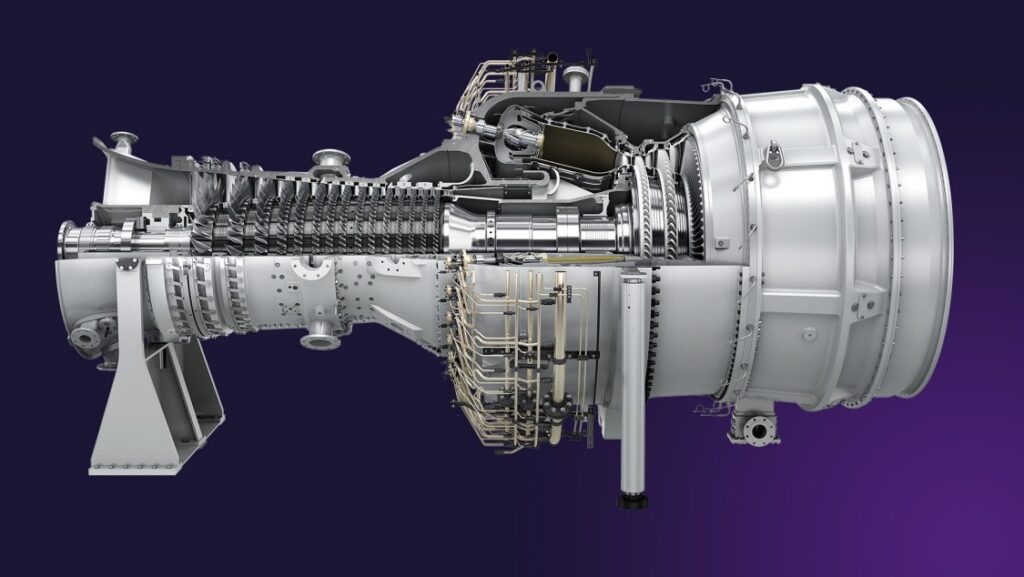
DIFFERENT EMISSION REDUCTION METHODS BEING APPLICABLE IN GAS TURBINES
Water Injection:
- Water injection involves injecting water into the combustion process to reduce peak flame temperatures and lower NOx emissions.
- It can improve the stability and efficiency of combustion, reducing the risk of flame instability and combustion-related issues.
- Water injection can help mitigate the formation of harmful pollutants, but it may increase the potential for corrosion and fouling in the turbine components.
Steam Injection:
- Steam injection involves introducing steam into the combustion process to lower flame temperatures and control NOx emissions.
- It can enhance combustion stability and reduce NOx formation by absorbing heat energy from the combustion process.
- Steam injection may require additional infrastructure and equipment for steam generation and control, adding complexity to the system.
Selective Catalytic Reduction (SCR):
- SCR is a post-combustion emission reduction method that involves injecting a reducing agent, typically ammonia or urea, into the flue gas stream to convert NOx into nitrogen and water.
- SCR can achieve high NOx reduction efficiency and is commonly used in gas turbines to meet stringent emission regulations.
- Proper SCR system design, including catalyst selection, sizing, and maintenance, is crucial to ensure effective and reliable operation.
Dry Combustors:
- Dry combustors are advanced combustion systems designed to achieve low emissions without the need for water or steam injection.
- These combustors typically incorporate lean-burn or ultra-low NOx technologies to minimize the formation of pollutants during the combustion process.
- Dry combustors offer improved reliability and operational flexibility by eliminating the need for water or steam injection systems.
Other Emission Reduction Methods:
- There are various other emission reduction methods used in gas turbines, such as low-NOx burners, lean premixing, and advanced control systems.
- Low-NOx burners optimize the combustion process to achieve lower emissions by controlling fuel-air mixing and flame stability.
- Lean premixing involves pre-mixing the fuel and air to achieve more uniform combustion and lower peak flame temperatures.
- Advanced control systems use sophisticated algorithms and sensors to optimize combustion parameters and maintain emissions within acceptable limits.
It’s important to note that the selection of emission reduction methods depends on various factors such as regulatory requirements, fuel characteristics, turbine design, and operational considerations. Careful engineering and design considerations are necessary to ensure the chosen method is compatible with the specific gas turbine application and meets the desired emission reduction targets while maintaining reliability and safety in power generation, oil, and gas industries.
LIMITATIONS IN ENGINEERING & DESIGN OF DIFFERENT EMISSION REDUCTION METHODS FOR GAS TURBINES
Water Injection:
- Limitations in water injection include the potential for corrosion and erosion in turbine components due to the presence of water in the combustion process.
- Proper material selection, coatings, and maintenance practices are necessary to mitigate these effects.
- Water injection may require additional infrastructure and equipment for water storage, treatment, and injection, adding complexity and maintenance requirements to the system.
Steam Injection:
- Steam injection can impose limitations such as increased operational complexity due to the need for steam generation and control systems.
- The availability and quality of steam, including pressure, temperature, and moisture content, must be carefully considered for optimal performance.
- Steam injection systems require regular maintenance to ensure proper operation and prevent issues such as steam nozzle fouling.
Selective Catalytic Reduction (SCR):
- SCR systems have limitations related to catalyst performance and durability.
- Catalyst deactivation can occur due to factors such as poisoning, fouling, or thermal degradation, requiring periodic catalyst replacement or regeneration.
- The design and integration of SCR systems must consider factors such as flue gas temperature, space requirements, and proper mixing of reducing agents for effective NOx reduction.
Dry Combustors:
- Dry combustors may have limitations in achieving ultra-low emissions under all operating conditions.
- Combustion stability and flame holding can be challenging, especially during low-load or turndown conditions.
- Dry combustors may require advanced control strategies and monitoring systems to ensure reliable operation across a wide range of operating conditions.
Other Emission Reduction Methods:
- Other emission reduction methods, such as low-NOx burners and lean premixing, may have limitations in terms of their effectiveness in achieving ultra-low emissions.
- These methods often require careful tuning and adjustment to maintain stable combustion and minimize the risk of flame instability or combustion-related issues.
- The design and integration of advanced control systems for emission reduction must consider the complexity of algorithms, sensor accuracy, and system response time.
It is crucial to thoroughly evaluate and understand the limitations of each emission reduction method during the engineering and design phase of gas turbines. Proper consideration of these limitations will help ensure the selected method is compatible with the specific application, meet emission reduction targets, and maintain the desired reliability and safety in the power generation, oil, and gas industries. Regular monitoring, maintenance, and optimization practices are essential to address any limitations and maximize the effectiveness of emission reduction systems in gas turbines.
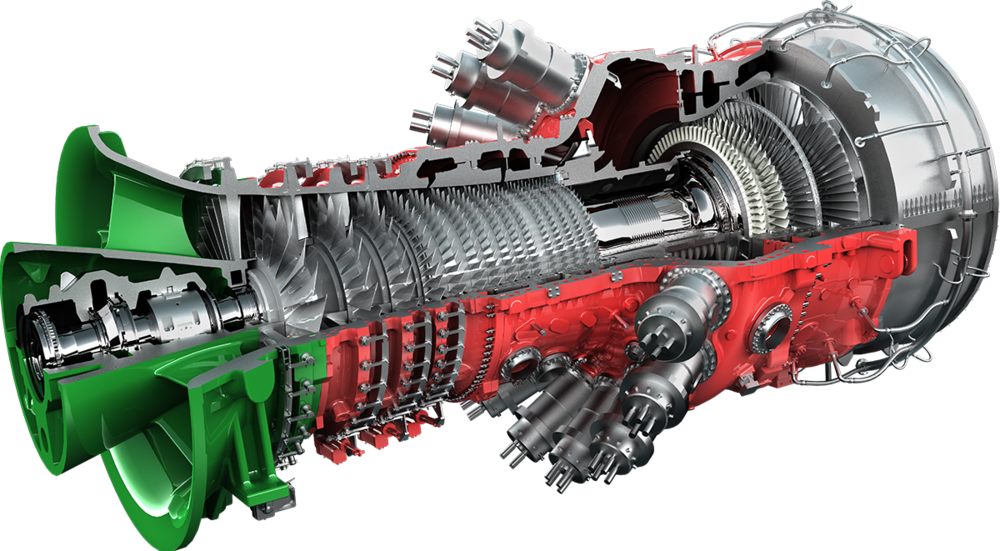
WHY, WHEN, WHERE, WHAT, WHICH AND HOW TO APPLY DIFFERENT EMISSION REDUCTION METHODS IN GAS TURBINES
Why: The main objective of applying emission reduction methods is to comply with environmental regulations, reduce air pollution, and improve the sustainability of operations in the power generation, oil, and gas industries. By reducing emissions, companies can enhance their environmental performance, meet regulatory requirements, and minimize the impact on human health and the environment.
When: The decision to apply emission reduction methods should be made during the design and engineering phase of gas turbine projects. It is essential to consider emission reduction measures early on to ensure proper integration into the system. However, retrofitting existing gas turbines with emission reduction technologies is also possible and can be done when there is a need to meet new emission standards or improve environmental performance.
Where: Emission reduction methods are typically applied in power plants, refineries, and other industrial facilities that utilize gas turbines. These methods can be used in both stationary and mobile applications, depending on the specific industry and operational requirements.
What: The engineering and design of emission reduction methods involve selecting and integrating appropriate technologies and equipment into gas turbine systems. This includes components such as injectors for water or steam injection, catalyst beds for SCR, combustion chambers for dry combustors, and associated control systems. Material selection, system layout, and integration with existing infrastructure are also crucial aspects to consider.
Which: The selection of the emission reduction method depends on various factors, including regulatory requirements, emission reduction targets, gas turbine configuration, fuel type, and operational conditions. Each method has its advantages, limitations, and applicability to different situations. A comprehensive analysis considering factors such as emission reduction efficiency, cost-effectiveness, operational feasibility, and system compatibility is necessary to determine the most suitable method for a specific project.
How: The engineering and design process involves several steps:
- Conducting a thorough emission assessment to understand the specific emission sources, pollutants, and regulatory requirements.
- Evaluating the available emission reduction methods and technologies based on their technical feasibility, effectiveness, and economic viability.
- Performing engineering calculations, simulations, and modeling to determine the system requirements, such as injection rates, catalyst sizing, or combustion chamber design.
- Integrating the selected emission reduction method into the gas turbine system, considering factors such as space availability, compatibility with existing components, and control system integration.
- Conducting pilot tests, prototype validation, and performance optimization to ensure the desired emission reduction levels are achieved while maintaining the reliability and safety of the gas turbine system.
- Regular monitoring, maintenance, and compliance reporting to ensure ongoing effectiveness and adherence to regulatory requirements.
By applying proper engineering and design practices, including thorough assessments, careful selection of methods, and robust integration, the reliability and safety of gas turbines can be improved while achieving significant emission reductions in the power generation, oil, and gas industries. Continuous monitoring and optimization are essential to maintain the performance of emission reduction systems over the operational life of the gas turbine.
PROCEDURES, ACTIONS, STUDIES, MITIGATIONS, RECOMMENDATIONS TO APPLY SEVERAL EMISSION REDUCTION METHODS IN GAS TURBINES
Procedures: a. Conduct an emission assessment: Perform a detailed assessment of the gas turbine’s emission profile to identify the specific pollutants and their concentrations. This assessment will serve as the basis for determining the emission reduction targets and selecting appropriate methods.
b. Evaluate emission reduction methods: Assess the available emission reduction methods, such as water injection, steam injection, SCR, dry combustors, and others. Consider factors such as their efficiency, effectiveness in reducing target pollutants, technical feasibility, and economic viability.
c. System design and integration: Determine the system requirements and design specifications for integrating the selected emission reduction method into the gas turbine system. This includes selecting appropriate components, such as injectors, catalyst beds, combustion chambers, control systems, and associated equipment.
d. Pilot testing and validation: Conduct pilot tests and validation studies to ensure the selected emission reduction method performs as expected. Evaluate the system’s performance, emissions reduction efficiency, and impact on gas turbine operation.
e. Optimization and monitoring: Continuously monitor and optimize the emission reduction system to maintain its effectiveness and reliability. Regularly assess the system’s performance, conduct emission measurements, and implement necessary adjustments to meet regulatory requirements and improve operational efficiency.
Actions: a. Material selection: Select appropriate materials for components exposed to the emission reduction method, considering factors such as corrosion resistance, temperature resistance, and compatibility with the gases involved.
b. Control system integration: Integrate the emission reduction system into the gas turbine control system to ensure seamless operation and effective coordination with other systems. Implement appropriate control strategies to optimize emissions reduction while maintaining safe and reliable operation.
c. Installation and commissioning: Follow proper installation and commissioning procedures to ensure the emission reduction system is correctly installed, calibrated, and tested. Conduct thorough inspections and functional tests to verify the system’s performance and safety.
Studies: a. Computational modeling and simulation: Utilize computational modeling and simulation tools to evaluate the performance and efficiency of different emission reduction methods under various operating conditions. This can help optimize the system design and identify potential issues in advance.
b. Environmental impact assessment: Conduct environmental impact assessments to evaluate the overall impact of the emission reduction methods on air quality, water usage, waste generation, and other environmental factors. This assessment will ensure compliance with regulations and support sustainable decision-making.
Mitigations: a. Monitoring and maintenance: Implement a comprehensive monitoring and maintenance program to regularly inspect, clean, and calibrate the emission reduction system components. This will help detect and address any issues promptly and ensure continuous, reliable operation.
b. Training and knowledge sharing: Provide training to operators and maintenance personnel on the proper operation, maintenance, and troubleshooting of the emission reduction system. Sharing knowledge and best practices will enhance system reliability and safety.
Recommendations: a. Collaborate with experts: Seek guidance and collaboration from experts, consultants, and technology providers with experience in emission reduction methods for gas turbines. Their expertise can help ensure effective engineering and design and avoid potential pitfalls.
b. Stay updated with regulations and standards: Keep abreast of evolving regulations and industry standards related to emissions reduction in the power generation, oil, and gas industries. Compliance with these regulations will ensure legal and environmental obligations are met.
c. Performance monitoring and reporting: Implement a robust performance monitoring and reporting system to track emission levels, system efficiency, and compliance with regulatory requirements. This information will help identify areas for improvement and demonstrate the system’s effectiveness.
By following these procedures, taking appropriate actions, conducting studies, implementing mitigations, and adhering to recommendations, the engineering and design of emission reduction methods in gas turbines can improve reliability and safety while achieving significant reductions in emissions in the power generation, oil, and gas industries. Regular monitoring, maintenance, and optimization are essential to sustain the performance of emission reduction systems over time.
