FACTORS IMPACTING MAINTAINABILITY - GAS TURBINES
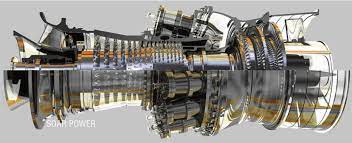
some critical factors that can affect or impact the maintainability of gas turbines:
Operating Conditions: The operating conditions of gas turbines can significantly impact their maintainability. Extreme temperatures, high humidity, and other environmental factors can cause wear and tear on components and result in more frequent maintenance requirements. Recommendations include conducting regular monitoring of operating conditions, taking corrective actions when necessary, and ensuring that the gas turbine is designed to operate in specific environmental conditions.
Maintenance Procedures and Practices: The maintenance procedures and practices used for gas turbines can also affect their maintainability. Poor maintenance practices can result in missed inspections, inadequate lubrication, or incorrect repairs, leading to increased downtime and costs. Recommendations include developing a comprehensive maintenance plan, using qualified and experienced personnel, and ensuring that all maintenance is properly documented.
Design and Equipment Selection: The initial design and equipment selection of gas turbines can have a significant impact on their maintainability. Poor equipment selection can result in frequent breakdowns and maintenance, leading to higher costs and downtime. Recommendations include reviewing the design and equipment selection before installation, selecting components that are easy to access and maintain, and ensuring that the gas turbine is designed for the specific operating conditions.
Component Access: The accessibility of components within gas turbines can also impact their maintainability. Poor access to critical components can lead to increased downtime and higher maintenance costs. Recommendations include designing gas turbines with easy access to critical components, conducting regular inspections to identify any accessibility issues, and making necessary modifications to improve access.
Quality of Materials: The quality of materials used in the construction of gas turbines can have a significant impact on their maintainability. Poor quality materials can result in increased wear and tear, corrosion, or other damage, leading to more frequent repairs and maintenance requirements. Recommendations include selecting high-quality materials that are resistant to wear, corrosion, and other damage, and ensuring that the materials are compatible with the specific operating conditions.
Training and Experience of Personnel: The training and experience of personnel involved in maintaining gas turbines can also impact their maintainability. Lack of training or experience can lead to mistakes or incorrect maintenance procedures, leading to increased downtime and costs. Recommendations include providing regular training and development opportunities for maintenance personnel, ensuring that they are familiar with the specific gas turbine design and operating conditions, and implementing a rigorous quality control process.
Data Analysis and Condition Monitoring: The use of data analysis and condition monitoring techniques can help to identify potential issues with gas turbines before they result in downtime or costly repairs. Recommendations include implementing a condition monitoring program, regularly collecting and analyzing data from gas turbines, and using the results to inform maintenance and repair decisions.
Overall, it is important to develop and implement a comprehensive maintenance program that addresses each of these critical factors to ensure the continued reliable operation of gas turbines. This program should include regular inspections, maintenance, and repairs, as well as ongoing monitoring and analysis of the gas turbine’s performance. By following these recommendations, the maintainability of gas turbines in both new and existing plants can be significantly improved.
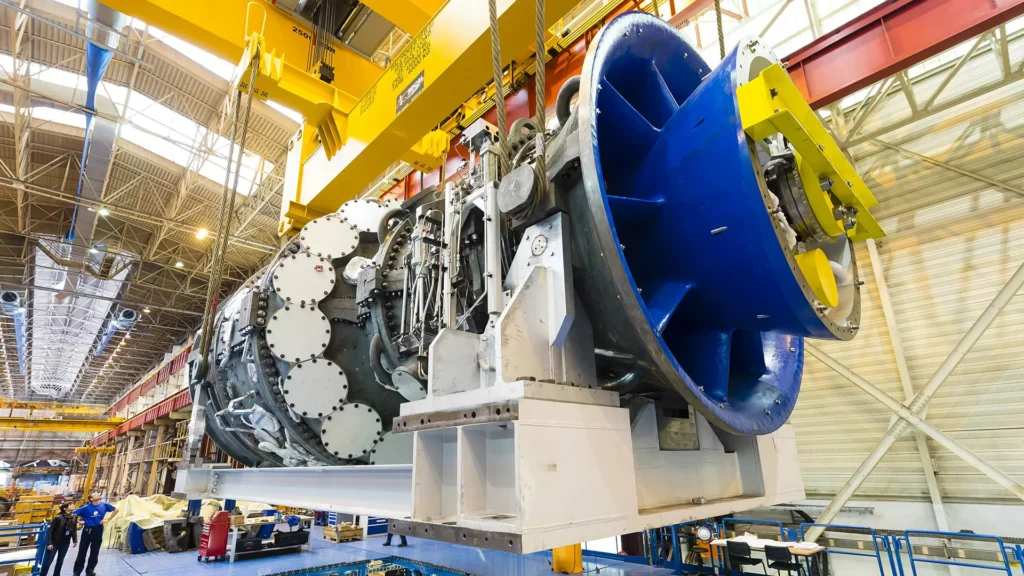
WHY, WHEN, WHERE, WHAT, WHICH, HOW TO APPLY MAINTAINABILITY STUDIES & ANALYSIS
To apply maintainability studies and analysis in gas turbines and improve maintainability, reliability, availability, and safety in existing plants and new projects for power generation plants, as well as the oil, gas, and petrochemical industries, let’s explore the details of why, when, where, what, which, and how to apply these studies:
Why apply maintainability studies and analysis?
- Improve Reliability: Maintainability studies identify potential failure points, weaknesses, and vulnerabilities in gas turbines, allowing for targeted improvements to enhance reliability and prevent unexpected failures.
- Enhance Availability: By identifying and addressing maintenance-related issues, maintainability studies aim to reduce downtime and increase the availability of gas turbines, ensuring continuous power generation and operational efficiency.
- Increase Safety: Thorough maintainability analysis ensures that maintenance tasks are carried out safely, minimizing the risk of accidents, malfunctions, and hazards to personnel and equipment.
- Optimize Cost and Resources: By optimizing maintenance activities, identifying critical components, and planning preventive measures, maintainability studies help allocate resources efficiently and reduce overall maintenance costs.
When to apply maintainability studies and analysis?
- Design Phase: Maintainability studies should be conducted during the design and engineering phase of gas turbines to optimize their maintainability, considering factors such as component accessibility, ease of inspection, and repairability. Early application ensures that design features align with maintainability objectives.
- Existing Plants: Maintainability studies can be applied at any stage in the lifecycle of existing plants to assess and improve the maintenance strategies and procedures for gas turbines. This includes routine maintenance, inspections, overhauls, and retrofits.
Where to apply maintainability studies and analysis?
- Design and Engineering: Apply maintainability studies during the design and engineering process of gas turbines to influence factors such as component layout, accessibility, ease of maintenance, and the use of standard or modular designs.
- Maintenance Planning: Utilize maintainability analysis to develop effective maintenance plans, schedules, and procedures. Determine the frequency of inspections, preventive maintenance activities, and predictive maintenance techniques.
What to analyze in maintainability studies?
- Component Accessibility: Evaluate the accessibility of critical components for maintenance tasks, including inspection, removal, and replacement. Assess the ease of access and the need for specialized tools or equipment.
- Maintenance Procedures: Analyze the existing maintenance procedures and workflows for gas turbines. Identify opportunities to streamline processes, reduce maintenance time, and minimize human error.
- Spare Parts and Inventory: Evaluate the availability, adequacy, and suitability of spare parts for gas turbines. Develop an efficient inventory management system to ensure timely availability of critical components.
Which techniques can be used for maintainability studies and analysis?
- Failure Mode and Effects Analysis (FMEA): Conduct FMEA to identify potential failure modes, their effects, and the criticality of each failure mode. Prioritize maintenance efforts based on the identified risks.
- Reliability Centered Maintenance (RCM): Apply RCM methodology to determine maintenance requirements based on the criticality of equipment and the consequences of failures.
- Task Analysis: Perform task analysis to identify the sequence of maintenance activities, potential hazards, and opportunities for improvement in gas turbine maintenance procedures.
How to apply it?
Define the Scope: Clearly define the scope of the maintainability study, including the specific objectives, the targeted gas turbine systems or components, and the timeframe for analysis.
Gather Data: Collect relevant data on gas turbine performance, maintenance history, failure records, and operational conditions. This data can come from plant maintenance records, equipment manuals, industry standards, and interviews with maintenance personnel.
Identify Critical Components: Identify the critical components of the gas turbines that significantly impact reliability, maintainability, and safety. These may include turbine blades, combustion systems, bearings, seals, control systems, and auxiliary equipment. Focus the analysis on these components.
Conduct Failure Mode and Effects Analysis (FMEA): Apply FMEA to identify potential failure modes, their causes, effects, and associated risks. Assess the criticality of each failure mode by considering factors such as safety, environmental impact, and economic consequences.
Prioritize Maintenance Activities: Prioritize maintenance activities based on the FMEA results. Focus on addressing high-risk failure modes and critical components. Develop maintenance strategies that include preventive, predictive, and corrective maintenance tasks.
Analyze Maintenance Procedures: Evaluate the existing maintenance procedures and workflows for gas turbines. Identify potential inefficiencies, bottlenecks, and safety hazards. Determine if procedures need to be revised or optimized to improve the efficiency and safety of maintenance activities.
Assess Component Accessibility: Evaluate the accessibility of components for maintenance tasks. Assess the ease of component removal, replacement, and inspection. Identify any design features or accessibility limitations that hinder maintenance activities and propose design modifications if necessary.
Review Spare Parts and Inventory Management: Evaluate the availability, adequacy, and suitability of spare parts for critical components. Develop an effective inventory management system to ensure that necessary spare parts are readily available, reducing downtime.
Implement Diagnostic and Monitoring Systems: Consider implementing or enhancing diagnostic and monitoring systems for gas turbines. These systems can provide real-time data on performance, condition monitoring, and early fault detection, enabling proactive maintenance.
Training and Skill Development: Provide training programs for maintenance personnel to enhance their knowledge and skills in maintaining gas turbines. Focus on safety procedures, proper maintenance techniques, and equipment-specific training.
Monitor and Continuous Improvement: Establish a monitoring system to track the effectiveness of the implemented maintenance strategies. Regularly review maintenance data, failure records, and operational performance to identify areas for continuous improvement and optimization.
Collaboration and Documentation: Involve cross-functional teams, including engineers, maintenance personnel, operators, and manufacturers, in the maintainability studies. Collaborate on findings, recommendations, and implementation plans. Document the findings, analysis, and actions taken for future reference.
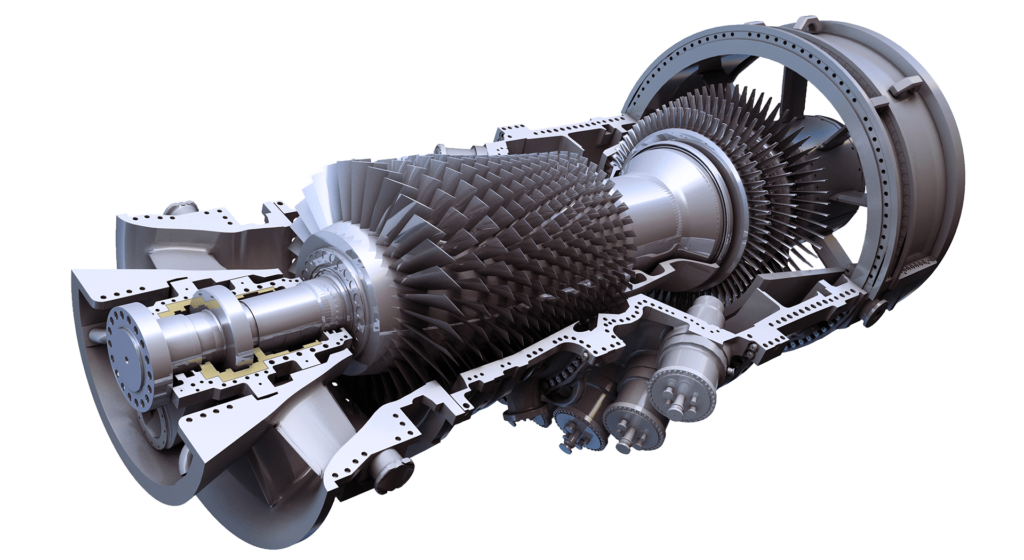
PROCEDURES, ACTIONS, STUDIES, MITIGATION, RECOMMENDATIONS TO APPLY MAINTAINABILITY IN ENGIEERING & DESIGN
To apply maintainability factors in the design and engineering of gas turbines and improve maintainability, reliability, availability, and safety in existing plants and new projects for the oil, gas, and petrochemical industries, the following procedures, actions, studies, mitigations, and recommendations can be considered:
Establish Design Guidelines: Develop design guidelines that incorporate maintainability considerations from the early stages of the gas turbine project. These guidelines should outline the requirements and expectations for maintainability, reliability, availability, and safety in the design and engineering process.
Conduct Maintainability Studies: Perform thorough maintainability studies during the design phase to identify potential maintainability issues and evaluate their impact on reliability, availability, and safety. These studies can involve analyzing component accessibility, ease of maintenance, repairability, and the use of standardized designs and interfaces.
Standardization and Modularity: Emphasize standardization and modular design principles in gas turbine engineering. Standardizing components, interfaces, and maintenance practices simplifies maintenance activities, reduces downtime, and improves interchangeability of parts. Modular designs allow for easier replacement of components or subsystems, minimizing downtime during repairs or upgrades.
Component Accessibility: Ensure easy access to critical components for maintenance tasks such as inspections, repairs, and replacements. Consider the placement and arrangement of components to facilitate safe and efficient access for maintenance personnel. Incorporate features such as removable panels, access hatches, or inspection ports.
Design for Ease of Maintenance: Design gas turbines with maintenance in mind. Consider maintenance tasks during the design process and aim to minimize the time, effort, and complexity of maintenance activities. Simplify disassembly and reassembly procedures, provide clear markings and labeling, and minimize the need for specialized tools or equipment.
Incorporate Condition Monitoring Systems: Integrate condition monitoring systems into the design of gas turbines. These systems allow real-time monitoring of key parameters such as vibration, temperature, and pressure. Proactive monitoring and early fault detection enable timely maintenance interventions, reducing the risk of unexpected failures.
Implement Built-in Diagnostics: Include built-in diagnostic capabilities in the gas turbine design. This enables the turbine to detect and diagnose faults or anomalies, providing maintenance personnel with valuable information for targeted maintenance actions.
Optimize Maintenance Procedures: Evaluate and optimize maintenance procedures for gas turbines, including disassembly, reassembly, and inspection tasks. Simplify procedures, reduce the number of steps, and minimize the use of specialized tools to enhance efficiency and reduce the potential for errors.
Spare Parts Management: Implement an effective spare parts management system for gas turbines. Maintain an up-to-date inventory, establish supplier relationships, and plan for obsolescence management to minimize downtime caused by parts unavailability. Ensure that critical spare parts are readily accessible when needed.
Training and Skill Development: Provide comprehensive training programs for maintenance personnel to enhance their knowledge and skills related to gas turbine maintenance. Training should cover safety procedures, proper maintenance techniques, troubleshooting, and the use of diagnostic tools.
Document Lessons Learned: Document and share lessons learned from previous gas turbine maintenance experiences and projects. Maintain a knowledge base that captures maintenance best practices, case studies, and successful strategies for improving maintainability, reliability, availability, and safety.
Continuous Improvement: Foster a culture of continuous improvement in gas turbine design and engineering. Regularly review maintenance data, failure records, and feedback from maintenance personnel to identify areas for improvement. Encourage collaboration among engineering, operations, and maintenance teams to drive ongoing enhancements.
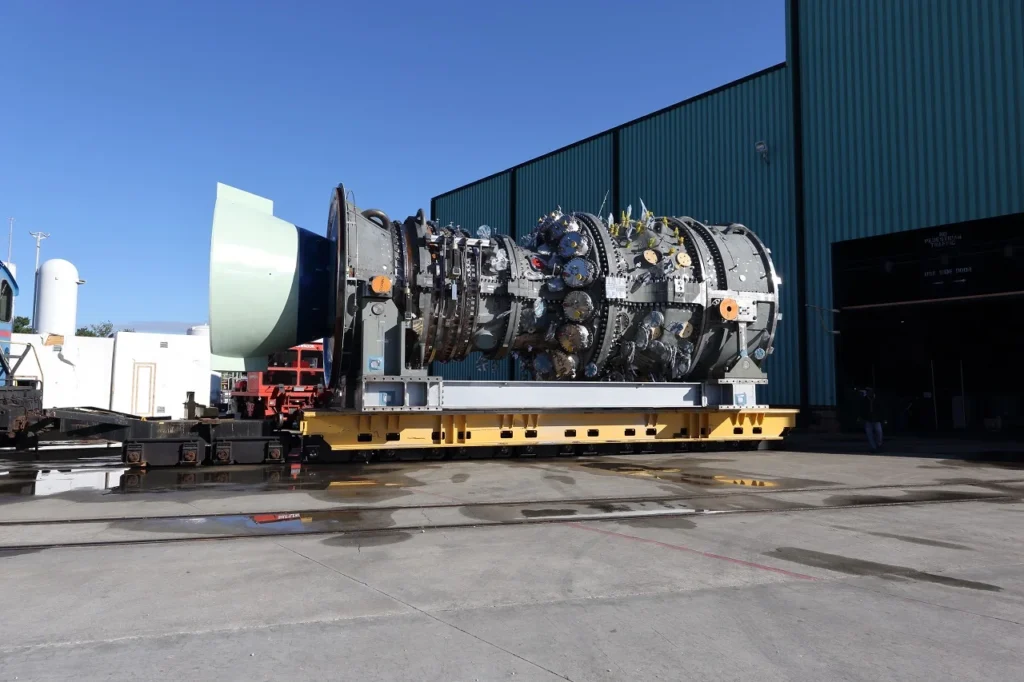