SPECIAL STEAM TURBINES - UPGRADE vs UPDATE vs UPRATE vs RERATE vs REVAMP
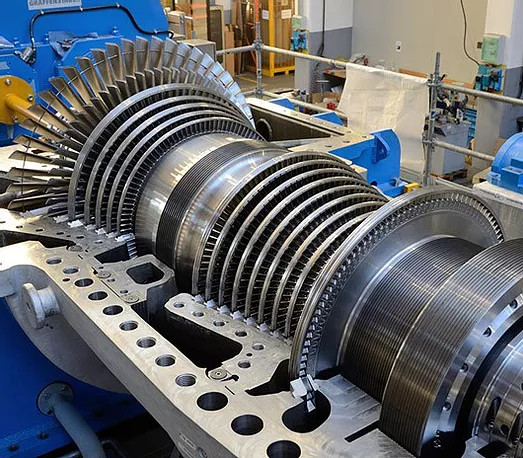
UPGRADE
UPDATE
Special steam turbines are typically used in industrial processes such as power generation, petrochemical production, and refining. These turbines are critical components of the process, and any unscheduled shutdowns or critical failures can have significant impacts on the production and profitability of the facility. Therefore, it is important to consider upgrades and modernizations to improve the reliability, maintainability, availability, safety, quality control, and efficiency of these turbines.
The reasons or actions to proceed with an upgrade or modernization related to the engineering and design of special steam turbines include:
Performance assessment: A performance assessment of the steam turbine will provide valuable information about its current operating condition, efficiency, and any areas for improvement.
Identify upgrade options: Based on the performance assessment, possible upgrades can be identified, such as retrofitting with new blades, bearings, or control systems, or upgrading the steam path design.
Design and engineering: Once the upgrade options have been identified, the design and engineering process can begin. This will involve detailed design work to ensure that the upgrades can be safely and reliably integrated into the existing turbine.
Installation and commissioning: The installation and commissioning process must be carefully managed to ensure that the new components are installed correctly and that the steam turbine can operate safely and reliably with the upgrades in place. This will require a comprehensive testing program to ensure that the new components are functioning as expected and that the steam turbine meets the new design specifications.
Ongoing maintenance: Once the upgrades have been installed, ongoing maintenance will be required to ensure that the steam turbine continues to operate safely and reliably. This will involve regular inspections, testing, and maintenance of the steam turbine’s components to identify and address any issues before they can lead to unscheduled shutdowns or critical failures.
Overall, the key to a successful upgrade or modernization of special steam turbines is careful planning and execution of the upgrade process, with a focus on improving the turbine’s reliability, maintainability, availability, safety, quality control, and efficiency. This will help to avoid unscheduled shutdowns and critical failures, and ensure that the turbine can continue to operate efficiently and reliably for many years to come.
An update to the engineering and design for special steam turbines can be done to improve the reliability, maintainability, availability, safety, quality control, and efficiency of the equipment, which can help avoid critical failures or unscheduled shutdowns. Some reasons for an update could include outdated technology or components, changes in operational requirements, or a desire to improve performance or reduce costs.
To proceed with an update, the first step would be to assess the current condition of the special steam turbine and identify areas where improvements can be made. This may involve analyzing performance data, conducting a risk assessment, or consulting with experts in the field.
Once areas for improvement have been identified, the design can be updated to incorporate new technologies or components, improve the overall efficiency of the turbine, or enhance safety features. It may also involve modifying the turbine’s controls or instrumentation to improve the monitoring and control of the equipment.
After the updated design has been developed, it will need to be validated through testing and verification before implementation. This may involve testing the updated turbine in a laboratory or a pilot installation before it is deployed in the field.
During implementation, the updated turbine will need to be installed and integrated into the existing system. This may involve modifications to piping, electrical connections, or control systems.
Finally, after the updated special steam turbine is operational, it will need to be monitored to ensure that it is performing as expected and to identify any issues that may arise. Regular maintenance and inspections will be necessary to ensure the continued reliability and efficiency of the equipment.
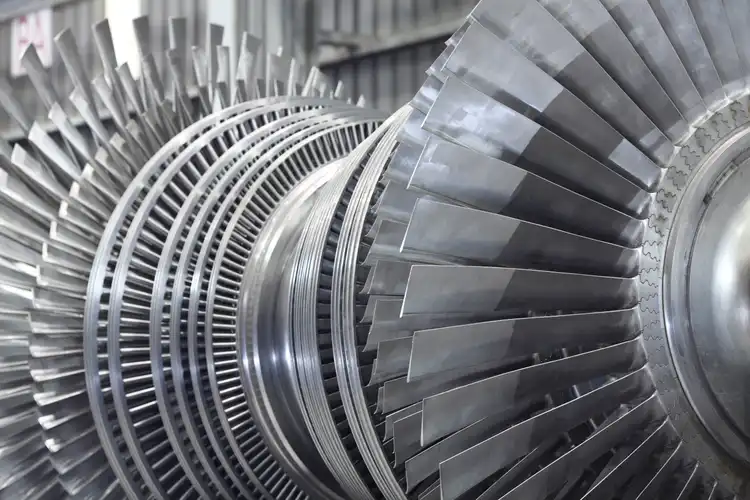
UPRATE
RERATE
An uprate to the engineering and design for special steam turbines can be done to increase the power output or improve the performance of the equipment while maintaining or improving reliability, maintainability, availability, safety, quality control, and efficiency. Some reasons for an uprate could include increased demand for power, changes in operational requirements, or a desire to improve the efficiency of the turbine.
To proceed with an uprate, the first step would be to evaluate the feasibility of the uprate based on the current condition and design of the special steam turbine. This may involve analyzing the performance data, conducting a risk assessment, or consulting with experts in the field.
Once the feasibility of the uprate has been established, the design can be updated to incorporate new technologies or components that can handle the increased power output or improve the efficiency of the turbine. This may involve upgrading the turbine’s components such as blades, nozzles, or diaphragms to withstand higher pressures and temperatures.
After the updated design has been developed, it will need to be validated through testing and verification before implementation. This may involve testing the uprated turbine in a laboratory or a pilot installation before it is deployed in the field.
During implementation, the uprated turbine will need to be installed and integrated into the existing system. This may involve modifications to piping, electrical connections, or control systems.
Finally, after the uprated special steam turbine is operational, it will need to be monitored to ensure that it is performing as expected and to identify any issues that may arise. Regular maintenance and inspections will be necessary to ensure the continued reliability and efficiency of the equipment. The operating procedures and maintenance practices may also need to be updated to reflect the changes made during the uprate process.
A rerate for special steam turbines involves modifying or upgrading the existing equipment to increase its power output beyond the original design specifications. The primary reasons for a rerate could be to meet increased power demand, optimize plant efficiency, or extend the life of the equipment.
To proceed with a rerate, the following actions should be taken:
Feasibility study: Conduct a feasibility study to determine if the rerate is technically and economically viable. This study will consider factors such as the condition of the existing equipment, the capacity of supporting systems, and the impact on the plant’s operations and maintenance.
Redesign: If the feasibility study determines that a rerate is possible, then the equipment will be redesigned to accommodate the increased power output. This redesign may involve modifications to the turbine rotor, steam path, or control system.
Component testing: The modified or upgraded components should undergo rigorous testing to ensure that they meet the required specifications and standards.
Installation and commissioning: After the modified or upgraded components have been tested and approved, they can be installed and commissioned. The installation and commissioning process should follow established protocols to ensure that the equipment is installed correctly and operates safely.
Operational testing: After the rerate, the equipment should undergo operational testing to ensure that it meets the required performance and efficiency standards.
Training: The operators and maintenance personnel should be trained on the new or modified equipment to ensure that they can operate and maintain it safely and effectively.
Ongoing maintenance and monitoring: Ongoing maintenance and monitoring should be conducted to ensure that the equipment operates at the highest levels of reliability, maintainability, availability, safety, quality control, and efficiency.
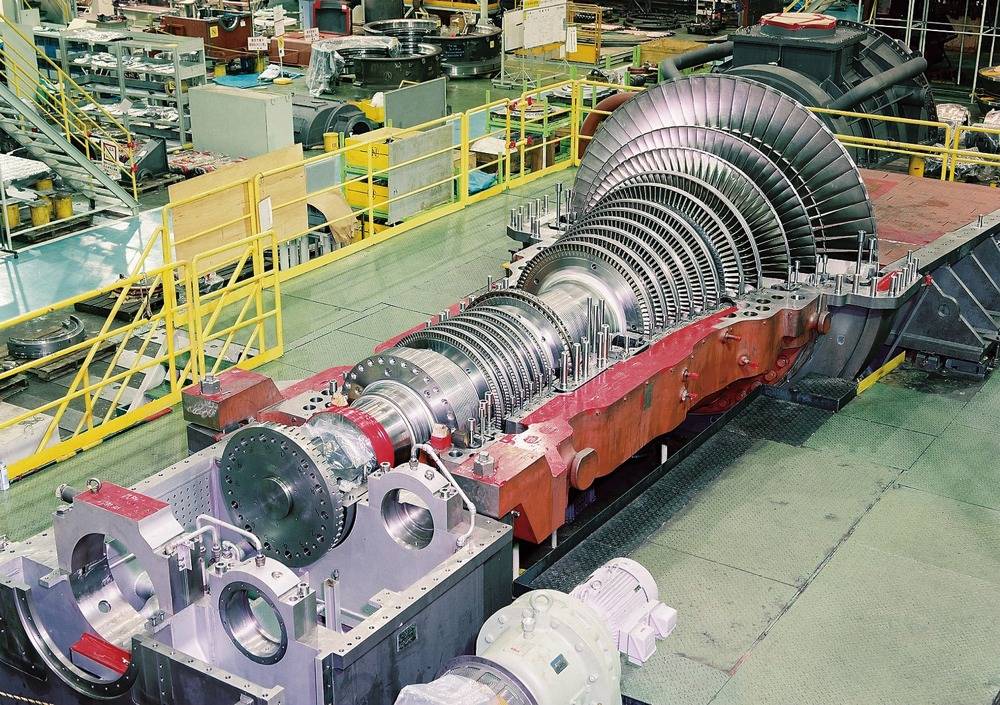
REVAMP
REVAMP strategies can also be applied to special steam turbines in the power generation, oil, gas, and petrochemical industries to enhance their reliability, performance, and prevent critical failures. Here’s an explanation of how REVAMP can be utilized for special steam turbines:
Efficiency and Performance Optimization: REVAMP projects often aim to improve the efficiency and performance of special steam turbines. This can involve various enhancements such as redesigning the turbine blades and nozzles to optimize steam flow, modifying the steam path for improved heat transfer, and upgrading control systems. These improvements result in increased power generation capacity, improved thermal efficiency, and reduced energy consumption.
Component Upgrades and Replacements: REVAMP initiatives may include upgrading or replacing critical components of special steam turbines. This can involve the replacement of worn-out or inefficient parts such as blades, casings, seals, and bearings with newer designs or advanced materials. Upgrading to more durable and efficient components enhances the turbine’s reliability, reduces maintenance requirements, and extends its operational life.
Advanced Monitoring and Diagnostics: Implementing advanced monitoring and diagnostic systems is crucial in REVAMP projects for special steam turbines. This includes the installation of sensors and data acquisition systems to monitor parameters such as temperature, pressure, vibration, and lubrication. By continuously monitoring turbine health, operators can detect potential issues early, predict maintenance needs, and prevent critical failures. Data analytics and predictive maintenance algorithms can help optimize maintenance schedules and maximize turbine performance.
Control System Upgrades: Upgrading the control systems of special steam turbines is another key aspect of REVAMP. Advanced control algorithms and automation technologies enable better regulation of steam flow, temperature, and other operating parameters. Improved control systems enhance the turbine’s response to load changes, increase stability, and optimize operation, leading to enhanced reliability and performance.
Safety and Environmental Enhancements: REVAMP initiatives also focus on safety and environmental considerations for special steam turbines. This can include the implementation of safety features such as overspeed protection systems, emergency shutdown mechanisms, and improved instrumentation and control systems. Environmental enhancements may involve upgrades to meet emission regulations, such as the integration of pollution control technologies and the use of alternative fuels.
By applying REVAMP strategies to special steam turbines, operators can improve their reliability, performance, and safety, while minimizing the risk of critical failures. These improvements result in increased operational efficiency, reduced downtime, improved safety, and compliance with environmental regulations.