ADVANCED CONTROL SYSTEMS (MODEL PREDICTIVE CONTROL (MPC), FUZZY LOGIC CONTROL, NEURAL NETWORKS AND SIMILAR TECHNOLOGY) - TURBOMACHINERY
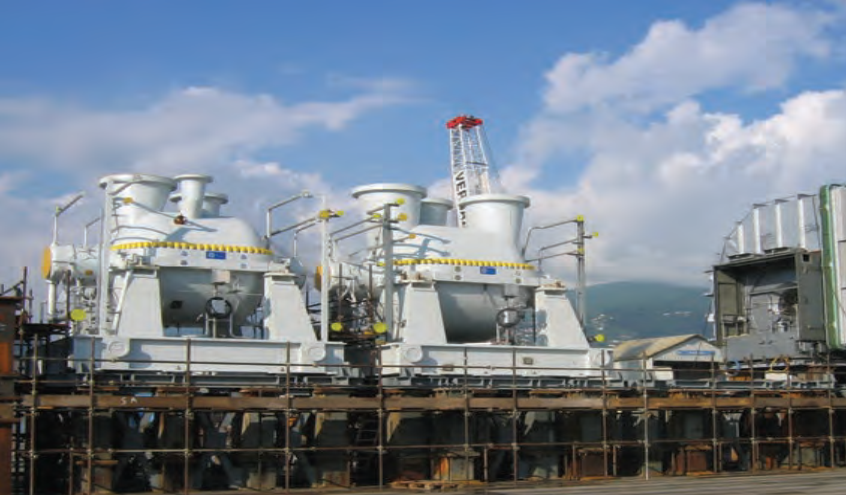
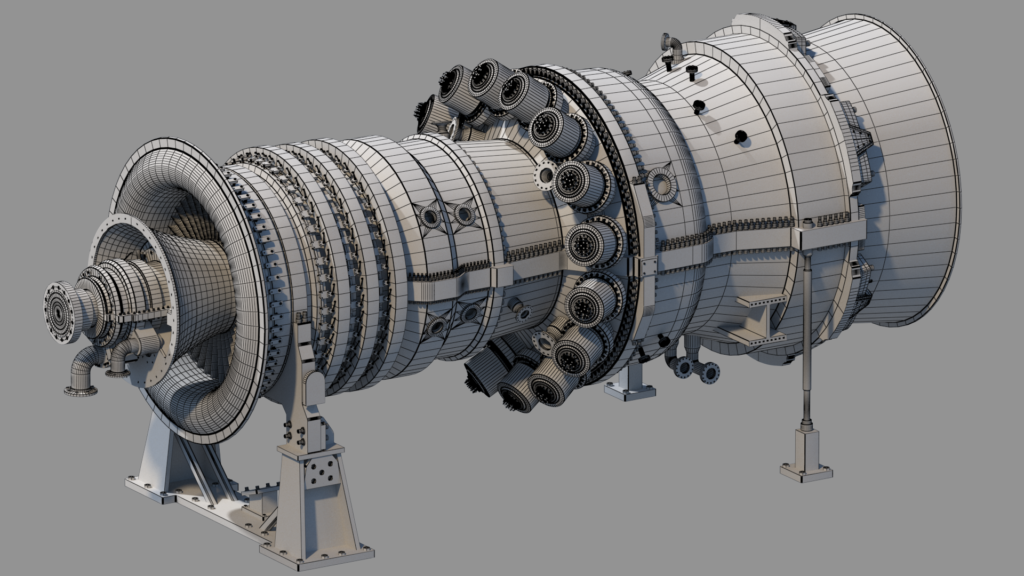
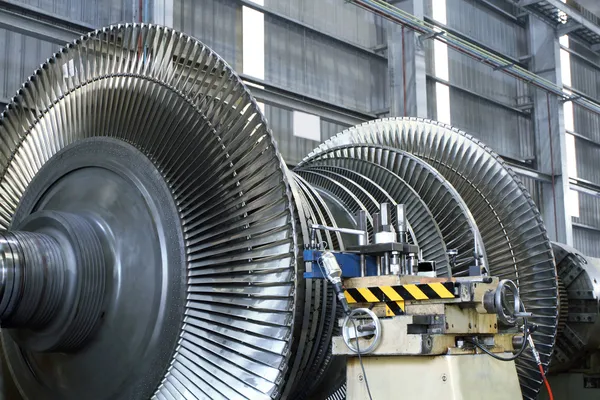
CENTRIFUGAL COMPRESSORS
GAS TURBINES
SPECIAL STEAM TURBINES
Advanced control systems, including model predictive control (MPC), fuzzy logic control, and other similar technologies, have played a significant role in improving the dynamic response and operational flexibility of turbomachinery, such as centrifugal compressors, gas turbines, and special steam turbines. These control systems utilize advanced algorithms, data-driven models, and intelligent decision-making to optimize the operation of turbomachinery and enhance reliability, safety, and performance. Here’s an overview of the key control systems and their impact:
- Model Predictive Control (MPC): Model Predictive Control is a sophisticated control technique that utilizes mathematical models of the turbomachinery system to predict its future behavior and optimize control actions. MPC considers system dynamics, constraints, and objectives to generate optimal control strategies. Benefits of MPC in turbomachinery include:
- Enhanced Stability: MPC accounts for system dynamics and can handle complex and nonlinear behavior, improving stability and response time.
- Optimization of Multiple Objectives: MPC optimizes multiple objectives, such as efficiency, emissions, and reliability, simultaneously, allowing for better operational flexibility and performance trade-offs.
- Constraint Handling: MPC incorporates constraints, such as equipment limits and safety limits, in the control strategy, ensuring safe and reliable operation even during abnormal conditions.
- Robustness: MPC can handle uncertainties and disturbances by adapting the control actions in real-time, leading to improved robustness and performance.
- Fuzzy Logic Control: Fuzzy Logic Control (FLC) is a control methodology that utilizes linguistic rules based on expert knowledge to make control decisions. FLC is particularly useful in turbomachinery applications where precise mathematical models may not be available or the system behavior is complex. Benefits of FLC in turbomachinery include:
- Adaptability: FLC can handle nonlinearities and uncertainties, making it suitable for controlling turbomachinery with varying operating conditions and complex dynamics.
- Expert Knowledge Incorporation: FLC allows operators to incorporate their domain expertise through linguistic rules, capturing their knowledge of the system behavior and control actions.
- Fault Detection and Tolerance: FLC can incorporate fault detection and tolerance mechanisms, allowing for continued operation even in the presence of certain faults or abnormal conditions.
- Transparency: FLC provides interpretability as linguistic rules are easily understandable, enabling operators to have insight into the control actions and decisions.
- Other Advanced Control Technologies: Other advanced control technologies, such as adaptive control, neural networks, and fuzzy-neural hybrid control, have also been applied in turbomachinery to improve reliability, safety, and performance. These technologies offer benefits such as adaptive tuning, learning capabilities, and increased robustness to disturbances and uncertainties.
Implementation considerations and recommendations:
- Accurate Modeling: Developing accurate mathematical models or data-driven models of the turbomachinery system is crucial for the effectiveness of advanced control systems. Models should capture the relevant dynamics, non-linearities, and operating conditions.
- Real-time Data Integration: Real-time sensor data integration into the control system enables continuous monitoring of system variables, facilitating adaptive and dynamic control actions.
- System Identification: System identification techniques can be employed to identify and validate the dynamic behavior of the turbomachinery system, improving the accuracy and reliability of control algorithms.
- Operator Training: Operators and control engineers should receive appropriate training to understand the advanced control systems, their tuning, and operation, enabling effective utilization and optimization.
- Continuous Monitoring and Maintenance: Regular monitoring, performance evaluation, and maintenance of the advanced control systems are necessary to ensure their continued effectiveness and adaptability to changing operating conditions.
By leveraging advanced control systems like MPC, FLC, and other similar technologies, turbomachinery operators can achieve improved dynamic response, operational flexibility, and performance, leading to enhanced reliability, safety, and overall equipment performance in applications such as centrifugal compressors, gas turbines, and special steam turbines.
ADVANTAGES & DISADVANTAGES USING ADVANCED CONTROL SYSTEMS IN TURBOMACHINERY
Advantages:
Enhanced Dynamic Response: Advanced control systems can improve the dynamic response of turbomachinery by accounting for system dynamics, non-linearities, and constraints. They enable faster and more accurate control actions, leading to improved stability, faster load changes, and reduced response time.
Optimized Performance: These control systems facilitate optimization of multiple objectives, such as efficiency, emissions, and reliability. They consider complex operating conditions, constraints, and objectives simultaneously, allowing for better operational flexibility and trade-offs to achieve optimal performance.
Adaptive and Robust Control: Advanced control systems, like neural networks and fuzzy-neural hybrid control, offer adaptive capabilities to handle varying operating conditions and uncertainties. They can self-adjust and learn from data, enabling robust control actions in the presence of disturbances or parameter variations.
Fault Detection and Tolerance: Certain advanced control systems, including fuzzy logic control and neural networks, can incorporate fault detection and tolerance mechanisms. This enables the system to detect and respond to faults or abnormal conditions, allowing for continued safe and reliable operation.
Expert Knowledge Incorporation: Fuzzy logic control and similar techniques allow operators to incorporate their domain expertise through linguistic rules. This facilitates the utilization of expert knowledge to guide control actions, making the control system more intuitive and transparent.
Disadvantages:
Model Complexity and Design Effort: Developing accurate mathematical models or data-driven models for advanced control systems can be complex and time-consuming. It requires a deep understanding of system dynamics, non-linearities, and operating conditions, as well as significant effort in model development and tuning.
Model Accuracy and Adaptability: The accuracy and adaptability of the control system depend on the quality and accuracy of the underlying models. If the models do not accurately represent the system behavior or fail to capture variations and uncertainties, the control system’s effectiveness may be compromised.
Tuning and Parameter Optimization: Proper tuning and optimization of the advanced control system parameters are crucial for optimal performance. This process can be challenging and may require extensive experience, expertise, and iterative adjustments to achieve the desired performance.
Computational Requirements: Advanced control systems, particularly model predictive control and neural networks, may have higher computational requirements. Real-time processing and optimization can be demanding, requiring sufficient computational resources to handle the complex calculations involved.
Interpretability and Transparency: Some advanced control systems, such as neural networks, can lack interpretability and transparency. The inner workings of the control algorithm may be challenging to understand, making it difficult for operators to interpret and validate the control actions and decisions.
It’s important to note that the advantages and disadvantages mentioned above are general considerations, and the specific implementation and performance of advanced control systems may vary based on the application, system complexity, available data, and expertise of the operators. Careful design, tuning, validation, and continuous monitoring are necessary to maximize the advantages and mitigate the limitations of advanced control systems in turbomachinery applications.
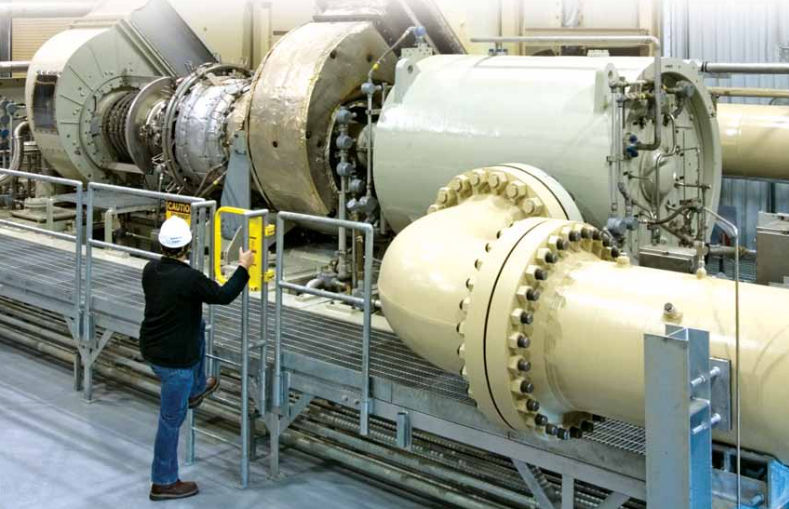
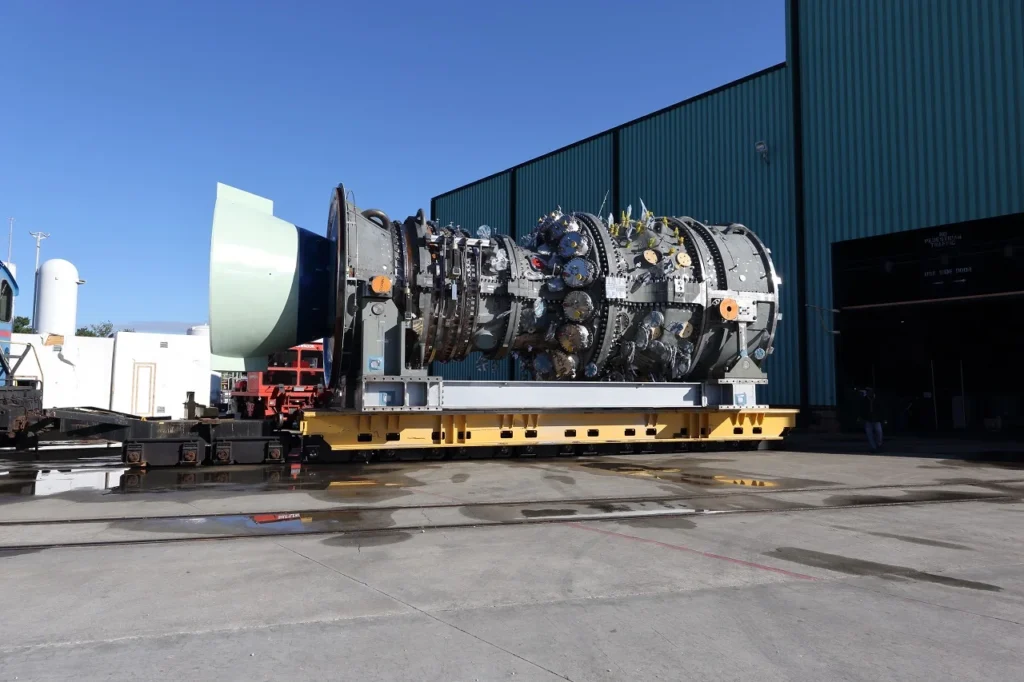
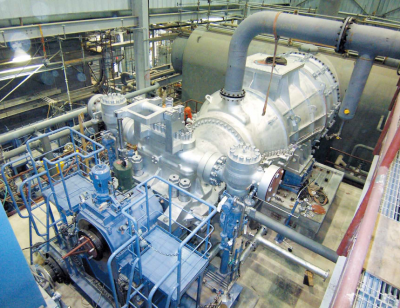
WHY, WHEN, WHERE, WHAT, WHICH, HOW TO USE ADVANCED CONTROL SYSTEMS IN TURBOMACHINERY
Why use advanced control systems?
- Advanced control systems offer several benefits, including improved dynamic response, optimized performance, adaptive and robust control, fault detection and tolerance, and expert knowledge incorporation. These benefits help achieve higher reliability, safety, and performance in turbomachinery systems.
When to use advanced control systems?
- Advanced control systems are particularly useful in situations where precise control, fast response, and optimal performance are crucial. They are employed during normal operations and challenging conditions when the system dynamics and constraints require advanced algorithms and decision-making to maintain safe and efficient operation.
Where are advanced control systems used?
- Advanced control systems can be applied in various industries, including the oil & gas sector, power generation plants, chemical processing facilities, and other industrial environments that utilize turbomachinery. They are used in onshore and offshore installations where high-performance control and operational flexibility are necessary.
What can be accomplished with advanced control systems?
- Advanced control systems can improve the dynamic response and operational flexibility of turbomachinery by optimizing performance, ensuring stability, reducing response time, adapting to varying operating conditions, handling uncertainties, and incorporating expert knowledge. They contribute to enhanced reliability, safety, and overall performance of the equipment.
Which components can benefit from advanced control systems?
- Advanced control systems can be applied to various components of turbomachinery, including compressors, turbines, combustion systems, and associated control systems. They address the control and optimization requirements of these components to improve their dynamic response and operational performance.
How are advanced control systems implemented?
- The implementation of advanced control systems involves the following steps: (1) Developing accurate mathematical models or data-driven models of the turbomachinery system; (2) Designing and tuning the control algorithms based on the specific control objectives, system dynamics, and constraints; (3) Integrating real-time data acquisition systems for monitoring and control; (4) Validating and testing the control system performance using simulations and real-world data; (5) Fine-tuning and optimizing control parameters based on operational experience and feedback.
It’s important to note that the selection and implementation of specific advanced control systems depend on the unique characteristics of the turbomachinery, control objectives, available resources, and expertise of the operators. Detailed analysis, system understanding, and consideration of operational requirements are necessary for successful implementation and achievement of the desired improvements in reliability, safety, and performance.
PROCEDURES, ACTIONS, STUDIES, ANALYSIS, MITIGATION AND RECOMMENDATIONS TO USE ADVANCED CONTROL SYSTEMS IN TURBOMACHINERY
- Procedures and Actions:
- System Analysis: Conduct a thorough analysis of the turbomachinery system, including the components, operating conditions, constraints, and control objectives.
- Control System Design: Select the appropriate advanced control system, such as MPC, fuzzy logic control, neural networks, or fuzzy-neural hybrid control, based on the specific requirements and characteristics of the turbomachinery system.
- Model Development: Develop accurate mathematical models or data-driven models of the turbomachinery system, considering system dynamics, non-linearities, and uncertainties.
- Controller Tuning: Determine the optimal parameters and tuning of the control algorithms to achieve the desired control objectives, stability, and performance.
- Integration of Real-Time Data: Implement data acquisition systems and integrate real-time data from sensors to enable monitoring and control actions.
- Validation and Testing: Validate and test the control system performance using simulations, hardware-in-the-loop testing, or real-world data to ensure its effectiveness and stability.
- Implementation and Deployment: Deploy the advanced control system in the turbomachinery system, including integration with existing control infrastructure, communication networks, and monitoring systems.
- Monitoring and Maintenance: Continuously monitor the performance of the advanced control system and conduct regular maintenance activities to ensure its continued effectiveness and adaptability.
- Studies and Analysis:
- System Dynamics and Modeling: Conduct studies to understand the system dynamics and develop accurate mathematical models or data-driven models of the turbomachinery system.
- Control Strategy Optimization: Perform optimization studies to determine the optimal control strategies, tuning parameters, and set-points for improved dynamic response and operational flexibility.
- Performance Evaluation: Analyze the performance of the advanced control system using simulations and real-world data, comparing it with baseline control strategies or reference models.
- Fault Detection and Diagnosis: Study and analyze methods for incorporating fault detection and diagnosis capabilities into the control system to enhance reliability and safety.
- Robustness Analysis: Conduct robustness analysis to evaluate the performance and adaptability of the advanced control system under varying operating conditions, uncertainties, and disturbances.
- Mitigations and Recommendations:
- Operator Training: Provide training to operators and control engineers on the implementation, operation, and maintenance of advanced control systems to ensure proper utilization and effective monitoring.
- Data Quality Assurance: Implement data quality assurance processes to ensure the accuracy, reliability, and completeness of the data used in the control system, including sensor calibration and validation.
- Cybersecurity Measures: Establish robust cybersecurity measures to protect the integrity, confidentiality, and availability of the control system and associated data.
- Continuous Monitoring and Optimization: Continuously monitor the performance of the advanced control system, collect operational data, and analyze its effectiveness. Implement optimization techniques to further enhance the performance and adaptability of the control system.
- Collaboration and Knowledge Sharing: Foster collaboration among industry stakeholders, control system developers, researchers, and equipment manufacturers to share best practices, insights, and lessons learned in implementing advanced control systems.
It’s important to note that the specific procedures, actions, studies, analyses, mitigations, and recommendations may vary based on the specific advanced control system selected, the characteristics of the turbomachinery system, and industry-specific requirements. Close collaboration with domain experts, control system developers, and equipment manufacturers is crucial for successful implementation and to achieve the desired improvements in reliability, safety, and performance.