PRESSURE FLUCTUATIONS IN THE COMBUSTION SYSTEM - GAS TURBINES
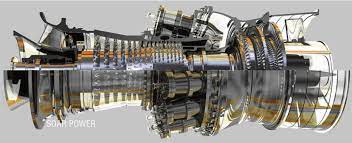
In gas turbines, pressure fluctuations in the combustion system can occur due to various factors, including flame pulsations. Flame pulsations refer to the periodic variations in the size, shape, or intensity of the flame. These pulsations can lead to fluctuations in the combustion process, which can result in several issues, including excessive mechanical stress, mechanical resonance, and combustion problems such as lean flame. Here’s an explanation of these aspects:
Excessive Mechanical Stress:
- Flame pulsations can cause rapid changes in heat release rates and localized variations in temperature and pressure within the combustion system.
- These rapid changes in thermal and mechanical loading can result in excessive mechanical stress on the turbine components, such as the combustion chamber walls, transition ducts, and fuel nozzles.
- Excessive mechanical stress can lead to material fatigue, deformation, and premature failure of these components, compromising the reliability and longevity of the gas turbine.
Mechanical Resonance:
- Mechanical resonance can occur when the natural frequency of the combustion system or its components coincides with the frequency of the flame pulsations.
- If the flame pulsation frequency matches the natural frequency of the combustion system, resonance amplifies the pressure fluctuations and mechanical stress, exacerbating the problem.
- Mechanical resonance can lead to significant vibrations and increased mechanical loading, which can result in structural damage, decreased component life, and potential safety risks.
Lean Flame Combustion Problems:
- Lean flame conditions refer to the operation of the gas turbine with a fuel-air mixture that has a relatively low fuel-to-air ratio.
- Flame pulsations can be more pronounced in lean flame conditions due to the increased sensitivity of lean flames to combustion instability.
- Lean flame combustion problems associated with flame pulsations can include flame blowout, flashback, or combustion instability, leading to reduced combustion efficiency, increased emissions, and potential equipment damage.
Analyzing pressure fluctuations associated with flame pulsations and addressing the associated risks requires several considerations:
- Monitoring Techniques: Utilize pressure sensors, dynamic flame sensors, and other instrumentation to monitor flame behavior and pressure fluctuations within the combustion system.
- Combustion Stability Analysis: Conduct comprehensive combustion stability analysis to identify the causes and characteristics of flame pulsations. This can involve experimental measurements, computational modeling, and data analysis techniques.
- System Design and Optimization: Ensure that the combustion system design and operational parameters are optimized to minimize the risk of flame pulsations. This may include appropriate fuel injection patterns, chamber geometry, and flame stabilization mechanisms.
- Fuel-Air Ratio Control: Maintain an appropriate fuel-air ratio to avoid lean flame conditions that can increase the likelihood of flame pulsations.
- Active Control Systems: Consider implementing active control strategies, such as fuel modulation or flame stabilization techniques, to dampen flame pulsations and mitigate the associated risks.
- Material Selection and Component Design: Utilize materials and component designs that can withstand the mechanical stress caused by flame pulsations, considering factors such as thermal expansion, vibration resistance, and fatigue strength.
- Ongoing Monitoring and Maintenance: Implement regular monitoring and maintenance programs to detect and address any emerging issues related to pressure fluctuations and flame pulsations.
By understanding and addressing pressure fluctuations associated with flame pulsations, gas turbine operators can mitigate the risks of excessive mechanical stress, mechanical resonance, and lean flame combustion problems. This leads to improved operational reliability, reduced maintenance costs, and enhanced combustion performance in gas turbines.
LIMITATIONS IN ENGINEERING & DESIGN TO AVOID PRESSURE FLUCTUATIONS IN THE COMBUSTION SYSTEMS
When it comes to avoiding and controlling pressure fluctuations in the combustion system of gas turbines, particularly those associated with flame pulsations and the risks of excessive mechanical stress, mechanical resonance, and combustion problems such as lean flame, there are certain limitations in engineering and design that need to be considered:
Complex Combustion Dynamics: The combustion process in gas turbines is complex, involving intricate interactions between fuel, air, and combustion products. It can be challenging to accurately predict and control flame pulsations and their associated pressure fluctuations due to the complex nature of combustion dynamics.
Sensitivity to Operating Conditions: Pressure fluctuations, flame pulsations, and the associated risks are often sensitive to changes in operating conditions such as fuel composition, load variations, and environmental factors. Achieving stable combustion across a wide range of operating conditions can be challenging.
Inherent System Variability: Gas turbine systems exhibit inherent variability, including variations in fuel properties, combustion chamber geometries, and flame stabilization mechanisms. This variability can contribute to variations in flame behavior and pressure fluctuations, making it difficult to implement a universal control solution.
Limitations of Monitoring Techniques: Monitoring flame pulsations and pressure fluctuations within the combustion system can be technically challenging. The availability and placement of sensors, their accuracy and sensitivity, and the ability to capture real-time data in a harsh operating environment can pose limitations in effectively monitoring and diagnosing the problem.
Trade-offs with Efficiency and Emissions: Implementing control measures to mitigate pressure fluctuations and flame pulsations may involve trade-offs with other performance parameters such as turbine efficiency and emissions. Striking a balance between stable combustion and optimal performance can be a complex task.
Retrofitting Challenges: Retrofitting existing gas turbine systems to address pressure fluctuations and flame pulsations can be challenging due to space constraints, compatibility issues with existing components, and the potential disruption to operations during the retrofitting process.
To overcome these limitations, it is important to take the following considerations into account:
- Conduct comprehensive research and development to better understand combustion dynamics and the factors contributing to flame pulsations and pressure fluctuations.
- Utilize advanced computational modeling techniques, such as computational fluid dynamics (CFD), to simulate and analyze the combustion process, enabling the optimization of combustion chamber design and operational parameters.
- Invest in advanced monitoring and diagnostic technologies that can provide real-time data on flame behavior, pressure fluctuations, and mechanical stress.
- Implement proactive maintenance and inspection programs to identify and address potential issues related to pressure fluctuations and flame pulsations.
- Collaborate with experts in combustion systems, control systems, and gas turbine design to develop tailored solutions for specific gas turbine configurations and operating conditions.
While there are limitations in engineering and design, continuous research, technological advancements, and collaborative efforts can help overcome these challenges and improve the control and mitigation of pressure fluctuations, flame pulsations, and their associated risks in the combustion systems of gas turbines.
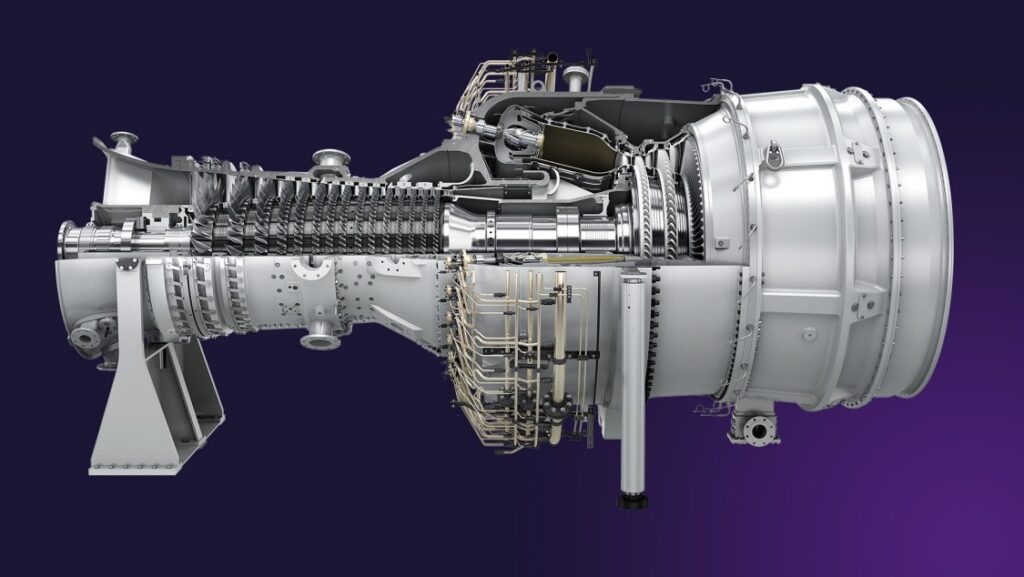
WHY, WHEN, WHERE, WHAT, WHICH AND HOW TO CONTROL THE PRESSURE FLUCTUATIONS IN COMBUSTION SYSTEMS
To avoid and control pressure fluctuations in the combustion system of gas turbines, particularly those associated with flame pulsations and the risks of excessive mechanical stress, mechanical resonance, and combustion problems such as lean flame, the following considerations should be taken into account:
Why to Avoid and Control Pressure Fluctuations:
- Pressure fluctuations can lead to increased mechanical stress, component fatigue, vibration, and potential damage to the gas turbine.
- Excessive mechanical stress and mechanical resonance can result in premature component failure, compromising the reliability and safety of the gas turbine.
- Combustion problems like lean flame can lead to reduced combustion efficiency, increased emissions, and potential damage to the combustion system.
When to Avoid and Control Pressure Fluctuations:
- Pressure fluctuations should be addressed throughout the operational life of the gas turbine, including during startup, steady-state operation, and shutdown.
- Control measures should be implemented during design, construction, commissioning, and ongoing operation of the gas turbine.
Where to Avoid and Control Pressure Fluctuations:
- Control and avoidance strategies should focus on the combustion system, including the combustion chamber, fuel injection system, flame stabilization mechanisms, and associated components.
What to Implement to Avoid and Control Pressure Fluctuations:
- Optimize Combustion System Design: Develop combustion chambers and associated components that minimize the potential for pressure fluctuations. Consider factors such as chamber geometry, swirl, fuel injection patterns, and flame stabilization methods.
- Fuel-Air Ratio Control: Maintain appropriate fuel-air ratios to prevent lean flame conditions, which can increase the likelihood of pressure fluctuations.
- Active Control Systems: Implement active control methods, such as fuel modulation or flame stabilization techniques, to mitigate pressure fluctuations and maintain stable combustion.
- Monitoring and Feedback Control: Utilize advanced sensors and monitoring systems to continuously measure and analyze flame behavior, pressure fluctuations, and mechanical stress. Implement feedback control mechanisms to adjust control parameters and maintain stable combustion.
Which Measures to Choose:
- The selection of measures will depend on the specific gas turbine design, operating conditions, and the characteristics of the pressure fluctuations. A combination of measures may be required to achieve effective control.
How to Implement Control and Avoidance Measures:
- Conduct comprehensive research, including computational modeling and experimental studies, to understand the causes and characteristics of pressure fluctuations and flame pulsations.
- Implement monitoring systems to continuously measure and analyze flame behavior, pressure fluctuations, and mechanical stress in real-time.
- Develop control strategies based on the acquired data and knowledge, utilizing feedback control systems to adjust control parameters and maintain stable combustion.
- Conduct regular inspections, maintenance, and optimization of the combustion system components.
- Collaborate with experts in combustion systems, control systems, and gas turbine design to develop and implement tailored solutions for specific gas turbine configurations and operating conditions.
By following these guidelines, gas turbine operators can effectively avoid and control pressure fluctuations associated with flame pulsations, mitigating the risks of excessive mechanical stress, mechanical resonance, and combustion problems such as lean flame. This leads to improved reliability, safety, combustion performance, and efficiency in gas turbines.
PROCEDURES, ACTIONS, STUDIES, ANALYSIS, MITIGATIONS AND RECOMMENDATIONS TO CONTROL AND AVOID THE PRESSURE FLUCTUATIONS IN COMBUSTION SYSTEMS IN GAS TURBINES
To avoid and control pressure fluctuations in the combustion system of gas turbines associated with flame pulsations and mitigate the risks of excessive mechanical stress, mechanical resonance, and combustion problems such as lean flame, the following procedures, actions, studies, analysis, mitigations, and recommendations can be implemented:
Procedures and Actions:
- Implement a Comprehensive Monitoring Program: Establish a monitoring system to continuously measure and record relevant parameters such as flame behavior, pressure, temperature, fuel-air ratio, and mechanical vibrations within the combustion system.
- Regular Inspection and Maintenance: Conduct routine inspections and maintenance of the combustion system components to ensure proper functioning, cleanliness, and structural integrity.
- Fuel-Air Ratio Control: Monitor and control the fuel-air ratio to maintain optimal combustion conditions and prevent lean flame operation.
- Implement Control Strategies: Develop and implement control strategies based on real-time monitoring data to mitigate pressure fluctuations, flame pulsations, and their associated risks. This may involve adjusting fuel injection, flame stabilization mechanisms, or introducing active control systems.
Studies and Analysis:
- Combustion Dynamics Studies: Conduct comprehensive studies and analysis to understand the combustion dynamics, flame behavior, and the factors contributing to flame pulsations and pressure fluctuations. This may involve computational modeling, simulations, and experimental investigations.
- Flame Stability Analysis: Perform flame stability analysis to identify the causes and characteristics of flame pulsations. This can include stability maps, analysis of heat release fluctuations, and identification of critical operating conditions.
- Resonance Analysis: Conduct resonance analysis to identify and address resonant frequencies within the combustion system that can amplify pressure fluctuations and mechanical stress.
- Combustion System Optimization: Utilize computational modeling techniques, such as computational fluid dynamics (CFD), to optimize the combustion system design, including chamber geometry, fuel injection patterns, and flame stabilization mechanisms.
Mitigations and Recommendations:
- Optimize Fuel Injection: Design and optimize fuel injection systems to ensure efficient fuel-air mixing and minimize the potential for local hotspots and combustion instability.
- Flame Stabilization Methods: Implement effective flame stabilization techniques, such as pilot flames, flame holders, or swirlers, to enhance flame stability and reduce the likelihood of flame pulsations.
- Active Control Systems: Consider the implementation of active control systems, such as fuel modulation or acoustic dampers, to actively suppress pressure fluctuations and stabilize combustion.
- Feedback Control Systems: Develop and implement feedback control systems that utilize real-time data to adjust control parameters and maintain stable combustion under varying operating conditions.
- Material Selection and Component Design: Use materials and component designs that can withstand the mechanical stress caused by pressure fluctuations and avoid mechanical resonance. Consider factors such as thermal expansion, vibration resistance, and fatigue strength.
- Continuous Monitoring and Evaluation: Regularly monitor and evaluate the effectiveness of control measures and make necessary adjustments based on performance and operational conditions.
It is important to involve experts in combustion systems, control systems, and gas turbine design to develop and implement these procedures, actions, studies, analysis, mitigations, and recommendations. Continuous monitoring, analysis, and optimization of control strategies are crucial to ensuring stable and efficient operation while minimizing pressure fluctuations, mitigating the risks of excessive mechanical stress, mechanical resonance, and combustion problems such as lean flame in gas turbines.