FREQUENT QUESTIONS & ANSWERS - CENTRIFUGAL COMPRESSORS
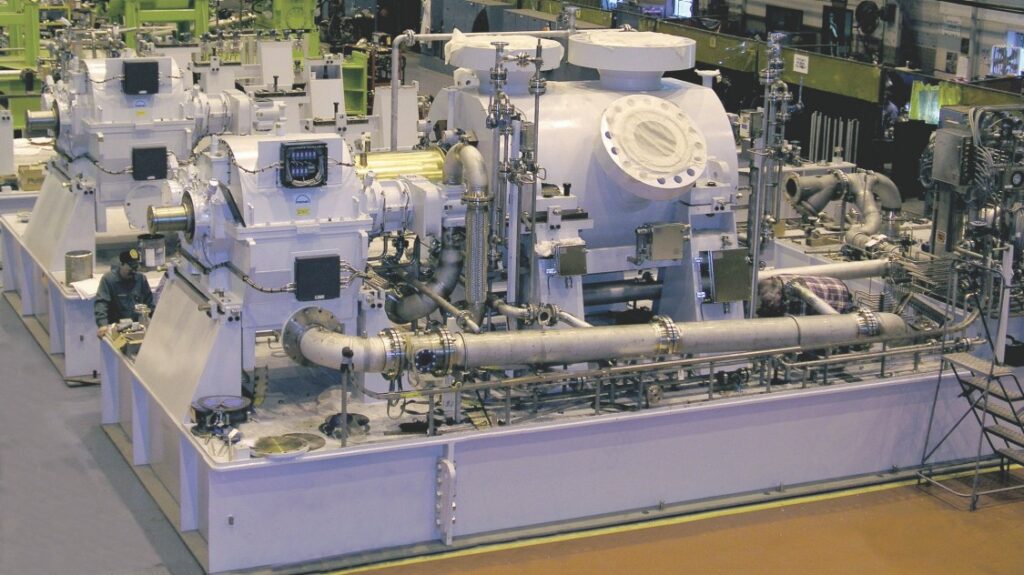
UPGRADE
UPDATE
Q: What is an upgrade or modernization for centrifugal compressors? A: An upgrade or modernization refers to the process of modifying or replacing certain components or systems of a centrifugal compressor to improve its performance, reliability, and efficiency.
Q: Why do centrifugal compressors require upgrades or modernizations? A: Centrifugal compressors may require upgrades or modernizations for various reasons, such as improving their efficiency, reliability, and safety, complying with new regulations or standards, reducing maintenance costs, and extending their lifespan.
Q: What components or systems can be upgraded or modernized in a centrifugal compressor? A: Components or systems that can be upgraded or modernized in a centrifugal compressor include impellers, diffusers, bearings, seals, control systems, and instrumentation.
Q: How can an upgrade or modernization improve the reliability of a centrifugal compressor? A: Upgrading or modernizing certain components or systems of a centrifugal compressor can improve its reliability by reducing the risk of mechanical failure, increasing the accuracy and responsiveness of control systems, and improving the overall performance of the compressor.
Q: Can an upgrade or modernization increase the efficiency of a centrifugal compressor? A: Yes, an upgrade or modernization can increase the efficiency of a centrifugal compressor by improving the design or performance of its components or systems, reducing losses due to leaks or inefficiencies, and optimizing its operation under various conditions.
Q: How long does an upgrade or modernization take to complete? A: The duration of an upgrade or modernization depends on various factors, such as the scope of work, the availability of replacement parts, the complexity of the compressor system, and the schedule of plant operations. Typically, upgrades or modernizations can take anywhere from a few weeks to several months to complete.
Q: How can I ensure the success of an upgrade or modernization project for my centrifugal compressor? A: To ensure the success of an upgrade or modernization project, it is important to engage experienced and qualified engineering and design professionals, follow best practices and standards, conduct thorough testing and commissioning, and establish clear communication and coordination among all stakeholders
What is a compressor update and why is it necessary? A compressor update involves replacing or upgrading some components of the centrifugal compressor to improve its performance, reliability, safety, and efficiency. It may also include changes in the compressor control system or process conditions. It is necessary to ensure that the compressor meets the changing needs of the process and operates efficiently and safely.
What components can be updated in a centrifugal compressor? Components that can be updated in a centrifugal compressor include impellers, diffusers, casings, bearings, seals, and control systems.
How do you determine which components need to be updated in a centrifugal compressor? The components that need to be updated in a centrifugal compressor depend on several factors, such as the age of the compressor, the process conditions, the operating history, the maintenance records, and the desired improvements in performance, reliability, safety, and efficiency. A thorough inspection, analysis, and testing of the compressor can help identify the critical components that need to be updated.
How much does a compressor update cost? The cost of a compressor update depends on several factors, such as the scope of the update, the extent of the required modifications, the cost of the new components, the labor cost, and the downtime cost. It is essential to perform a cost-benefit analysis and evaluate the long-term savings in energy, maintenance, and downtime costs that may result from the update.
How long does a compressor update take? The duration of a compressor update depends on several factors, such as the scope of the update, the complexity of the modifications, the availability of the required components, and the downtime allowed. It is essential to plan the update carefully and coordinate with the maintenance team and the process operators to minimize the downtime and ensure a safe and successful update.
Can a compressor update be performed on an existing compressor or only on a new compressor? A compressor update can be performed on both new and existing compressors. In fact, updating an existing compressor can be more cost-effective than purchasing a new compressor, especially if the existing compressor has a sound mechanical foundation and can be updated to meet the process needs. However, the feasibility and cost-effectiveness of the update depend on the specific circumstances of the compressor and the process.
How often should a compressor be updated? The frequency of compressor updates depends on several factors, such as the age of the compressor, the process conditions, the operating history, the maintenance records, and the desired improvements in performance, reliability, safety, and efficiency. In general, it is recommended to update the compressor components periodically and proactively to avoid critical failures and unscheduled shutdowns. The specific interval of the updates should be determined based on the results of the inspection, analysis, and testing of the compressor.
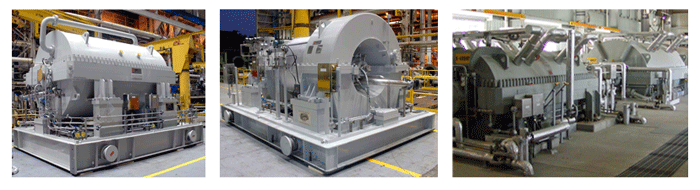
UPRATE
RERATE
What is an uprate for centrifugal compressors? A: An uprate for centrifugal compressors is a modification or enhancement made to increase the compressor’s capacity and efficiency beyond its original design parameters.
Why would I want to uprate my centrifugal compressor? A: Uprating your centrifugal compressor can help increase its output capacity, reduce energy consumption, and improve overall performance, leading to increased reliability, availability, and reduced maintenance costs.
What are the potential risks associated with uprating a centrifugal compressor? A: Uprating a centrifugal compressor can lead to increased operating temperatures and pressures, which may result in higher stresses on the compressor components, increased vibrations, and potential damage or failure. Therefore, it is crucial to conduct thorough analysis and testing before implementing any uprate modifications.
How can I determine if my centrifugal compressor is suitable for an uprate? A: The suitability of a centrifugal compressor for an uprate depends on several factors, such as its age, condition, and original design parameters. A comprehensive analysis of the compressor’s performance, including its mechanical and aerodynamic characteristics, must be conducted to determine its suitability for an uprate.
What types of modifications can be made to uprate a centrifugal compressor? A: The modifications required for uprating a centrifugal compressor can vary depending on the specific compressor design and application. Common modifications include increasing impeller diameter, modifying diffusers or volutes, adding or modifying inlet guide vanes, and optimizing the compressor’s control system.
How can I ensure the success of an uprate project for my centrifugal compressor? A: Successful uprate projects require a thorough understanding of the compressor’s operating conditions, performance characteristics, and design limitations. Conducting extensive analysis and testing, working closely with experienced compressor manufacturers and engineering firms, and following industry standards and guidelines can help ensure the success of an uprate project.
Q: What is a compressor rerate? A: A compressor rerate involves modifying an existing compressor to increase its flow rate, pressure, or power output. This is done by changing certain components, such as the impeller, diffuser, or inlet guide vanes.
Q: Why would I want to rerate my compressor? A: Rerating your compressor can be a cost-effective way to increase its output without having to replace the entire unit. It can also help improve the efficiency, reliability, and availability of your compressor.
Q: What are some factors to consider when deciding whether to rerate my compressor? A: The decision to rerate your compressor should be based on several factors, including the age and condition of the compressor, the cost of a new compressor versus the cost of rerating, and the expected performance gains from rerating.
Q: What are some common modifications made during a compressor rerate? A: The modifications made during a compressor rerate depend on the specific needs of the compressor, but can include changing the impeller or diffuser geometry, adding or removing inlet guide vanes, or increasing the size of the compressor casing.
Q: How can I ensure that my rerated compressor will be reliable and safe? A: It is important to work with a qualified compressor manufacturer or service provider to ensure that the rerate is performed correctly and that all safety and reliability considerations are taken into account. This may involve conducting a detailed engineering analysis or simulation to verify the performance of the modified compressor.
Q: What are some potential benefits of rerating my compressor? A: Some potential benefits of rerating your compressor include increased output and efficiency, improved reliability and availability, and reduced maintenance and operating costs.
Q: How can I determine if my compressor is a good candidate for rerating? A: A qualified compressor manufacturer or service provider can conduct a thorough evaluation of your compressor to determine if it is a good candidate for rerating. This may involve an inspection of the compressor components, a review of its operating history, and an analysis of its performance data.
REVAMP
Q1: What is REVAMP, and how does it benefit centrifugal compressors? A1: REVAMP refers to Retrofits, Upgrades, Enhancements, and Modernizations of Plants. It involves implementing modifications and upgrades to centrifugal compressors to improve their reliability, performance, and safety. REVAMP projects can enhance compressor efficiency, increase capacity, reduce energy consumption, and extend the operational life of the equipment.
Q2: What are some common modifications and upgrades made during a centrifugal compressor REVAMP project? A2: Common modifications and upgrades in centrifugal compressor REVAMP projects include aerodynamic redesigns, impeller and diffuser modifications, clearance optimization, mechanical component upgrades, control system improvements, condition monitoring implementation, and safety system enhancements.
Q3: How can REVAMP improve the reliability of centrifugal compressors? A3: REVAMP enhances the reliability of centrifugal compressors by addressing potential failure points and implementing upgrades. This includes upgrading worn-out or inefficient components, optimizing clearance between impellers and casings, implementing advanced condition monitoring systems, and improving safety systems to prevent critical failures and enhance overall reliability.
Q4: Can REVAMP projects improve the performance of existing centrifugal compressors? A4: Yes, REVAMP projects can significantly improve the performance of existing centrifugal compressors. Upgrades such as aerodynamic redesign, impeller and diffuser modifications, and control system enhancements can increase efficiency, capacity, and overall performance of the compressor.
Q5: Is REVAMP only applicable to existing centrifugal compressors, or can it be implemented in new projects as well? A5: REVAMP strategies can be applied to both existing centrifugal compressors and new projects. In new projects, REVAMP principles can be incorporated from the beginning, considering the latest technologies and design enhancements to ensure optimum reliability, performance, and safety.
Q6: How does REVAMP help in avoiding critical failures in centrifugal compressors? A6: REVAMP helps in avoiding critical failures by proactively addressing potential issues through upgrades and enhancements. By implementing condition monitoring systems, improving safety systems, and upgrading critical components, operators can detect early warning signs, prevent failures, and ensure the reliability of the compressor.
Q7: Are there any safety considerations in centrifugal compressor REVAMP projects? A7: Yes, safety considerations are an important aspect of REVAMP projects for centrifugal compressors. Upgrades may include the installation of improved safety systems, enhanced vibration monitoring, and explosion-proof designs to ensure safe and reliable operation.
Q8: Can REVAMP projects help in complying with environmental regulations? A8: Yes, REVAMP projects often include measures to ensure compliance with environmental regulations. Upgrades may involve improving energy efficiency, reducing emissions, and integrating environmental control technologies to minimize the environmental impact of compressor operations.
Q9: How long does a typical centrifugal compressor REVAMP project take? A9: The duration of a centrifugal compressor REVAMP project can vary depending on the scope and complexity of the upgrades. It can range from several weeks to months, considering factors such as engineering design, procurement, installation, and commissioning.
Q10: What are the potential cost savings associated with centrifugal compressor REVAMP projects? A10: Centrifugal compressor REVAMP projects can lead to cost savings through improved efficiency, reduced maintenance requirements, increased capacity, and optimized operation. These factors contribute to lower energy consumption, reduced downtime, and improved overall performance, resulting in significant cost savings over the operational life of the compressor.
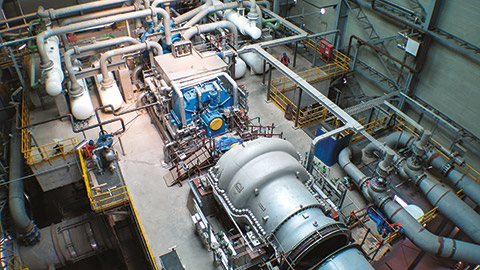