MAINTENANCE PHILOSOPHIES - CENTRIFUGAL COMPRESSORS
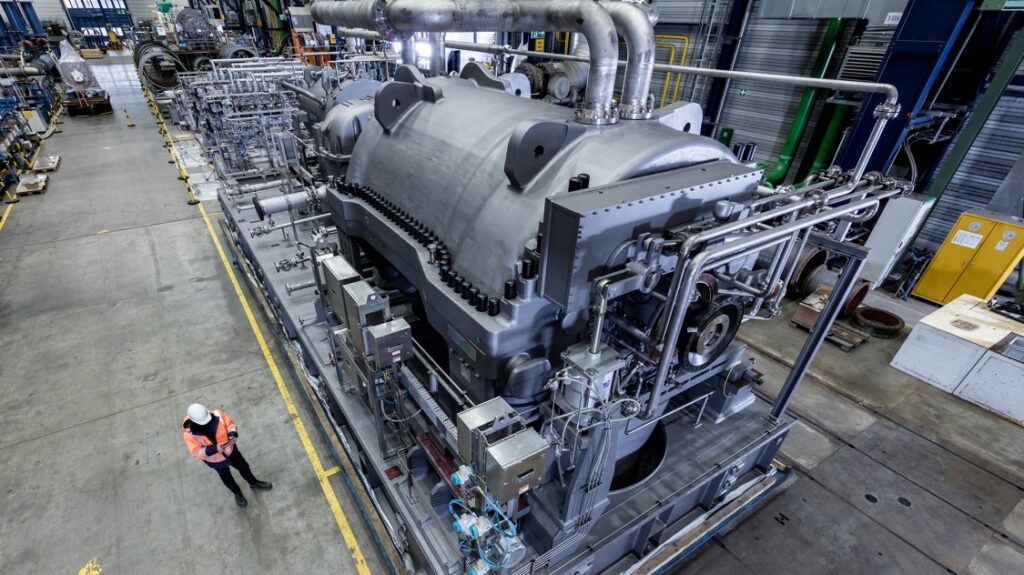
ADVANTAGES & DISADVANTAGES OF USING DIFFERENT MAINTENANCE PHILOSOPHIES
Advantages:
Preventive Maintenance:
- Advantages:
- Increases equipment reliability by addressing potential failure points proactively.
- Extends equipment lifespan by preventing premature failures.
- Reduces the likelihood of unplanned downtime and production losses.
- Considerations:
- Requires regular inspections and maintenance activities, which may lead to increased maintenance costs.
- It may not identify certain failure modes that are not detected through routine inspections alone.
- Advantages:
Predictive Maintenance:
- Advantages:
- Enables condition-based maintenance, leading to more targeted and efficient maintenance activities.
- Minimizes downtime by identifying potential failures before they occur.
- Optimizes maintenance resource allocation and reduces unnecessary maintenance actions.
- Considerations:
- Requires specialized monitoring techniques and equipment to gather and analyze data.
- Initial investment in monitoring systems and training may be required.
- Some failure modes may not exhibit clear precursors, making prediction challenging.
- Advantages:
Reliability-Centered Maintenance (RCM):
- Advantages:
- Maximizes reliability by identifying critical failure modes and implementing appropriate maintenance strategies.
- Optimizes maintenance intervals based on the criticality and consequences of failure.
- Reduces the likelihood of catastrophic failures and associated safety risks.
- Considerations:
- Requires a comprehensive understanding of equipment failure modes and associated risks.
- Implementation may involve complex analysis and decision-making processes.
- Regular review and updates are necessary to account for changes in equipment and operating conditions.
- Advantages:
Total Productive Maintenance (TPM):
- Advantages:
- Involves all stakeholders in maintenance activities, fostering a culture of ownership and accountability.
- Improves equipment effectiveness and productivity through autonomous and planned maintenance actions.
- Enhances communication and collaboration between maintenance and production teams.
- Considerations:
- Requires cultural and organizational changes to embrace TPM principles.
- Initial training and implementation efforts may be time-consuming and require resources.
- Alignment and coordination across different departments and shifts may be challenging.
- Advantages:
Risk-Based Maintenance (RBM):
- Advantages:
- Prioritizes maintenance activities based on risk assessments, optimizing resource allocation.
- Reduces the likelihood of critical failures by focusing on high-risk equipment and failure modes.
- Aligns maintenance efforts with safety and environmental objectives.
- Considerations:
- Requires comprehensive risk assessments and data analysis capabilities.
- May involve complex decision-making processes and require specialized expertise.
- Continuous monitoring and reassessment of risks are necessary to ensure effectiveness.
- Advantages:
It’s important to note that the advantages and considerations mentioned above are general in nature. The specific benefits and challenges of implementing maintenance philosophies can vary depending on factors such as the industry, equipment, operational conditions, and the organization’s existing maintenance practices.
By carefully considering the advantages and potential considerations of each maintenance philosophy, organizations can select and implement the most suitable approaches to enhance reliability, maintainability, availability, and safety in their centrifugal compressors, thereby avoiding environmental risks and critical failures or unscheduled shutdowns.
WHY, WHEN, WHERE, WHAT, WHICH, HOW TO APPLY MAINTENANCE PHILOSOPHIES IN CENTRIFUGAL COMPRESSORS
WHY Implement Different Maintenance Philosophies:
- Enhanced Reliability: Different maintenance philosophies help improve the reliability of centrifugal compressors by identifying potential failure points, implementing preventive measures, and optimizing maintenance strategies.
- Improved Maintainability: By adopting effective maintenance philosophies, the ease and efficiency of maintaining centrifugal compressors can be enhanced, reducing downtime and improving overall productivity.
- Increased Availability: Proper maintenance philosophies contribute to maximizing the availability of centrifugal compressors, ensuring they are operational when required and minimizing unscheduled shutdowns.
- Safety Enhancement: Maintenance philosophies prioritize safety considerations, ensuring that equipment is well-maintained and capable of operating within safe parameters, thus reducing the risk of accidents or environmental incidents.
WHEN to Implement Different Maintenance Philosophies:
- Existing Plants: Implementation of different maintenance philosophies can be initiated as part of maintenance improvement programs in existing industrial plants to address reliability issues, reduce downtime, and improve safety.
- New Projects: Incorporating maintenance philosophies into the design phase of new projects allows for the development of optimized maintenance strategies from the outset, ensuring long-term reliability and safety.
WHERE to Implement Different Maintenance Philosophies:
- Oil, Gas, and Petrochemical Industries: Maintenance philosophies are particularly relevant in the oil, gas, and petrochemical industries, where centrifugal compressors play a critical role in various processes such as gas compression, refining, and petrochemical production.
WHAT Different Maintenance Philosophies Provide:
- Preventive Maintenance: This philosophy focuses on scheduled maintenance activities, such as inspections, component replacements, and lubrication, aimed at preventing failures before they occur and maximizing equipment lifespan.
- Predictive Maintenance: Predictive maintenance utilizes monitoring techniques and condition-based assessments to identify potential failures or performance deviations, allowing for proactive maintenance actions.
- Reliability-Centered Maintenance (RCM): RCM involves analyzing the criticality and failure modes of equipment, determining appropriate maintenance tasks, and optimizing maintenance intervals to maximize reliability and safety.
- Total Productive Maintenance (TPM): TPM emphasizes involving all stakeholders in equipment maintenance, promoting a culture of ownership, and implementing autonomous and planned maintenance activities to enhance overall equipment effectiveness.
- Risk-Based Maintenance (RBM): RBM focuses on identifying and prioritizing maintenance tasks based on risk assessments, considering factors such as criticality, consequence of failure, and probability of occurrence.
WHICH Maintenance Philosophies to Choose:
- The selection of maintenance philosophies depends on factors such as equipment criticality, operational requirements, available resources, and specific industry regulations. A combination of different philosophies may be adopted to address different aspects of maintenance.
HOW to Implement Different Maintenance Philosophies:
- Data Collection and Analysis: Implement robust data collection systems to gather information on equipment performance, failure history, and operating conditions. Analyze this data to identify patterns and develop maintenance strategies.
- Condition Monitoring: Utilize advanced techniques such as vibration analysis, thermography, oil analysis, and performance monitoring to assess equipment health and identify early signs of degradation or potential failures.
- Maintenance Planning and Scheduling: Develop comprehensive maintenance plans and schedules based on the chosen maintenance philosophies, ensuring that tasks are prioritized and resources are allocated efficiently.
- Training and Skill Development: Provide appropriate training to maintenance personnel to ensure they have the necessary skills and knowledge to implement the chosen maintenance philosophies effectively.
- Continuous Improvement: Foster a culture of continuous improvement, encouraging feedback, monitoring performance metrics, and implementing lessons learned to refine and optimize maintenance strategies over time.
By applying these different maintenance philosophies internationally, the reliability, maintainability, availability, and safety of centrifugal compressors in existing industrial plants and new projects in the oil, gas, and petrochemical industries can be improved, helping to avoid environmental risks and critical failures or unscheduled shutdowns.
PROCEDURES, ACTIONS & RECOMMENDATIONS - MAINTENANCE PHILOSOPHIES
Here are some procedures, actions, and recommendations to be applied in centrifugal compressors for each maintenance philosophy to improve reliability, maintainability, availability, and safety in existing industrial plants for power generation, oil, gas, and petrochemical industries and avoid critical failures or unscheduled shutdowns:
- Reactive Maintenance:
- Procedures: This is the “run-to-failure” approach where maintenance is only performed after the equipment has already broken down.
- Actions: The compressor is only attended to once it has already failed. The repair team would then be called to repair or replace the damaged components.
- Recommendations: This approach should only be applied to low criticality components or equipment. It is not recommended for high criticality components or equipment.
- Preventive Maintenance:
- Procedures: This approach involves performing maintenance tasks at predetermined intervals, regardless of the actual condition of the equipment.
- Actions: Maintenance tasks are performed on a schedule that is set based on the compressor’s history, operating conditions, and manufacturer’s recommendations.
- Recommendations: This approach is recommended for low to medium criticality components or equipment. However, it can be costly if the maintenance schedule is too frequent or if the components are replaced too often.
- Condition Based Maintenance:
- Procedures: This approach involves monitoring the condition of the equipment and performing maintenance only when it is needed based on the equipment’s condition.
- Actions: The condition of the compressor is monitored through vibration analysis, oil analysis, temperature measurements, and other tools. Maintenance is then performed based on the results of the analysis.
- Recommendations: This approach is recommended for high criticality components or equipment. It reduces maintenance costs and minimizes downtime by addressing problems only when necessary.
- Risk Based Maintenance:
- Procedures: This approach involves identifying the equipment’s criticality and the probability of failure.
- Actions: The compressor is assessed based on its criticality and the probability of failure. Maintenance is then performed based on the level of risk identified.
- Recommendations: This approach is recommended for all equipment types. It prioritizes maintenance tasks based on the level of risk and ensures that high-risk equipment is attended to first.
- Proactive Maintenance:
- Procedures: This approach involves performing maintenance tasks before a problem occurs.
- Actions: The compressor is inspected regularly, and potential issues are identified before they lead to failure.
- Recommendations: This approach is recommended for all equipment types. It is the most effective way to minimize downtime and increase reliability.
- Reliability Centered Maintenance:
- Procedures: This approach involves analyzing the equipment’s reliability and determining which maintenance tasks will be most effective in improving reliability.
- Actions: The compressor’s reliability is analyzed based on its criticality, operating conditions, and maintenance history. Maintenance tasks are then determined based on the analysis.
- Recommendations: This approach is recommended for all equipment types. It ensures that maintenance tasks are performed only when necessary, which reduces maintenance costs and minimizes downtime.
- Total Productive Maintenance:
- Procedures: This approach involves ensuring that equipment is maintained in a way that maximizes its productivity.
- Actions: The compressor is monitored and maintained based on its productivity level. Maintenance tasks are performed to ensure that the compressor is running at maximum efficiency.
- Recommendations: This approach is recommended for all equipment types. It ensures that equipment is maintained in a way that maximizes its productivity, which increases efficiency and reduces downtime.
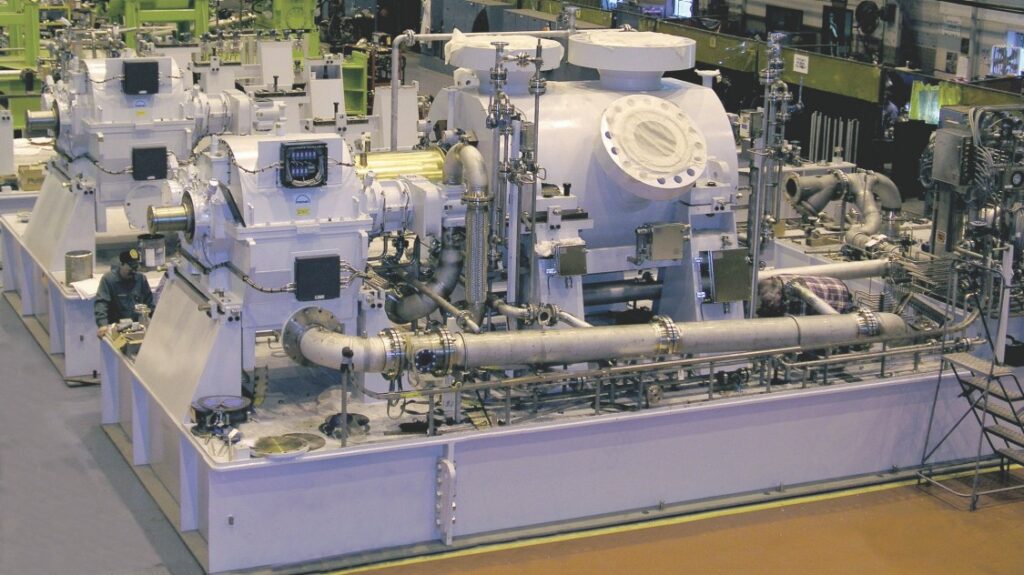
FREQUENT QUESTIONS & ANSWERS - CENTRIFUGAL COMPRESSORS
Here are some of the most frequent questions and answers asked about different maintenance philosophies related to centrifugal compressors in the oil, gas, and petrochemical industries:
- What is reactive maintenance, and when is it appropriate for centrifugal compressors?
Reactive maintenance involves waiting until a piece of equipment fails before performing maintenance or repairs. It is generally not recommended for centrifugal compressors as it can lead to unplanned downtime and more costly repairs. However, it may be appropriate for less critical or easily replaceable components.
- What is preventive maintenance, and when is it appropriate for centrifugal compressors?
Preventive maintenance involves performing maintenance on a schedule, typically based on manufacturer recommendations or industry best practices. It is appropriate for centrifugal compressors when there are known failure modes or wear mechanisms that can be mitigated through routine maintenance, such as changing filters, lubricating bearings, or checking alignment.
- What is condition-based maintenance, and when is it appropriate for centrifugal compressors?
Condition-based maintenance involves monitoring the condition of equipment through various techniques, such as vibration analysis or oil analysis, and performing maintenance or repairs when specific thresholds or indicators are reached. It is appropriate for centrifugal compressors when there are specific failure modes or wear mechanisms that can be detected through monitoring and mitigated through targeted maintenance.
- What is risk-based maintenance, and when is it appropriate for centrifugal compressors?
Risk-based maintenance involves assessing the risks associated with equipment failure and prioritizing maintenance activities accordingly. It is appropriate for centrifugal compressors when there are specific failure modes or wear mechanisms that pose a significant risk to safety, the environment, or production, and when the costs of failure are high.
- What is reliability-centered maintenance, and when is it appropriate for centrifugal compressors?
Reliability-centered maintenance involves analyzing the functions and performance requirements of equipment and developing a maintenance strategy that maximizes reliability and availability. It is appropriate for centrifugal compressors when there are complex or critical systems that require a comprehensive understanding of the equipment and its failure modes.
- What is total productive maintenance, and when is it appropriate for centrifugal compressors?
Total productive maintenance involves involving all personnel in the maintenance and improvement of equipment and processes, with a focus on continuous improvement and waste reduction. It is appropriate for centrifugal compressors when there are opportunities to optimize performance or reduce waste through collaboration and engagement of all stakeholders.
- What are some of the key benefits and drawbacks of different maintenance philosophies for centrifugal compressors?
The key benefits of different maintenance philosophies include increased reliability, reduced downtime and repair costs, and improved safety and environmental performance. However, each approach has its drawbacks, such as increased costs associated with more frequent or specialized maintenance activities, or the risk of missing important maintenance activities or failure modes. It is important to select a maintenance philosophy that aligns with the specific needs and goals of the organization and equipment.