HOW TO REDUCE RISKS IN ENVIRONMENTAL FAILURES - CENTRIFUGAL COMPRESSORS
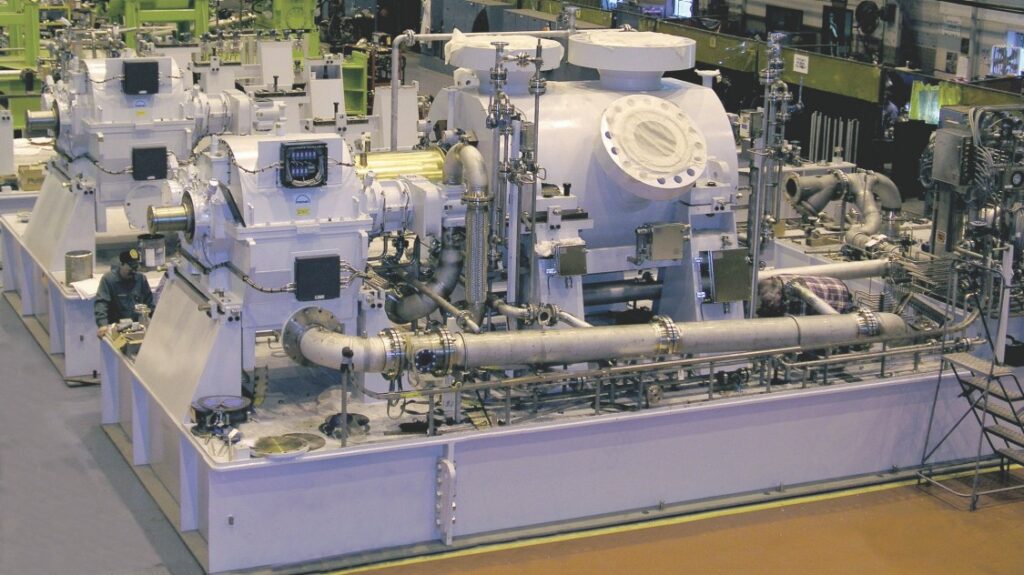
PROCEDURES, ACTIONS, STUDIES, RECOMMENDATIONS TO REDUCE RISKS IN ENVIRONMENTAL FAILURES
some reasons, procedures, actions, and recommendations to reduce environmental risks and avoid critical failures or unscheduled shutdowns in turbomachinery like centrifugal compressors in oil, gas, and petrochemical industries:
Reasons for reducing environmental risks:
- To comply with environmental regulations and standards
- To reduce the impact of operations on the environment
- To protect the health and safety of workers and the public
- To maintain a positive public image and reputation
- To avoid costly fines, penalties, and legal action
- To ensure the reliability and availability of equipment
Procedures and actions for reducing environmental risks:
- Conduct a thorough environmental impact assessment (EIA) before the start of a new project or before any modifications are made to an existing plant.
- Implement an effective environmental management system (EMS) to manage environmental risks and ensure compliance with regulations and standards.
- Use environmentally friendly technologies and materials whenever possible, such as low-emission fuels and high-efficiency compressors.
- Implement effective monitoring and control measures for emissions, spills, and other environmental hazards.
- Train personnel on environmental issues and ensure they are aware of their roles and responsibilities.
- Regularly inspect and maintain equipment to ensure it is operating efficiently and in compliance with environmental regulations.
- Develop contingency plans for responding to environmental incidents, such as spills or leaks.
Recommendations for reducing environmental risks:
- Consider using renewable energy sources, such as solar or wind power, to reduce reliance on fossil fuels and emissions.
- Encourage the use of energy-efficient practices, such as reducing unnecessary equipment running time and optimizing process parameters.
- Develop partnerships with suppliers and vendors who prioritize environmental sustainability.
- Participate in industry initiatives and programs to share best practices and learn about new technologies and approaches.
- Regularly review and update environmental management plans and procedures to reflect changing regulations and industry standards.
- Foster a culture of environmental responsibility among employees and stakeholders by promoting sustainable practices and recognizing achievements in this area.
In summary, reducing environmental risks requires a proactive approach that includes thorough planning, effective management, and ongoing monitoring and improvement. By taking these steps, the risks of critical failures or unscheduled shutdowns in turbomachinery like centrifugal compressors can be minimized, protecting the environment, ensuring regulatory compliance, and maintaining operational reliability and availability.
WHY, WHEN, WHICH, WHERE & HOW TO REDUCE CRITICAL RISKS IN ENVIRONMENTAL FAILURES
Reducing environmental impacts and failures in centrifugal compressors is crucial to maintain their reliability, availability, maintainability, and safety while avoiding issues in new projects and existing plants in the oil, gas, and petrochemical industries. Here are some considerations:
Why: The reduction of environmental impacts and failures is important to meet environmental regulations, improve sustainability practices, ensure compliance, protect the environment, and enhance the overall performance of centrifugal compressors.
When: Environmental impact and failure reduction efforts should be considered throughout the lifecycle of the centrifugal compressors:
- Design phase: Environmental considerations should be integrated into the compressor design, focusing on energy efficiency, emissions reduction, noise control, and material selection.
- Installation phase: Proper installation practices should be followed to prevent errors and ensure the correct alignment, connection, and integration of the compressor into the overall system.
- Operation phase: Ongoing monitoring, maintenance, and optimization measures should be implemented to minimize environmental impacts and detect potential failure risks.
- Decommissioning phase: Proper disposal or recycling of compressor components should be conducted to minimize environmental harm.
Which: The following areas should be addressed to reduce environmental impacts and failures in centrifugal compressors:
- Energy efficiency: Enhancing the compressor’s energy efficiency through design improvements, variable speed drives, optimized control systems, and regular maintenance can reduce energy consumption and associated environmental impacts.
- Emissions control: Implementing emission control technologies, such as gas treatment systems and catalytic converters, can minimize air pollutants emitted during compressor operation.
- Noise control: Employing noise reduction measures, such as acoustic enclosures, barriers, and vibration isolation, can mitigate noise pollution generated by compressors.
- Material selection: Choosing environmentally friendly and sustainable materials for compressor construction can minimize environmental impacts during the manufacturing, use, and disposal phases.
- Waste management: Proper waste management practices, including the handling and disposal of compressor-related waste, such as lubricants and filters, should be followed to minimize environmental contamination.
Where: These efforts should be applied in locations where centrifugal compressors are utilized, such as oil refineries, gas processing plants, petrochemical facilities, and other industrial sites.
How: To reduce environmental impacts and failures in centrifugal compressors, the following actions and strategies can be implemented:
- Conduct environmental impact assessments during the design phase to identify potential issues and incorporate mitigation measures.
- Regularly monitor and analyze compressor performance, emissions, and energy consumption to detect deviations, inefficiencies, and potential failure risks.
- Implement preventive maintenance programs to ensure proper lubrication, inspection, and calibration of compressor components.
- Train and educate operators and maintenance personnel on environmentally friendly practices, safety protocols, and proper handling of compressor systems.
- Establish and adhere to strict compliance with environmental regulations, industry standards, and best practices.
- Foster a culture of environmental responsibility and sustainability throughout the organization, promoting awareness and engagement.
By addressing these aspects and implementing proactive measures to reduce environmental impacts and failures in centrifugal compressors, organizations can improve reliability, availability, maintainability, and safety while minimizing environmental harm in new projects and existing plants within the oil, gas, and petrochemical industries.
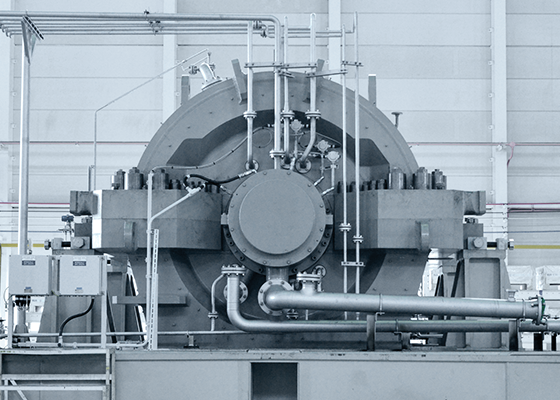
LIMITATIONS IN ENGINEERING & DESIGN ABOUT TO REDUCE RISKS IN ENVIRONMENTAL FAILURES
When it comes to reducing environmental failures in centrifugal compressors and improving reliability and safety in the oil, gas, and petrochemical industries, there are several limitations in engineering and design that need to be considered. Here are some key limitations:
Material Selection: The selection of materials for centrifugal compressors is crucial to ensure resistance to corrosive environments and maintain mechanical integrity. However, finding materials that are both durable and resistant to harsh operating conditions can be challenging.
Environmental Factors: Centrifugal compressors are exposed to various environmental factors such as high temperatures, humidity, and contaminants. These factors can lead to accelerated corrosion, erosion, and fouling, impacting the performance and reliability of the compressors.
Operational Conditions: The operating conditions of centrifugal compressors, such as flow rates, pressure differentials, and temperature ranges, can significantly affect their performance and reliability. Designing the compressors to operate within safe and efficient ranges while considering the specific process requirements can be complex.
Maintenance and Inspection: Proper maintenance and inspection play a crucial role in identifying potential failures and ensuring the longevity of centrifugal compressors. However, access limitations, safety concerns, and the need for specialized equipment can make inspection and maintenance challenging, particularly for large compressors in existing plants.
Cost Constraints: Implementing advanced engineering and design features to reduce environmental failures can often involve additional costs. Balancing the need for improved reliability and safety with budgetary limitations can be a constraint for both existing plants and new projects.
Retrofitting Existing Plants: Retrofitting existing plants with new centrifugal compressors or implementing design modifications can be logistically challenging. Space limitations, compatibility with existing infrastructure, and potential disruptions to ongoing operations must be carefully considered.
Regulatory Compliance: The oil, gas, and petrochemical industries are subject to strict regulatory requirements regarding environmental and safety standards. Ensuring compliance with these regulations while improving the reliability of centrifugal compressors can be a complex task.
To overcome these limitations, collaboration between engineers, designers, operators, and manufacturers is essential. Advanced materials research, innovative design techniques, improved maintenance strategies, and adherence to industry standards can collectively contribute to reducing environmental failures and enhancing reliability and safety in centrifugal compressors for both existing plants and new projects.
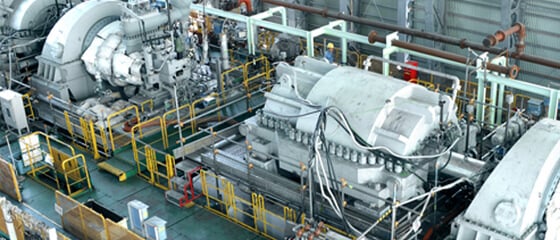