REPETITIVE FAILURES IN CRITICAL & MAIN PARTS - SPECIAL STEAM TURBINES
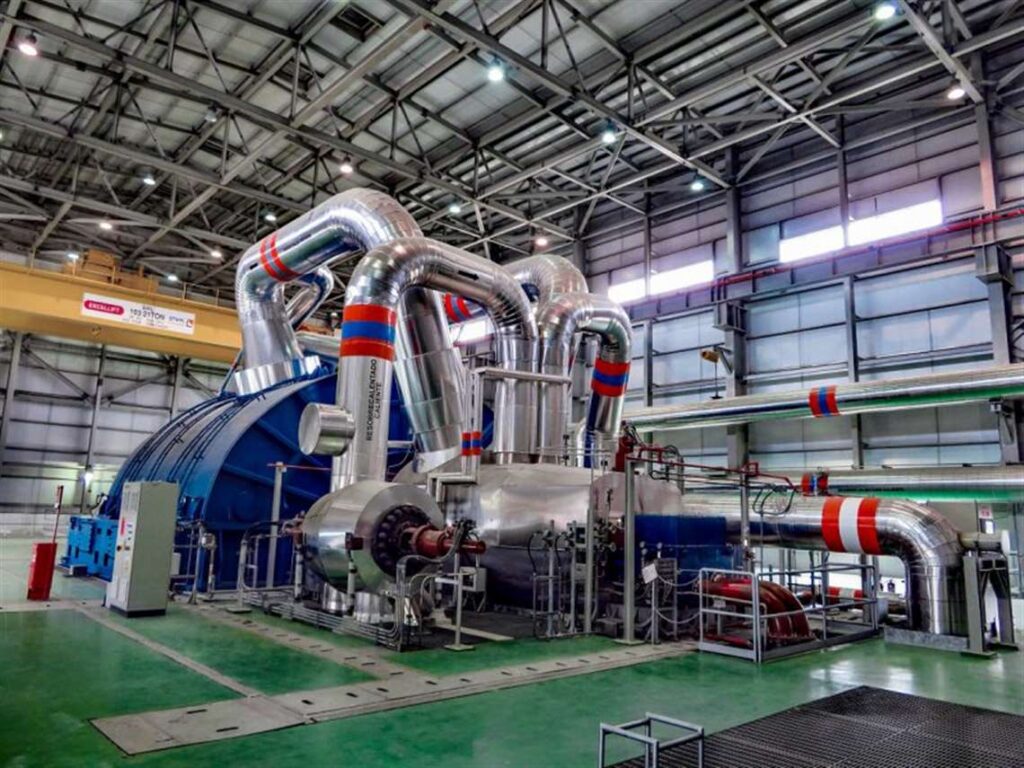
Failure analysis: When a failure or unexpected shutdown occurs in a special steam turbine, a thorough failure analysis should be conducted to determine the root cause of the issue. This analysis should include a review of operating conditions, maintenance history, and equipment design.
Inspection and maintenance: Regular inspections and maintenance of critical parts in special steam turbines, such as turbine blades, rotors, and casings, can help prevent unexpected failures. Maintenance activities should include monitoring of vibration and temperature, oil analysis, and visual inspections.
Operating procedures: Proper operating procedures for special steam turbines should be established and followed to minimize the risk of failures or unexpected shutdowns. These procedures should include guidelines for startup and shutdown, as well as operating parameters such as steam quality, temperature, and pressure.
Training: Operators and maintenance personnel should receive training on the proper operation and maintenance of special steam turbines. This training should cover topics such as equipment design, operating procedures, maintenance practices, and troubleshooting.
Design improvements: Special steam turbine manufacturers should continuously improve the design of their equipment to minimize the risk of failures or unexpected shutdowns. This can include the use of advanced materials, improved blade and rotor designs, and better seals.
Root cause analysis: In addition to failure analysis, a root cause analysis should be conducted to identify the underlying cause of the failure or unexpected shutdown. This analysis should consider factors such as equipment design, operating conditions, and maintenance practices.
Industry standards: Industry standards such as ASME PTC 6 provide guidelines for the design, operation, and maintenance of special steam turbines. Compliance with these standards can help minimize the risk of failures or unexpected shutdowns.
Risk management: A comprehensive risk management program should be established to identify, evaluate, and mitigate risks associated with special steam turbines. This program should include risk assessments, risk mitigation plans, and contingency plans for unexpected failures or shutdowns.
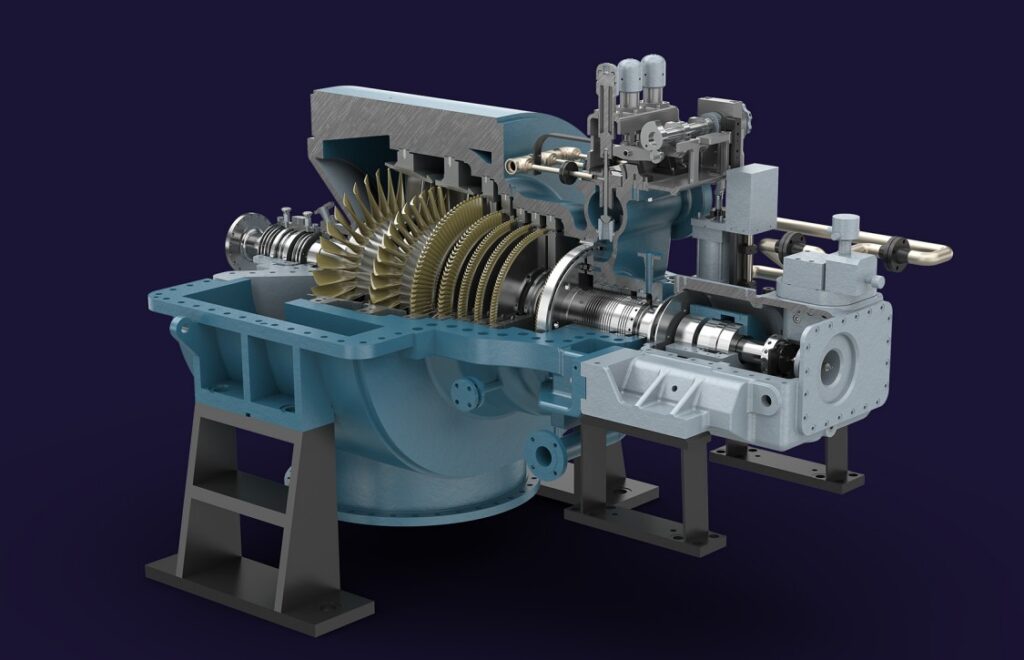
WHY, WHEN, WHERE, WHAT, WHICH, HOW, TO APPLY ENGINEERING & DESIGN ABOUT REPETITIVE FAILURES IN CRITICAL & MAIN PARTS
Why to apply repetitive & critical failure parts studies and analysis in the engineering and design of special steam turbines:
- To identify and understand the failure patterns and root causes of repetitive and critical failures in special steam turbines.
- To improve the maintainability, reliability, availability, and safety of special steam turbines by addressing the identified failure modes and their underlying causes.
- To minimize unplanned downtime, maintenance costs, and operational risks associated with repetitive and critical failures.
- To optimize the performance and efficiency of special steam turbines by eliminating or mitigating the impact of failure-prone components or systems.
When to apply repetitive & critical failure parts studies and analysis:
- During the design and engineering phase of special steam turbines, to proactively identify and address potential failure modes and critical components.
- As part of the regular maintenance and inspection activities, to assess the performance and condition of key components and systems and identify any repetitive or critical failure patterns.
- After major incidents or significant failures, to investigate the root causes and prevent similar failures from occurring in the future.
- During the design or upgrade of existing plants or the construction of new projects for power generation, oil, gas, and petrochemical industries.
Where to apply repetitive & critical failure parts studies and analysis:
- In existing plants operating special steam turbines, to identify and mitigate the risks associated with repetitive and critical failures.
- In new projects for power generation plants, oil, gas, and petrochemical industries, to ensure the reliability and safety of the special steam turbines from the early stages of design and engineering.
What to analyze in repetitive & critical failure parts studies and analysis:
- The historical data and maintenance records of special steam turbines to identify patterns of failures and recurring issues.
- The specific components, systems, and processes that are prone to repetitive or critical failures.
- The root causes and contributing factors behind the identified failure modes.
Which techniques to use in repetitive & critical failure parts studies and analysis:
- Root cause analysis (RCA) to investigate the underlying causes of failures and identify the primary failure modes.
- Failure modes and effects analysis (FMEA) to assess the potential failure modes, their effects, and the criticality of components.
- Fault tree analysis (FTA) to analyze the logical relationships between various failure events and identify the critical paths leading to failures.
How to apply repetitive & critical failure parts studies and analysis:
- Collect and analyze data on failures, maintenance activities, and equipment performance to identify repetitive and critical failure parts.
- Conduct detailed inspections, assessments, and testing of components and systems to identify potential failure modes and their causes.
- Use appropriate analytical tools and methodologies to determine the root causes and criticality of failure parts.
- Develop and implement mitigation strategies, including design improvements, maintenance programs, and monitoring systems, to address the identified failure modes and enhance the reliability and safety of special steam turbines.
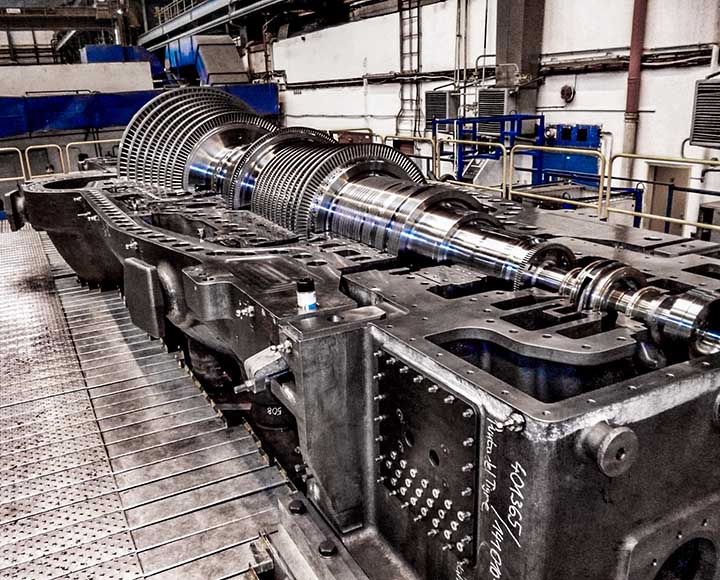
PROCEDURES, ACTIONS, STUDIES, MITIGATION, RECOMMENDATIONS TO APPLY THE ENGINEERING & DESIGN FOR REPETITIVE FAILURES IN CRITICAL & MAIN PARTS
To apply repetitive & main failure parts analysis in the design and engineering of special steam turbines, the following procedures, actions, studies, mitigations, and recommendations can be considered:
- Data Collection and Analysis:
- Collect and analyze historical data, maintenance records, and failure reports of special steam turbines to identify patterns of repetitive and main failures.
- Categorize and prioritize failure events based on their impact on maintainability, reliability, availability, and safety.
- Failure Modes and Effects Analysis (FMEA):
- Perform FMEA to systematically identify potential failure modes and their effects on special steam turbines.
- Evaluate the severity, probability of occurrence, and detectability of each failure mode to prioritize actions.
- Root Cause Analysis (RCA):
- Conduct RCA to determine the underlying causes of repetitive and main failure events.
- Use techniques such as the “5 Whys” or fishbone diagrams to identify the root causes contributing to the failure modes.
- Component and System Assessment:
- Evaluate the criticality and performance of individual components and systems within the special steam turbine.
- Identify components that are prone to repetitive failures or have a significant impact on overall reliability and safety.
- Design Improvements:
- Implement design modifications to address identified failure modes and improve the reliability and safety of the special steam turbine.
- Consider alternative materials, improved manufacturing processes, redundancy, or enhanced protection mechanisms to mitigate failure risks.
- Maintenance Strategies:
- Develop proactive maintenance strategies tailored to address the identified repetitive and main failure parts.
- Implement condition-based maintenance, predictive maintenance, or reliability-centered maintenance programs to detect and prevent failures.
- Monitoring and Control Systems:
- Install monitoring and control systems to continuously monitor the health and performance of critical components and systems.
- Implement real-time data analysis and remote monitoring to identify potential failure trends and take proactive measures.
- Training and Knowledge Sharing:
- Provide training and education programs to the maintenance and operations teams to improve their understanding of the special steam turbine’s failure modes and mitigation strategies.
- Encourage knowledge sharing and collaboration between different stakeholders to foster a proactive approach towards addressing repetitive and main failure parts.
- Continuous Improvement:
- Regularly review and update the analysis and mitigation measures based on new information, industry standards, and lessons learned.
- Conduct periodic audits and assessments to monitor the effectiveness of implemented actions and identify further areas for improvement.
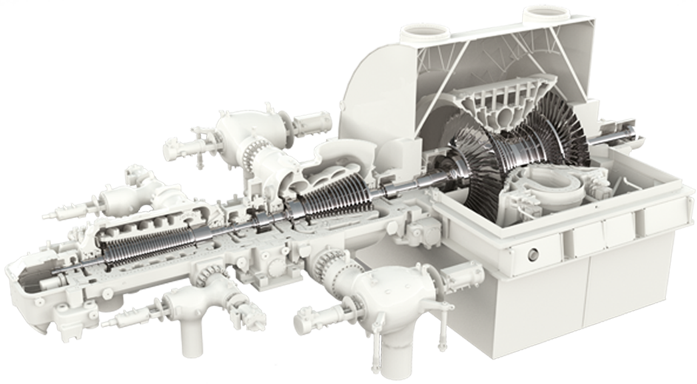