ADDITIVE MANUFACTURING (3D PRINTING) - TURBOMACHINERY
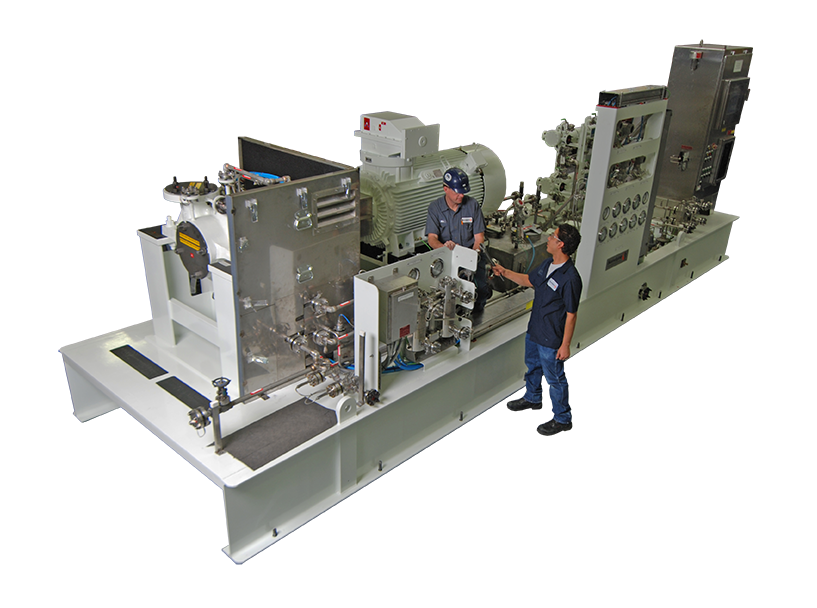
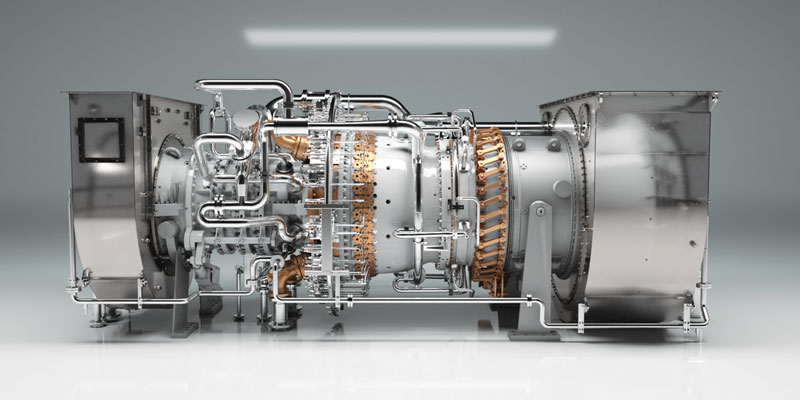
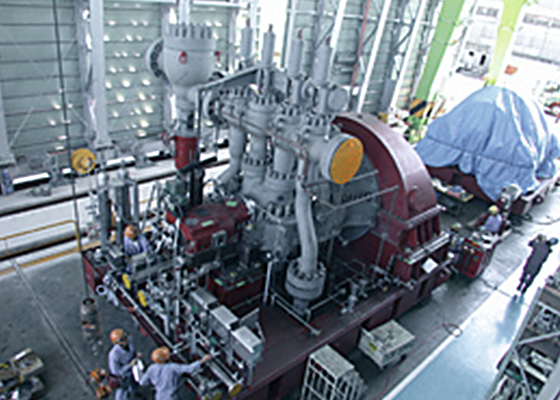
CENTRIFUGAL COMPRESSORS
GAS TURBINES
SPECIAL STEAM TURBINES
Complex Geometries: Additive manufacturing enables the production of highly complex geometries that were traditionally challenging or impossible to manufacture using conventional methods. Turbomachinery components, such as blades, vanes, and impellers, can be designed with intricate internal cooling channels, optimized aerodynamic profiles, and tailored shapes for improved performance. These complex geometries enhance reliability by optimizing fluid flow, reducing turbulence, and minimizing stress concentrations.
Lightweight Design: Additive manufacturing allows for the creation of lightweight structures without compromising strength or performance. By optimizing the component’s internal lattice structures or using topology optimization algorithms, it’s possible to reduce the weight of turbomachinery parts, resulting in reduced inertia, improved efficiency, and increased power-to-weight ratio. Lighter components can also lead to reduced mechanical loads and wear on supporting structures and bearings, enhancing overall reliability.
Customization and Rapid Prototyping: Additive manufacturing facilitates customization and rapid prototyping of turbomachinery components. This capability allows engineers to quickly iterate designs, test new concepts, and optimize performance based on specific requirements. By enabling rapid prototyping, additive manufacturing accelerates the development process, reduces lead times, and enhances the overall design quality, leading to improved reliability and safety.
Material Flexibility: Additive manufacturing offers a wide range of materials suitable for turbomachinery applications, including high-temperature alloys, superalloys, and metal matrix composites. These materials provide excellent mechanical properties, temperature resistance, and corrosion resistance required for demanding operating conditions in the oil & gas industry and power generation plants. The ability to select materials tailored to specific applications improves reliability, durability, and safety.
Reduced Assembly and Part Count: Additive manufacturing allows for the consolidation of multiple parts into a single component. By integrating several individual pieces into a single 3D-printed part, assembly time and potential points of failure are reduced. Fewer joints and interfaces minimize the risk of leaks, misalignments, and structural weaknesses, thereby improving reliability and safety.
Repair and Maintenance: Additive manufacturing offers the capability to repair or replace damaged or worn-out turbomachinery components more efficiently. Instead of sourcing and waiting for replacement parts, 3D printing enables on-demand production of spare parts, reducing downtime and improving the availability of equipment. This capability is particularly advantageous in remote locations where spare parts may not be readily available.
Improved Cooling and Heat Transfer: Additive manufacturing allows for the creation of intricate internal cooling channels within turbomachinery components. These channels enhance the cooling capacity of blades, vanes, and other critical parts, enabling better heat dissipation and reducing the risk of thermal damage. Improved cooling leads to enhanced reliability and safety by preventing component degradation and extending their operational life.
Overall, additive manufacturing in turbomachinery provides opportunities for design optimization, lightweighting, customization, rapid prototyping, and efficient repair. These benefits contribute to improved reliability, safety, and operational performance in the oil & gas industry and power generation plants by enhancing component efficiency, reducing downtime, and enabling more effective maintenance strategies.
ADVANTAGES & DISADVANTAGES APPLYING ADDITIVE MANUFACTURING (3D PRINTING) IN TURBOMACHINERY
Advantages:
Design Flexibility: Additive manufacturing allows for the creation of complex geometries and intricate internal structures that are difficult or impossible to achieve with traditional manufacturing methods. This flexibility enables the optimization of component designs for improved performance, efficiency, and reliability.
Customization and Rapid Prototyping: Additive manufacturing enables the production of customized components tailored to specific applications or operating conditions. It also allows for rapid prototyping, facilitating iterative design improvements, reducing development time, and enhancing reliability and safety through quicker validation and testing.
Lightweight Design: By utilizing advanced lattice structures and topology optimization, additive manufacturing can produce lightweight components without sacrificing strength. Lighter parts reduce inertia, improve efficiency, and decrease mechanical loads on supporting structures, leading to enhanced reliability and operational performance.
Reduced Assembly and Part Count: Additive manufacturing enables the consolidation of multiple parts into a single component, reducing assembly time and the number of potential failure points. Fewer joints and interfaces minimize the risk of leaks, misalignments, and structural weaknesses, enhancing reliability and safety.
On-Demand Manufacturing and Repair: Additive manufacturing facilitates on-demand production of spare parts, reducing downtime and improving equipment availability. It also enables efficient repair by replacing damaged or worn-out components without the need for complex supply chains. This capability enhances reliability and operational performance, particularly in remote locations.
Disadvantages:
Material Limitations: While additive manufacturing offers a wide range of materials suitable for turbomachinery applications, certain specialized alloys and composites may not be readily available or feasible to 3D print. Material limitations can impact the performance, durability, and reliability of components.
Quality Control and Certification: Ensuring consistent quality and adherence to industry standards can be challenging in additive manufacturing. Stringent quality control processes and certification procedures are necessary to guarantee the reliability and safety of 3D-printed components, which may involve additional time and cost considerations.
Limited Size and Scalability: Additive manufacturing currently faces limitations in terms of component size and scalability. Producing large-scale turbomachinery parts using 3D printing can be technically challenging and time-consuming. This constraint may restrict the application of additive manufacturing in certain turbomachinery systems.
Surface Finish and Post-Processing: 3D-printed parts may exhibit rougher surface finishes compared to components produced through traditional manufacturing techniques. Additional post-processing steps, such as machining or surface treatments, may be required to achieve the desired surface quality, introducing additional time, cost, and complexity.
Cost Considerations: While additive manufacturing can offer benefits in terms of customization and reduced assembly, the initial setup and equipment costs for implementing 3D printing can be significant. Additionally, depending on the specific application and volume requirements, the cost of 3D-printed components may be higher than those produced using conventional methods.
Process Validation and Optimization: Implementing additive manufacturing in turbomachinery requires thorough process validation and optimization to ensure consistent quality, repeatability, and reliability. The development of suitable process parameters, material selection, and post-processing techniques can be time-consuming and resource-intensive.
It’s important to note that the advantages and disadvantages of additive manufacturing in turbomachinery may vary depending on the specific application, operating conditions, and industry requirements. As technology continues to advance, ongoing research and development efforts aim to address these challenges and expand the use of additive manufacturing in turbomachinery for improved reliability, safety, and operational performance.
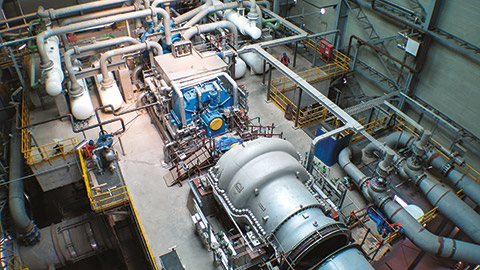
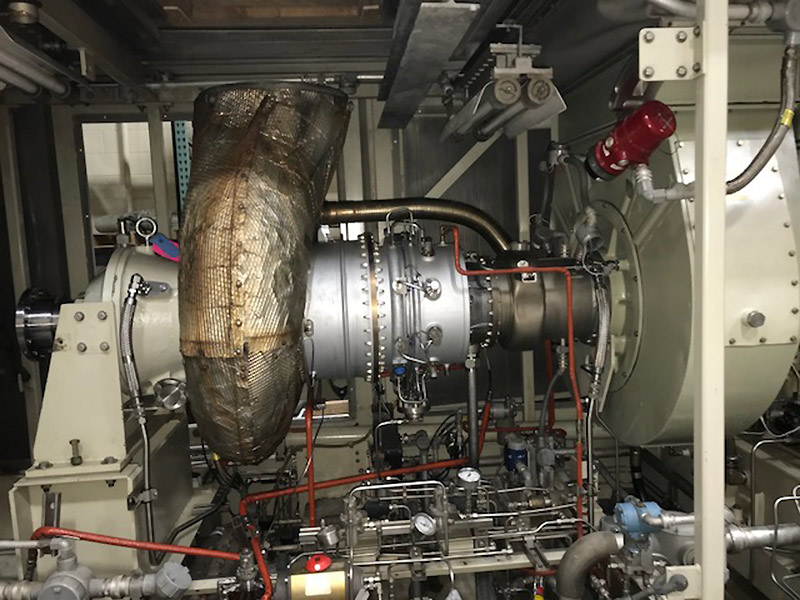
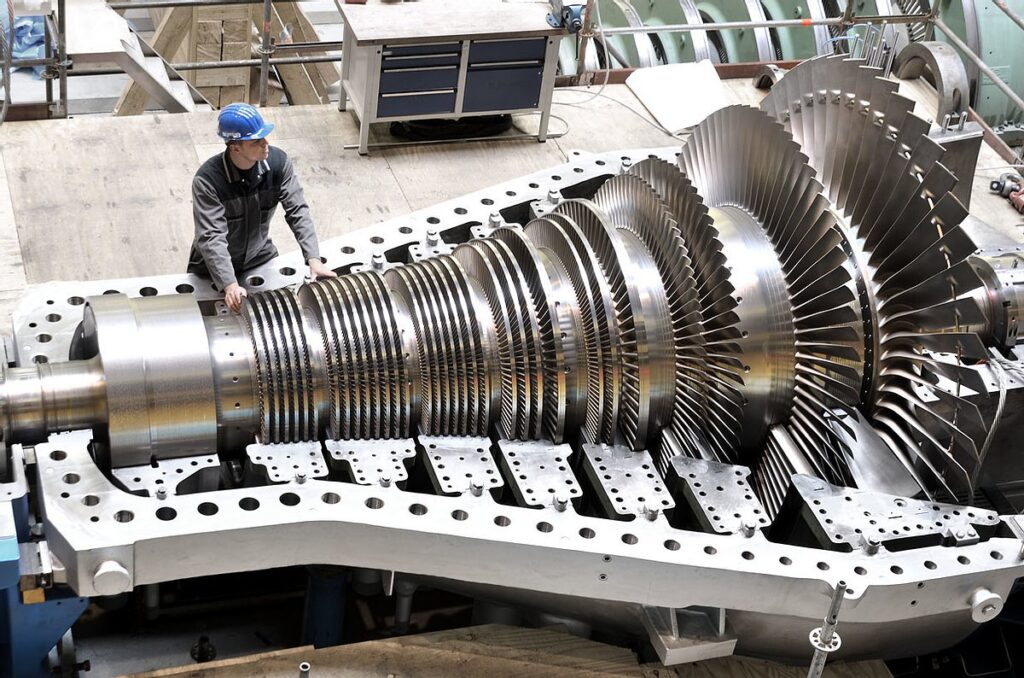
LIMITATIONS APPLYING ADDITIVE MANUFACTURING (3D PRINTING) IN TURBOMACHINERY
Size Constraints: Additive manufacturing techniques currently face limitations in terms of the size of components that can be printed. Turbomachinery parts, such as large impellers or rotors, may exceed the maximum build volume of 3D printers. This limitation restricts the application of additive manufacturing to smaller or less complex components, potentially limiting its impact on overall system performance.
Material Selection: While there is a wide range of materials available for additive manufacturing, certain specialized alloys or composites used in turbomachinery may not be suitable for 3D printing. Materials with specific mechanical properties, high-temperature resistance, or corrosion resistance may have limited options in additive manufacturing, affecting the overall reliability and operational performance of the equipment.
Manufacturing Time: Additive manufacturing can be a time-consuming process, particularly for larger or complex components. The layer-by-layer printing method can result in longer production times compared to conventional manufacturing methods. This limitation can impact the availability and turnaround time for producing or repairing critical turbomachinery components.
Surface Finish and Post-Processing: 3D-printed components often exhibit rougher surface finishes compared to those produced through traditional manufacturing methods. Additional post-processing steps, such as machining or surface treatments, may be required to achieve the desired surface quality and dimensional accuracy. These additional steps can introduce complexity, cost, and potential variability in the final product.
Quality Control and Certification: Ensuring consistent quality and meeting industry standards can be challenging in additive manufacturing. Stringent quality control processes and certification procedures are necessary to guarantee the reliability and safety of 3D-printed turbomachinery components. Developing and implementing quality assurance protocols specific to additive manufacturing can be time-consuming and resource-intensive.
Cost Considerations: While additive manufacturing can offer benefits in terms of customization and reduced assembly, it can be a costly manufacturing method. The initial setup and equipment costs for implementing 3D printing can be significant. Additionally, depending on the specific application and volume requirements, the cost of 3D-printed components may be higher than those produced using conventional methods, impacting the economic feasibility of widespread adoption.
Process Validation and Optimization: Implementing additive manufacturing in turbomachinery requires rigorous process validation and optimization to ensure consistent quality and repeatability. Identifying suitable process parameters, validating material properties, and optimizing printing techniques can be complex and time-consuming. These challenges can delay the adoption of additive manufacturing in critical turbomachinery applications.
It’s worth noting that ongoing advancements in additive manufacturing technology and materials research aim to address these limitations. As the technology evolves, researchers and industry experts are actively working to overcome these challenges and expand the applications of additive manufacturing in turbomachinery, ultimately enhancing reliability, safety, and operational performance in the oil & gas industry and power generation plants.
WHY, WHEN, WHERE, WHAT, WHICH, AND HOW TO APPLY ADDITIVE MANUFACTURING (3D PRINTING) IN TURBOMACHINERY
Why apply additive manufacturing?
- Additive manufacturing offers several advantages such as design flexibility, customization, rapid prototyping, lightweight design, and on-demand manufacturing/repair. These benefits can enhance the reliability, safety, and operational performance of turbomachinery by optimizing component designs, reducing weight, improving efficiency, enabling customization, and minimizing downtime through efficient repair processes.
When to apply additive manufacturing?
- Additive manufacturing can be applied during different stages of the turbomachinery lifecycle, including initial design, prototyping, production, and maintenance/repair. It can be used when there is a need for complex geometries, customization, quick design iterations, lightweight structures, on-demand spare parts, or efficient repair processes.
Where is additive manufacturing used?
- Additive manufacturing can be utilized in various settings, including manufacturing facilities, research and development labs, and maintenance/repair facilities for turbomachinery. It can be applied in both onshore and offshore oil & gas facilities, power generation plants, and any other industry that utilizes turbomachinery.
What components can be 3D printed?
- Additive manufacturing can be used to produce various components of turbomachinery, including blades, vanes, impellers, casings, combustion chambers, and cooling channels. These components are critical for the reliable and safe operation of centrifugal compressors, gas turbines, and special steam turbines.
Which materials can be used?
- A wide range of materials can be used in additive manufacturing for turbomachinery. This includes high-temperature alloys, superalloys, metal matrix composites, and other specialized materials suitable for turbomachinery applications. Material selection depends on factors such as mechanical properties, temperature resistance, corrosion resistance, and specific operating conditions.
How is additive manufacturing applied?
- The application of additive manufacturing involves several steps, including component design using computer-aided design (CAD) software, selection of suitable materials, optimization of build parameters, 3D printing using additive manufacturing machines, post-processing (such as machining or surface treatments), and quality control/validation to ensure reliability and safety.
Overall, additive manufacturing is applied in turbomachinery to address specific needs such as design optimization, customization, lightweighting, rapid prototyping, on-demand manufacturing/repair, and improved efficiency. It can be utilized at different stages of the turbomachinery lifecycle and in various settings to enhance reliability, safety, and operational performance in the oil & gas industry and power generation plants.
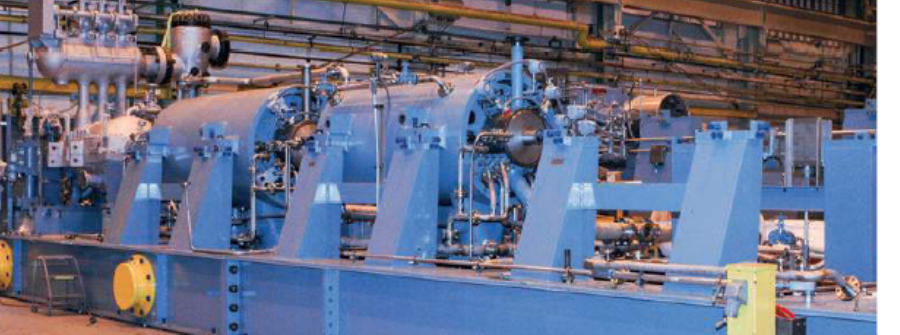
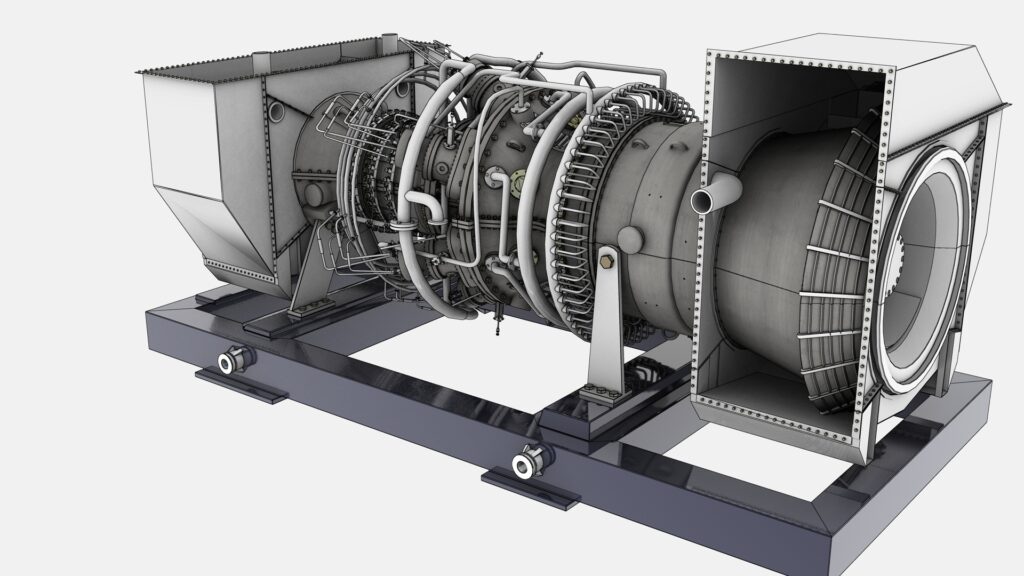
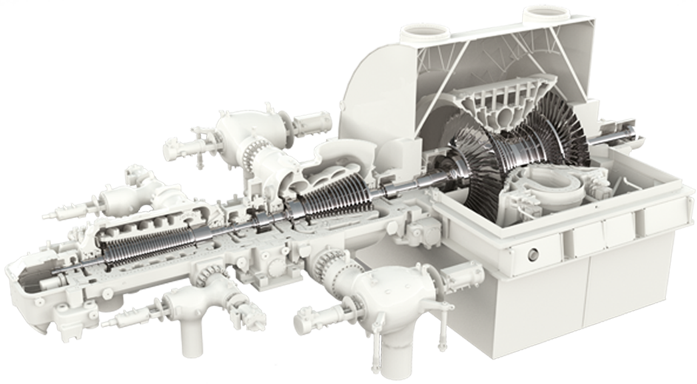
PROCEDURES, ACTIONS, STUDIES, ANALYSIS, MITIGATION AND RECOMMENDATIONS OF APPLYING ADDITIVE MANUFACTURING (3D PRINTING) IN TURBOMACHINERY
- Procedures and Actions:
- Design Validation: Thoroughly validate the additive manufacturing design through simulations, prototyping, and testing to ensure it meets performance and safety requirements.
- Material Selection: Carefully select materials suitable for turbomachinery applications, considering mechanical properties, high-temperature resistance, and corrosion resistance.
- Process Optimization: Optimize additive manufacturing parameters, such as printing speed, layer thickness, and heat treatment, to achieve desired material properties and quality.
- Post-Processing: Implement appropriate post-processing techniques, such as machining or surface treatments, to achieve required surface finish and dimensional accuracy.
- Quality Control and Validation: Establish rigorous quality control procedures to ensure consistent quality and compliance with industry standards. Validate the printed components through non-destructive testing and performance assessments.
- Studies and Analysis:
- Material Characterization: Conduct material characterization studies to understand the properties and behavior of additive manufacturing materials under relevant operating conditions.
- Failure Mode and Effects Analysis (FMEA): Perform FMEA to identify potential failure modes, assess their severity, and develop mitigation strategies to enhance reliability and safety.
- Computational Fluid Dynamics (CFD): Utilize CFD simulations to study fluid flow patterns, pressure distributions, and temperature profiles within the turbomachinery components to optimize performance and mitigate potential issues.
- Finite Element Analysis (FEA): Perform FEA to evaluate stress, strain, and deformation in critical components, ensuring structural integrity and identifying areas for design improvements.
- Mitigations and Recommendations:
- Robust Design: Optimize the design of additive manufacturing components to minimize stress concentrations, improve fluid dynamics, and enhance reliability under varying operating conditions.
- Material Testing and Certification: Conduct thorough material testing and certification processes to ensure material properties meet required standards and specifications.
- In-Service Monitoring: Implement condition monitoring systems to detect early signs of degradation or failure and enable proactive maintenance actions.
- Training and Knowledge Transfer: Train personnel involved in additive manufacturing processes to ensure their proficiency in handling and operating the equipment, as well as understanding potential risks and best practices.
- Collaboration and Industry Standards: Foster collaboration among industry stakeholders, regulatory bodies, and research institutions to develop industry standards, guidelines, and best practices specific to additive manufacturing in turbomachinery.
It’s essential to note that the specific procedures, actions, studies, analyses, mitigations, and recommendations may vary based on the unique characteristics of the turbomachinery, the selected additive manufacturing technologies, and the industry standards and regulations applicable to the oil & gas industry and power generation plants. Therefore, it is crucial to conduct comprehensive research, engage with domain experts, and adhere to relevant guidelines and standards throughout the application of additive manufacturing in turbomachinery.