Consulting – USING BIOFUEL vs HYDROGEN – GAS TURBINES
USING BIOFUEL vs HYDROGEN IN COMBUSTION - GAS TURBINES
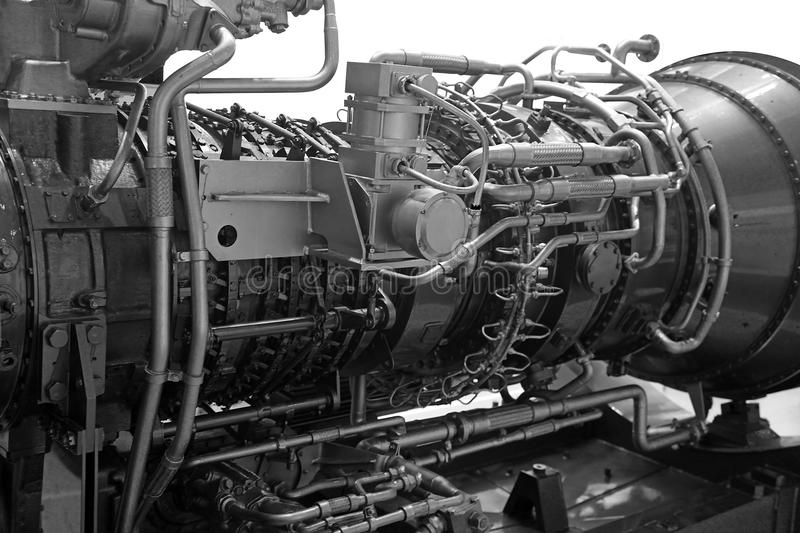
LIMITS IN ENGINEERING & DESIGN - BIOFUEL vs HYDROGEN
Fuel Composition and Properties: Both biofuels and hydrogen have different combustion characteristics compared to conventional fossil fuels. Biofuels often have lower energy densities and different chemical compositions, which may require modifications to burner designs and combustion processes. Hydrogen, on the other hand, has a high reactivity and low ignition energy, necessitating specialized handling and safety measures.
Flame Stability and Combustion Dynamics: Biofuels and hydrogen can exhibit different flame stability characteristics compared to conventional fuels. Maintaining stable and efficient combustion with varying compositions and properties can be challenging. It requires careful design considerations and potentially advanced control systems to ensure reliable and safe operation.
Emissions and Pollutant Control: While biofuels offer potential environmental benefits due to their renewable nature, they may still produce emissions such as nitrogen oxides (NOx) and particulate matter during combustion. Managing and controlling these emissions can be crucial for meeting environmental regulations. Hydrogen combustion, on the other hand, produces minimal carbon emissions but can generate higher levels of NOx due to high flame temperatures.
Infrastructure and Compatibility: Integrating biofuels or hydrogen into existing gas turbine plants may require modifications to infrastructure and combustion systems. Compatibility issues, such as material compatibility with hydrogen, may arise, and additional safety measures, such as leak detection systems and explosion prevention, need to be considered.
Fuel Supply and Availability: Biofuels are derived from renewable sources, but their availability can be limited and dependent on factors like agricultural yields and production capacity. Hydrogen, although a promising alternative, requires dedicated production and distribution infrastructure to ensure a reliable supply, which can be a limitation in some regions.
Safety Considerations: Both biofuels and hydrogen introduce specific safety considerations. Biofuels can present flammability and storage challenges, while hydrogen has a wide flammability range and requires stringent safety protocols due to its high reactivity and potential for embrittlement of materials.
System Integration and Efficiency: Integrating biofuels or hydrogen into existing gas turbine systems may require retrofitting or redesigning components, which can impact overall system efficiency. Additionally, the lower energy density of biofuels and the lower calorific value of hydrogen can affect the overall performance and power output of the gas turbine.
To overcome these limitations, careful engineering and design considerations should be applied, including advanced combustion modeling, material selection, control systems optimization, and thorough safety assessments. It’s crucial to assess the specific requirements and challenges of each project and conduct detailed feasibility studies to ensure the successful integration of biofuels or hydrogen into gas turbine systems while prioritizing reliability, safety, environmental sustainability, and regulatory compliance.
ADVANTAGES & DISADVANTAGES USING BIOFUELS vs HYDROGEN IN GAS TURBINES
Advantages of Biofuels:
- Renewable and Sustainable: Biofuels are derived from organic matter, such as plant materials or waste, making them a renewable energy source. Their use helps reduce dependence on fossil fuels and contributes to mitigating climate change.
- Carbon Emission Reduction: Biofuels generally have lower carbon emissions compared to fossil fuels. They can help reduce greenhouse gas emissions, supporting environmental sustainability and meeting emission reduction targets.
- Compatibility with Existing Infrastructure: Biofuels can often be blended with conventional fuels or used as drop-in replacements in existing industrial plants with minimal modifications to infrastructure, allowing for smoother integration.
- Local Production and Energy Security: Biofuels can be produced locally, reducing dependence on international fuel supplies and enhancing energy security.
- Potential for Waste Management: Biofuels can be produced from organic waste materials, offering an opportunity for waste management and reducing environmental pollution.
Disadvantages of Biofuels:
- Limited Availability and Feedstock Competition: The availability of biofuels can be limited, as their production depends on factors such as agricultural yields and land use. Competition for feedstock resources with food production can also be a concern.
- Lower Energy Density: Biofuels typically have lower energy densities compared to fossil fuels, which may result in a reduction in power output and efficiency of gas turbines.
- Impact on Food Prices: The use of certain feedstocks for biofuel production, such as corn or soybeans, can lead to increased competition with food production, potentially impacting food prices and food security.
- Emissions and Pollution: While biofuels have lower carbon emissions, they can still generate pollutants such as nitrogen oxides (NOx) and particulate matter during combustion, necessitating appropriate emission control measures.
- Fuel Stability and Quality: The quality and stability of biofuels can vary, leading to challenges in storage, handling, and combustion. Proper fuel management and quality control measures are essential to ensure reliable operation
Advantages of Hydrogen:
- Zero Carbon Emissions: Hydrogen combustion produces no direct carbon emissions, making it a clean energy source and a valuable solution for decarbonizing power generation and reducing greenhouse gas emissions.
- High Energy Density: Hydrogen has a high energy density, enabling improved power output and efficiency in gas turbines, potentially resulting in higher overall plant performance.
- Fuel Flexibility: Hydrogen can be produced from various sources, such as renewable energy, natural gas reforming with carbon capture, or biomass gasification. This flexibility allows for diversified fuel options, enhancing energy security and reducing dependency on specific resources.
- Potential for Energy Storage: Hydrogen can be utilized for energy storage, enabling the integration of renewable energy sources and providing grid balancing capabilities, enhancing the reliability and availability of power generation.
- Wide Range of Applications: Hydrogen can be used not only in gas turbines but also in fuel cells for various applications, including transportation, heating, and industrial processes, providing versatility in energy usage.
Disadvantages of Hydrogen:
- Infrastructure Requirements: Widespread adoption of hydrogen as a fuel requires significant infrastructure development, including production, storage, transportation, and distribution networks. Building this infrastructure can be costly, time-consuming, and require significant investment.
- Safety Concerns: Hydrogen has a wide flammability range and low ignition energy, making it highly combustible. It requires specialized storage and handling systems, stringent safety protocols, and measures to prevent leaks, detect potential hazards, and minimize explosion risks.
- Carbon Emission during Production: Although hydrogen combustion is emission-free, the production methods can still generate carbon emissions, especially if derived from fossil fuel sources without carbon capture and storage. It is important to ensure that hydrogen production methods are environmentally sustainable.
- Material Compatibility: Hydrogen can cause hydrogen embrittlement in certain materials, potentially leading to material degradation, reduced component reliability, and safety risks. Careful selection of materials and adherence to stringent material compatibility standards is necessary.
- Scale-up and Cost: Large-scale production and cost competitiveness of hydrogen can be challenging. Currently, the cost of hydrogen production and infrastructure is higher compared to conventional fuels, making it less economically viable in some contexts. However, ongoing technological advancements and increased scale can lead to cost reduction in the future.
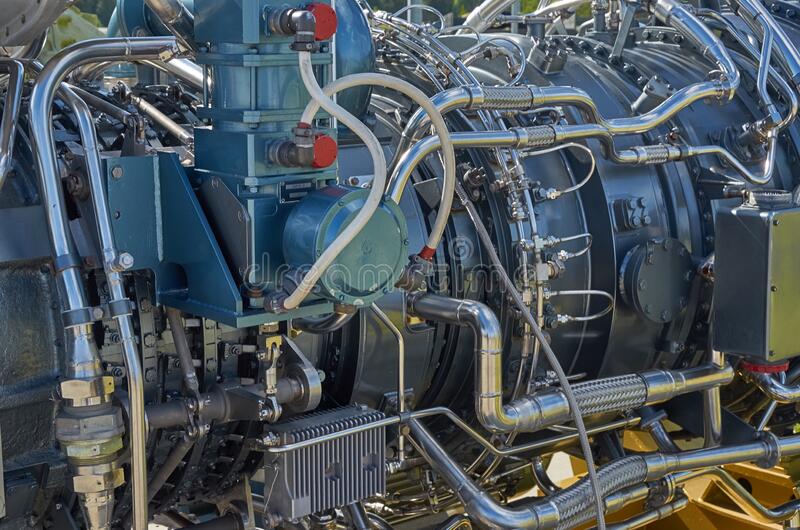
WHY, WHEN, WHERE, WHAT, WHICH, HOW TO APPLY BIOFUELS vs HYDROGEN
Why:
- Environmental Sustainability: Both hydrogen and biofuels offer the advantage of reducing carbon emissions and supporting environmental sustainability goals.
- Renewable Energy Transition: The use of hydrogen and biofuels facilitates the transition from fossil fuels to renewable energy sources, promoting a cleaner and more sustainable energy mix.
- Regulatory Compliance: Utilizing hydrogen and biofuels can help meet increasingly stringent environmental regulations and reduce the potential for penalties or non-compliance.
When:
- Availability of Feedstock: The availability of feedstock, whether it is biomass for biofuels or the availability of hydrogen production methods, is a key factor in determining when to use hydrogen or biofuels.
- Technological Maturity: Consider the maturity and readiness of the technology for using hydrogen or biofuels in gas turbines. Evaluate if the technology is sufficiently advanced and economically viable for deployment.
Where:
- Existing Industrial Plants: Consider retrofitting existing gas turbine plants to accommodate the use of hydrogen or biofuels. Assess the feasibility of integrating these fuels into the existing infrastructure and systems.
- New Projects: When planning new power generation, oil, and gas projects, evaluate the potential for incorporating hydrogen or biofuels from the initial design phase. Determine if the infrastructure and equipment can support the use of these fuels.
What:
- Fuel Selection: Evaluate the specific needs and requirements of the project, considering factors such as energy density, emissions, feedstock availability, and compatibility with existing infrastructure.
- Performance Optimization: Assess the potential impact of using hydrogen or biofuels on gas turbine performance, including power output, efficiency, and reliability. Optimize the combustion process and control systems accordingly.
Which:
- Comparative Analysis: Conduct a thorough comparative analysis of hydrogen and biofuels, considering factors such as carbon emissions, feedstock availability, infrastructure requirements, safety considerations, and cost-effectiveness. Select the fuel that aligns best with the project’s objectives and constraints.
How:
- Engineering Design: Engage engineering expertise to design or retrofit gas turbines and combustors to accommodate the use of hydrogen or biofuels. Consider fuel storage, delivery systems, material compatibility, safety protocols, and emission control technologies.
- Safety Measures: Implement robust safety measures, including leak detection systems, explosion prevention mechanisms, and proper handling and storage procedures, to ensure the safe use of hydrogen or biofuels.
- Monitoring and Maintenance: Establish a comprehensive monitoring and maintenance program to ensure the ongoing reliability and performance of gas turbines using hydrogen or biofuels. Regular inspections, testing, and preventive maintenance are essential.
It’s important to note that the specific implementation of hydrogen or biofuels in gas turbines will depend on the unique circumstances of each project, including location, resource availability, regulatory environment, and project goals. Consulting with experts in the field is recommended to ensure the most effective and safe utilization of these fuels.
PROCEDURES, ACTIONS, STUDIES, MITIGATION, RECOMMENDATIONS USING BIOFUELS vs HYDROGEN
Feasibility Studies: Conduct comprehensive feasibility studies to evaluate the suitability of hydrogen or biofuels for the specific project. This includes assessing fuel availability, infrastructure requirements, technical feasibility, safety considerations, emissions control, and economic viability.
System Design and Modifications: Engage experienced engineers and designers to modify or design gas turbine systems for the use of hydrogen or biofuels. This involves considering factors such as fuel storage, delivery systems, combustion chamber modifications, and material compatibility.
Safety Measures and Risk Assessment: Conduct thorough risk assessments and implement appropriate safety measures specific to hydrogen or biofuels. This includes establishing safety protocols, leak detection systems, explosion prevention mechanisms, and ensuring compliance with safety standards and regulations.
Emission Control Technologies: Implement effective emission control technologies, such as selective catalytic reduction (SCR) systems or particulate matter filters, to mitigate emissions associated with hydrogen or biofuels combustion. Regular monitoring and maintenance of these systems are essential.
Fuel Quality and Supply Chain Management: Establish stringent fuel quality control measures for both hydrogen and biofuels. This includes ensuring consistent fuel composition, purity, and quality throughout the supply chain to maintain optimal combustion performance and reliability.
Training and Education: Provide comprehensive training programs for operators, maintenance personnel, and other relevant staff to ensure they have the necessary knowledge and skills to handle, store, and operate gas turbine systems using hydrogen or biofuels safely and efficiently.
Performance Monitoring and Maintenance: Implement robust monitoring systems to track the performance of gas turbines using hydrogen or biofuels. Regular inspections, testing, and preventive maintenance are critical to maintaining reliable and efficient operation.
Collaboration and Knowledge Sharing: Foster collaboration among industry stakeholders, research institutions, and technology providers to share best practices, lessons learned, and advancements in hydrogen and biofuels utilization in gas turbines. This facilitates continuous improvement and promotes the adoption of innovative solutions.
Regulatory Compliance and Standards: Stay updated with regulatory requirements related to the use of hydrogen or biofuels in gas turbines. Adhere to relevant standards, codes, and guidelines to ensure compliance with safety, environmental, and quality regulations.
Lifecycle Analysis and Sustainability Assessments: Conduct lifecycle assessments to evaluate the overall environmental impact and sustainability of using hydrogen or biofuels in gas turbines. Identify areas for improvement and implement measures to enhance sustainability throughout the lifecycle, including feedstock sourcing, production, utilization, and waste management.
By implementing these procedures, actions, studies, mitigation measures, and recommendations, the use of hydrogen or biofuels in gas turbines can be optimized to improve reliability, availability, safety factors, mitigate environmental risks, and minimize failures in power generation, oil, and gas industries. It is important to adapt these recommendations to the specific context and requirements of each project and seek expertise from relevant industry professionals.
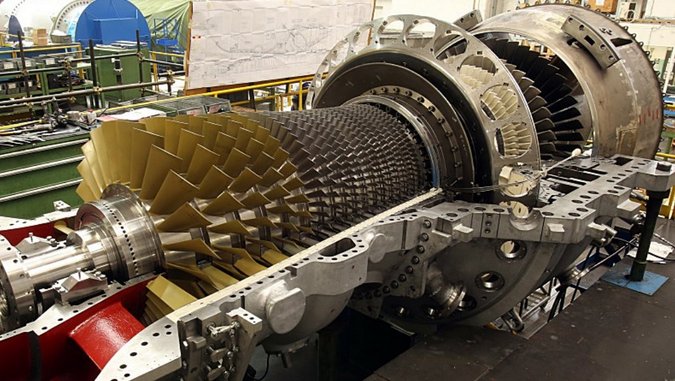
Consulting – USING BIOFUEL vs HYDROGEN – GAS TURBINES Leer más »