PERFORMANCE TEST (AT SHOP vs AT SITE) - SPECIAL STEAM TURBINES
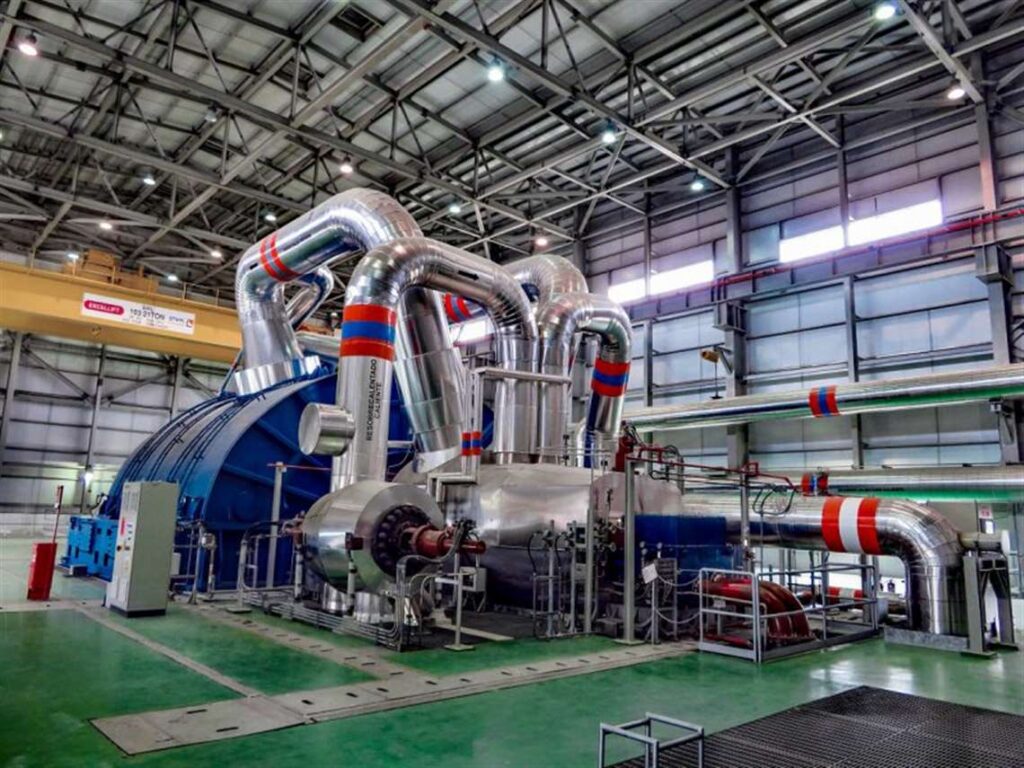
ADVANTAGES IN PERFORMANCE TEST (AT SHOP)
ADVANTAGES IN PERFORMANCE TEST (AT SITE)
The advantages of performing a performance test at shop for special steam turbines are:
Quality control: A performance test at shop ensures that the manufacturer produces a turbine that meets the design requirements and specifications. This helps to ensure that the quality of the turbine is maintained and avoids the potential for failure due to manufacturing defects.
Time and cost savings: Conducting a performance test at shop is more efficient and cost-effective than testing at the site. The shop test allows for greater control over the testing environment and can be completed faster than on-site testing.
Early detection of problems: Testing at the shop allows for the early detection of any issues with the turbine before it is shipped to the customer. This enables the manufacturer to address any problems before the turbine is installed, reducing the risk of unplanned downtime or catastrophic failure.
Improved reliability and safety: Conducting a performance test at shop ensures that the turbine is operating at peak performance and is less likely to experience issues related to performance or safety during operation.
Documentation: The performance test results provide valuable documentation for the turbine, which can be used for future reference, maintenance, and troubleshooting.
In summary, performing a performance test at shop for special steam turbines can improve the reliability, safety, and efficiency of the turbine, while also providing cost and time savings.
The advantages of performing a performance test at site for special steam turbines include:
Accurate assessment of performance: Site conditions can have a significant impact on the performance of the steam turbine, including the ambient temperature, humidity, and altitude. By conducting a performance test at the site, the actual operating conditions can be accurately measured and used to evaluate the performance of the steam turbine.
Detection of issues: Site performance tests can help to identify issues that may not have been detected during factory testing or commissioning, such as issues with the steam quality or steam flow rates. Identifying and addressing these issues can help to improve the reliability and safety of the steam turbine.
Optimization of performance: By conducting a performance test at site, the steam turbine can be optimized for the specific operating conditions and requirements of the plant. This can help to improve the efficiency of the turbine, reduce maintenance costs, and extend the life of the equipment.
Compliance with standards and regulations: Many industries have standards and regulations that require performance testing of steam turbines at site. By complying with these standards and regulations, companies can ensure that their equipment is safe and reliable, and avoid potential legal and financial consequences.
Verification of contractual guarantees: Performance testing at site can help to verify that the steam turbine is meeting the contractual guarantees for performance and efficiency, providing assurance to the customer and reducing the risk of disputes or legal action.
DISADVANTAGES IN PERFORMANCE TEST (AT SHOP)
DISADVANTAGES IN PERFORMANCE TEST (AT SITE)
There are several disadvantages to performing a performance test on special steam turbines at a shop. Some of them are:
Cost: Setting up a shop for conducting performance tests can be quite expensive and may require additional equipment and manpower.
Time: It can take a significant amount of time to disassemble and transport a steam turbine to a shop for testing. This can cause downtime for the power plant or industrial process.
Limited testing scope: Testing at a shop may not allow for a complete understanding of the turbine’s performance under site-specific conditions. The test conditions at the shop may not be representative of the actual conditions at the power plant or industrial process.
Transport risks: The transportation of a large and heavy turbine to and from the shop can be risky and may result in damage to the equipment.
Difficulty in replicating site conditions: It may be difficult to replicate the actual site conditions in a shop setting, which could lead to inaccuracies in the performance test results.
Some disadvantages of performing a performance test on special steam turbines at site could be:
Downtime: Performing a performance test at site requires shutting down the turbine, which means that the production process will stop during the test, leading to loss of revenue.
Safety concerns: Conducting a performance test at site can pose safety risks to personnel working on or around the turbine, as well as the surrounding area.
Accessibility issues: It may be difficult to access and inspect certain parts of the turbine when it is installed at a site, leading to limited testing capabilities.
Weather conditions: The performance test may be affected by weather conditions, such as wind, humidity, and temperature, which could impact the accuracy of the results.
Equipment availability: In some cases, specialized equipment may be required to perform the performance test, which may not be available at the site, leading to additional costs and delays.
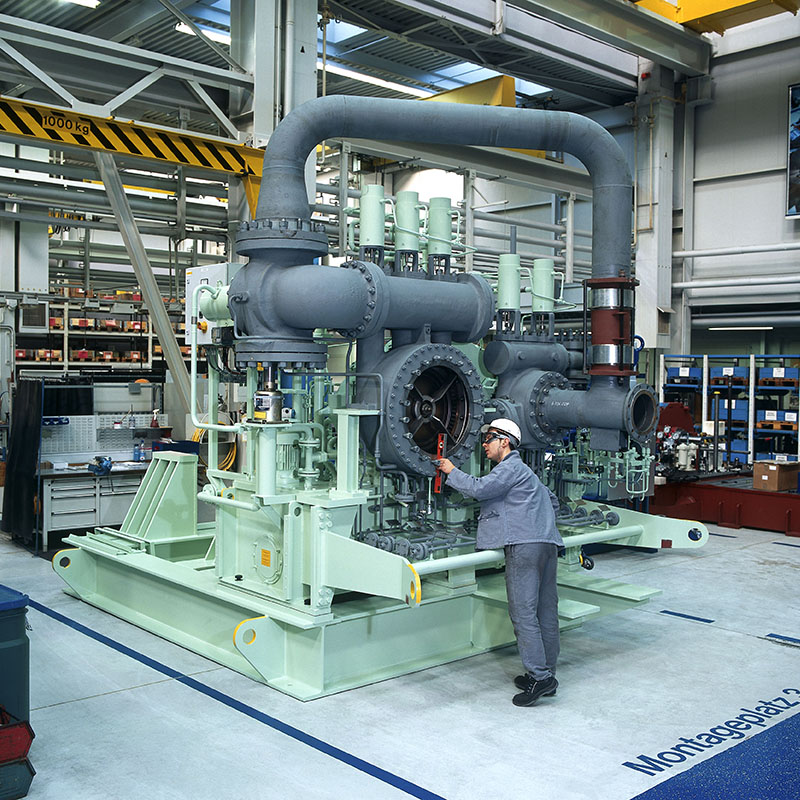
WHY, WHEN, WHERE, WHAT, WHICH, HOW TO APPLY THE PERFORMANCE TEST AT SHOP vs AT SITE
Why apply performance tests at the shop and at the site? Performance tests at the shop and at the site are essential to ensure the reliable and safe operation of special steam turbines. Shop tests are typically conducted during the manufacturing process to verify the turbine’s performance characteristics, while site tests are performed after installation to validate performance under actual operating conditions.
When to apply performance tests: Performance tests at the shop are typically conducted before the turbine is shipped to the site, while site tests are performed after installation and commissioning. Shop tests ensure that the turbine meets the specified performance criteria before being deployed, while site tests verify performance in the actual operating environment.
Where to apply performance tests: Shop performance tests are conducted at the manufacturing facility or a dedicated test site, where the turbine can be thoroughly evaluated under controlled conditions. Site performance tests are conducted at the installation site, where the turbine is integrated into the power generation plant or industrial facility.
What is involved in performance tests: Performance tests involve measuring and evaluating key parameters of the special steam turbine to assess its performance characteristics. This includes measurements such as power output, efficiency, steam flow rate, inlet and outlet pressures and temperatures, vibration levels, and control system functionality.
Which factors determine the need for performance tests: The need for performance tests is determined by factors such as the criticality of the steam turbine in the plant’s operations, the complexity of the turbine design, the size and capacity of the turbine, regulatory requirements, and the presence of contractual obligations.
How to apply performance tests at the shop and at the site: a. Shop Performance Tests:
- Develop a comprehensive test plan that outlines the specific procedures, measurements, and acceptance criteria.
- Conduct mechanical inspections to ensure the turbine components meet specified tolerances and quality standards.
- Perform performance testing under controlled conditions, measuring parameters such as power output, efficiency, and vibration levels.
- Evaluate control system functionality, including startup, shutdown, and safety sequences.
- Document the test procedures, measurements, observations, and deviations, and provide a comprehensive report.
b. Site Performance Tests:
- Prepare the installation site and ensure proper commissioning and integration of the steam turbine into the power generation plant.
- Conduct performance tests under actual operating conditions, measuring parameters such as power output, efficiency, steam flow rate, and control system response.
- Monitor and assess vibration levels, temperature profiles, and other critical parameters during site tests.
- Verify control system functionality, including safety interlocks and emergency shutdown procedures.
- Document the site performance test procedures, measurements, observations, deviations, and provide a comprehensive report.
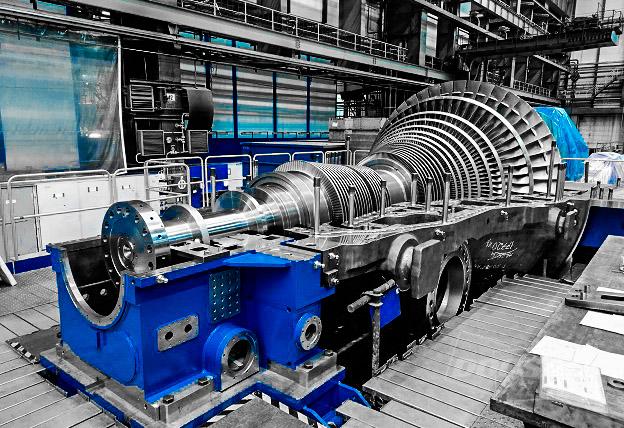
PROCEDURES, ACTIONS, STUDIES, MITIGATION, RECOMMENDATIONS TO APPLY PERFORMANCE TEST AT SHOP vs AT SITE
Procedures for Performance Testing: a. Shop Performance Testing:
- Develop a detailed test plan that outlines the specific test procedures, measurements, acceptance criteria, and safety considerations.
- Conduct mechanical inspections and functional checks to ensure all components are installed correctly and meet the specified tolerances.
- Perform performance tests under controlled conditions, measuring parameters such as power output, efficiency, steam flow rate, temperature, and pressure.
- Evaluate the performance of control systems, including startup, shutdown, and safety sequences.
- Document the test procedures, measurements, observations, and any deviations from expected performance.
b. Site Performance Testing:
- Prepare the installation site, ensuring proper alignment, connection to auxiliary systems, and commissioning of the steam turbine.
- Develop a comprehensive test plan that includes procedures for testing under actual operating conditions, safety protocols, and data collection methods.
- Conduct performance tests, measuring parameters such as power output, efficiency, steam flow rate, temperature, and pressure under real-world operating conditions.
- Monitor critical parameters, such as vibration levels, temperature profiles, and control system response, during site performance testing.
- Document the site performance test procedures, measurements, observations, deviations, and any necessary adjustments made during testing.
Actions for Performance Testing: a. Shop Performance Testing:
- Ensure proper installation and alignment of components, including blades, rotors, nozzles, and casings.
- Verify the calibration and accuracy of measurement instruments used during performance testing.
- Conduct thorough inspections of the steam turbine to identify and address any potential issues before testing.
- Follow standardized procedures for starting up, operating, and shutting down the turbine during shop testing.
b. Site Performance Testing:
- Implement safety measures and protocols to protect personnel and equipment during site performance testing.
- Monitor and record operating parameters, including steam conditions, temperature, pressure, and control system responses.
- Collect data at different operating conditions to evaluate the turbine’s performance across a range of operating scenarios.
- Perform vibration analysis and monitoring to identify potential issues related to rotor dynamics and blade integrity.
- Conduct thorough functional tests of control systems, safety interlocks, and emergency shutdown procedures.
Studies for Performance Testing Improvement: a. Failure Analysis Studies:
- Perform failure analysis studies to identify common failure modes and root causes specific to special steam turbines.
- Analyze historical data, case studies, and industry research to understand failure mechanisms and improve testing protocols.
- Study maintenance records and repair histories to identify recurring issues and implement corrective actions.
b. Reliability and Safety Studies:
- Conduct reliability and safety studies to assess potential risks, vulnerabilities, and safety concerns associated with special steam turbines.
- Identify critical failure points and implement measures to mitigate risks, such as redundancy, safety interlocks, and protective systems.
Mitigation Measures:
Quality Assurance:
- Implement robust quality assurance programs throughout the manufacturing process to ensure that special steam turbines meet design specifications and industry standards.
- Conduct thorough inspections and tests at each stage of production to identify and address any potential quality issues.
Component Testing and Certification:
- Ensure that all critical components of the steam turbine, such as blades, rotors, casings, and control systems, undergo rigorous testing and certification before installation.
- Verify the compliance of components with industry standards and specifications to mitigate the risk of component failures.
Training and Competency:
- Provide comprehensive training to operators and maintenance personnel on the proper operation and maintenance of special steam turbines.
- Ensure that personnel involved in performance testing are well-trained and competent in conducting the tests and interpreting the results.
Risk Assessment:
- Perform thorough risk assessments to identify potential hazards associated with the performance testing process.
- Implement appropriate risk mitigation measures to minimize the likelihood of accidents or incidents during testing.
Recommendations:
Standardized Test Procedures:
- Develop standardized test procedures that cover all critical aspects of performance testing, including instrumentation, data collection, and safety protocols.
- Ensure that these procedures are followed consistently during both shop and site performance tests.
Realistic Operating Conditions:
- Replicate operating conditions as closely as possible during performance tests to obtain accurate performance data.
- Consider factors such as steam temperature, pressure, flow rate, and ambient conditions to ensure realistic test conditions.
Comprehensive Data Collection:
- Implement a comprehensive data collection system during performance testing to capture all relevant parameters.
- Use advanced instrumentation and data acquisition tools to accurately measure and record performance data.
Vibration Analysis and Monitoring:
- Conduct vibration analysis and monitoring during performance tests to detect any excessive vibration levels that could indicate potential issues with rotor dynamics or blade integrity.
- Implement appropriate measures to mitigate vibration-related risks.
Continuous Improvement:
- Continuously review and analyze performance test results to identify areas for improvement in the design, manufacturing, and operation of special steam turbines.
- Incorporate lessons learned from performance testing into future turbine designs and testing procedures.
Compliance with Regulations and Standards:
- Ensure that performance testing of special steam turbines complies with relevant regulations, industry standards, and best practices.
- Stay updated with any changes in regulatory requirements and industry standards related to performance testing.
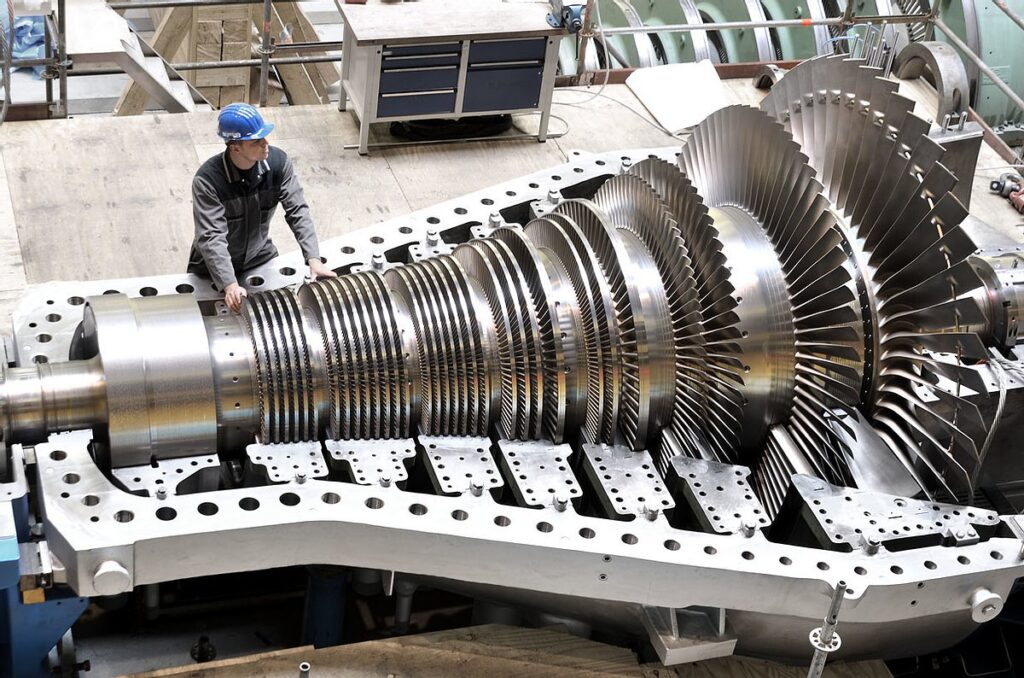