CENTRIFUGAL COMPRESSORS - UPGRADE vs UPDATE vs UPRATE vs RERATE vs REVAMP
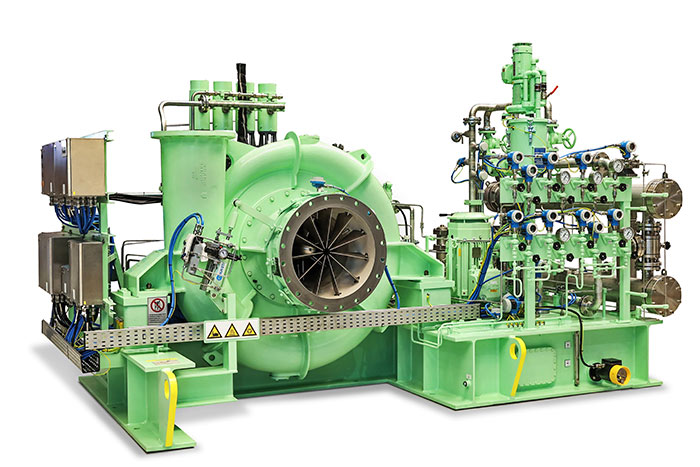
UPGRADE
UPDATE
Improved efficiency: Modernizing the compressor’s design can lead to improved efficiency and reduced energy consumption. This can involve upgrading to more advanced control systems, using more efficient materials or components, or incorporating variable speed drives. By improving efficiency, you can lower operating costs and reduce the compressor’s environmental impact.
Enhanced reliability: Upgrading or modernizing the compressor can improve its overall reliability. This can involve replacing worn or outdated components, upgrading to more robust materials, or implementing advanced monitoring systems. By doing so, you can reduce the risk of equipment failure and unscheduled downtime.
Improved safety: Modernizing the compressor’s design can also improve its safety features. This can involve implementing fail-safe mechanisms, upgrading to more advanced sensors or alarms, or improving operator training. By improving safety, you can reduce the risk of accidents or injuries and improve overall workplace safety.
Improved maintainability: Upgrading or modernizing the compressor’s design can also improve its maintainability. This can involve simplifying the design, using standardized components, or implementing advanced diagnostic systems. By doing so, you can reduce the time and effort required for maintenance and repairs, and improve overall equipment uptime.
Enhanced quality control: Upgrading or modernizing the compressor’s design can also improve its quality control. This can involve implementing advanced testing or monitoring systems, upgrading to more accurate sensors or controls, or implementing statistical process control techniques. By improving quality control, you can ensure that the compressor is meeting all relevant standards and regulations and reduce the risk of equipment failure.
In summary, upgrading or modernizing engineering and design for centrifugal compressors can have a significant impact on their reliability, maintainability, availability, safety, quality control, and efficiency. By focusing on improving these key areas, you can avoid critical failures or unscheduled shutdowns, lower operating costs, and improve overall equipment performance.
Conduct a thorough analysis of the compressor’s current performance: Before any updates are made, it’s important to understand how the compressor is currently performing. This can involve reviewing operational data, conducting tests, and analyzing maintenance records. By doing so, you can identify areas where improvements are needed and prioritize which updates to make first.
Review and update maintenance procedures: One of the best ways to improve reliability and maintainability is to review and update maintenance procedures. This can involve creating a comprehensive maintenance schedule, developing standard operating procedures, and providing training to maintenance personnel. By doing so, you can ensure that the compressor is being properly maintained and reduce the likelihood of unscheduled downtime.
Improve safety features: Safety is paramount when it comes to compressors, especially in industrial settings. Updating safety features can involve adding sensors or alarms to detect potential issues, implementing fail-safe mechanisms, and ensuring that proper safety protocols are being followed. By doing so, you can reduce the risk of accidents or injuries and improve overall safety.
Incorporate new technology: Advances in technology can provide significant benefits when it comes to compressor performance. For example, incorporating new sensors or control systems can improve efficiency and reduce energy consumption. Additionally, new materials or manufacturing techniques can enhance the durability and reliability of components. By staying up-to-date with the latest technology, you can ensure that your compressor is operating at peak performance.
Implement a quality control program: Quality control is essential to ensuring that your compressor is operating as intended. This can involve conducting regular inspections, performing tests, and using statistical process control techniques to identify issues before they become critical. By implementing a quality control program, you can improve efficiency, reduce downtime, and ensure that your compressor is meeting all relevant standards and regulations.
In summary, updating engineering and design for centrifugal compressors can involve a range of actions and considerations. By focusing on reliability, maintainability, availability, safety, quality control, and efficiency, you can ensure that your compressor is operating as intended and avoid critical failures or unscheduled shutdowns.
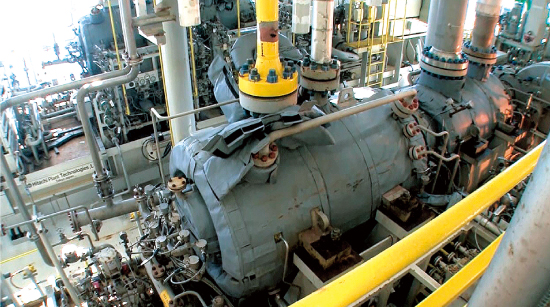
UPRATE
RERATE
Review and analyze the compressor’s current performance: Before any uprate modifications are made, it’s important to review and analyze the compressor’s current performance. This can involve reviewing operational data, conducting tests, and analyzing maintenance records. By doing so, you can identify areas where improvements are needed and prioritize which modifications to make first.
Upgrade components: One way to improve the capacity or performance of a centrifugal compressor is to upgrade its components. This can involve replacing or upgrading the impeller, diffuser, or other critical components with higher-performance versions. By doing so, you can increase the compressor’s flow rate, pressure, or other performance parameters.
Increase the speed: Increasing the speed of a centrifugal compressor is another way to improve its capacity or performance. This can involve upgrading the motor or using a variable frequency drive to increase the compressor’s rotational speed. By doing so, you can increase the compressor’s flow rate or pressure.
Redesign the compressor: Redesigning the compressor can also improve its capacity or performance. This can involve increasing the number of impellers or diffusers, changing the compressor’s configuration, or using more advanced materials or manufacturing techniques. By doing so, you can improve the compressor’s efficiency, reliability, and overall performance.
Improve safety features: Increasing the capacity or performance of a centrifugal compressor can also impact its safety features. It’s important to ensure that any modifications made do not compromise the safety of the compressor or the operators working with it. This can involve upgrading safety systems, implementing fail-safe mechanisms, and providing additional operator training.
Implement a quality control program: Increasing the capacity or performance of a centrifugal compressor can also impact its quality control. It’s important to ensure that any modifications made are properly tested and meet all relevant standards and regulations. By implementing a quality control program, you can ensure that the compressor is operating as intended and reduce the risk of equipment failure.
In summary, an uprate of a centrifugal compressor can have a significant impact on its reliability, maintainability, availability, safety, quality control, and efficiency. By focusing on upgrading components, increasing speed, redesigning the compressor, improving safety features, and implementing a quality control program, you can ensure that the uprate project improves the compressor’s performance while avoiding critical failures or unscheduled shutdowns.
Identify the need for a rerate: The need for a rerate may arise due to changes in operating conditions, process requirements, or regulatory standards. Before any modifications are made, it’s important to identify the need for a rerate and evaluate the potential benefits and risks.
Review and analyze the compressor’s current performance: Before any rerate modifications are made, it’s important to review and analyze the compressor’s current performance. This can involve reviewing operational data, conducting tests, and analyzing maintenance records. By doing so, you can identify areas where modifications are needed and prioritize which modifications to make first.
Modify components: Modifying components is one way to change the performance parameters of a centrifugal compressor. This can involve changing the impeller, diffuser, or other critical components to increase or decrease the compressor’s flow rate, pressure, or other performance parameters.
Adjust operating parameters: Adjusting the operating parameters of a centrifugal compressor is another way to change its performance parameters. This can involve changing the inlet or discharge pressure, temperature, or other operating parameters to achieve the desired performance.
Implement a quality control program: Implementing a quality control program is critical when undertaking a rerate project. It’s important to ensure that any modifications made are properly tested and meet all relevant standards and regulations. By implementing a quality control program, you can ensure that the compressor is operating as intended and reduce the risk of equipment failure.
Upgrade safety features: Modifying a centrifugal compressor to change its performance parameters can also impact its safety features. It’s important to ensure that any modifications made do not compromise the safety of the compressor or the operators working with it. This can involve upgrading safety systems, implementing fail-safe mechanisms, and providing additional operator training.
In summary, a rerate of a centrifugal compressor can have a significant impact on its reliability, maintainability, availability, safety, quality control, and efficiency. By identifying the need for a rerate, reviewing and analyzing the compressor’s current performance, modifying components or adjusting operating parameters, implementing a quality control program, and upgrading safety features, you can ensure that the rerate project improves the compressor’s performance while avoiding critical failures or unscheduled shutdowns.
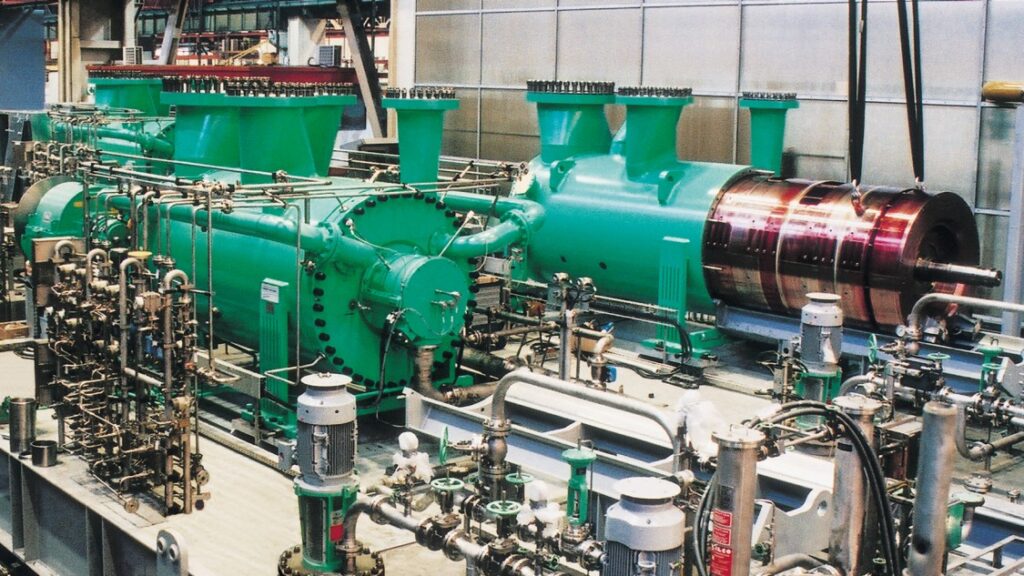
REVAMP
REVAMP, which stands for “Retrofits, Upgrades, Enhancements, and Modernizations of Plants,” refers to a strategy employed to enhance existing machinery and systems in order to optimize their performance, extend their operational life, and prevent critical failures. In the context of centrifugal compressors, REVAMP involves implementing various modifications and upgrades to improve their reliability and efficiency.
Here are some common approaches used in REVAMP projects for centrifugal compressors:
Performance Enhancements: REVAMP focuses on improving the efficiency and output of the compressors. This can include aerodynamic redesign of impellers and diffusers, optimizing the clearance between impellers and casings, and enhancing inlet and discharge configurations. These modifications aim to increase the compressor’s capacity, improve its energy efficiency, and reduce operating costs.
Advanced Control Systems: Upgrading the control systems of centrifugal compressors can lead to more precise operation and better performance. Advanced control algorithms and automation technologies enable tighter control over process variables, such as flow rates, pressures, and temperatures. This results in improved stability, reduced energy consumption, and enhanced overall system reliability.
Mechanical Upgrades: REVAMP projects may involve mechanical upgrades to critical components of centrifugal compressors. This can include replacing worn-out or outdated parts, such as bearings, seals, and impellers, with newer, more durable materials or designs. Upgrading to more robust and reliable components helps prevent failures and extends the operational life of the compressors.
Condition Monitoring and Predictive Maintenance: Implementing advanced condition monitoring systems and predictive maintenance strategies is a crucial part of REVAMP. These technologies allow operators to monitor the health and performance of centrifugal compressors in real-time, detecting any potential issues before they escalate into critical failures. By identifying early warning signs of problems, maintenance activities can be scheduled proactively, minimizing downtime and maximizing reliability.
Safety and Environmental Compliance: REVAMP projects also address safety and environmental concerns. Upgrades may include implementing safety features, such as improved emergency shutdown systems, enhanced vibration monitoring, and explosion-proof designs. Additionally, modifications may be made to ensure compliance with environmental regulations, such as reducing emissions or improving energy efficiency.
By applying REVAMP strategies to centrifugal compressors, both in new projects and existing plants, the aim is to enhance their reliability, optimize performance, and minimize the risk of critical failures. These improvements result in increased operational efficiency, reduced downtime, improved safety, and a more sustainable operation within the oil, gas, and petrochemical industries.