FACTORS IMPACTING AVAILABILITY – GAS TURBINES
FACTORS IMPACTING AVAILABILITY - GAS TURBINES

- Design and Operating Conditions: The design and operating conditions of gas turbines can impact their availability. Gas turbines that are designed for high efficiency and reliability, with features such as advanced aerodynamics and cooling systems, can improve availability. Operating conditions such as high temperatures, high altitudes, and dirty air can also impact gas turbine availability.
Recommendations: Consider design features that improve reliability and efficiency, such as advanced aerodynamics, efficient cooling systems, and improved materials. Implement regular inspections and maintenance to identify and address potential issues early on. Consider upgrading or modifying gas turbines to better handle challenging operating conditions.
- Maintenance and Repair Practices: Proper maintenance and repair practices are critical to maintaining gas turbine availability. Neglecting regular maintenance can lead to unexpected downtime and costly repairs. Repair practices that are not performed correctly or efficiently can also impact availability.
Recommendations: Implement a comprehensive maintenance program that includes regular inspections, cleaning, lubrication, and component replacements. Use OEM-approved parts and materials for repairs and replacements. Provide proper training to maintenance personnel to ensure that repairs are performed correctly and efficiently.
- Spare Parts Availability: The availability of spare parts can impact gas turbine availability. If spare parts are not readily available, repairs may take longer than expected, resulting in extended downtime.
Recommendations: Maintain an adequate inventory of critical spare parts to minimize downtime in the event of a failure. Work with suppliers to ensure that spare parts are readily available when needed.
- Human Factors: Human factors such as operator error, inadequate training, and insufficient supervision can impact gas turbine availability.
Recommendations: Provide proper training to operators and maintenance personnel to ensure that they understand how to properly operate and maintain gas turbines. Implement procedures to ensure that operators and maintenance personnel follow best practices and are properly supervised.
- Technology: Advances in technology can impact gas turbine availability. New technologies such as sensors and monitoring systems can help identify potential issues before they result in downtime.
Recommendations: Consider implementing advanced technologies such as vibration sensors and condition monitoring systems to identify potential issues early on. Use data analysis and predictive maintenance techniques to optimize maintenance schedules and improve availability.
By addressing these critical factors, users and manufacturers can work together to improve the availability of gas turbines in both existing and new plants.
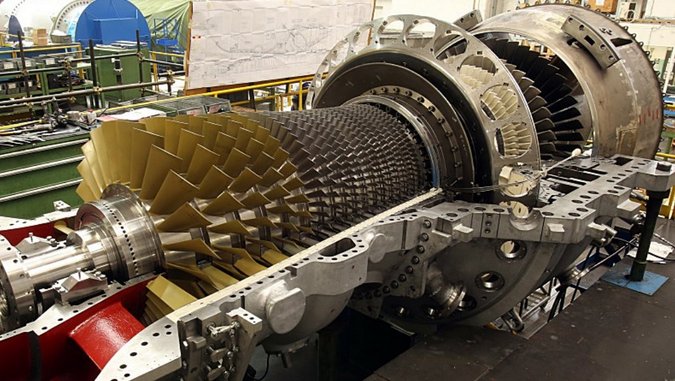
WHY, WHEN, WHERE, WHAT, WHICH, HOW TO APPLY AVAILABILITY FACTORS IN ENGINEERING & DESIGN
Why to Apply Availability Studies and Analysis as Part of Engineering & Design in Gas Turbines:
- Improve Maintainability: Availability studies and analysis help identify potential maintenance challenges and design flaws, allowing for improvements to be made that enhance the ease and efficiency of maintenance activities.
- Enhance Reliability: By analyzing failure modes and their impact on availability, reliability issues can be identified and addressed during the design phase, resulting in more reliable gas turbine systems.
- Increase Availability: Availability studies and analysis enable the identification of critical components and failure modes that can cause downtime. By addressing these factors during design, availability can be improved, reducing unplanned outages and maximizing the operational uptime of gas turbines.
- Ensure Safety: Analyzing the availability of safety systems and their impact on overall system availability helps ensure that the gas turbine operates safely and reliably, reducing the risk of accidents or equipment failures.
When to Apply Availability Studies and Analysis: Availability studies and analysis should be conducted during the design and engineering phase of gas turbines. It is important to consider availability factors from the early stages of design to ensure that reliability and maintainability considerations are integrated into the system design.
Where to Apply Availability Studies and Analysis: Availability studies and analysis should be applied in both existing plants and new projects for power generation plants, as well as in the oil, gas, and petrochemical industries where gas turbines are widely used. This includes gas turbine installations in various applications such as power plants, refineries, petrochemical plants, and offshore platforms.
What to Analyze in Availability Studies and Analysis: In availability studies and analysis for gas turbines, the following aspects can be analyzed:
- Component reliability and failure modes.
- System architecture and redundancy.
- Maintenance strategies and practices.
- Impact of maintenance activities on system availability.
- Availability of critical safety systems.
- Failure data analysis and root cause identification.
- Mean Time Between Failures (MTBF) and Mean Time To Repair (MTTR) calculations.
- Failure rate analysis and probability of failure calculations.
Which Methods and Tools to Use for Availability Studies and Analysis: Various methods and tools can be used for availability studies and analysis in gas turbines, including:
- Fault Tree Analysis (FTA) to identify critical failure modes and their causes.
- Failure Mode and Effects Analysis (FMEA) to assess the impact of failure modes on availability.
- Reliability Block Diagrams (RBD) to model system architecture and analyze the availability of critical components and subsystems.
- Reliability-centered Maintenance (RCM) to determine the most effective maintenance strategies based on criticality and impact on availability.
- Condition Monitoring techniques to assess the health and performance of critical components.
How to apply it?
Define Availability Objectives: Clearly define the availability objectives for the gas turbine system. This includes specifying the desired level of availability, downtime limits, and performance metrics.
Identify Critical Components: Identify the critical components of the gas turbine that significantly impact availability. These may include turbine blades, rotors, combustion systems, bearings, control systems, and auxiliary equipment. Focus the analysis on these components.
Data Collection: Gather relevant data on the performance, maintenance history, failure records, and operational conditions of the gas turbine system. This data can come from plant maintenance records, equipment manuals, industry standards, and interviews with maintenance personnel.
Analyze Failure Data: Analyze historical failure data to identify common failure modes, their frequency, and their impact on availability. Determine the root causes of failures and assess the effectiveness of existing maintenance practices in mitigating downtime.
Reliability Analysis: Perform reliability analysis to assess the reliability characteristics of critical components and the overall system. This can involve analyzing failure rates, mean time between failures (MTBF), mean time to repair (MTTR), and other reliability parameters.
Reliability Block Diagrams (RBD): Develop RBDs to model the system architecture of the gas turbine, identifying critical components and potential failure paths. Analyze the impact of different failure scenarios on system availability.
Fault Tree Analysis (FTA): Utilize FTA to systematically analyze potential system failures, identifying the root causes and evaluating their impact on system availability. This can help in prioritizing reliability improvement measures.
Redundancy and Backup Systems: Evaluate the redundancy and backup systems in place for critical components of the gas turbine. Identify potential single points of failure and develop strategies to enhance redundancy and improve system availability.
Maintenance Strategies: Assess the existing maintenance strategies and practices for the gas turbine. Evaluate the effectiveness of preventive maintenance, predictive maintenance, and corrective maintenance activities in minimizing downtime and improving availability.
Risk Assessment: Conduct a risk assessment to identify and prioritize the risks associated with failures and their impact on availability, safety, and operational continuity. This helps in allocating resources and prioritizing improvement efforts.
Design Improvements: Based on the findings from availability studies and analysis, incorporate design improvements in the gas turbine. This may include component selection, system architecture modifications, enhanced redundancy, and improved maintenance access.
Documentation and Knowledge Sharing: Document the findings, analysis, and recommendations resulting from the availability studies and analysis. Share this information with relevant stakeholders, including design engineers, maintenance personnel, and operators, to ensure the implementation of improvement measures.
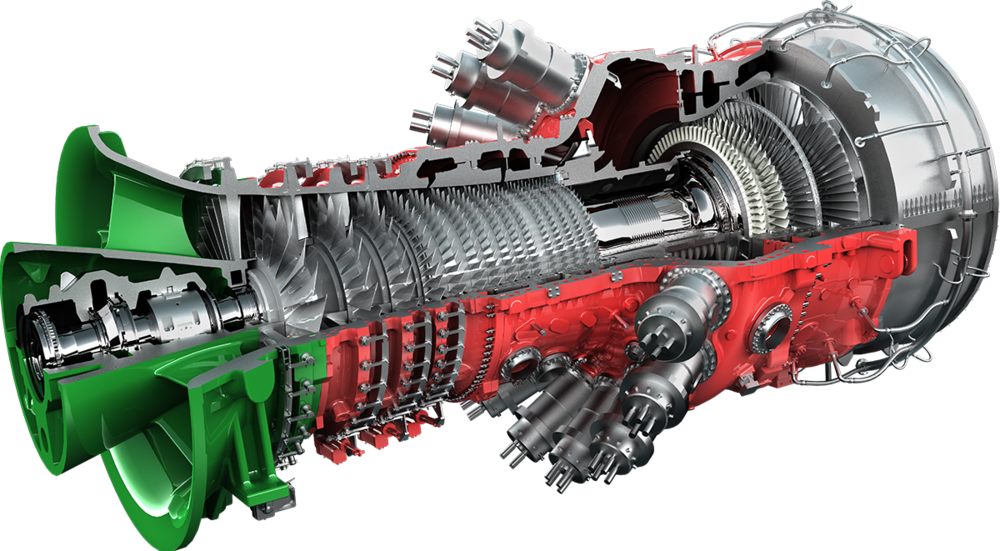
PROCEDURES, ACTIONS, STUDIES, MITIGATION, RECOMMENDATIONS TO APPLY AVAILABLITY FACTORS IN ENGINEERING & DESIGN
To apply availability factors in the design and engineering of gas turbines, with the aim of improving maintainability, reliability, availability, and safety in existing plants and new projects for power generation, oil, gas, and petrochemical industries, the following procedures, actions, studies, mitigations, and recommendations can be considered:
Reliability Analysis:
- Perform reliability analysis to identify the critical components and failure modes that have the greatest impact on availability.
- Analyze failure data and historical performance to determine failure rates, mean time between failures (MTBF), and mean time to repair (MTTR) for key components.
- Use reliability prediction techniques to estimate the expected reliability and availability of the gas turbine system.
Fault Tree Analysis (FTA):
- Conduct fault tree analysis to identify the root causes of failures and their potential impact on availability.
- Develop fault tree diagrams to visualize the failure paths and evaluate the probabilities of different failure events.
- Prioritize the critical failure events based on their impact on availability and develop mitigation strategies for each event.
Redundancy and Backup Systems:
- Evaluate the level of redundancy in the gas turbine system to ensure that critical components have backup systems in place.
- Assess the effectiveness of redundancy configurations in improving system availability and reducing single points of failure.
- Design and engineer backup systems that can quickly and seamlessly take over in case of component failures.
Maintenance Strategies:
- Implement a comprehensive maintenance strategy that includes preventive maintenance, predictive maintenance, and corrective maintenance.
- Establish regular inspection and maintenance schedules for critical components, considering their failure modes and recommended maintenance practices.
- Utilize condition monitoring techniques, such as vibration analysis and thermal imaging, to proactively detect and address potential issues before they lead to failures.
Reliability-Centered Maintenance (RCM):
- Apply reliability-centered maintenance principles to determine the most effective maintenance tasks and intervals for critical components.
- Prioritize maintenance activities based on their impact on availability and safety.
- Continuously monitor and analyze maintenance data to optimize maintenance practices and improve system availability.
Component Selection and Design:
- Select and design components that have a proven track record of reliability and availability.
- Consider factors such as component robustness, ease of maintenance, and availability of spare parts when selecting components.
- Collaborate with component suppliers and manufacturers to ensure that the selected components meet the required reliability and availability standards.
Safety Considerations:
- Integrate safety features into the gas turbine design to prevent accidents and minimize the impact of failures on personnel and the environment.
- Conduct hazard and risk assessments to identify potential safety hazards and mitigate them through appropriate design measures.
- Comply with relevant safety standards and regulations to ensure the safe operation of the gas turbine system.
Documentation and Knowledge Management:
- Document all design decisions, maintenance procedures, and mitigation strategies for future reference and knowledge transfer.
- Establish a centralized knowledge management system to capture and share lessons learned from previous projects and maintenance activities.
- Foster a culture of continuous improvement by actively learning from past experiences and implementing best practices.
FACTORS IMPACTING AVAILABILITY – GAS TURBINES Leer más »