MAINTENANCE PHILOSOPHIES - SPECIAL STEAM TURBINES
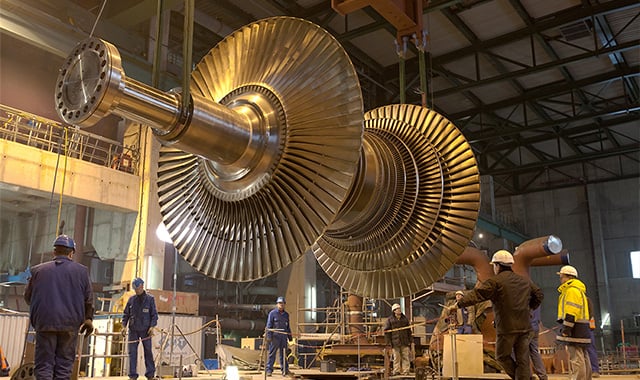
ADVANTAGES & DISADVANTAGES IN DIFFERENT MAINTENANCE PHILOSOPHIES APPLIED IN SPECIAL STEAM TURBINES
Advantages:
Preventive Maintenance:
- Advantages:
- Enhances reliability by addressing potential failure points and implementing routine inspections and maintenance activities.
- Extends the lifespan of special steam turbines by preventing premature failures.
- Reduces the likelihood of unscheduled downtime, thereby improving availability and productivity.
- Enhances safety by identifying and rectifying potential safety hazards during regular maintenance.
- Considerations:
- It may require downtime for scheduled maintenance activities, impacting production.
- Routine inspections and maintenance activities can result in increased maintenance costs.
- Advantages:
Predictive Maintenance:
- Advantages:
- Enables condition-based maintenance, allowing for targeted and efficient maintenance actions based on real-time equipment data.
- Minimizes downtime by identifying potential failures before they occur, improving availability and operational efficiency.
- Optimizes maintenance resource allocation and reduces unnecessary maintenance activities, thereby reducing costs.
- Enhances safety by detecting and addressing potential failure modes early on.
- Considerations:
- Requires specialized monitoring techniques and equipment to gather and analyze data.
- Initial investment in monitoring systems and training may be required.
- Some failure modes may not exhibit clear precursors, making prediction challenging.
- Advantages:
Reliability-Centered Maintenance (RCM):
- Advantages:
- Maximizes reliability by identifying critical failure modes specific to special steam turbines and implementing appropriate maintenance strategies.
- Optimizes maintenance intervals based on the criticality and consequences of failure, minimizing downtime and enhancing availability.
- Reduces the likelihood of catastrophic failures, enhancing safety and minimizing environmental risks.
- Considerations:
- Requires a comprehensive understanding of special steam turbine failure modes and associated risks.
- Implementation may involve complex analysis and decision-making processes.
- Regular review and updates are necessary to account for changes in equipment and operating conditions.
- Advantages:
Total Productive Maintenance (TPM):
- Advantages:
- Involves all stakeholders in maintenance activities, fostering a culture of ownership and accountability.
- Improves special steam turbine effectiveness and productivity through autonomous and planned maintenance actions.
- Enhances communication and collaboration between maintenance and operations teams, leading to improved overall performance.
- Considerations:
- Requires cultural and organizational changes to embrace TPM principles.
- Initial training and implementation efforts may be time-consuming and resource-intensive.
- Alignment and coordination across different departments and shifts may be challenging.
- Advantages:
Risk-Based Maintenance (RBM):
- Advantages:
- Prioritizes maintenance activities based on risk assessments, optimizing resource allocation and focusing on high-risk equipment and failure modes.
- Reduces the likelihood of critical failures, enhancing safety and minimizing environmental risks.
- Aligns maintenance efforts with safety and environmental objectives.
- Considerations:
- Requires comprehensive risk assessments and data analysis capabilities.
- May involve complex decision-making processes and require specialized expertise.
- Continuous monitoring and reassessment of risks are necessary to ensure effectiveness.
- Advantages:
It’s important to note that the advantages and considerations mentioned above are general in nature. The specific benefits and challenges of implementing maintenance philosophies can vary depending on factors such as the type of special steam turbine, operational conditions, and the organization’s existing maintenance practices.
By carefully considering the advantages and potential considerations of each maintenance philosophy, organizations can select and implement the most suitable approaches to enhance reliability, maintainability, availability, and safety in their special steam turbines, thereby avoiding environmental risks and critical failures or unscheduled shutdowns.
WHY, WHEN, WHERE, WHAT, WHICH, HOW TO APPLY DIFFERENT MAINTENANCE PHILOSOPHIES IN SPECIAL STEAM TURBINES
Why Apply Different Maintenance Philosophies?
- Special steam turbines are critical components in power generation, oil, gas, and petrochemical industries, and their reliable operation is essential for productivity, safety, and minimizing environmental risks.
- Different maintenance philosophies help improve the reliability, maintainability, availability, and safety of special steam turbines by addressing potential failure points, optimizing maintenance strategies, and reducing the likelihood of critical failures or unscheduled shutdowns.
When to Apply Different Maintenance Philosophies?
- Maintenance philosophies can be applied throughout the lifecycle of special steam turbines, including during the design, construction, commissioning, operation, and decommissioning phases.
- It is beneficial to incorporate maintenance considerations from the early stages of new projects to ensure the design and selection of appropriate maintenance strategies.
- For existing industrial plants, maintenance philosophies can be implemented during regular maintenance cycles or during major overhaul or retrofitting projects.
Where to Apply Different Maintenance Philosophies?
- Different maintenance philosophies can be applied to special steam turbines used in power generation plants, oil refineries, petrochemical facilities, and other industrial applications.
- They are relevant for both onshore and offshore installations, depending on the specific application and industry requirements.
What are the Different Maintenance Philosophies?
- The different maintenance philosophies include preventive maintenance, predictive maintenance, reliability-centered maintenance (RCM), total productive maintenance (TPM), and risk-based maintenance (RBM).
- Preventive maintenance involves scheduled inspections, maintenance activities, and component replacements to prevent failures.
- Predictive maintenance relies on condition monitoring techniques and data analysis to identify potential failures and schedule maintenance actions when necessary.
- RCM focuses on identifying critical failure modes, their causes, and appropriate maintenance strategies based on the consequences of failure.
- TPM involves involving all stakeholders in maintenance activities to improve overall equipment effectiveness, productivity, and safety.
- RBM prioritizes maintenance activities based on risk assessments to focus resources on high-risk equipment and failure modes.
Which Maintenance Philosophy to Choose?
- The choice of maintenance philosophy depends on factors such as the criticality of the special steam turbine, the consequences of failure, the available resources, and the organization’s goals and capabilities.
- It may be beneficial to employ a combination of maintenance philosophies tailored to the specific needs and requirements of the special steam turbine and industry.
How to Apply Different Maintenance Philosophies?
- Implementing maintenance philosophies involves several steps, including:
- Conducting a thorough assessment of the special steam turbine’s operational context, failure modes, and associated risks.
- Selecting and implementing appropriate maintenance strategies based on the chosen philosophy, such as developing preventive maintenance schedules, deploying condition monitoring systems, or conducting risk assessments.
- Training and educating maintenance personnel on the chosen philosophy and equipping them with the necessary skills and tools.
- Establishing a feedback loop to monitor the effectiveness of maintenance actions, review performance, and continuously improve maintenance strategies.
- Implementing maintenance philosophies involves several steps, including:
By applying different maintenance philosophies to special steam turbines, organizations can enhance their reliability, maintainability, availability, and safety in existing industrial plants and for new projects in power generation, oil, gas, and petrochemical industries. This helps avoid environmental risks, minimize critical failures, and prevent unscheduled shutdowns, ensuring the efficient and sustainable operation of special steam turbines.
PROCEDURES, ACTIONS & RECOMMENDATIONS - MAINTENANCE PHILOSOPHIES
The procedures, actions, and recommendations for each maintenance philosophy can also be applied to special steam turbines in order to improve their reliability, maintainability, availability, and safety. However, there are some additional considerations that are specific to steam turbines. Here are some specific procedures, actions, and recommendations for each maintenance philosophy:
- Reactive maintenance:
- Monitor the temperature and pressure of the steam to prevent overheating or overspeed conditions
- Inspect the rotor and blades for signs of damage or wear
- Document failures and their causes to identify any recurring failure modes
- Develop a plan to address recurring failure modes
- Consider a proactive maintenance approach to prevent failures from occurring in the first place
- Preventive maintenance:
- Develop a maintenance schedule based on manufacturer recommendations and/or experience
- Inspect the rotor and blades for signs of damage or wear
- Clean the steam path and perform visual inspections of the turbine casing and piping
- Replace components that are approaching their end-of-life or that show signs of wear and tear
- Consider using non-destructive testing techniques such as ultrasonic testing to identify potential issues before they become critical
- Predictive maintenance:
- Install sensors and data collection systems to monitor steam temperature, pressure, and vibration
- Use analytics to identify patterns and trends in the data
- Develop models to predict when maintenance is required
- Use machine learning and artificial intelligence to improve the accuracy of predictions
- Develop a comprehensive plan for collecting and analyzing data
- Use predictive maintenance in conjunction with other maintenance approaches for a comprehensive maintenance strategy
- Reliability-centered maintenance (RCM):
- Identify critical equipment and failure modes
- Determine the consequences of failure, such as steam leaks or overspeed conditions
- Develop maintenance tasks to prevent or mitigate failures
- Use a risk-based approach to prioritize maintenance tasks
- Continuously review and update the RCM plan based on changing conditions and new information
- Total productive maintenance (TPM):
- Develop a culture of ownership and accountability for equipment maintenance
- Train employees on maintenance procedures and techniques
- Implement an ongoing improvement program to identify opportunities for improvement
- Develop a comprehensive training program for employees, including safety procedures for working with steam turbines
- Foster a culture of continuous improvement
- Use TPM in conjunction with other maintenance approaches for a comprehensive maintenance strategy
In addition to these maintenance philosophies, there are also some specific procedures and recommendations that can be applied to steam turbines:
- Monitor the quality of the steam to prevent damage to the turbine blades and components
- Use water treatment to prevent corrosion and scale buildup
- Develop a comprehensive safety program for working with steam turbines, including lockout/tagout procedures and personal protective equipment (PPE)
- Inspect the turbine casing and piping for leaks or corrosion
- Perform regular testing of the turbine control system and safety systems to ensure they are functioning properly
By implementing a comprehensive maintenance strategy that incorporates multiple maintenance philosophies and specific procedures for steam turbines, the reliability, maintainability, availability, and safety of these turbines in industrial plants can be significantly improved, thereby reducing the risk of critical failures or unscheduled shutdowns.
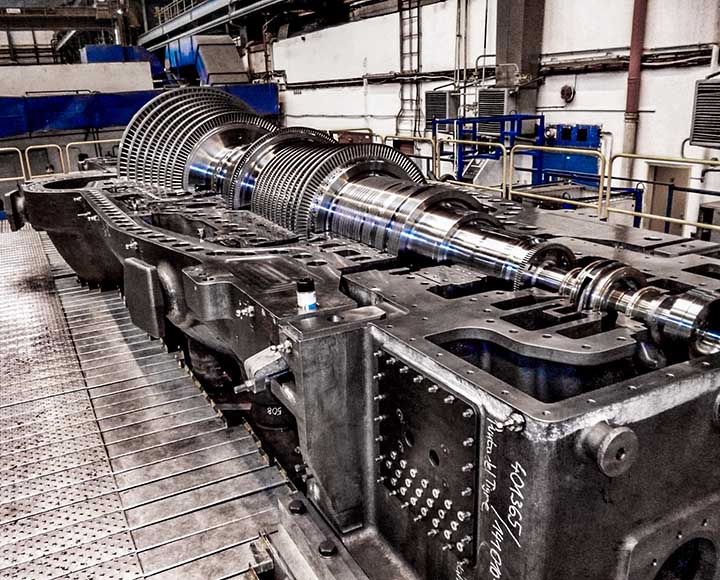
FREQUENT QUESTIONS & ANSWERS - MAINTENANCE PHILOSOPHIES - SPECIAL STEAM TURBINES
Here are some of the most frequent questions and answers asked about different maintenance philosophies related to special steam turbines in the oil, gas, and petrochemical industries:
- What is reactive maintenance, and when is it appropriate for special steam turbines?
Reactive maintenance involves waiting until a piece of equipment fails before performing maintenance or repairs. It is generally not recommended for special steam turbines as it can lead to unplanned downtime and more costly repairs. However, it may be appropriate for less critical or easily replaceable components.
- What is preventive maintenance, and when is it appropriate for special steam turbines?
Preventive maintenance involves performing maintenance on a schedule, typically based on manufacturer recommendations or industry best practices. It is appropriate for special steam turbines when there are known failure modes or wear mechanisms that can be mitigated through routine maintenance, such as changing filters, lubricating bearings, or checking alignment.
- What is condition-based maintenance, and when is it appropriate for special steam turbines?
Condition-based maintenance involves monitoring the condition of equipment through various techniques, such as vibration analysis or oil analysis, and performing maintenance or repairs when specific thresholds or indicators are reached. It is appropriate for special steam turbines when there are specific failure modes or wear mechanisms that can be detected through monitoring and mitigated through targeted maintenance.
- What is risk-based maintenance, and when is it appropriate for special steam turbines?
Risk-based maintenance involves assessing the risks associated with equipment failure and prioritizing maintenance activities accordingly. It is appropriate for special steam turbines when there are specific failure modes or wear mechanisms that pose a significant risk to safety, the environment, or production, and when the costs of failure are high.
- What is reliability-centered maintenance, and when is it appropriate for special steam turbines?
Reliability-centered maintenance involves analyzing the functions and performance requirements of equipment and developing a maintenance strategy that maximizes reliability and availability. It is appropriate for special steam turbines when there are complex or critical systems that require a comprehensive understanding of the equipment and its failure modes.
- What is total productive maintenance, and when is it appropriate for special steam turbines?
Total productive maintenance involves involving all personnel in the maintenance and improvement of equipment and processes, with a focus on continuous improvement and waste reduction. It is appropriate for special steam turbines when there are opportunities to optimize performance or reduce waste through collaboration and engagement of all stakeholders.
- What are some of the key benefits and drawbacks of different maintenance philosophies for special steam turbines?
The key benefits of different maintenance philosophies include increased reliability, reduced downtime and repair costs, and improved safety and environmental performance. However, each approach has its drawbacks, such as increased costs associated with more frequent or specialized maintenance activities, or the risk of missing important maintenance activities or failure modes. It is important to select a maintenance philosophy that aligns with the specific needs and goals of the organization and equipment.