RECENT ADVANCES IN TECHNOLOGY - 1 / CENTRIFUGAL COMPRESSORS
JOURNAL & THRUST BEARINGS - MAGNETIC vs LUBE OIL BEARINGS
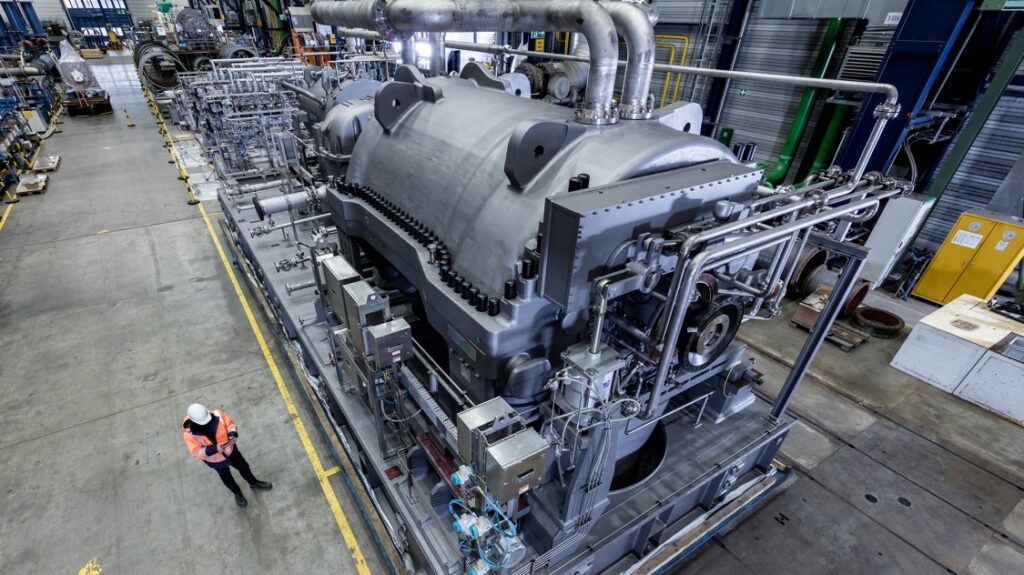
ADVANTAGES & DISADVANTAGES - MAGNETICS vs LUBE OIL BEARINGS
Journal and thrust magnetic bearings offer a number of advantages over traditional lubricated bearings in centrifugal compressors and turbomachinery. These include improved reliability, maintainability, availability, and safety.
Advantages:
Reliability: Magnetic bearings do not suffer from the same wear and tear as traditional lubricated bearings, reducing the likelihood of mechanical failure. They are also less susceptible to damage from contamination or insufficient lubrication, which can cause lubricated bearings to fail.
Maintenance: Magnetic bearings require less maintenance than traditional bearings. They do not require lubrication or regular replacement, and their non-contact design reduces the likelihood of mechanical problems.
Availability: Because magnetic bearings are less likely to fail and require less maintenance, they offer improved availability. This is especially important in the oil, gas, and petrochemical industries, where unplanned downtime can be extremely costly.
Safety: Magnetic bearings reduce the risk of fires and explosions caused by leaks of flammable materials, which can occur with lubricated bearings. This is because they do not require oil or other lubricants, which can ignite under certain conditions.
Disadvantages:
Cost: Magnetic bearings are more expensive to manufacture and install than traditional bearings. This can make them less attractive for new projects, where cost is a major factor in decision-making.
Complexity: Magnetic bearings are more complex than traditional bearings, requiring specialized knowledge and skills to install and maintain. This can increase the cost and time required for maintenance and repairs.
Power consumption: Magnetic bearings require electrical power to operate, which can increase power consumption and costs. This may not be a significant issue for smaller machines, but can be a concern for larger machinery.
Limited application: Magnetic bearings may not be suitable for all applications. They may not be appropriate for machines that operate at extremely high temperatures or pressures, for example.
Overall, the decision to use magnetic bearings over traditional lubricated bearings will depend on a number of factors, including the specific application, the cost of the equipment, and the availability of skilled personnel to maintain and repair the equipment.
LIMITATIONS IN ENGINEERING & DESIGN FOR MAGNETIC BEARINGS
While journal and thrust magnetic bearings offer numerous advantages over traditional lubricated oil bearings in centrifugal compressors and turbomachinery, there are also some limits in their engineering and design. These include the following:
Operational limits: One of the main limitations of magnetic bearings is their operational limits. They may not be suitable for machines that operate at very high speeds or high temperatures, or under extreme conditions such as in corrosive environments. The engineering and design of magnetic bearings must take these operational limits into account to ensure that the bearings operate safely and efficiently.
Power consumption: Magnetic bearings require electrical power to operate, which can increase power consumption and costs. This may not be a significant issue for smaller machines, but can be a concern for larger machinery, especially if the power supply is unreliable or subject to frequent fluctuations.
Complexity: Magnetic bearings are more complex than traditional bearings and require specialized knowledge and skills to design, install and maintain. This can increase the cost and time required for maintenance and repairs.
Cost: Magnetic bearings are more expensive to manufacture and install than traditional bearings. This can make them less attractive for new projects, where cost is a major factor in decision-making.
Availability of skilled personnel: The installation, maintenance and repair of magnetic bearings require specialized knowledge and skills, which may not be readily available in some regions or industries. This can limit the widespread adoption of magnetic bearings in certain applications.
Safety concerns: While magnetic bearings can reduce the risk of fires and explosions caused by leaks of flammable materials, there may be safety concerns related to the use of electrical power and the potential for magnetic fields to interfere with other equipment or sensitive electronic components.
Design integration: Magnetic bearings require integration with other system components, such as controllers, sensors and power supplies. The design and engineering of these components must be carefully coordinated to ensure that the system operates as intended.
Overall, while journal and thrust magnetic bearings offer significant advantages over traditional lubricated oil bearings, their engineering and design must take into account their operational limits, power consumption, complexity, cost, availability of skilled personnel, safety concerns, and design integration to ensure reliable and safe operation in centrifugal compressors and turbomachinery in oil, gas, and petrochemical industries.
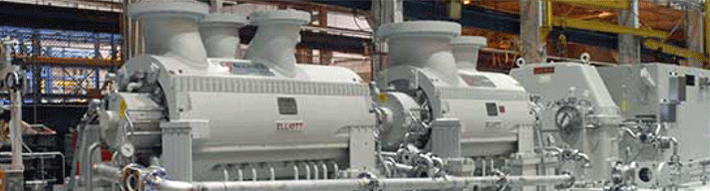
WHY, WHERE, WHEN TO USE MAGNETIC BEARINGS IN TURBOMACHINERY
Journal and thrust magnetic bearings can be used in centrifugal compressors and turbomachinery to improve reliability, maintainability, availability, and safety in new projects and existing plants in the oil, gas, and petrochemical industries. Below are some key reasons why, where, and when to use magnetic bearings instead of traditional lubricated oil bearings:
Reliability: Magnetic bearings offer higher reliability than lubricated oil bearings as they do not suffer from the same wear and tear caused by friction and lubricant breakdown. This can reduce the likelihood of critical failures and unscheduled shutdowns, leading to improved overall equipment reliability.
Maintainability: Magnetic bearings require less maintenance than traditional bearings. They do not require regular lubrication or replacement, and their non-contact design reduces the likelihood of mechanical problems. This can reduce maintenance costs and increase equipment uptime.
Availability: Magnetic bearings can improve equipment availability by reducing the frequency of maintenance and repair. This can be particularly important in the oil, gas, and petrochemical industries where unscheduled downtime can be very costly.
Safety: Magnetic bearings eliminate the risk of oil leakage, which can be a major safety concern in the presence of flammable gases and liquids. They also reduce the risk of fires and explosions caused by leaks of flammable materials, which can occur with lubricated bearings. This can improve overall plant safety.
High-speed applications: Magnetic bearings are well-suited for high-speed applications where lubricated bearings may fail due to increased friction, heat, and wear. This can include centrifugal compressors, turbo-expanders, and other types of turbomachinery used in the oil, gas, and petrochemical industries.
Large machines: Magnetic bearings can also be advantageous in large machines where the weight and size of traditional bearings can create additional mechanical stresses and loads. This can lead to improved equipment performance and reduced maintenance requirements.
Harsh environments: Magnetic bearings can operate in harsh environments where lubricated bearings may not be suitable, such as in corrosive or contaminated conditions. They can also be used in extreme temperature applications where lubricants may break down or freeze.
In summary, journal and thrust magnetic bearings can be used in a wide range of applications to improve equipment reliability, maintainability, availability, and safety in the oil, gas, and petrochemical industries. Their use can help reduce the likelihood of critical failures and unscheduled shutdowns, leading to improved overall equipment performance and reduced maintenance costs.
PROCEDURES, ACTIONS, STUDIES AND RECOMMENDATIONS USING MAGNETIC BEARINGS
In order to use journal and thrust magnetic bearings instead of lubricated oil bearings in centrifugal compressors and turbomachinery to improve reliability, maintainability, availability, and safety, the following procedures, actions, studies, and recommendations can be considered:
Conduct a feasibility study: Before deciding to use magnetic bearings, a feasibility study should be conducted to evaluate the suitability of magnetic bearings for the specific application. This study should consider factors such as equipment size, speed, load, and operating environment.
Design and analysis: The design and analysis of the equipment should be performed to ensure that it is compatible with magnetic bearings. This includes structural analysis, vibration analysis, and rotor dynamics analysis. The design should also consider the required power electronics and control system.
Selection of magnetic bearing supplier: A reputable magnetic bearing supplier should be selected who can provide high-quality bearings, power electronics, and control systems. The supplier should be experienced in designing, manufacturing, and installing magnetic bearings for the oil, gas, and petrochemical industries.
Installation and commissioning: The installation and commissioning of magnetic bearings should be performed by experienced professionals. The installation process should follow the supplier’s guidelines and recommendations.
Performance testing: After installation, the equipment should undergo performance testing to ensure that it meets the required specifications. This testing should include functional testing, dynamic testing, and load testing.
Training and maintenance: Operators and maintenance personnel should be trained in the proper operation and maintenance of magnetic bearings. The maintenance procedures should include periodic inspection, cleaning, and replacement of components as required.
Monitoring and diagnostics: Monitoring and diagnostics systems should be installed to detect any potential issues with the magnetic bearings. These systems can include vibration monitoring, temperature monitoring, and oil analysis.
In summary, the use of journal and thrust magnetic bearings in centrifugal compressors and turbomachinery to improve reliability, maintainability, availability, and safety requires a comprehensive approach that includes feasibility studies, design and analysis, supplier selection, installation and commissioning, performance testing, training and maintenance, and monitoring and diagnostics. By following these procedures, actions, studies, and recommendations, critical failures and unscheduled shutdowns can be reduced, leading to improved overall equipment performance and reduced maintenance costs in the oil, gas, and petrochemical industries.
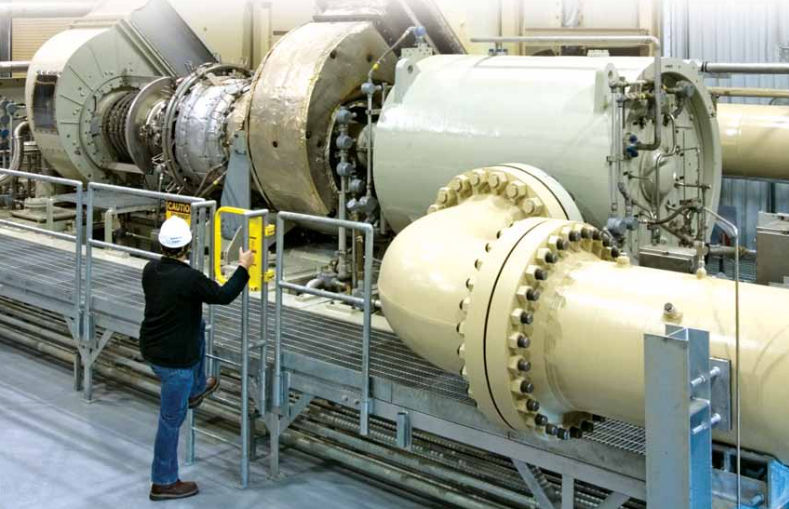
CRITICAL RISKS USING MAGNETIC BEARINGS INSTEAD OF LUBE OIL BEARINGS
Using journal and thrust magnetic bearings instead of lubricated oil bearings in centrifugal compressors and turbomachinery can offer several advantages, such as improved reliability, maintainability, availability, and safety. However, there are also critical risks associated with using these types of bearings that need to be addressed to avoid critical failures and unscheduled shutdowns. Some of these risks include:
Compatibility with Existing Equipment: Retrofitting existing equipment with journal and thrust magnetic bearings may require modifications to the equipment, such as changes in shaft diameter or the addition of support structures. These modifications can increase the risk of equipment failure or operational issues.
Bearing Reliability: The reliability of journal and thrust magnetic bearings can be affected by several factors, including electrical supply reliability, magnetic field strength, and the presence of any contaminants or debris in the system. A failure of the bearing can lead to equipment damage, unscheduled shutdowns, and potential safety hazards.
Bearing Control System: The control system for journal and thrust magnetic bearings needs to be carefully designed and maintained to ensure the safe and reliable operation of the equipment. Control system failures can lead to bearing damage, equipment failure, and safety hazards.
Maintenance: Proper maintenance of journal and thrust magnetic bearings is essential to ensure their safe and reliable operation. This includes regular inspection, cleaning, and replacement of any worn or damaged components. Failure to perform proper maintenance can lead to equipment damage, unscheduled shutdowns, and safety hazards.
Cost: Journal and thrust magnetic bearings can be more expensive than traditional lubricated bearings. The increased cost can be a barrier to adoption and can impact project feasibility and profitability.
Technology Maturity: Journal and thrust magnetic bearing technology is relatively new and may not have been widely adopted or tested in all applications. This can lead to uncertainty around the long-term reliability and performance of the technology.
In summary, critical risks associated with using journal and thrust magnetic bearings in centrifugal compressors and turbomachinery include compatibility with existing equipment, bearing reliability, control system reliability, maintenance, cost, and technology maturity. Addressing these risks through appropriate safety measures, maintenance practices, and technology selection can help to reduce the likelihood of critical failures and unscheduled shutdowns.