SPEED GOVERNOR vs BACK-PRESSURE GOVERNOR vs SPEED & AUTOMATIC EXTRACTION PRESSURE GOVERNOR - CONTROLS IN STEAM TURBINES
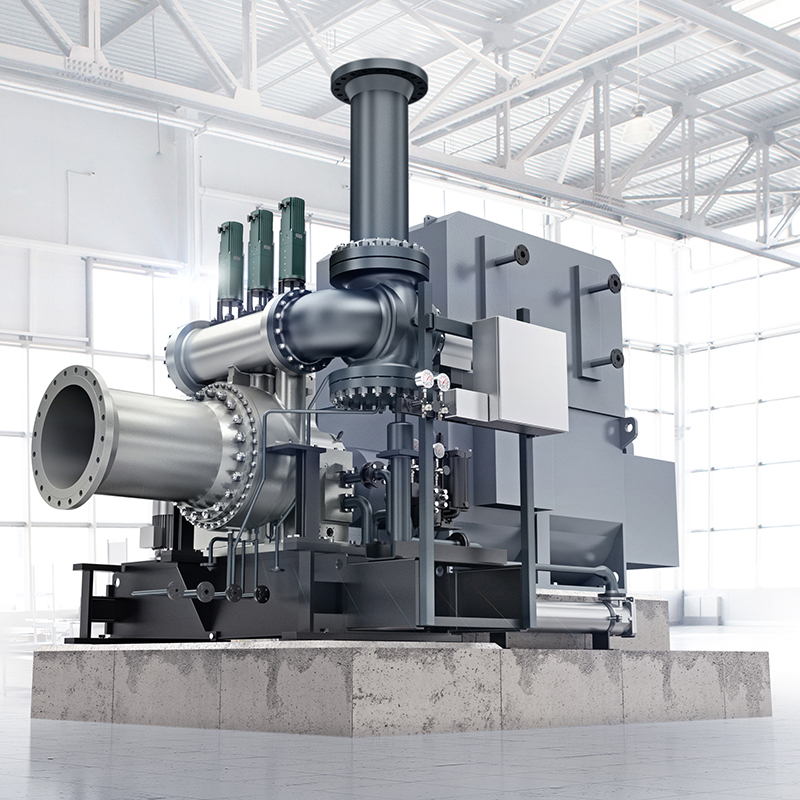
LIMITATIONS IN ENGINEERING & DESIGN FOR SPECIAL STEAM TURBINES
Speed Governor:
- Limitations:
- Limited control over steam flow and extraction pressures: Speed governors primarily focus on maintaining a constant speed or rotational speed of the turbine. They may have limited capability to adjust extraction pressures and steam flow rates for various operating conditions.
- Insensitivity to load fluctuations: Speed governors may not respond quickly to sudden load changes, resulting in transient response issues and potential instability in the turbine system.
- Reduced flexibility for power system integration: Speed governors may have limited compatibility with an advanced grid control and synchronization requirements, which can restrict their ability to contribute to the stability and reliability of the overall power system.
- Limitations:
Back-Pressure Governor:
- Limitations:
- Limited efficiency optimization: Back-pressure governors control the extraction pressure of steam from the turbine, often to supply process steam. However, they may not offer precise control for optimizing efficiency since the back pressure is primarily dictated by process steam demand, limiting the ability to maximize power generation.
- Decreased turbine output: By controlling the back pressure, these governors indirectly affect the exhaust steam conditions, resulting in reduced turbine output and power generation capacity.
- Dependence on process steam demand: Back-pressure governors are sensitive to changes in the process steam demand, which can impact the overall stability and control of the turbine system.
- Limitations:
Speed and Automatic Extraction Pressure Governor:
- Limitations:
- Complexity and system integration challenges: The integration of speed control and automatic extraction pressure control introduces increased complexity in the turbine control system. This complexity can lead to challenges in system design, operation, and maintenance.
- Risk of interactions between control modes: The interaction between speed control and extraction pressure control can lead to potential conflicts or instability in the control system if not properly designed and coordinated.
- Maintenance and calibration requirements: The combination of multiple control modes in a single governor system may require more frequent maintenance and calibration to ensure accurate and reliable performance.
- Limitations:
To overcome these limitations and improve the reliability, availability, maintainability, safety factors, and environmental risks associated with governor controls in special-purpose steam turbines, the following measures can be considered:
- Perform detailed engineering studies and system simulations to optimize the control system design and ensure compatibility with the specific turbine application and operating conditions.
- Implement advanced control algorithms and strategies that offer enhanced response time, stability, and flexibility to accommodate load changes and variations in steam demand.
- Conduct regular maintenance and calibration of the governor control system to ensure accurate and reliable performance.
- Incorporate advanced monitoring and diagnostic systems to detect and diagnose potential control system issues, allowing for timely maintenance and troubleshooting.
- Collaborate with turbine manufacturers and industry experts to stay updated on the latest advancements in governor control technologies and incorporate them into the design and operation of the turbine system.
- Implement comprehensive training programs for operators and maintenance personnel to ensure proper understanding and operation of the governor controls.
By addressing these limitations and implementing the recommended measures, it is possible to improve the reliability, availability, maintainability, safety factors, and environmental performance of special-purpose steam turbines in the power generation, oil, and gas industries.
WHY, WHEN, WHERE, WHAT, WHICH, HOW TO APPLY GOVERNOR CONTROLS IN STEAM TURBINES
Why use Speed Governor, Back-Pressure Governor, and Speed & Automatic Extraction Pressure Governor Controls:
- Speed Governor: Speed governors are commonly used in steam turbines to regulate the rotational speed, ensuring stable operation and maintaining the desired power output. They provide control over the turbine speed and help maintain grid stability.
- Back-Pressure Governor: Back-pressure governors are employed to control the extraction pressure of steam from the turbine. They are typically used when there is a need to supply process steam to industrial applications.
- Speed & Automatic Extraction Pressure Governor: This control system combines both speed control and automatic extraction pressure control. It offers a more comprehensive approach to governing the steam turbine, enabling precise control over speed and extraction pressure simultaneously.
When and Where to Use:
- Speed Governor: Speed governors are suitable for applications where maintaining a constant rotational speed is critical, such as in power generation, where grid synchronization and stability are crucial.
- Back-Pressure Governor: Back-pressure governors are utilized in situations where process steam demand is the primary consideration, such as industrial plants requiring steam for their manufacturing processes.
- Speed & Automatic Extraction Pressure Governor: This control system is beneficial in applications that require simultaneous control of both speed and extraction pressure, enabling better optimization of power generation and steam supply.
What to Consider:
- System Requirements: Consider the specific requirements of the steam turbine system, including power output, steam demand, grid synchronization, and process steam requirements.
- Operational Flexibility: Evaluate the flexibility needed in the control system to respond to varying load conditions, steam demands, and grid stability requirements.
- Efficiency Optimization: Determine the importance of maximizing thermal efficiency and power output while considering the impact on extraction pressure control and process steam supply.
Which Control System to Choose:
- Selection should be based on a comprehensive evaluation of the specific project requirements, system design, and operational objectives.
- Consult with turbine manufacturers, engineering experts, and control system specialists to determine the most suitable governor control system for the given application.
How to Implement:
- Engage in a detailed engineering study to analyze the system dynamics, performance requirements, and control strategies.
- Design the control system with proper sensors, actuators, and control algorithms to ensure accurate and responsive control.
- Conduct system simulations and modeling to validate the control system’s performance under various operating conditions.
- Perform commissioning and testing to verify the control system’s functionality and compatibility with the steam turbine and overall plant operations.
- Establish a comprehensive maintenance and monitoring program to ensure the long-term reliability, availability, and maintainability of the governor control system.
By carefully considering these factors and following the recommended implementation approach, the use of speed governor, back-pressure governor, or speed & automatic extraction pressure governor controls can contribute to improving the reliability, availability, maintainability, and safety factors of special purpose steam turbines. Additionally, these controls can help avoid environmental risks and critical failures, ultimately enhancing the performance of power generation, oil, and gas industries.
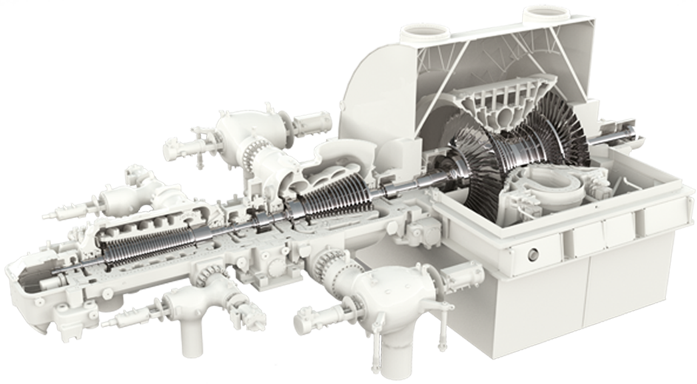
PROCEDURES, ACTIONS, STUDIES, MITIGATION, RECOMMENDATIONS TO APPLY GOVERNOR CONTROLS IN STEAM TURBINES
Procedures and Actions:
- Conduct a thorough analysis of the specific application requirements, including power output, steam demand, process requirements, and grid stability considerations.
- Engage in engineering studies to evaluate the suitability of different governor control systems and their impact on turbine performance.
- Develop control system design specifications, considering the control algorithm, sensors, actuators, and control interfaces.
- Implement the control system design, ensuring proper installation and integration with the steam turbine and other plant systems.
- Perform comprehensive testing and commissioning of the control system to verify its functionality, responsiveness, and reliability.
- Establish maintenance procedures and schedules for regular inspections, calibrations, and performance monitoring of the governor controls.
Studies:
- Conduct system dynamics studies to analyze the interaction between the turbine and the governor control systems.
- Perform simulation and modeling studies to evaluate the control system’s performance under various operating conditions, including load changes and disturbances.
- Investigate historical operational data and case studies to identify potential challenges and areas for improvement.
- Research the latest advancements in governor control technology and best practices in the industry.
Mitigation:
- Implement redundant and fail-safe systems to ensure reliability and availability of the governor controls.
- Monitor and analyze real-time data to detect anomalies and deviations from normal operation, allowing for timely mitigation of potential failures.
- Employ condition monitoring techniques to identify early signs of component degradation or malfunction.
- Implement preventive maintenance programs to address wear and tear, corrosion, and other potential issues that may affect the governor control systems.
- Implement backup power and control systems to ensure continued operation in the event of power outages or control system failures.
Recommendations:
- Collaborate with turbine manufacturers, control system suppliers, and industry experts to obtain guidance and recommendations specific to the turbine model and application requirements.
- Stay updated with industry standards and guidelines related to governor control systems.
- Regularly review and optimize control system settings to ensure they are aligned with the turbine’s operational requirements and performance goals.
- Foster a culture of safety, training, and continuous improvement to enhance the understanding and operation of governor control systems.
- Conduct periodic reviews and audits to assess the effectiveness of the control systems and identify opportunities for enhancement.
By following these procedures, taking appropriate actions, conducting studies, implementing mitigations, and adhering to recommendations, the use of speed governor, back-pressure governor, or speed & automatic extraction pressure governor controls can contribute to improving the reliability, availability, maintainability, and safety factors of special purpose steam turbines. These measures can also help avoid environmental risks and critical failures, ensuring efficient and safe operation in power generation, oil, and gas industries.
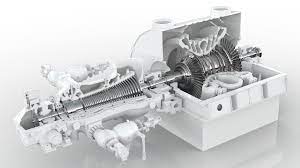