PERFORMACE TEST (AT SHOP vs AT SITE) - TURBOMACHINERY
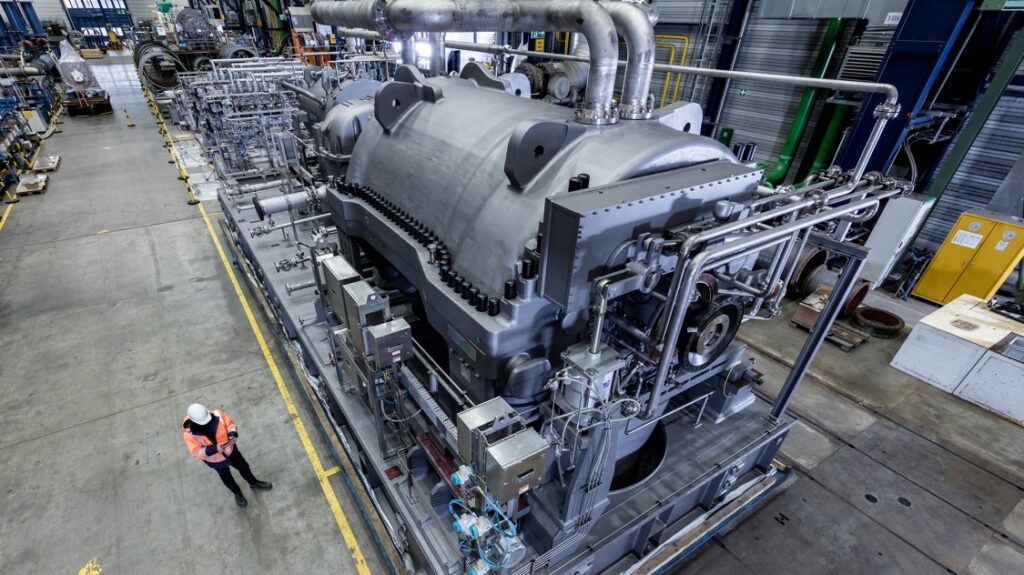
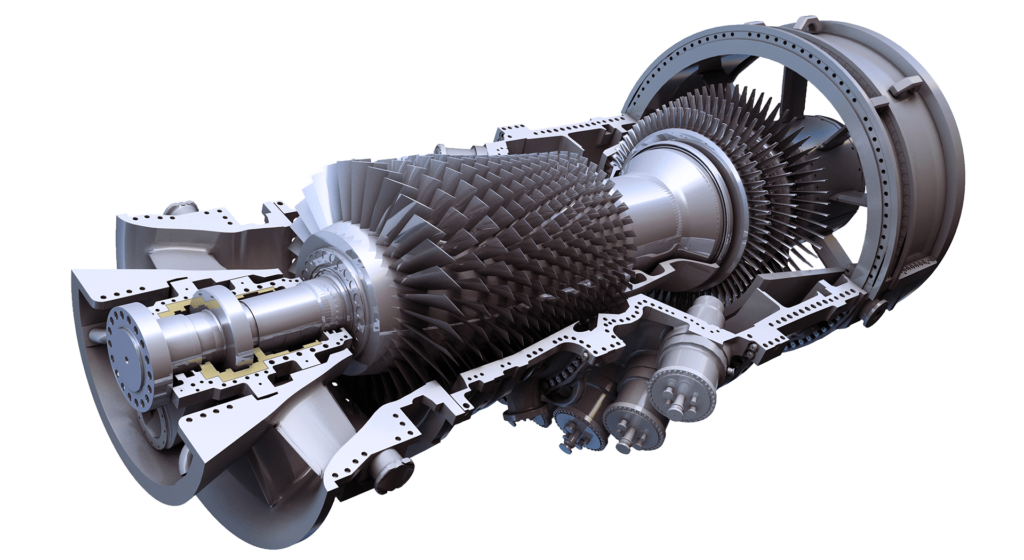
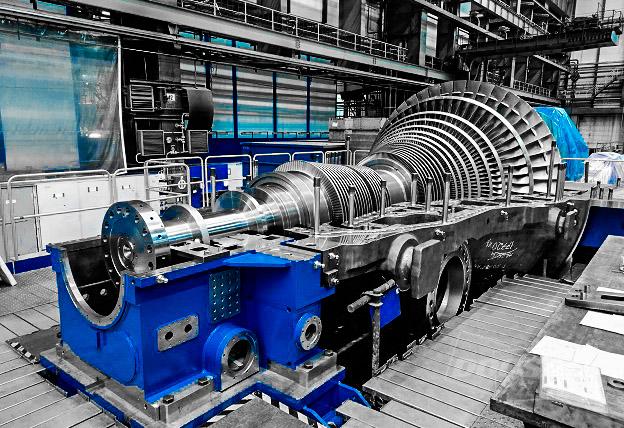
CENTRIFUGAL COMPRESSORS
GAS TURBINES
SPECIAL STEAM TURBINES
FREQUENT QUESTIONS & ANSWERS ABOUT PERFORMANCE TEST
CENTRIFUGAL COMPRESSORS
Here are some frequently asked questions and answers regarding performance testing of centrifugal compressors:
Q: What is a performance test for centrifugal compressors? A: A performance test is a type of test conducted on a centrifugal compressor to evaluate its performance in terms of efficiency, capacity, power consumption, and other parameters.
Q: Why is a performance test necessary for centrifugal compressors? A: A performance test is necessary to ensure that the centrifugal compressor is operating efficiently, safely, and at its design capacity. It can also help identify any potential issues or inefficiencies that could lead to critical risks and failures.
Q: When should a performance test be conducted for a centrifugal compressor? A: A performance test should be conducted during the commissioning stage of a new centrifugal compressor or when the compressor undergoes major repairs or modifications. It is also recommended to conduct regular performance tests to ensure ongoing efficiency and reliability.
Q: What standards are used for performance testing of centrifugal compressors? A: The most commonly used standard for performance testing of centrifugal compressors is ASME PTC-10. Other standards may be used depending on the specific application and industry.
Q: Where should a performance test be conducted for a centrifugal compressor, at the shop or at the site? A: The decision to conduct a performance test at the shop or at the site depends on various factors such as the size of the compressor, accessibility, and availability of testing facilities. Site tests are typically preferred as they provide a more accurate representation of real-world operating conditions.
Q: How long does a performance test take? A: The duration of a performance test depends on various factors such as the size of the compressor and the parameters being tested. Typically, a performance test can take anywhere from a few hours to several days.
Q: What are some benefits of conducting a performance test for a centrifugal compressor? A: Some benefits of conducting a performance test include identifying potential issues before they become critical, improving efficiency and reliability, reducing downtime and maintenance costs, and ensuring compliance with industry standards and regulations.
GAS TURBINES
Here are some common questions and answers related to performance testing of gas turbines:
Q: What is the purpose of a performance test for gas turbines? A: The main purpose of a performance test for gas turbines is to verify their operational efficiency and to identify any performance deviations or issues that could lead to equipment failures or safety hazards. It is also used to ensure compliance with regulatory standards and to optimize operational costs.
Q: When is it necessary to perform a performance test for gas turbines? A: A performance test is typically conducted during the commissioning of a new gas turbine or after a major overhaul or repair work. It may also be performed periodically to monitor the performance and efficiency of the turbine, or if there are any significant changes in the operating conditions.
Q: What are the benefits of conducting a performance test at a shop rather than on-site? A: Conducting a performance test at a shop allows for greater control over the testing environment, reducing the potential for external factors to affect the results. Additionally, it can minimize downtime for the equipment being tested and reduce disruptions to the overall process plant operations.
Q: What are the benefits of conducting a performance test on-site rather than at a shop? A: Conducting a performance test on-site allows for a more accurate representation of the actual operating conditions, including variables such as ambient temperature and humidity, gas quality, and inlet pressure. It also allows for easier access to the equipment being tested, which can facilitate troubleshooting and identification of any issues that may arise.
Q: What standards are typically used for performance testing of gas turbines? A: The ASME PTC-22 standard is commonly used for performance testing of gas turbines, along with other international standards such as ISO 2314 and API 616.
Q: How long does a performance test for a gas turbine typically take? A: The duration of a performance test can vary depending on the specific equipment being tested and the testing procedures used. Generally, a full-scale performance test can take anywhere from several days to several weeks to complete.
Q: What are the potential risks or drawbacks of conducting a performance test for a gas turbine? A: There are some potential risks associated with performance testing, including the potential for equipment damage or failure during testing, and the possibility of measurement errors or inaccuracies. Additionally, performance testing can be costly and time-consuming, and may require significant planning and coordination with other plant operations.
SPECIAL STEAM TURBINES
Here are some frequently asked questions and answers regarding performance testing for special steam turbines:
Q: What is a special steam turbine? A: A special steam turbine is a type of turbine that is designed for a specific application or function, such as driving a pump or compressor in an industrial process.
Q: Why is performance testing important for special steam turbines? A: Performance testing is important for special steam turbines because it allows for the identification of any inefficiencies or malfunctions that may be affecting the turbine’s performance. By detecting these issues early, they can be addressed before they lead to more serious problems, such as equipment failure or safety hazards.
Q: What is the difference between testing at a shop and testing at a site? A: Testing at a shop involves conducting the performance test on the turbine while it is in a controlled environment, such as a manufacturing facility. Testing at a site involves conducting the test on the turbine while it is installed and operating in its intended location. Testing at a site allows for a more accurate assessment of the turbine’s performance under real-world conditions.
Q: What is ASME PTC-6? A: ASME PTC-6 is a performance testing standard developed by the American Society of Mechanical Engineers (ASME) for steam turbines. It provides guidelines for conducting performance tests and evaluating the results.
Q: What are some of the benefits of performance testing for special steam turbines? A: Some of the benefits of performance testing for special steam turbines include:
- Improved efficiency and energy savings
- Identification of issues that could lead to equipment failure or safety hazards
- Verification of the turbine’s design specifications
- Optimization of maintenance and repair schedules
- Improved overall reliability and performance of the turbine.
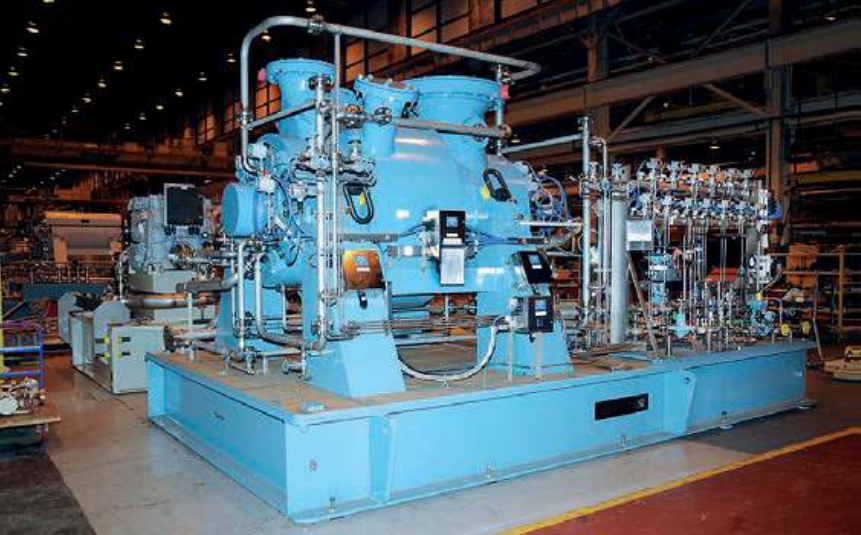
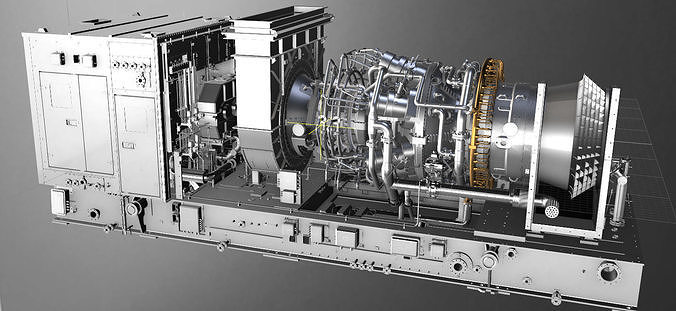
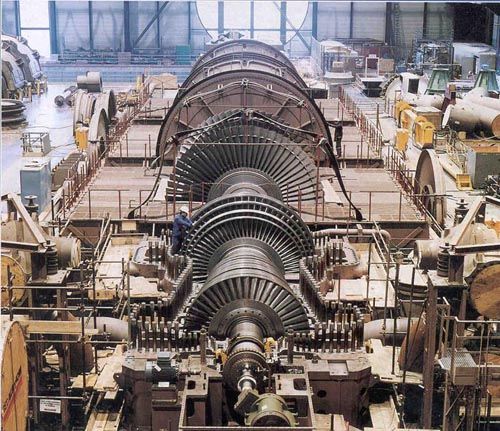