ADVANCES IN TECHNOLOGY FOR CENTRIFUGAL COMPRESSORS
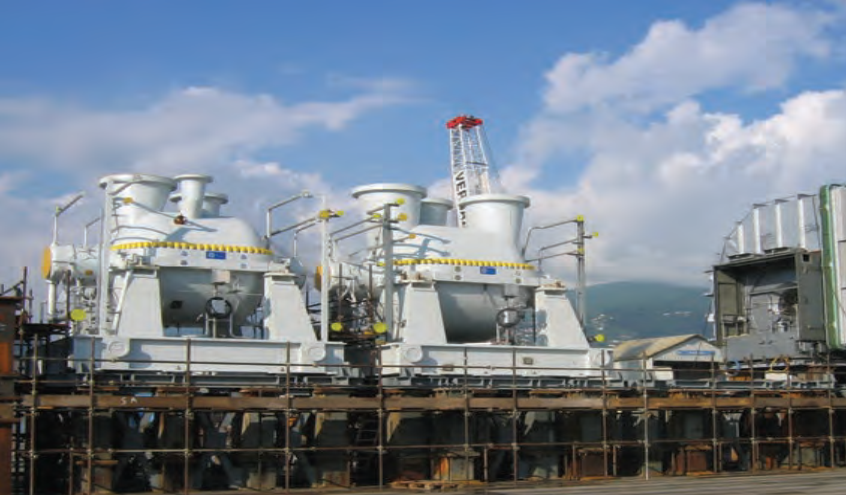
ROTODYNAMIC DESIGN IN CENTRIFUGAL COMPRESSORS
DEVELOPMENT IN DRY GAS SEALS SYSTEMS
Firstly, let’s consider the lateral analysis, which is an essential component of the rotodynamic design. This analysis focuses on the evaluation of the lateral stability of the compressor’s components, such as the impeller, bearings, and casing. The analysis considers the lateral loads generated during operation and ensures that the components can withstand these loads without experiencing excessive deflection or deformation. The results of the lateral analysis are used to determine the optimal thickness and stiffness of the components, ensuring that they can withstand the lateral forces generated during operation.
Similarly, torsional analysis is also a vital aspect of the rotodynamic design. It focuses on the evaluation of the torsional stability of the compressor’s components, which can experience twisting forces during operation. These forces can lead to excessive stresses and deformation, causing critical failures or unscheduled shutdowns. Torsional analysis considers the torsional stiffness and damping of the components to ensure that they can withstand the twisting forces generated during operation.
Furthermore, stiffness and damping are also crucial considerations during the rotodynamic design. These factors affect the dynamic behavior of the compressor components, such as the impeller, shaft, and bearings, and can influence the natural frequencies of these components. The design ensures that the stiffness and damping of the components are optimized to reduce the risk of fatigue failures and vibration problems, which can lead to critical failures or unscheduled shutdowns.
The critical speed map is another essential component of the rotodynamic design. This map identifies the speeds at which the compressor is prone to resonance, which can cause severe damage or failure. The map considers the natural frequencies of the compressor components and the rotational speed of the compressor to determine the critical speeds. The design ensures that the compressor operates at speeds outside the critical speed range to prevent resonance and avoid critical failures.
Stability analysis is also essential during the rotodynamic design to ensure that the compressor operates within a stable range of flow rates and pressure ratios. The analysis considers the dynamic behavior of the compressor components and identifies the stability limits of the compressor. The design ensures that the compressor operates within these limits to avoid surging or stalling, which can lead to unscheduled shutdowns and severe damage to the compressor.
Finally, typical mode shapes are analyzed during the design phase to identify any potential resonance or vibration modes that may cause critical failures. The analysis considers the natural frequencies of the compressor components and determines the mode shapes that can lead to resonance or vibration problems. The design ensures that the compressor components are designed to avoid these modes, reducing the risk of critical failures or unscheduled shutdowns.
In conclusion, the rotodynamic design of industrial centrifugal compressors is a complex process that considers several critical factors to ensure the reliability, maintainability, and safety of the compressor. These factors include lateral and torsional analysis, stiffness, damping, critical speed map, stability analysis, and typical mode shapes. The design ensures that the compressor can operate efficiently without experiencing critical failures or unscheduled shutdowns, improving the overall performance and longevity of the compressor.
In recent years, dry gas seal systems have become increasingly popular in centrifugal compressors in the oil, gas, and petrochemical industries. These seal systems offer several advantages over other mechanical seal designs, including improved reliability, reduced maintenance requirements, and reduced risk of environmental leaks.
API 692 is a widely recognized standard for the engineering and design of dry gas seal systems for centrifugal compressors. This standard provides guidelines for the selection of suitable materials, design considerations, and testing procedures to ensure the reliability and safety of the seal system. By following these guidelines, engineers and designers can ensure that the dry gas seal system is properly designed to meet the specific operating conditions and requirements of the compressor.
One major advantage of dry gas seal systems is their ability to operate without any liquid lubrication, which eliminates the need for oil-based lubrication systems that can contribute to environmental leaks. This is particularly important in industries where environmental regulations are strict, and any leaks or spills can have significant consequences for the environment and the surrounding communities.
Another advantage of dry gas seal systems is their reduced maintenance requirements. Traditional mechanical seals require regular maintenance and replacement, which can be time-consuming and costly. Dry gas seals, on the other hand, can operate for extended periods of time without maintenance or replacement, reducing the overall lifecycle cost of the compressor.
Dry gas seals also offer improved reliability compared to other seal designs. The absence of liquid lubricants reduces the risk of seal face damage, and the seal design allows for self-cleaning of the seal faces, reducing the risk of blockages and failures. Additionally, dry gas seals are less susceptible to process upsets and contamination, which can lead to premature failures in other seal designs.
Finally, dry gas seal systems can be retrofitted to existing compressors, allowing operators to upgrade their equipment without the need for significant modifications or downtime. This can be particularly beneficial for operators looking to improve the reliability and safety of their existing equipment while minimizing disruption to their operations.
In conclusion, dry gas seal systems offer several advantages over other mechanical seal designs in terms of reliability, maintenance requirements, and environmental safety. By following the guidelines set out in API 692, engineers and designers can ensure that the dry gas seal system is properly designed to meet the specific operating conditions and requirements of the compressor, and operators can benefit from improved reliability and reduced environmental risk in both new projects and existing operating plants.
LIMITS IN ENGINEERING & DESIGN ABOUT ROTODYNAMIC ANALYSIS
LIMITS IN ENGINEERING & DESIGN IN DRY GAS SEALS SYSTEMS
While rotodynamic analysis is crucial in the engineering and design of industrial centrifugal compressors, it is important to recognize that there are limits to what can be achieved through analysis alone. The design process involves a balance of trade-offs between performance, reliability, and cost, and there are practical limitations to what can be achieved within these constraints.
One limitation of the rotodynamic analysis is the accuracy of the assumptions used in the analysis. Simplifying assumptions are often made to simplify the analysis, but these assumptions can introduce errors into the design. Additionally, the analysis is typically based on a steady-state model, which may not accurately represent the transient behavior of the compressor during start-up or shutdown. Therefore, it is essential to validate the assumptions used in the analysis through testing and modeling to ensure the accuracy of the design.
Another limitation of the rotodynamic analysis is the uncertainty in the operating conditions of the compressor. The analysis assumes a specific range of operating conditions, such as flow rate and pressure, but the actual operating conditions may vary due to changes in the process or environmental conditions. Therefore, the design must incorporate sufficient margins to account for these uncertainties to ensure the reliability and safety of the compressor.
Furthermore, there are limitations in the available materials and manufacturing processes that can affect the design of the compressor. The design must consider the mechanical properties of the materials used, such as the strength and ductility, to ensure that the compressor can withstand the loads and stresses experienced during operation. Additionally, the design must consider the manufacturing process used to produce the components, such as casting or forging, to ensure that the components can be produced with the required accuracy and quality.
Cost is also a limitation in the engineering and design of industrial centrifugal compressors. The design must balance the cost of the components, the operating costs, and the overall reliability and safety of the compressor. While a more robust design may increase the reliability and safety of the compressor, it may also increase the cost of the compressor. Therefore, the design must balance these trade-offs to achieve the desired performance and reliability while minimizing costs.
Finally, the design of the compressor must consider the maintenance and repair requirements of the compressor. While a more complex design may improve the performance and reliability of the compressor, it may also increase the complexity and cost of maintenance and repair. Therefore, the design must consider the practicality of maintaining and repairing the compressor and ensure that the design can be easily serviced and repaired when necessary.
In conclusion, while rotodynamic analysis is an essential aspect of the engineering and design of industrial centrifugal compressors, there are limitations to what can be achieved through analysis alone. The design process must balance the trade-offs between performance, reliability, cost, and practicality to achieve the desired outcomes. By considering these limitations during the design phase, the design can improve the reliability, maintainability, and safety of the compressor and reduce the risk of critical failures and unscheduled shutdowns.
While dry gas seal systems offer many advantages over other seal designs, there are some limitations that must be considered during the engineering and design phase to ensure high reliability and avoid critical failures and environmental leaks in the oil, gas, and petrochemical industries.
One major limitation is that dry gas seals require a clean and dry gas supply to operate properly. Any impurities, moisture, or other contaminants in the gas can cause damage to the seal faces and reduce the effectiveness of the seal. Therefore, it is essential to ensure that the gas supply is properly filtered and dried before it reaches the dry gas seal system. This requires careful selection of filtration and drying equipment, as well as appropriate maintenance procedures to ensure that the gas supply remains clean and dry over time.
Another limitation is the need for appropriate venting and monitoring systems to prevent the build-up of pressure or gases within the seal chamber. Excessive pressure or gas accumulation can cause seal face damage or even catastrophic failure, leading to unplanned downtime, equipment damage, and potential environmental leaks. Therefore, it is important to design the seal system with appropriate venting and monitoring systems to ensure that any pressure or gas buildup is safely vented before it can cause any damage.
Additionally, dry gas seals require more precise alignment and balancing than other seal designs. Even small misalignments or imbalances can cause increased wear and damage to the seal faces, leading to reduced reliability and increased maintenance requirements. Therefore, it is important to ensure that the compressor rotor is properly balanced and aligned during installation and that appropriate monitoring systems are in place to detect any changes in alignment or balance over time.
Finally, dry gas seal systems may not be suitable for all types of applications or operating conditions. In some cases, other seal designs may be more appropriate, depending on factors such as the gas composition, pressure, temperature, and flow rates. Therefore, it is important to carefully consider the specific operating conditions and requirements of the compressor when selecting the appropriate seal system.
In conclusion, while dry gas seal systems offer many benefits in terms of reliability and environmental safety, there are also several limitations that must be considered during the engineering and design phase to ensure high reliability and avoid critical failures and environmental leaks in the oil, gas, and petrochemical industries. By carefully selecting appropriate equipment, designing appropriate venting and monitoring systems, ensuring proper alignment and balancing, and considering the specific operating conditions and requirements of the compressor, engineers and designers can ensure that the dry gas seal system is properly designed to meet the specific needs of the application.
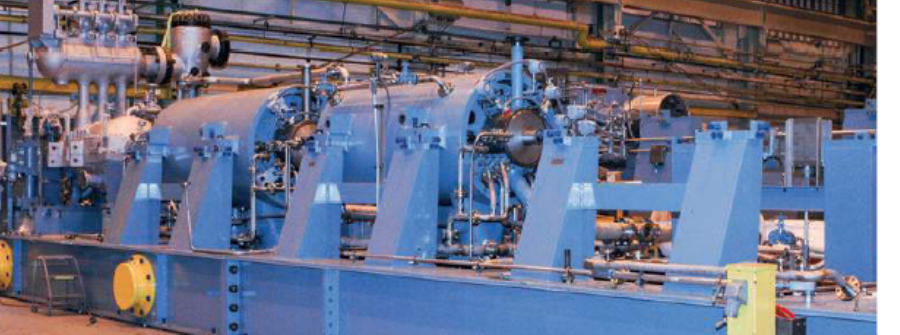
CRITICAL RISKS IN BAD ROTODYNAMIC ANALYSIS OR STUDIES CAUSING FAILURES
PROCEDURES, ACTIONS, STUDIES, MITIGATIONS, RECOMMENDATIONS TO GET HIGH RELIABILITY IN DGS SYSTEMS
Inadequate rotodynamic studies or analysis can pose critical risks to the reliability, maintainability, and safety of industrial centrifugal compressors, which can lead to critical failures and unscheduled shutdowns. These risks can arise due to a number of factors, including errors in the assumptions made during the analysis, insufficient consideration of the operating conditions and environmental factors, and a lack of understanding of the mechanical properties of the materials used in the compressor.
One critical risk of bad rotodynamic studies is the failure to accurately predict the critical speed of the compressor. The critical speed is the rotational speed at which the natural frequency of the rotor coincides with the frequency of one or more modes of vibration, leading to excessive vibrations and potentially catastrophic failures. Inaccurate predictions of the critical speed can result in the selection of a rotor that is not properly designed to avoid resonance, leading to dangerous levels of vibrations and potential failures.
Another critical risk of bad rotodynamic studies is the failure to properly account for lateral and torsional vibrations in the compressor. These vibrations can result in excessive stresses on the compressor components, leading to fatigue failure and reduced reliability. Additionally, if the compressor is not properly designed to avoid resonance, these vibrations can lead to excessive wear on the bearings and other components, reducing the overall lifespan of the compressor.
Insufficient consideration of damping and stiffness can also pose critical risks to the reliability and safety of the compressor. Damping is essential in reducing the amplitude of vibrations in the compressor, while stiffness is crucial in maintaining the integrity of the compressor under operating loads. If these factors are not properly accounted for in the analysis, the compressor may be subject to excessive vibrations and stresses that can lead to critical failures.
Finally, bad rotodynamic studies can result in the selection of materials and manufacturing processes that are not suitable for the operating conditions of the compressor. For example, if the compressor is operating in a corrosive environment, the selection of materials that are not resistant to corrosion can lead to premature failure of the compressor components. Similarly, if the manufacturing process used to produce the components is not capable of producing components with the required accuracy and quality, the resulting compressor may not perform as expected and may be subject to premature failure.
In conclusion, the risks of bad rotodynamic studies or analysis in industrial centrifugal compressors can have serious consequences for the reliability, maintainability, and safety of the compressor, leading to critical failures and unscheduled shutdowns. By properly accounting for factors such as critical speed, lateral and torsional vibrations, damping and stiffness, and materials selection and manufacturing processes during the engineering and design phase, the risks of these failures can be mitigated, and the overall reliability and safety of the compressor can be improved.
To ensure high reliability and avoid critical failures and environmental leaks in dry gas seal systems for centrifugal compressors, several procedures, actions, studies, mitigations, and recommendations can be applied during the engineering and design phase and throughout the lifecycle of the equipment.
Gas Supply Preparation: One of the critical steps in ensuring the reliability of dry gas seal systems is to prepare the gas supply. This involves the filtration and drying of gas before it enters the dry gas seal system. The gas supply should be free from contaminants, moisture, and other impurities to prevent damage to the seal faces.
Venting and Monitoring Systems: Proper venting and monitoring systems should be in place to prevent the build-up of pressure or gases within the seal chamber. An accumulation of pressure or gas can lead to seal face damage or catastrophic failure, leading to equipment damage, unplanned downtime, and potential environmental leaks.
Alignment and Balancing: Proper alignment and balancing of the compressor rotor are crucial to ensure the longevity of the dry gas seal system. Even a small misalignment or imbalance can cause increased wear and damage to the seal faces, leading to reduced reliability and increased maintenance requirements. Therefore, it is important to ensure that the compressor rotor is correctly balanced and aligned during installation and appropriate monitoring systems are in place to detect any changes in alignment or balance over time.
Maintenance and Inspection: Regular maintenance and inspection of the dry gas seal system are necessary to ensure its reliability and longevity. Maintenance tasks may include replacing damaged or worn seal faces, monitoring seal performance, and inspecting the venting and monitoring systems.
Risk Assessment and Mitigation: A risk assessment should be conducted to identify potential hazards and risks associated with the dry gas seal system. Appropriate mitigation measures should be taken to reduce the likelihood of failure and to minimize the consequences of any failure.
Material Selection: The selection of appropriate materials for the dry gas seal system is crucial to ensure the longevity and reliability of the system. The selection of materials should take into account factors such as the gas composition, temperature, and pressure, as well as the operating conditions and requirements of the compressor.
Training and Education: Proper training and education for operators and maintenance personnel are critical to ensuring the reliable operation of the dry gas seal system. Operators and maintenance personnel should be knowledgeable about the design and operation of the dry gas seal system and should be trained to detect and respond to any potential issues or malfunctions.
In conclusion, to ensure high reliability and avoid critical failures and environmental leaks in dry gas seal systems for centrifugal compressors, several procedures, actions, studies, mitigations, and recommendations can be applied during the engineering and design phase and throughout the lifecycle of the equipment. By taking appropriate measures, engineers and designers can ensure the safe and reliable operation of the dry gas seal system in the oil, gas, and petrochemical industries.
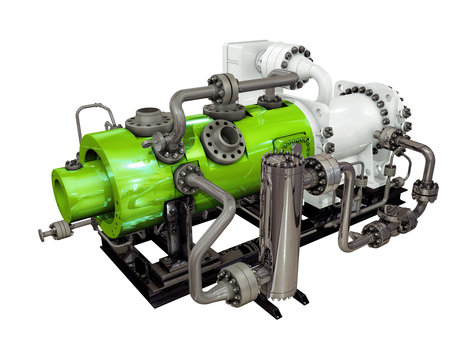
ADVANCES IN SUBSEA COMPRESSION SYSTEMS
RESONANCE & STRUCTURAL PROBLEMS IN CENTRIFUGAL COMPRESSORS
Subsea compression systems using centrifugal compressors have experienced significant advances in recent years, leading to improvements in reliability, safety, and environmental protection.
One of the main benefits of subsea compression systems is that they allow for the compression of gas at the wellhead, reducing the need for complex and expensive surface facilities. This results in cost savings and improved operational efficiency.
Advances in engineering and design have enabled the development of highly reliable subsea compression systems. For example, the use of dry gas seals instead of traditional mechanical seals has greatly reduced the risk of environmental leaks. Additionally, the development of subsea variable frequency drives has improved the efficiency and performance of subsea compressors, while also reducing the need for maintenance.
In terms of mitigating risks, thorough studies and simulations are performed during the design phase to identify potential hazards and assess the performance of the system under different operating conditions. This includes analyzing the effects of temperature and pressure fluctuations, as well as the impact of water depth and subsea currents.
Recommendations for improving reliability in subsea compression systems include the use of advanced materials and coatings to protect against corrosion, the incorporation of redundant systems and sensors to improve fault tolerance, and the implementation of advanced control systems to optimize performance and minimize downtime.
Overall, the advances made in subsea compression systems using centrifugal compressors have greatly improved the reliability and safety of these systems, making them an attractive option for new projects and existing plants in the oil, gas, and petrochemical industries.
Resonance is a critical problem associated with centrifugal compressors that can cause mechanical and structural issues leading to failures and environmental hazards. Resonance is a condition where the natural frequency of the compressor or its components matches with the frequency of the vibrations induced by the compressor operation. This can lead to amplified vibrations, which can cause fatigue and wear and tear of the compressor components, leading to mechanical failure.
Resonance can occur due to various reasons, such as improper design, inadequate material selection, incorrect assembly, or changes in the operating conditions. The resonance can occur in various parts of the compressor, such as the impeller, shaft, bearings, seals, and foundation. The resonance of the impeller and shaft can cause high stresses leading to cracking and ultimately failure. Resonance of the bearings can cause excessive wear and tear, leading to premature failure.
The resonance can also affect the foundation of the compressor, leading to structural damage and leakage of the process fluid. The leakage of the process fluid can cause environmental hazards and safety risks to the workers in the plant.
To avoid resonance-related issues, it is crucial to perform thorough engineering and design studies during the design phase of the compressor. The studies should include dynamic analysis, modal analysis, and frequency response analysis to identify and mitigate potential resonance issues. Material selection, assembly procedures, and operating conditions should also be carefully considered to avoid resonance-related failures.
During the maintenance and operation phase, it is essential to monitor the compressor’s vibrations regularly and perform vibration analysis to detect and diagnose any resonance-related issues. Any potential issues should be addressed promptly to avoid critical failures and environmental hazards. It is also crucial to train the plant personnel in resonance-related issues and provide them with proper procedures and tools to mitigate the risks.
LIMITS IN ENGINEERING & DESIGN FOR SUBSEA COMPRESSION SYSTEMS
LIMITS IN ENGINEERING & DESIGN ABOUT RESONANCE & STRUCTURAL PROBLEMS IN CENT. COMPRESSORS
Despite the advancements in subsea compression systems using centrifugal compressors, there are still limits in engineering and design that must be considered to ensure the reliability and safety of these systems.
One limitation is the need for regular maintenance and inspection of subsea components, which can be challenging due to the remote location and harsh operating conditions. Access to subsea equipment is limited and maintenance activities may require specialized tools and equipment, as well as experienced personnel.
Another limitation is the impact of environmental factors such as water depth, temperature, and pressure on the performance of the system. These factors can affect the reliability and efficiency of the subsea compression system, and must be carefully considered during the design phase to ensure that the system can operate safely and effectively under a range of conditions.
Furthermore, subsea compression systems are often subject to stringent regulatory requirements to ensure environmental protection, which may impose additional design and operational limitations. For example, regulations may require the use of certain materials or the implementation of specific safety features to prevent environmental leaks.
In order to mitigate these limitations and improve the reliability and safety of subsea compression systems, engineers and designers must carefully consider the design and operation of the system. This may include the use of advanced materials and coatings to protect against corrosion, the incorporation of redundant systems and sensors to improve fault tolerance, and the implementation of advanced control systems to optimize performance and minimize downtime. In addition, regular maintenance and inspection of subsea equipment is essential to ensure the continued safe and effective operation of the system.
The limits in engineering and design associated with resonance, mechanical, and structural issues using centrifugal compressors are crucial to ensuring high reliability and preventing critical failures in oil, gas, and petrochemical industries. These limits can include limitations in materials selection, design, and manufacturing processes that can affect the compressor’s mechanical and structural integrity.
One of the primary limitations is the selection of materials for the compressor components. The materials used must have high fatigue resistance and be able to withstand high stress levels, especially in areas prone to resonance, such as impellers and shafts. The design must also consider factors such as manufacturing tolerances, surface roughness, and other mechanical properties that can affect the compressor’s performance and reliability.
Another limitation is the design of the compressor system to avoid resonant frequencies that can cause excessive vibration and damage to the components. This includes selecting an appropriate compressor speed, blade count, and spacing to avoid excitation of resonant frequencies. Adequate damping and stiffness must also be designed into the system to prevent vibration and other structural issues.
Furthermore, proper maintenance and operation practices must be established to ensure the continued reliability of the compressor. This includes regular inspections, monitoring of vibration levels, and timely repairs or replacements of components as needed.
In summary, the limits in engineering and design associated with resonance, mechanical, and structural issues using centrifugal compressors include materials selection, design considerations, and proper maintenance and operation practices. These limitations must be carefully considered to improve the reliability and prevent critical failures in new projects and existing plants in oil, gas, and petrochemical industries.
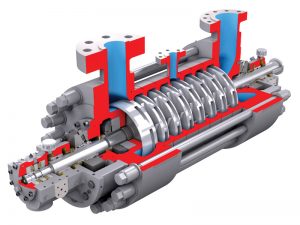
PROCEDURES, ACTIONS, STUDIES, RECOMMENDATIONS, AND CRITICAL RISKS IN SUBSEA COMPRESSION SYSTEMS
CRITICAL RISKS AND PROCEDURES, ACTIONS, STUDIES, MITIGATION AND RECOMMENDATIONS IN RESONACE & STRUCTURAL PROBLEMS
Subsea compression systems using centrifugal compressors face a range of critical risks and potential failures that can impact the reliability, safety, and environmental impact of the system. These risks and failures must be carefully managed through a range of procedures, actions, studies, mitigations, and recommendations to ensure that the system can operate safely and effectively over its entire lifecycle.
One critical risk for subsea compression systems is the potential for environmental leaks, which can have severe consequences for marine life and the surrounding ecosystem. To mitigate this risk, the system should be designed with multiple barriers and redundancies to prevent leaks from occurring. In addition, regular inspection and maintenance should be conducted to identify and address potential leaks before they become a critical issue.
Another critical risk is the potential for equipment failure due to harsh operating conditions and the remote location of subsea components. To address this risk, the system should be designed with a high degree of fault tolerance and redundancy, including multiple compressors and other critical components. Regular maintenance and inspection should also be conducted to identify and address potential failures before they result in a system shutdown or critical failure.
To improve the reliability, maintenance, and operation of subsea compression systems using centrifugal compressors, a range of procedures, actions, studies, and recommendations should be implemented. These may include:
- Conducting detailed engineering and design studies to optimize the system for the specific operating conditions and environmental factors that will be encountered.
- Incorporating advanced monitoring and control systems to optimize performance and reduce downtime.
- Implementing regular maintenance and inspection procedures to identify and address potential issues before they become critical.
- Conducting risk assessments and contingency planning to prepare for potential failures and minimize their impact on the system.
- Implementing advanced communication systems to enable remote monitoring and control of subsea equipment, reducing the need for personnel to access the site in person.
- Conducting regular training and competency assessments for personnel involved in the operation and maintenance of the system to ensure that they are able to perform their duties safely and effectively.
By implementing these procedures, actions, studies, and recommendations, subsea compression systems using centrifugal compressors can achieve high levels of reliability, safety, and environmental performance, reducing the risk of critical failures and unscheduled shutdowns, and helping to protect the surrounding ecosystem.
The critical risks associated with resonance, mechanical and structural issues in centrifugal compressors include increased vibrations leading to mechanical failure, decreased efficiency and increased maintenance costs. Additionally, resonance can cause severe structural damage to the compressor and surrounding equipment.
To mitigate these risks, it is essential to conduct thorough engineering and design studies, including finite element analysis (FEA) and modal analysis, to identify potential resonance and mechanical issues. These studies should be carried out during the design phase and continuously throughout the operation of the compressor.
Procedures for mitigating these risks include the installation of vibration monitoring systems and regular inspections of the compressor and its surrounding equipment to identify any early signs of resonance, mechanical or structural issues. The use of appropriate material selection and robust design principles, such as avoiding critical speed zones and ensuring adequate stiffness and damping, can also help prevent resonance issues.
It is recommended to carry out regular maintenance on the compressor, including vibration analysis, lubrication analysis, and mechanical inspections to detect and prevent any issues that could lead to resonance. Additionally, it is essential to train personnel to recognize the early warning signs of resonance and take corrective actions before they escalate into critical failures.
Overall, it is critical to prioritize reliability in the design, maintenance, and operation of centrifugal compressors to avoid resonance-related risks and ensure the safety and efficiency of oil, gas and petrochemical plants.
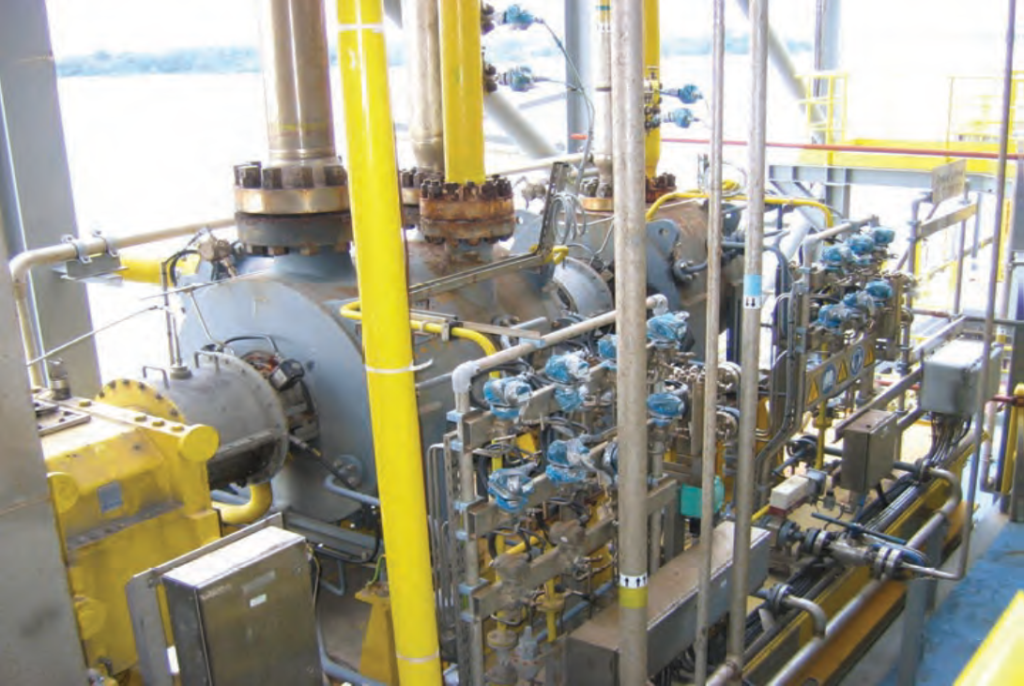