OEM vs NON-OEM - SPARE PARTS - GAS TURBINES
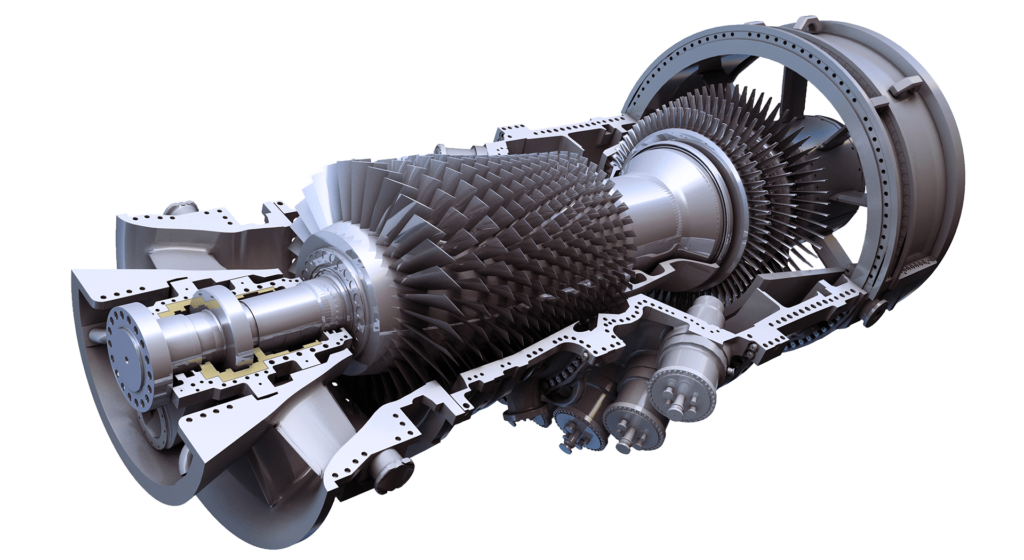
LIMITS IN ENGINEERING & DESIGN - OEM vs NON-OEM - SPARE PARTS
When choosing between OEM (Original Equipment Manufacturer) and non-OEM spare parts for gas turbines in the power generation, oil, gas, and petrochemical industries, it is important to understand the limits in engineering and design. These limits impact the reliability, maintainability, availability, and safety of the gas turbine systems. Let’s explore these limits in more detail:
- Reliability: OEM Parts: OEM spare parts are designed and manufactured by the original equipment manufacturer. They are engineered to meet the manufacturer’s specifications, ensuring compatibility and reliability. OEM parts undergo rigorous testing and quality control processes to ensure consistent performance and reliability. Using OEM parts can enhance the overall reliability of the gas turbine system.
Non-OEM Parts: Non-OEM spare parts may have variations in quality and performance. While some non-OEM parts may meet the required standards, others may not undergo the same level of testing or adhere to the manufacturer’s specifications. This variability in quality can introduce risks to the reliability of the gas turbine system. It is essential to thoroughly evaluate the non-OEM supplier’s reputation, quality control measures, and performance track record to ensure reliability.
- Maintainability: OEM Parts: OEM spare parts are specifically designed to fit seamlessly into the gas turbine system. They are engineered for compatibility and ease of installation, maintenance, and replacement. OEM parts often come with detailed documentation and technical support, facilitating efficient and effective maintenance practices. Using OEM parts simplifies the maintenance process and reduces downtime.
Non-OEM Parts: Non-OEM spare parts may not have the same level of compatibility with the gas turbine system. They might have variations in dimensions, tolerances, or material properties that can impact the ease of installation and maintenance. This can lead to challenges during maintenance activities and longer downtime. Thorough evaluation of the non-OEM parts’ compatibility and working closely with the supplier can help mitigate these limitations.
- Availability: OEM Parts: OEM spare parts benefit from the manufacturer’s well-established supply chains and service networks. Manufacturers prioritize the availability of spare parts for their equipment throughout its lifecycle. This ensures timely access to OEM parts, minimizing downtime and maximizing the availability of the gas turbine system.
Non-OEM Parts: The availability of non-OEM spare parts can vary depending on the supplier and the specific gas turbine model. Non-OEM suppliers may have limited stock or face difficulties in sourcing parts for older or less common turbine models. This can lead to delays in obtaining the required spare parts, resulting in longer downtime. It is crucial to establish agreements with reliable non-OEM suppliers to ensure the availability of spare parts when needed.
- Safety: OEM Parts: OEM spare parts undergo rigorous testing and certification processes to ensure compliance with safety standards and regulations. They are designed with specific safety features and considerations, minimizing the risk of critical failures and associated safety hazards. Manufacturers prioritize the safety of their equipment and provide comprehensive safety documentation and guidelines.
Non-OEM Parts: The safety features and compliance of non-OEM spare parts can vary. Without proper evaluation and verification, non-OEM parts may not meet the same safety standards as OEM parts. This can introduce potential risks to the safety of the gas turbine system. It is essential to evaluate the safety credentials of non-OEM parts and ensure they meet the required safety standards and regulations.
In summary, while OEM spare parts offer higher reliability, maintainability, availability, and safety due to their adherence to manufacturer’s specifications and rigorous testing, non-OEM spare parts can provide cost-saving opportunities. However, non-OEM parts come with inherent risks, such as variations in quality, compatibility, and safety. Thorough evaluation, proper verification, and collaboration with reputable non-OEM suppliers are essential to mitigate these risks and ensure the reliable and safe operation of gas turbine systems.
WHY, WHEN, WHERE, WHAT, WHICH, HOW TO APPLY ENGINEERING & DESIGN IN SPARE PARTS FOR OEM vs NON-OEM
When considering the use of OEM (Original Equipment Manufacturer) vs. non-OEM spare parts for gas turbines in the power generation, oil, gas, and petrochemical industries, it is important to thoroughly assess and apply engineering and design principles. This approach ensures the desired improvements in reliability, maintainability, availability, and safety. Let’s explore the key aspects of applying engineering and design in the context of OEM vs. non-OEM spare parts for gas turbines:
- WHY Choose OEM or Non-OEM Parts: The decision to choose OEM or non-OEM spare parts should be based on several factors:
- Reliability: OEM parts are designed and manufactured to meet specific performance standards and specifications. They have undergone rigorous testing and quality control processes, which enhances their reliability. Non-OEM parts, on the other hand, may vary in quality and performance, so careful evaluation is required.
- Maintainability: OEM parts are designed for compatibility and ease of installation, maintenance, and replacement. They are engineered to fit seamlessly into the gas turbine system, simplifying maintenance activities. Non-OEM parts may not have the same level of compatibility, so their maintainability should be assessed.
- Availability: OEM parts benefit from established supply chains and service networks, ensuring timely access to spare parts. Non-OEM parts may have varying availability, particularly for older or less common turbine models, so supplier reliability and stock availability must be considered.
- Safety: OEM parts undergo stringent testing and certification processes to ensure compliance with safety standards. They are designed with specific safety features and considerations. Non-OEM parts may not have the same level of safety assurance, so thorough evaluation and verification are necessary.
- WHEN to Choose OEM or Non-OEM Parts: The decision to choose OEM or non-OEM spare parts should be made at various stages:
- New Projects: In new gas turbine projects, it is advisable to consider OEM parts due to their established compatibility, reliability, and safety assurances. OEM parts also provide comprehensive documentation and technical support, facilitating the design and installation processes.
- Existing Plants: For existing gas turbine plants, the choice may depend on factors such as the age of the equipment, availability of OEM parts, maintenance requirements, and cost considerations. A thorough assessment of the benefits and risks associated with each option is crucial.
WHERE to Apply OEM or Non-OEM Parts: The application of OEM or non-OEM parts can be determined based on the specific components within the gas turbine system. Critical components that directly affect the performance, reliability, and safety of the turbine, such as blades, rotors, and bearings, may require the use of OEM parts. Less critical components or those with lower safety implications may be considered for non-OEM parts, provided they meet the required standards.
WHAT and WHICH Parts to Choose: For critical components, it is recommended to prioritize OEM parts due to their reliability and safety assurances. These components are designed to precise specifications and often undergo specialized manufacturing processes. Non-critical or auxiliary parts may be considered for non-OEM alternatives, provided they meet the required standards and compatibility requirements.
HOW to Apply OEM or Non-OEM Parts:
Identify the Requirements: Clearly define the specific requirements for the spare parts, considering factors such as compatibility, performance, reliability, safety, and regulatory compliance. This involves understanding the gas turbine system, its critical components, and the operational conditions.
Conduct a Risk Assessment: Evaluate the risks associated with using non-OEM parts, considering factors like component failure, warranty coverage, impact on performance and safety, and compliance with industry standards. This assessment helps in understanding the potential implications and making an informed decision.
Engage with OEM Suppliers: For critical components, engage with OEM suppliers who have the expertise, knowledge, and experience in designing and manufacturing the required spare parts. Collaborate closely with them to ensure the parts meet the necessary specifications and performance standards.
Evaluate Non-OEM Suppliers: Conduct thorough evaluations of non-OEM suppliers, considering factors such as reputation, quality control processes, track record, and customer feedback. Verify their capabilities to design, manufacture, and deliver parts that meet the required standards.
Perform Testing and Validation: Test and validate both OEM and non-OEM spare parts to ensure they meet the specified requirements. This involves performance testing, durability testing, compatibility testing, and compliance with relevant industry standards. Engage in close collaboration with suppliers to address any identified issues and ensure the parts meet the desired performance levels.
Document and Traceability: Ensure proper documentation and traceability of all spare parts, whether OEM or non-OEM. This includes maintaining records of specifications, certifications, testing results, and any modifications made. Proper documentation facilitates future maintenance, replacements, and compliance with regulations.
Consider Long-Term Support: Evaluate the long-term support and availability of spare parts from both OEM and non-OEM suppliers. Assess factors such as lead time, availability, pricing, and warranty coverage. Consider the supplier’s service network, technical support, and their ability to provide timely assistance when required.
Implement a Maintenance Strategy: Develop a comprehensive maintenance strategy that accounts for the specific requirements of the gas turbine system. This strategy should include routine inspections, preventive maintenance, and proactive replacement of critical components based on their expected lifespan. Consider OEM recommendations for maintenance practices and intervals.
Monitor Performance and Feedback: Continuously monitor the performance of both OEM and non-OEM spare parts, tracking metrics such as reliability, maintenance costs, downtime, and safety incidents. Collect feedback from operational personnel and maintenance teams to identify any issues or opportunities for improvement.
Continuous Improvement: Regularly assess and update the spare parts strategy based on performance feedback, technological advancements, industry best practices, and changes in operational requirements. Emphasize continuous improvement to optimize reliability, maintainability, availability, and safety of the gas turbine system.

PROCEDURES, ACTIONS, STUDIES, MITIGATION, RECOMMENDATIONS ABOUT OEM vs NON-OEM IN SPARE PARTS
To effectively apply OEM and non-OEM spare parts in gas turbines and improve reliability, maintainability, availability, safety, and mitigate critical failures and environmental risks in power generation, oil, gas, and petrochemical industries, the following procedures, actions, studies, mitigation measures, and recommendations can be implemented:
Procedures: a. Establish a standardized procurement process: Define a clear procedure for evaluating and procuring spare parts, including OEM and non-OEM options. This ensures consistency and adherence to quality and safety standards. b. Develop a comprehensive spare parts management plan: Create a plan that outlines inventory management, maintenance schedules, and replacement strategies for different parts, considering their criticality and expected lifecycles. c. Implement a rigorous quality control process: Establish procedures to inspect, test, and validate both OEM and non-OEM parts to ensure they meet required specifications and performance standards. d. Document and track spare parts information: Maintain a comprehensive database or system to track spare parts information, including specifications, certifications, maintenance records, and performance history.
Actions: a. Perform a thorough analysis of critical components: Identify the most critical components in the gas turbine system and prioritize the use of OEM parts for these components. Non-critical parts with lower risks can be considered for non-OEM alternatives, subject to careful evaluation. b. Conduct a comprehensive supplier evaluation: Evaluate both OEM and non-OEM suppliers based on their reputation, track record, quality control processes, and ability to meet delivery timelines. c. Engage in collaborative partnerships: Establish strong partnerships with OEM suppliers to ensure access to genuine spare parts and technical support. Collaborate with non-OEM suppliers to develop a clear understanding of their capabilities and ensure they can meet the required standards. d. Implement preventive maintenance strategies: Develop and implement a preventive maintenance program that includes regular inspections, testing, and replacement of critical parts based on recommended intervals from OEMs or industry best practices. e. Train and educate maintenance personnel: Provide training and education programs for maintenance personnel to enhance their knowledge and skills in handling OEM and non-OEM spare parts.
Studies: a. Failure analysis and root cause investigation: Conduct studies and analysis to identify common failure modes and root causes associated with both OEM and non-OEM spare parts. This helps in understanding the limitations and potential risks of using non-OEM parts. b. Comparative studies: Perform comparative studies to assess the performance, reliability, and safety aspects of OEM and non-OEM spare parts. Evaluate factors such as failure rates, maintenance costs, and downtime to make informed decisions.
Mitigation: a. Develop a risk management plan: Identify potential risks associated with using non-OEM parts and develop a risk management plan to mitigate those risks. This may include implementing additional inspections, quality control measures, or establishing contingency plans. b. Establish warranty and support agreements: Ensure that non-OEM suppliers provide warranty coverage and support services comparable to OEMs. This ensures that adequate support is available in the event of component failure or operational issues.
Recommendations
Prioritize OEM Parts for Critical Components:
- Critical components, such as turbine blades and bearings, should be sourced from OEMs to ensure reliability, performance, and compliance with industry standards.
- OEM parts typically undergo rigorous testing and meet strict quality control standards, reducing the risk of failures and ensuring proper fit and function within the turbine system.
Evaluate Non-Critical Components for Non-OEM Alternatives:
- Non-critical components, which have lower risks and less impact on overall system performance, can be considered for non-OEM alternatives.
- Conduct a thorough evaluation of non-OEM suppliers, considering their reputation, track record, quality control processes, and ability to meet performance requirements.
Perform Comparative Analysis:
- Conduct comparative studies and analysis to assess the performance, reliability, and safety aspects of both OEM and non-OEM spare parts.
- Consider factors such as failure rates, maintenance costs, availability, lead times, and compatibility with the existing system.
- Use the results of these analyses to make informed decisions regarding the use of OEM or non-OEM parts.
Engage in Collaborative Partnerships:
- Establish strong partnerships with OEM suppliers to ensure access to genuine spare parts and technical support.
- Collaborate with non-OEM suppliers to develop a clear understanding of their capabilities and ensure they can meet the required quality standards.
- Maintain open lines of communication with suppliers to address any concerns, obtain technical advice, and resolve issues promptly.
Maintain Comprehensive Spare Parts Inventory:
- Develop and implement a comprehensive spare parts inventory management system.
- Maintain an up-to-date database or system that includes information on OEM and non-OEM parts, including specifications, certifications, maintenance records, and performance history.
- Regularly review and update the inventory based on equipment usage, failure analysis, and recommendations from OEMs or industry experts.
Implement Preventive Maintenance Strategies:
- Develop and implement a preventive maintenance program that includes regular inspections, testing, and replacement of critical parts based on recommended intervals from OEMs or industry best practices.
- Establish clear procedures and guidelines for maintenance personnel regarding the inspection, installation, and maintenance of both OEM and non-OEM spare parts.
- Ensure that maintenance activities are carried out by trained and qualified personnel to maintain the integrity and performance of the gas turbine system.
Monitor Performance and Conduct Audits:
- Continuously monitor the performance of both OEM and non-OEM spare parts, including their failure rates, performance degradation, and maintenance costs.
- Conduct periodic audits to assess the quality and reliability of non-OEM parts, ensuring they meet the required specifications and performance standards.
- Address any performance issues promptly and take corrective actions to mitigate risks and improve overall system reliability.
Stay Informed and Updated:
- Stay abreast of industry developments, advancements, and recommendations regarding the use of OEM and non-OEM spare parts in gas turbines.
- Attend industry conferences, seminars, and training programs to gain insights into best practices and emerging technologies.
- Regularly communicate with OEMs, suppliers, and industry experts to understand the latest advancements and recommendations related to spare parts.
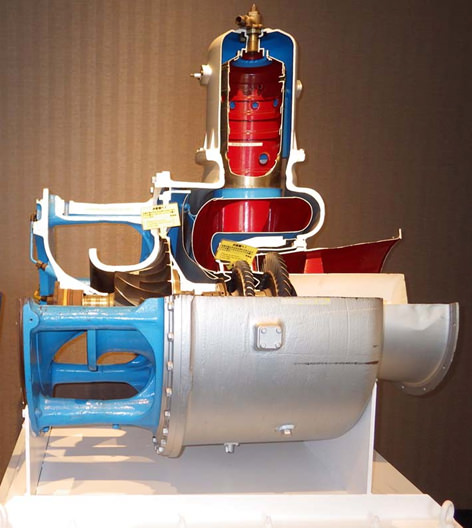