RECENT ADVANCES IN TECHNOLOGY – GAS TURBINES – 2
EMISSION CONTROL, MONITORING & PROTECTION SYSTEMS IN EXHAUST GASES OF GAS TURBINES
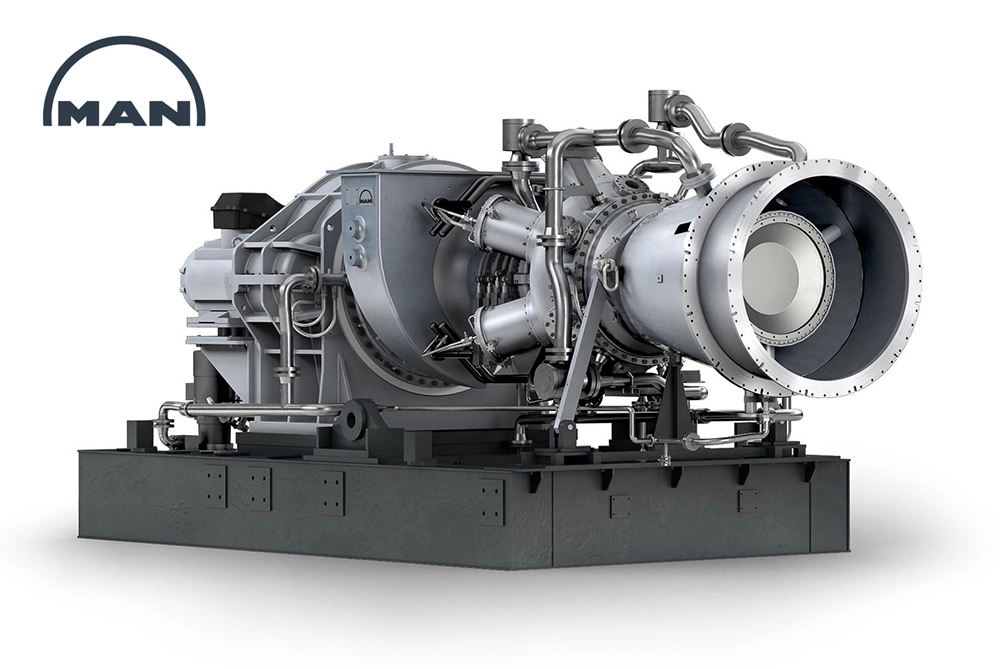
EMISION CONTROL, MONITORING & PROTECTION SYSTEMS IN EXHAUST GASES
Emission control, monitoring, and protection systems are used to minimize the impact of exhaust gases on the environment and ensure compliance with regulatory standards. In gas turbines, these systems are designed to monitor and control the emissions of pollutants such as nitrogen oxides (NOx), carbon monoxide (CO), and particulate matter.
To improve reliability, maintainability, safety, and avoid critical failures or costly shutdowns, the following procedures, actions, studies, mitigations, and recommendations are typically applied in the design, installation, and operation of these systems:
Design and installation: Emission control systems must be properly designed and installed to ensure their effectiveness. This includes selecting appropriate technologies such as catalytic converters, selective catalytic reduction (SCR), or oxidation catalysts. The systems must also be properly integrated with the gas turbine and other plant equipment.
Regular maintenance: Regular maintenance of the emission control systems is essential to ensure their reliability and maintainability. This includes regular inspections, cleaning, and replacement of components as necessary.
Monitoring and reporting: Continuous monitoring of emissions is essential to ensure compliance with regulatory standards. Monitoring systems should be installed to measure emissions in real-time and report to plant operators and regulatory agencies.
Emergency shutdown: In the event of a malfunction or abnormal operation of the emission control system, an emergency shutdown system should be installed to shut down the gas turbine and prevent the release of harmful pollutants.
Training and procedures: Proper training and procedures should be developed and implemented for plant personnel responsible for the operation and maintenance of the emission control system.
Regular testing and certification: Emission control systems should be regularly tested and certified by third-party agencies to ensure compliance with regulatory standards.
Critical risks associated with emission control systems include failure to meet regulatory standards, equipment malfunction or failure, and safety hazards associated with handling and storage of harmful pollutants. Effective mitigation strategies include regular maintenance and inspection, monitoring and reporting, emergency shutdown procedures, proper training and procedures, and regular testing and certification.
LIMITATIONS IN ENGINEERING & DESIGN OF EMISION CONTROL, MOMITORING & PROTECTION SYSTEM IN EXHAUST GASES
There are several limits in engineering and design related to emission control, monitoring, and protection systems in exhaust gases coming out of gas turbines. Some of these limits are:
Technology Limitations: The technology for emission control and monitoring is continuously evolving, but there are still limitations in the efficiency and accuracy of these systems. It is important to ensure that the chosen technology is appropriate for the specific application and that the design is optimized for the best performance.
Space Limitations: The space available for installation of these systems can be limited in existing plants, and it may be difficult to find suitable locations for the equipment without affecting the operation of the gas turbine.
Cost Limitations: Implementation of these systems can be expensive, and there may be limitations on the budget available for the project. It is important to balance the cost with the potential benefits and ensure that the chosen design is cost-effective.
Regulatory Limitations: There may be regulatory limitations and requirements for the emissions that need to be met, and the design of the system needs to comply with these regulations.
Maintenance Limitations: The maintenance of these systems can be complex and time-consuming, and it is important to ensure that the design allows for easy maintenance and minimizes the impact on the operation of the gas turbine.
Overall, it is important to consider all these limitations and design the emission control, monitoring, and protection systems in exhaust gases coming out of gas turbines with a focus on the specific application and potential benefits.
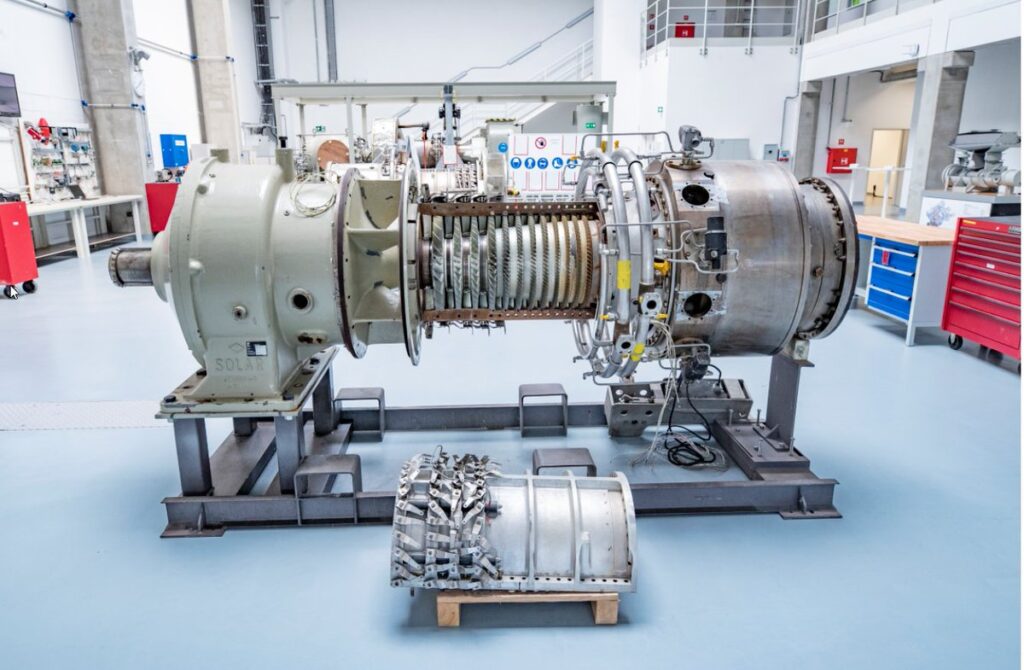
WHY, WHERE, WHEN TO APPLY EMISSIONS CONTROL, MONITORING & PROTECTION IN EXHAUST GASES
The application of emission control, monitoring, and protection systems in exhaust gases coming out of gas turbines is essential for several reasons:
Environmental Compliance: Compliance with environmental regulations is necessary for companies operating in the oil, gas, and petrochemical industries. The emission control systems ensure that the pollutants from the exhaust gases are within acceptable limits set by regulatory authorities.
Health and Safety: Exhaust gases from gas turbines can contain toxic substances that pose a risk to human health and safety. The emission control systems minimize these risks by removing the harmful substances from the exhaust gases.
Equipment Protection: The presence of corrosive or abrasive materials in exhaust gases can cause damage to equipment downstream of the gas turbine. The monitoring and protection systems help to identify and prevent such damage.
Operational Efficiency: The emission control systems can improve the efficiency of gas turbines by reducing the amount of energy lost through exhaust gases. The monitoring systems can also help to identify and address operational inefficiencies in the gas turbine.
The application of emission control, monitoring, and protection systems is recommended for both new projects and existing plants in the oil, gas, and petrochemical industries. It is especially important in plants located in areas with strict environmental regulations or where the health and safety risks associated with exhaust gases are high.
The specific timing for the application of these systems depends on the project or plant’s design, regulatory requirements, and operational needs. In new projects, the emission control, monitoring, and protection systems should be incorporated into the design from the outset. For existing plants, the systems can be retrofitted as needed to improve performance and meet regulatory requirements.
PROCEDURES, ACTIONS, STUDIES, MITIGATIONS, RECOMMENDATION TO USE EMISSION CONTROL, MONITORING & PROTECTION SYSTEM IN EXHAUST GASES
Here are some general procedures, actions, studies, mitigations, and recommendations related to emission control, monitoring, and protection systems in exhaust gases from gas turbines:
Identify and comply with local emissions regulations and guidelines: Make sure to follow the local emissions regulations and guidelines in the region where the gas turbine is located. These regulations may vary by region or country, so it is important to stay up-to-date with the latest requirements.
Choose the appropriate emission control technology: There are various types of emission control technologies available, such as selective catalytic reduction (SCR), exhaust gas recirculation (EGR), and oxidation catalysts. Choose the technology that best fits the specific application, taking into consideration factors such as the type of fuel used, the size of the gas turbine, and the level of emissions required.
Conduct regular emission monitoring: Regular emission monitoring should be conducted to ensure that the gas turbine is operating within the acceptable emission levels. This can be achieved through continuous emissions monitoring systems (CEMS) or periodic emissions testing.
Use predictive maintenance techniques: Predictive maintenance techniques such as vibration analysis and oil analysis can help detect potential issues with the gas turbine before they become critical, reducing the risk of unscheduled downtime and costly repairs.
Implement safety measures: Implement safety measures such as fire protection systems, gas detection systems, and emergency shutdown systems to protect personnel and equipment in the event of an emergency.
Provide proper training: Provide proper training to operators and maintenance personnel to ensure that they are familiar with the gas turbine and the emission control, monitoring, and protection systems. This can help prevent accidents, reduce downtime, and ensure that the gas turbine is operating at peak efficiency.
Conduct regular inspections: Conduct regular inspections of the emission control, monitoring, and protection systems to ensure that they are operating correctly and are in good condition. Replace any components that are worn or damaged to prevent failure during operation.
Overall, the key to successful emission control, monitoring, and protection systems in exhaust gases from gas turbines is to ensure that they are designed, installed, and maintained properly. By following best practices and taking a proactive approach to maintenance and safety, the risk of critical failures or costly shutdowns can be minimized.
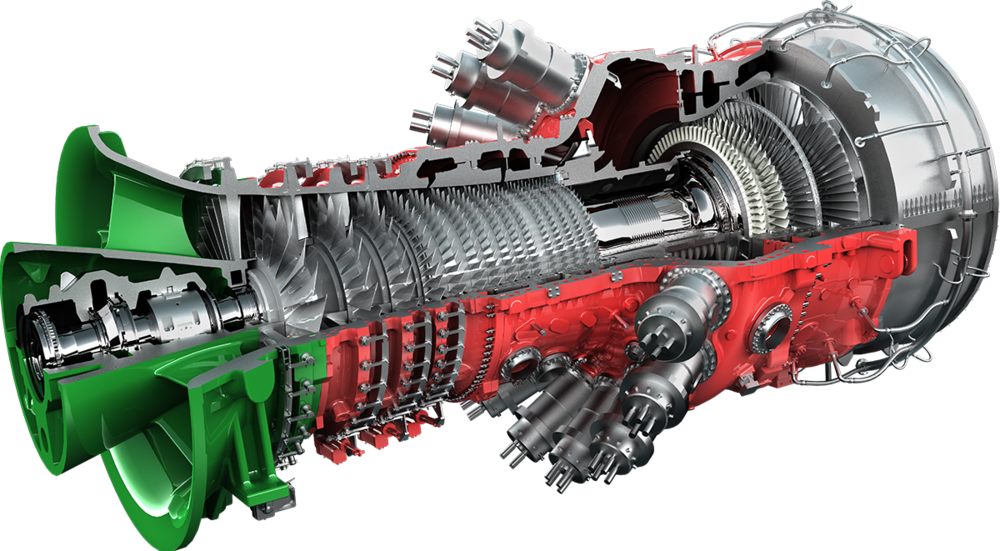
CRITICAL RISKS USING EMISSION CONTROL, MONITORING & PROTECTION SYSTEM FOR THE EXHAUST GASES
There are several critical risks associated with the emission control, monitoring, and protection systems in exhaust gases coming out of gas turbines. These risks include:
Equipment malfunction: The emission control systems are complex and rely on multiple components working together. If any of these components malfunction, the system may not work as intended, which can result in emissions exceeding allowable limits.
Human error: Operators of the equipment can make mistakes in monitoring or adjusting the emission control systems, which can lead to unsafe emissions.
Inadequate maintenance: Regular maintenance and inspections of the emission control systems are critical to their proper functioning. If maintenance is not performed regularly, the equipment may not function as intended, leading to emissions exceeding allowable limits.
Failure to comply with regulations: Failure to comply with emissions regulations can lead to fines, legal action, and damage to a company’s reputation.
Insufficient training: Operators and maintenance personnel must be adequately trained to ensure they understand the operation and maintenance of the emission control systems. Insufficient training can lead to mistakes and unsafe emissions.
To mitigate these risks, it is important to have a comprehensive maintenance and inspection program, including regular equipment testing, monitoring, and calibration. Personnel responsible for the equipment should also receive regular training on its operation and maintenance. It is also important to ensure compliance with all applicable regulations and to have processes in place for identifying and addressing any potential issues before they become critical.
RECENT ADVANCES IN TECHNOLOGY – GAS TURBINES – 2 Leer más »