ADVANCES IN THE STEAM PATH OPTIMIZATION OF SPECIAL STEAM TURBINES
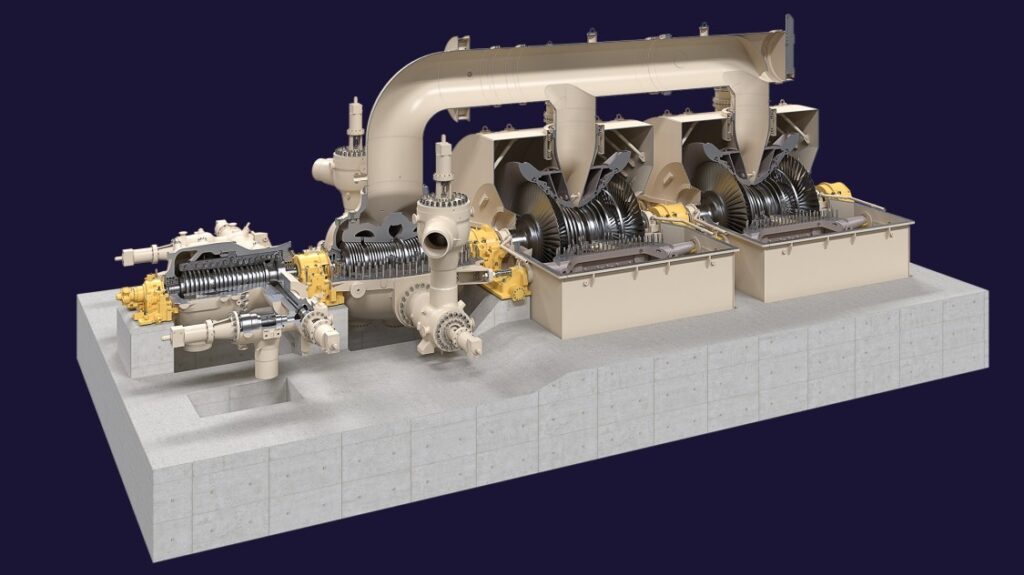
LIMITATIONS IN ENGINEERING & DESIGN TO GET THE STEAM PATH OPTIMIZATION
Space Constraints: Optimizing the steam path within the given physical space of the turbine can be challenging. Space limitations may restrict the ability to incorporate larger blade profiles, additional stages, or advanced cooling mechanisms, which can potentially limit performance improvements.
Manufacturing and Cost Considerations: Designing and manufacturing complex steam path geometries can be more challenging and costly. Special manufacturing techniques, precision machining, and quality control measures may be required, which can impact production timelines and costs.
Blade Vibrations and Resonance: Modifying the steam path geometry may influence blade dynamics and introduce the potential for increased vibrations and resonance. These dynamic effects need to be carefully evaluated to avoid detrimental impacts on turbine reliability and blade fatigue life.
Cooling and Thermal Stresses: Altering the steam path design may affect the cooling requirements and the distribution of thermal stresses within the turbine components. Ensuring effective cooling and managing thermal gradients is crucial to prevent excessive component temperatures and thermal fatigue.
Material Compatibility and Durability: Introducing changes to the steam path design may require the use of new materials or coatings. Compatibility with existing materials, as well as long-term durability and resistance to erosion, corrosion, and other degradation mechanisms, must be carefully considered.
Operational Flexibility: Steam path optimization should balance the operational flexibility of the turbine. Modifications should not hinder the turbine’s ability to handle different load demands, rapid start-ups, and load changes typically encountered in power generation plants.
Computational Complexity: Analyzing the complex fluid dynamics and thermodynamics involved in steam path optimization requires advanced computational fluid dynamics (CFD) modeling and simulation. These analyses can be computationally intensive and require specialized expertise.
Integration Challenges: Implementing steam path optimization may require integration with other turbine systems, such as control systems, cooling systems, and sealing arrangements. Ensuring seamless integration and compatibility with existing equipment can present engineering challenges.
Maintenance and Serviceability: Changes to the steam path design should consider the impact on maintenance and serviceability. Accessibility to components, ease of inspection, and maintenance requirements should be evaluated to minimize downtime and ensure effective maintenance practices.
Regulatory Compliance: Any modifications to the steam path design must comply with relevant industry standards, codes, and regulations. These include safety standards, environmental regulations, and performance requirements, which may impose additional design constraints.
It is essential to carefully evaluate and address these limitations during the engineering and design phase of steam path optimization for special steam turbines. Collaboration with experienced turbine manufacturers, engineering consultants, and industry experts is crucial to navigate these limitations effectively and achieve the desired high reliability, availability, safety, and operational performance.
WHY, WHEN, WHERE, WHAT, WHICH AND HOW TO GET STEAM PATH OPTIMIZATION IN SPECIAL STEAM TURBINES
- Why:
- Steam path optimization aims to improve turbine efficiency, performance, and reliability, resulting in reduced downtime and increased availability.
- It enhances the overall operational performance of the steam turbine, enabling efficient power generation and minimizing energy losses.
- When:
- Steam path optimization can be considered during the design phase of a new turbine or as part of a retrofit or upgrade project for existing turbines.
- It can also be beneficial when addressing specific performance issues or to meet changing operational requirements.
- Where:
- Steam path optimization is applicable to special steam turbines used in oil & gas facilities, power generation plants, combined cycle plants, and cogeneration plants.
- It can be implemented in various turbine configurations, including extraction, backpressure, condensing, and reheat turbines.
- What:
- Steam path optimization involves optimizing the flow path geometry, blade profiles, inlet and outlet areas, and internal cooling systems of the turbine.
- It includes evaluating and improving aspects such as blade aerodynamics, steam flow distribution, velocity profiles, and blade surface cooling.
- Which:
- The selection of specific optimization techniques and methods depends on the turbine design, operating conditions, and goals of the steam path optimization.
- Consideration should be given to factors such as blade shape, twist angle, aspect ratio, steam expansion, and control of secondary flow effects.
- How:
- Conduct a thorough assessment of the existing steam path design, performance data, and operational conditions.
- Utilize advanced computational fluid dynamics (CFD) modeling and simulation techniques to analyze and optimize the flow path geometry and aerodynamics.
- Consider blade design modifications, such as profiling, twist, or stacking, to enhance efficiency and reduce losses.
- Evaluate and optimize the cooling systems to ensure proper blade temperature distribution and minimize thermal stresses.
- Perform performance testing and validation to verify the improvements achieved through steam path optimization.
- Collaborate with turbine manufacturers, engineering consultants, and experts in steam turbine design and optimization for guidance and expertise.
- Comply with relevant international standards, codes, and regulations, ensuring safety, environmental compliance, and performance requirements.
It is important to note that steam path optimization is a specialized and complex process that requires expertise in steam turbine design, fluid dynamics, and computational modeling. Collaboration with experienced professionals and adherence to industry best practices are crucial to successfully achieve the desired high reliability, availability, safety, and operational performance in special steam turbines.
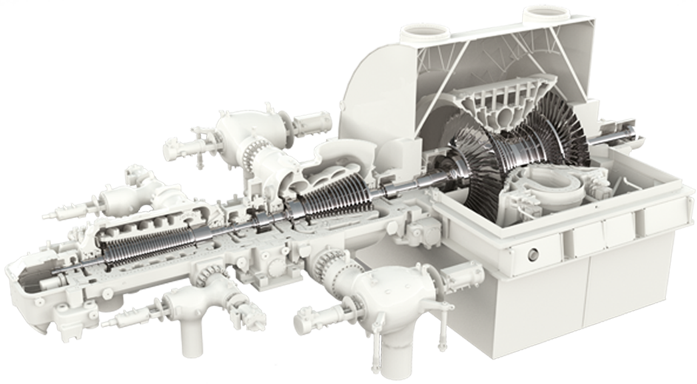
PROCEDURES, ACTIONS, STUDIES, ANALYSIS, MITIGATIONS AND RECOMMENDATIONS TO GET STEAM PATH OPTIMIZATION IN SPECIAL STEAM TURBINES
- Procedures:
- Develop a comprehensive steam path optimization procedure that outlines the steps, responsibilities, and criteria for evaluating and optimizing the turbine’s flow path.
- Define a clear process for data collection, performance assessment, design modifications, and verification of the optimized steam path.
- Actions:
- Gather operational data and performance information of the existing steam turbine to establish a baseline for evaluation.
- Conduct detailed inspections and measurements of the turbine components, including blade profiles, clearances, and cooling systems.
- Collaborate with turbine manufacturers, engineering consultants, and experts to gain insights into turbine design, performance, and optimization techniques.
- Studies and Analysis:
- Perform computational fluid dynamics (CFD) simulations to analyze the flow path, aerodynamics, and thermal characteristics of the turbine.
- Utilize CFD modeling to identify areas of flow separation, high turbulence, or inefficient energy conversion within the steam path.
- Conduct sensitivity analyses to evaluate the impact of design modifications on turbine performance and efficiency.
- Design Modifications:
- Optimize blade profiles, stacking, and twist angles to improve aerodynamic efficiency and reduce losses.
- Enhance internal cooling systems to improve blade temperature distribution and minimize thermal stresses.
- Optimize inlet and outlet areas, as well as nozzle and diaphragm designs, to ensure smooth and efficient flow transitions.
- Performance Testing and Verification:
- Conduct performance testing and validation to verify the improvements achieved through steam path optimization.
- Measure key performance indicators, such as turbine efficiency, power output, and steam consumption, to assess the effectiveness of the optimization efforts.
- Compare the optimized turbine’s performance with the baseline data to evaluate the achieved reliability, availability, and operational performance.
- Mitigations:
- Address any potential risks associated with design modifications, such as blade vibrations, resonance, or increased thermal stresses.
- Implement appropriate mitigations based on the findings of structural and dynamic analyses to ensure safe and reliable turbine operation.
- Conduct risk assessments and hazard analyses to identify potential safety risks and propose suitable mitigation strategies.
- Recommendations:
- Regularly monitor and maintain the optimized steam path to ensure continued high performance and reliability.
- Incorporate advanced condition monitoring and predictive maintenance techniques to detect and address any early signs of performance degradation or component issues.
- Stay updated with industry advancements and best practices in steam turbine design and optimization to continuously improve performance and operational efficiency.
It is important to note that steam path optimization for special steam turbines is a complex and specialized field that requires expertise in turbine design, fluid dynamics, and computational modeling. Collaboration with experienced turbine manufacturers, engineering consultants, and industry experts is crucial to navigate these procedures, analyses, mitigations, and recommendations effectively, ensuring the achievement of high reliability, availability, safety, and operational performance.