Consulting – TECHNOLOGY FOR POWER AUGMENTATION IN GAS TURBINES
TECHNOLOGY ABOUT POWER AUGMENTATION IN GAS TURBINES
There are several technologies available that can increase or augment the output power in gas turbines, including:
Water injection: Water injection is a process that involves injecting water into the combustion chamber of a gas turbine to increase power output and improve efficiency. Water injection can reduce the temperature of the combustion gases, which reduces the NOx emissions, increases the mass flow rate of air, and reduces the compressor discharge temperature.
Steam injection: Steam injection is a process that involves injecting steam into the combustion chamber of a gas turbine to increase power output and efficiency. Steam injection increases the mass flow rate of air, reduces the compressor discharge temperature, and reduces the NOx emissions.
Inlet air cooling: Inlet air cooling is a process that involves cooling the incoming air before it enters the gas turbine. Cooling the air increases the mass flow rate of air, which increases the power output and efficiency of the gas turbine. Inlet air cooling can be achieved using different methods, such as evaporative cooling, absorption cooling, and mechanical cooling.
Compressor intercooling: Compressor intercooling is a process that involves cooling the compressed air between compressor stages to reduce the compressor discharge temperature. Lowering the compressor discharge temperature increases the mass flow rate of air, which increases the power output and efficiency of the gas turbine.
Turbine blade cooling: Turbine blade cooling is a process that involves cooling the turbine blades to reduce the temperature of the turbine components and increase their lifespan. The cooling can be achieved using different methods, such as film cooling, impingement cooling, and convective cooling.
Exhaust heat recovery: Exhaust heat recovery is a process that involves recovering the waste heat from the exhaust gases of the gas turbine and using it to produce additional power or to provide heating or cooling.
All of these technologies can improve the efficiency, performance, reliability, availability, and safety of gas turbines. However, each technology has its own benefits and drawbacks, and the most suitable technology will depend on the specific requirements of the gas turbine and its operating conditions. Careful evaluation and analysis should be conducted before implementing any of these technologies to ensure they are applied in the most effective and efficient way possible.
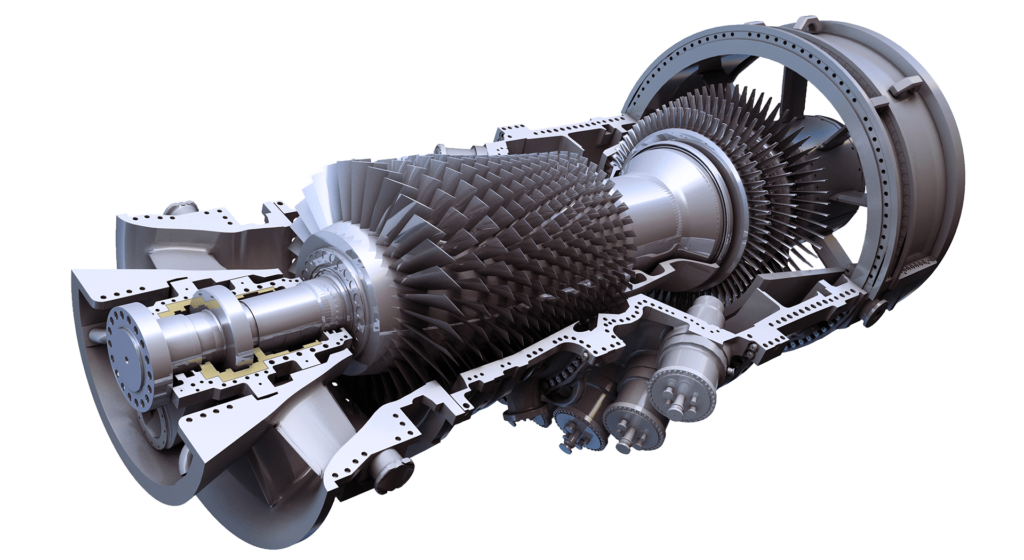
LIMITS IN ENGINEERING & DESIGN TO INCREASE THE OUTPUT POWER
While there are several technologies available to increase or augment the output power in gas turbines, there are also limits in engineering and design that must be considered. These limits can affect the efficiency, performance, reliability, availability, and safety of gas turbines. Some of the main limits include:
Material limitations: The use of water injection, steam injection, or cooling water systems at inlet air can increase the temperature and pressure within the gas turbine, which can put stress on the materials used in the turbine. This stress can cause mechanical failure and reduce the lifespan of the turbine. Therefore, the materials used in the turbine must be carefully selected and designed to withstand the increased stress.
Combustion instability: The use of water injection or steam injection can affect the combustion stability within the gas turbine. The presence of water or steam in the combustion chamber can change the fuel-air mixture, which can cause instability in the combustion process. This instability can lead to reduced performance and reliability of the gas turbine.
Environmental limits: The use of water injection or cooling water systems can have environmental impacts, such as water usage and discharge. These impacts must be considered in the design and operation of the gas turbine to ensure compliance with environmental regulations and minimize the impact on local ecosystems.
Cost limitations: The implementation of these technologies can involve significant costs in terms of design, construction, and operation. These costs must be carefully evaluated against the expected benefits to ensure that the investment is justified.
Overall, the limits in engineering and design for increasing or augmenting the output power in gas turbines must be carefully evaluated and addressed to ensure the efficiency, performance, reliability, availability, and safety of the gas turbine. The implementation of these technologies should be approached with a holistic view that considers the technical, environmental, and economic factors to maximize the benefits and minimize the risks.
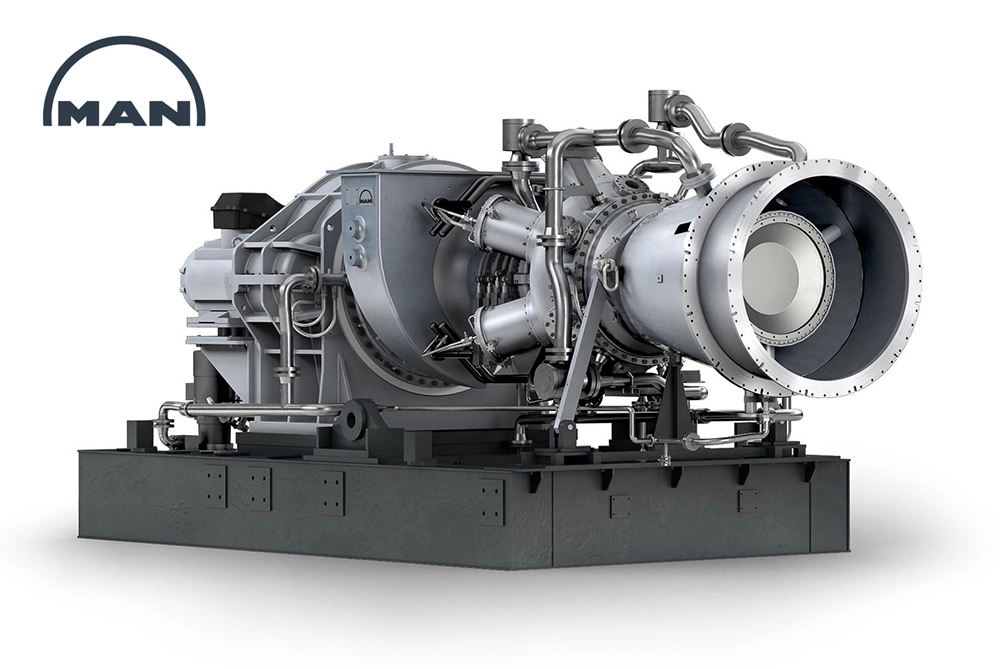
WHY, WHEN, WHERE TO INCREASE OR AUGMENT THE OUTPUT POWER IN GAS TURBINES
The reasons for increasing or augmenting the output power in gas turbines using technologies such as water injection, steam injection, or cooling water systems at inlet air can vary depending on the specific situation. Generally, these technologies are implemented to improve the efficiency, performance, reliability, availability, and safety of gas turbines. The following are some common reasons for their implementation:
Efficiency improvement: By increasing the power output of a gas turbine, the efficiency of the power generation process can be improved. This can lead to reduced fuel consumption, lower emissions, and lower operating costs.
Peak demand management: During periods of peak demand for electricity, it may be necessary to increase the power output of gas turbines to meet the increased demand. Technologies such as water or steam injection can provide a quick and effective way to increase power output during these periods.
Fuel flexibility: In some cases, the use of water or steam injection can allow gas turbines to operate on lower quality fuels. This can increase the flexibility of the power generation system and reduce dependence on a single fuel source.
Maintenance reduction: By increasing the power output of a gas turbine, the number of turbines required to meet power demand can be reduced. This can result in lower maintenance costs and improved reliability.
The specific technology and implementation approach will depend on the particular gas turbine and its operating conditions. The decision to implement these technologies should be based on a careful evaluation of the technical, environmental, and economic factors. The implementation of these technologies should also be done in accordance with industry standards and regulations to ensure safety and reliability.
PROCEDURES, ACTIONS, STUDIES, MITIGATION, RECOMMENDATIONS TO INCREASE OR AUGMENT THE OUTPUT POWER IN GAS TURBINES
The procedures, actions, studies, mitigation, and recommendations to increase or augment the output power in gas turbines using technologies such as water injection, steam injection, or cooling water systems at inlet air can vary depending on the specific situation. However, the following are some general steps and considerations:
Feasibility study: A feasibility study should be conducted to determine the technical, economic, and environmental feasibility of implementing these technologies. This study should consider the specific gas turbine, operating conditions, and regulatory requirements.
Design and engineering: Once the feasibility study has been completed, the gas turbine system should be designed and engineered to incorporate the chosen technology. This includes modifications to the gas turbine, control system, and supporting infrastructure.
Testing and commissioning: Before the system is put into operation, testing and commissioning should be conducted to ensure that the modifications have been successfully implemented and that the system is operating as expected.
Ongoing monitoring and maintenance: Once the system is operational, ongoing monitoring and maintenance should be conducted to ensure that the system is operating safely and reliably. This includes monitoring performance metrics, conducting regular inspections and maintenance, and addressing any issues that arise.
Mitigation of risks: Implementation of these technologies may introduce new risks to the gas turbine system. Mitigation measures should be implemented to ensure that these risks are identified and managed effectively. This may include developing contingency plans, conducting risk assessments, and implementing appropriate safety measures.
Industry standards and regulations: The implementation of these technologies should be done in accordance with industry standards and regulations to ensure safety and reliability. These standards and regulations may include those related to gas turbine design, installation, operation, and maintenance.
Overall, the successful implementation of these technologies requires careful planning, design, testing, and ongoing maintenance. The goal should be to increase power output while ensuring the reliability, availability, and safety of the gas turbine system.
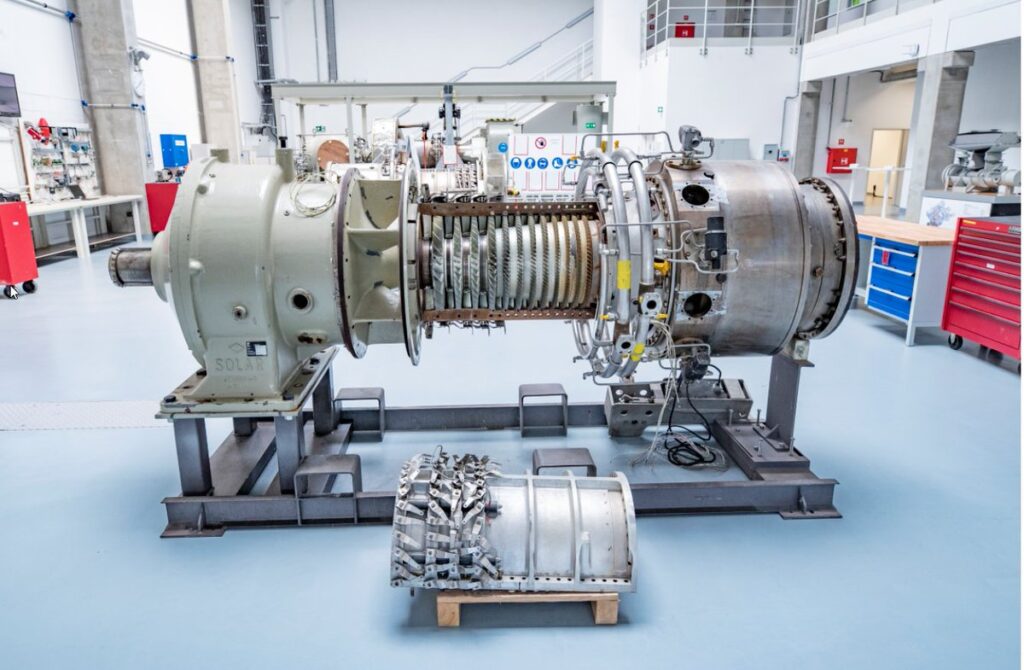